Insinöörit käyttävät CAD-ohjelmistoa suunnitellakseen kaikki projektissa tarvittavat osat ja komponentit. Digitaalisessa maailmassa on helppo saavuttaa täydellisyys. Todellisessa elämässä valmistus ei koskaan ole 100-prosenttisen tarkkaa.
Joskus muutaman millimetrin poikkeamat perusmitoista voivat olla aivan hienoja. Samaan aikaan kaksi toisiinsa sopivaa komponenttia voi vaatia erittäin suurta tarkkuutta.
Edellytetyn poikkeaman pitämiseksi ennalta määritellyllä alueella on mahdollista käyttää teknisiä toleransseja. Mittatoleranssit ovat hyvin yleisiä, mutta niistä puuttuu keinoja joidenkin erittäin tärkeiden valmistusnäkökohtien ilmoittamiseen. Tässä kohtaa GD&T eli geometrinen mitoitus & tolerointi astuu kuvaan.
Se on muoto kuvata mitat ja toleranssit täysin uudella tavalla. Käyttämällä yhteistä insinöörisymbolien kieltä se auttaa paikantamaan kaikki tarvittavat tiedot helposti.
- Mikä on GD&T?
- Miksi soveltaa GD&T:tä?
- Täydellinen kokoonpano
- Yhteinen järjestelmä suunnittelutarkoituksen selittämiseen
- Säästää aikaa ja rahaa
- Mitä kannattaa ottaa huomioon?
- Piirustuksen ymmärrettävyys
- Kireät toleranssit vain tarvittaessa
- GD&T-ominaisuudet & Symbolit
- Nimellismitat
- Ominaisuuden ohjauskehys
- Johtonuoli
- Geometrinen ominaisuustunnus
- Toleranssilokero
- Datums
- Materiaaliolosuhdemodifioijat
- Maksimaalisen materiaaliehdon muokkaaja
- Least material condition modifier
- Ominaisuuden koosta riippumatta (RFS)
- Datat ja Feature Callouts
- GD&T-symbolit
- Muodonohjaus
- Suoruus
- Leveys
- Ympyrämäisyys
- Sylinterimäisyys
- Profiilinohjaukset
- Viivaprofiili
- Pintaprofiili
- Orientointiohjaukset
- Kulmikkuus
- Paralllisuus
- Perpendicularity
- Sijainnin ohjaukset
- Keskeisyys
- Symmetria
- Tosi sijainti
- How to Apply GD&T Position Tolerance to a Hole
- Runout Controls
- Ympyräpoikkeama
- Tarkastus
Mikä on GD&T?
Se on symboli- ja standardijärjestelmä, jota insinöörit käyttävät valmistustietojen antamiseen tuotantotiimille.
Syyt geometrisen mitoituksen ja toleroinnin (GD&T) käyttöön ovat:
- Se varmistaa, että toisiinsa sopivat osat sopivat hyvin yhteen
- Yleismaailmallinen kieli toimii riippumatta siitä, kenen kanssa työskentelet
- Toleranssit antavat rajan huonoimmille mahdollisille olosuhteille
- Määrittelee tuotanto- ja tarkastusprosesseja
Stanley Parkerin katsotaan olleen insinööri, joka kehitti GD&T-järjestelmän vuonna 1938.
Sitä ennen kaikki piirteet käyttivät vain X-Y-akseleita esimerkiksi reiän sijainnin määrittämiseen. Sijaintitoleranssin antaminen tuolla asteikolla tarkoittaa sitä, että ympyränmuotoisen reiän sijainti voi poiketa suorakulmion muotoisesti aiotusta kohdasta.
Olemme kuitenkin itse asiassa halunneet, että toleranssialue olisi ympyrä, koska se mahdollistaa yhdenmukaisen mittauksen kaikissa kulmissa, kun taas suorakulmio on pitempi kulmiin päin ja lyhyempi sivuille päin.
Niin kun Parker tajusi tämän, hän alkoi työstää uutta konseptia, joka hyväksyttiin sotatekniikan standardiksi 50-luvulla.
Tänä päivänä GD&T on tärkeä osa insinöörityötä, varsinkin kun luodaan osia, jotka vaativat CNC-työstöpalveluja. Ominaisuuksia kuvaava amerikkalainen standardi on ASME Y14.5-2018 ja eurooppalainen vastine on ISO 1101-2017.
GD&T keskittyy yksinomaan tuotteen geometriaan. Lineaariset mitat, pinnankarheus, kierteet jne. eivät kuulu tähän standardiin.
Miksi soveltaa GD&T:tä?
Meillä on perinteisiä menetelmiä mittojen ja toleranssien merkitsemiseen. Mihin siis tarvitaan geometrista mitoitusta ja tolerointia?
Geometrinen mitoitus ja tolerointi (GD&T) tarjoaa joitakin ainutlaatuisia etuja tavanomaisiin menetelmiin verrattuna. Katsotaanpa, mitä nämä ovat.
Täydellinen kokoonpano
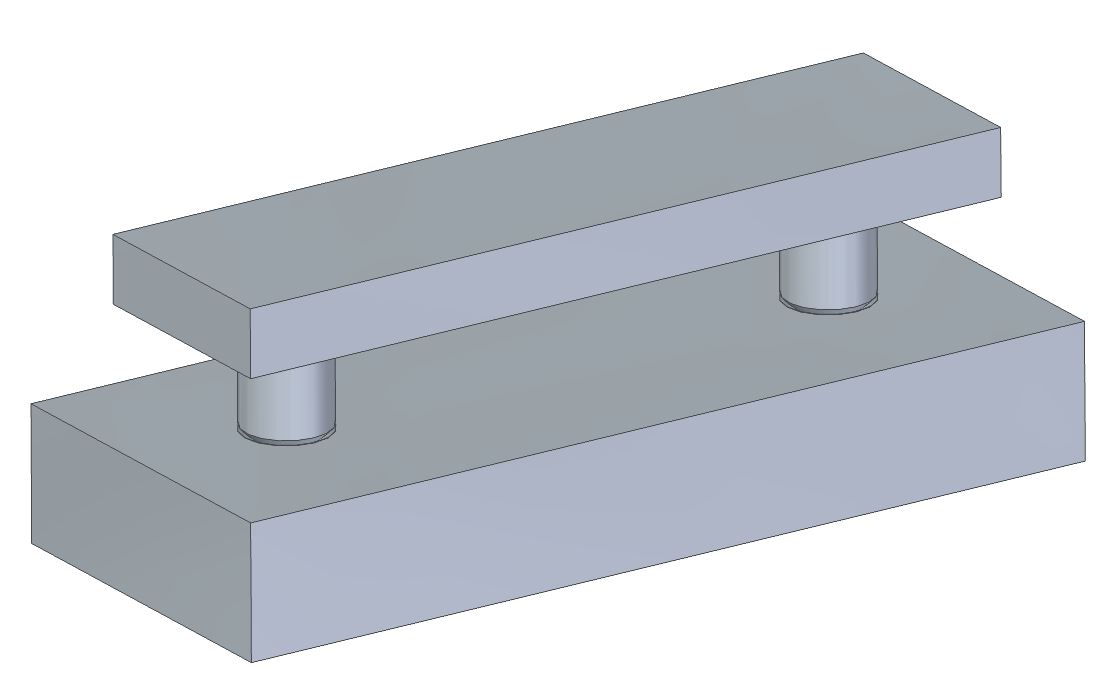
Traditionaalisen mitoituksen ja toleranssin käytön merkittävin haittapuoli on se, että ne merkitsevät yksittäisen osan ja osan ominaisuustietoja. Se ei takaa, miten hyvin osat sopivat ja toimivat kokoonpanotasolla.
Tämä on tärkeää, koska useimmat osat eivät ole käyttökelpoisia itsessään. Tarkastellaan esimerkkiä yhdystangosta. Itsessään siitä ei ole meille mitään hyötyä. Mutta kun yhdistämme sen kampiakseliin ja mäntään, siitä tulee hieman hyödyllisempi, sillä se muuntaa männän lineaarisen liikkeen kampiakselin pyörimisliikkeeksi.
Kun tästä kokoonpanosta tulee osa isompaa kokoonpanoa, kuten dieselmoottoria, se voi päätyä osaksi generaattoria, joka tarjoaa meille monia käyttötarkoituksia.
Sentähän varten on ratkaisevaa, että osien on sovitettava hyvin toisiinsa. Siksi tarvitsemme GD&T:tä. Sen avulla voimme olla sataprosenttisen varmoja siitä, että osat sopivat yhteen ja toimivat juuri niin kuin tarvitaan.
Yhteinen järjestelmä suunnittelutarkoituksen selittämiseen
GD&T tarjoaa suunnittelijalle myös alustan, jonka avulla hän voi välittää suunnittelutarkoituksen kaikille asiaankuuluville osastoille. Näitä ovat:
- Tuotanto
- Tarkastus
- Suunnitteluosaston tulevat suunnittelijat, jotka ottavat työn haltuunsa, jos alkuperäinen suunnitteluryhmä ei ole käytettävissä
Määritelmät, sanasto ja säännöt ovat suoraviivaisia ja yleisesti ymmärrettäviä. Tämän ansiosta symbolit on helppo kääntää jokaiselle insinöörille, ja ne ovat erinomainen tapa välittää suunnittelijan aikomus.
Säästää aikaa ja rahaa
Tämä on GD&T:n käytön tärkein etu. Tämän järjestelmän käyttö vähentää hukkaa, koska se vähentää suunnittelu-valmistus-testisovitussyklien määrää.
Tämä johtuu siitä, että valmistetut osat sopivat hyvin ensimmäisellä yrityksellä, ja näin ollen hylkäysten määrä on vähäinen. Yhteisen kielen käyttö vähentää myös tarkastukseen tarvittavaa vaivaa.
Hae valmistustarjous sekunneissa
-
Tarjous sekunneissa
-
Lyhyet läpimenoajat
-
Toimitus Fractoryn toimesta
Pyydä tarjousta
Mitä kannattaa ottaa huomioon?
Geometrinen mitoitus ja tolerointi on tehokkaampi järjestelmä verrattuna perinteisiin toleransseihin. Se toimii kuitenkin vain, jos kaikki osastot (suunnittelu, insinöörityö, valmistus) osaavat lukea ja tulkita tietoja.
Sentähän varten on tärkeää, että teknisiä piirustuksia laadittaessa ja eri osien ominaisuuksia toleroitaessa noudatetaan suositeltuja ohjeita/konventioita kaikkien niiden eduksi, jotka ovat vuorovaikutuksessa piirustuksen kanssa missä tahansa tuotekehitysvaiheessa.
Näiden ohjeiden/konventioiden noudattamisella varmistetaan piirustuksen standardisointi ja se, että piirustuksen erityispiirteistä puhuttaessa ollaan kaikki samoilla linjoilla. Joitakin näistä hyvistä käytännöistä ovat seuraavat.
Piirustuksen ymmärrettävyys
Tämä on kiistatta piirustuksen tärkein ominaisuus. Ymmärrettävyydellä tarkoitetaan selkeyttä, jolla osan ominaisuudet piirretään ja toleranssit esitetään piirustuksessa. Joitakin tapoja parantaa piirustuksen ymmärrettävyyttä ovat:
- Piirrä oikeat profiilit kaikille osan piirteille.
- Merkitse mitat ja toleranssit piirustuksen ulkopuolelle (ei päälle). Käytä valkoista tilaa tehokkaasti.
- Lukusuunnan on oltava vakio. Lukijan tulee pystyä lukemaan kaikki mitat pitämällä piirustusta pystyssä.
- Kirjoita samansuuntaisten osan piirteiden mitat avaruuteen.
- Esittele osa ja sen toiminta lyhyesti.
- Määritä kulmat vain silloin, kun ne eivät ole suorakulmaisia (90°).
Kireät toleranssit vain tarvittaessa
Jollei osan istuvuus/toiminto sitä vaadi, toleranssit on pidettävä mahdollisimman väljinä. Tämä vähentää valmistuskustannuksia ja läpimenoaikaa. Suosittelemme jättämään valmistusmenetelmän valinnan koneistajille.
Suunnittelijan on mainittava myös piirustuksen yleistoleranssi. Tämä toimii vakiotoleranssina kaikille osan ominaisuuksille. Jos osan piirteillä on eri toleranssiraja, suunnittelijan on mainittava ne asianmukaisissa kohdissa.
Nämä erityiset toleranssirajat syrjäyttävät yleistoleranssit. Kun määrittelet erityisiä toleranssirajoja, suosi toiminnallisia piirteitä muiden piirteiden sijaan.
GD&T-ominaisuudet & Symbolit
GD&T-kielellä pystytään määrittelemään jokseenkin kaikki ominaisuudet, jotka ovat välttämättömiä täydellisen kokoonpanon takaamiseksi.
Järjestelmä käyttää useita symboleja tähän tarkoitukseen. Jotta näitä insinöörisymboleja voidaan käyttää piirustuksissa oikein, on ensin tunnettava joitakin tämän järjestelmän perusrakennuspalikoita.
Voidaan aloittaa erilaisista määritelmistä, terminologioista ja säännöistä, ennen kuin päästään GD&T-symboleihin.
Nimellismitat
Nimellismitta on todellisen profiilin ominaisuussuuruus. Se on tarkka mitta, jonka haluaisimme saavuttaa ihanteellisesti. Piirteen erityispiirteillä, kuten koolla, suuntauksella, sijainnilla vertailupisteestä, on nimellismitta, johon koneistajat tähtäävät.
Piirustuksessa ne esitetään laatikon sisällä. Se voidaan esittää numerona tai jostain suositusta standardista, kuten ASME:stä.
Ominaisuuden ohjauskehys
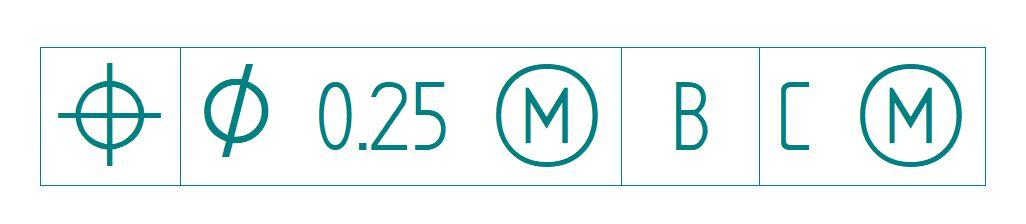
Tämä kehys sisältää tietoa kappaleen erityispiirteistä. Se sisältää erilaisia lokeroita, joissa kukin lokero määrittelee osan ominaisuuden tietyn ominaisuuden. Ominaisuuden ohjauskehys välittää yhdellä silmäyksellä koneistuksessa ja tarkastuksessa tarvittavat tiedot.
Ominaisuuden ohjauskehys voidaan jakaa neljään pääosaan seuraavasti.
Johtonuoli
Tämä nuoli merkitsee ohjattavan osan ominaisuuden. Jos se johtaa pintaan, pinta on geometrisen valvonnan piirissä. Jos se merkitsee halkaisijamittaa, GD&T ohjaa akselia. Tätä nuolta ei välttämättä ole joissakin tapauksissa.
Geometrinen ominaisuustunnus
Ensimmäisessä lokerossa (vasemmalta alkaen) on geometrinen ominaisuustunnus. Tässä määritetään geometrinen ominaisuus. Kaikkiaan geometrisia toleransseja on symbolien lukumäärän perusteella 14 erilaista ja luokiteltuna 15 erilaista.
Geometristen ominaisuuksien eri tyypit ovat muodonohjaus, profiilinohjaus, sijainninohjaus, suunnanohjaus jne. Sukellamme syvällisemmin kuhunkin luokkaan myöhemmin.
Toleranssilokero
2. lohko sisältää enintään 3 (joskus 2 tai 1) eri symbolia.
Ensimmäinen symboli osoittaa toleranssialueen tyypin. Halkaisijasymboli (⌀) tarkoittaa halkaisijavyöhykettä (sylinterimäinen toleranssialue). Pallonmuotoisen vyöhykkeen määrittämiseksi symboli on kirjain ”S”, jota seuraa halkaisijan symboli (⌀). Jos symbolia ei ole, oletetaan, että kyseessä on täysin leveä vyöhyke.
Lohkon 2 toinen symboli ilmoittaa toleranssialueen arvon millimetreinä. Tämän arvon on aina oltava 2. lohkossa.
Tämän lohkon kolmas symboli on toleranssin modifioija. Tämä materiaalin muokkaaja on läsnä vain silloin, kun piirteellä on koko, esimerkiksi reikä. Esimerkkejä materiaalimodifioijista ovat MMC (Maximum material condition) ja LMC (Least material condition). Lisätietoa käytettävissä olevista eri modifioijista käsitellään myöhemmin artikkelissa.
Datums
Kolmas lohko antaa tiedot datum(e)ista, joiden vähimmäismäärä on 1 ja enimmäismäärä 3 datumia. Jos datumeita on kolme, niitä kutsutaan ensisijaiseksi, toissijaiseksi ja kolmanneksi datumiksi, ja kukin niistä esitetään eri laatikossa (esimerkiksi yllä olevassa kuvassa niitä on kaksi). Tämä lohko voi sisältää myös materiaalin muokkaajan.
Kaikki edellä mainitut tiedot auttavat meitä ymmärtämään, miten ominaisuuden ohjauskehystä luetaan. Jotta ymmärtäisimme paremmin, miten toleranssia voidaan säätää materiaaliolosuhdemodifioijien avulla, meidän on tunnettava eri vaihtoehdot.
Materiaaliolosuhdemodifioijat
Materiaaliolosuhdemodifioijat välittävät tarkoituksen, kun toleranssi koskee piirrettä tietyllä piirrekoolla. Aina kun annamme jollekin piirteelle toleransseja, se määrittää kaksi materiaaliolosuhdetta
- Maksimimateriaaliolosuhde
- Vähimmäismateriaaliolosuhde
Harkitaan akselia, jonka halkaisija on 100 mm. Jos valmistuksessa annamme sille ±0,2 mm:n toleranssin, akselissa on 100,2 mm:n kohdalla suurin mahdollinen määrä materiaalia. Tätä tarkoitamme materiaalin maksimitilanteella.
Toisaalta sama akseli, kun se valmistetaan halkaisijaltaan 99,8 mm, sisältää vähiten materiaalia. Näitä rajoja kutsutaan materiaaliolosuhteiksi.
Geometrisia toleransseja voidaan soveltaa piirteeseen kolmella eri tavalla. Nämä ovat seuraavat:
- Maksimaalinen materiaaliehto
- Vähimmäismateriaaliehto
- Ominaisuuden koosta riippumatta
Maksimaalisen materiaaliehdon muokkaaja
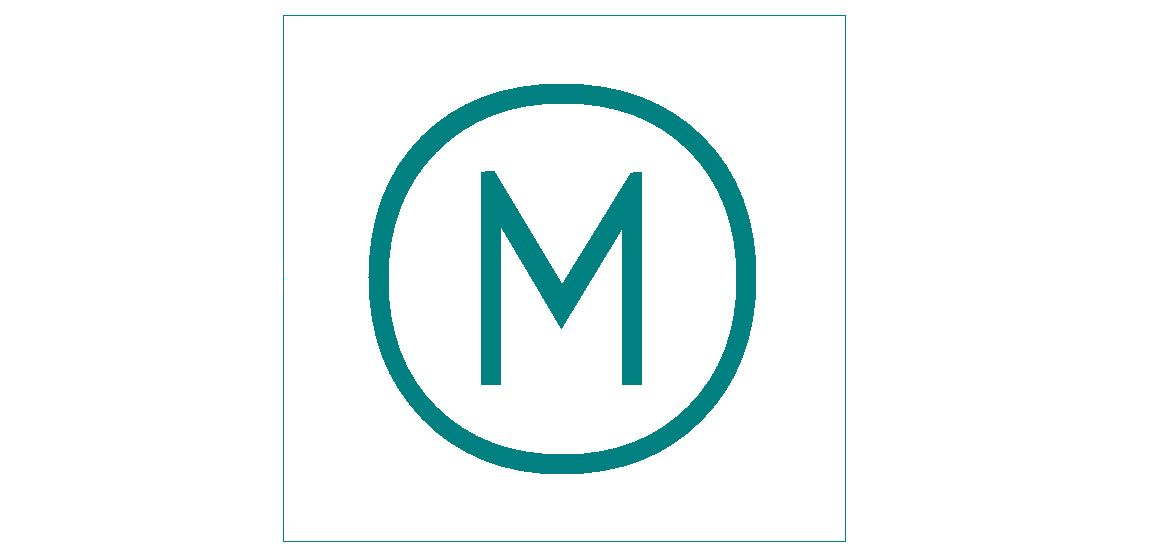
Kuvaamme tämän ehdon ympyröitynä ”M”:llä, joka on merkitty toleranssiarvon perään ominaisuuden ohjausosastossa. Piirre sisältää maksimimateriaalin tällä piirrekoolla.
Ulkoisen FOS:n (Feature Of Size), kuten akselin halkaisijan, osalta MMC edustaa suurinta kokoa. Sisäisen FOS:n, kuten reiän halkaisijan, osalta MMC edustaa pienintä mahdollista kokoa ilmoitettujen toleranssirajojen puitteissa, koska pienempi reikä tarkoittaa, että materiaalia jää enemmän.
Kun on sovellettava geometrista toleranssia suurimmassa materiaaliolosuhteessa, mainitaan tämä olosuhde piirteen ohjauskehyksessä.
Least material condition modifier
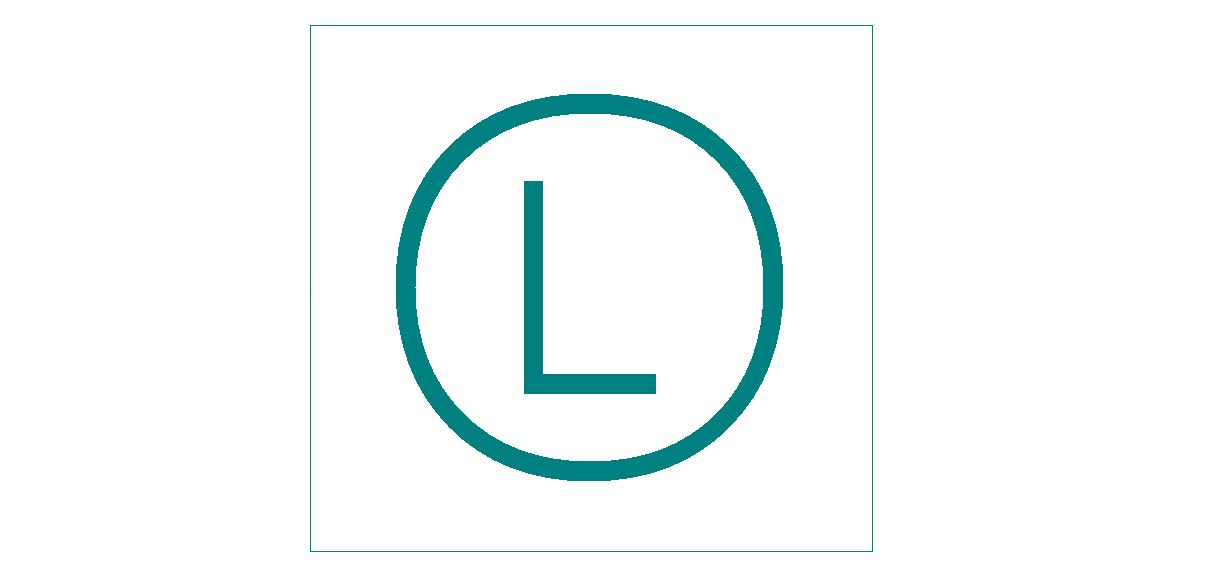
LMC on olosuhde, jossa materiaalissa on vähiten materiaalia.
Ulkoisen FOS:n osalta se on pienin mahdollinen koko ilmoitetuissa rajoissa. Ja sisäisen FOS:n osalta se on suurin mahdollinen koko.
Kuvaamme tämän modifioijan L-kirjaimella ympyrän sisällä. Tämä ominaisuus poistaa ylimääräistä materiaalia ja siten painoa. Sovellettaessa geometrisia toleransseja tässä tilassa käytämme sen symbolia piirteen ohjauskehyksessä.
Ominaisuuden koosta riippumatta (RFS)
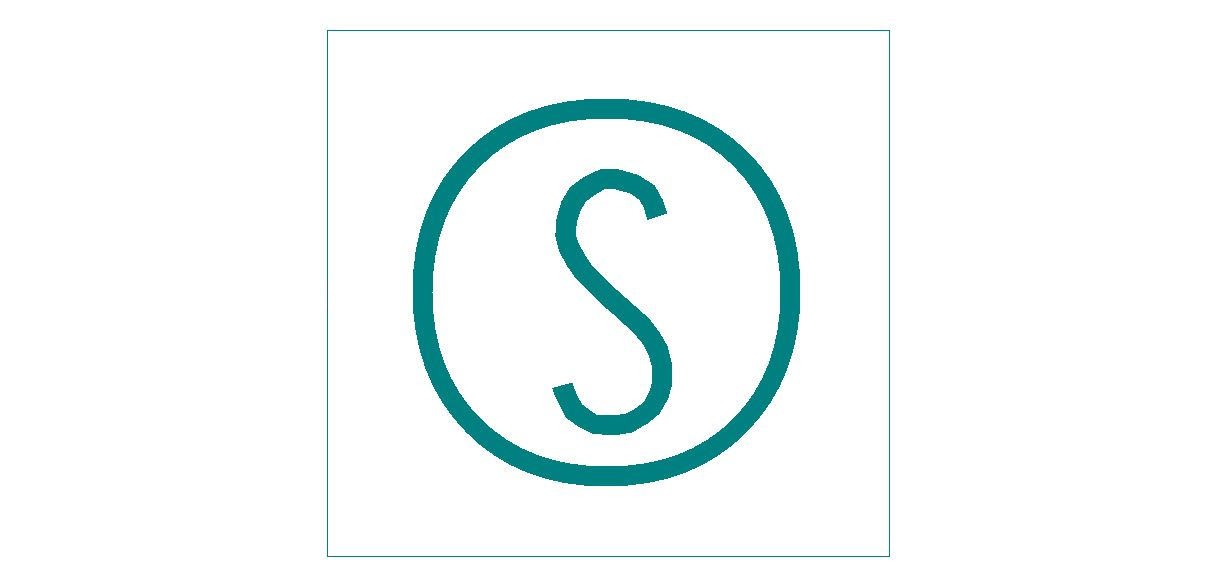
Kun annettuja geometrisia toleransseja sovelletaan millä tahansa FOS:n koon inkrementillä, ilmaisemme sen RFS:llä. RFS:n symboli oli ympyrän ympäröimä S-kirjain, mutta sitä ei enää tarvita, koska RFS:ää pidetään nykyään oletusehtona, eikä siihen tarvita symbolia.
Datat ja Feature Callouts
Datat ovat vertailupisteitä mittatoleranssien mittaamista varten. Se voi olla piste, viiva tai taso. Datumin avulla luodaan Datum Reference Frames (DRF). DRF on periaatteessa 3D-koordinaattijärjestelmä, joka auttaa meitä määrittelemään kaikkien muiden piirteiden sijainnit DRF:n suhteen.
On kuusi vapausastetta (kolme translaatio- ja kolme rotaatioastetta), joita meidän on hallittava, jotta voimme valmistaa ja tarkastaa osia tehokkaasti. Käytämme DRF:ää näiden vapausasteiden määrittämiseen.
Datum-piirteet ovat varsinaisia osan piirteitä, kuten reikiä ja uria. Niissä voi esiintyä poikkeamia halutusta asennosta.
Kaikista datum-piirteistä asetamme etusijalle ne, jotka sopivat yhteen kokoonpanon muiden osien kanssa. Voimme mainita useamman kuin yhden nollakohdan piirteen ohjauskehyksessä. Ominaisuuksien ohjauskehyksessä olevien DRF:ien järjestyksen mukaan osat sovitetaan DRF:iin tärkeysjärjestyksessä.
GD&T-symbolit
Ominaisuuksien erilaisten geometristen ominaisuuksien esittämiseen on käytettävissä jopa 14 GD- ja T-symbolia. Nämä symbolit auttavat meitä määrittelemään nämä ominaisuudet lopputuotteen vaatimuksina.
Sijoitamme nämä symbolit ominaisuuden ohjauskehyksen ensimmäiseen lokeroon. Tarkastelemme näitä toleranssinohjauksen tyyppejä.
Muodonohjaus
Kuten nimikin kertoo, muodonohjaus liittyy piirteen lopulliseen muotoon tai muotoon. Määrittelemme muodonohjaukset rajoittamaan geometrisen toleranssin poikkeamaa sen ideaalimuodosta. Joitakin suosittuja muodonohjausominaisuuksia ovat seuraavat.
Suoruus
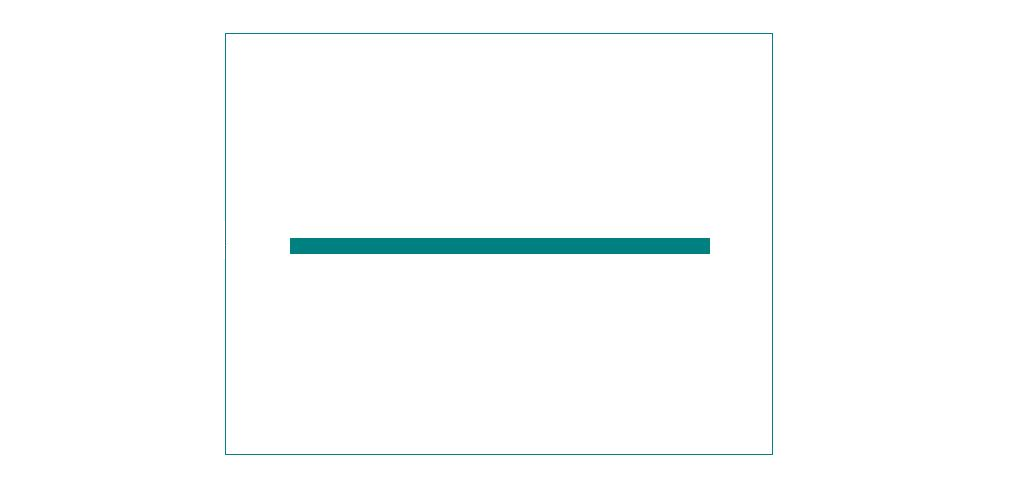
Merkitäksemme piirteen (kuten akselin tai pinnan) suoruusominaisuutta käytämme sen symbolia (suora vaakasuora viiva) ensimmäisessä lokerossa.
Pinnan suoruus voi koskea litteitä pintoja, kuten lohkon sivua, tai kaarevia pintoja, kuten sylinterin sivua, akselin suunnan mukaisesti. Se määrittelee pinnalla olevan viivan (2 dimensiota) sallitun vaihtelun tietyn toleranssin sisällä.
Aksiaalinen suoruus koskee yleensä esimerkiksi akselin tai reiän akselia. Go/no go -mittari on tarkastustyökalu, jolla varmistetaan, että osa on vaatimusten mukainen.
Leveys
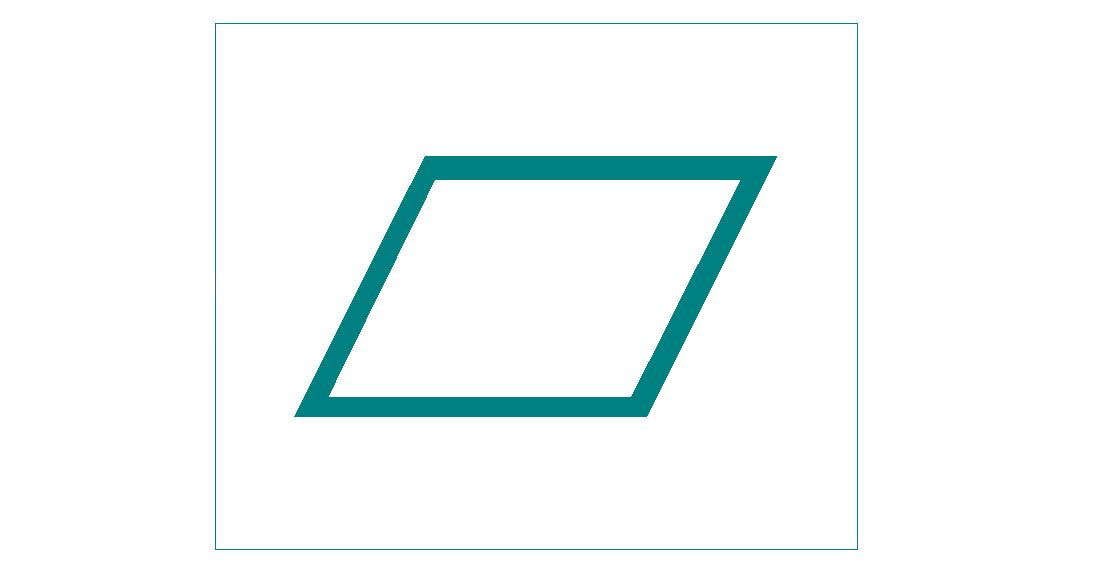
Käytämme tätä ominaisuutta piirteistä, kuten osan pinnasta. Tasaisuuden symboli on oikealle kallistettu parallelogrammi. Tasaisen pinnan korkeimman ja matalimman pisteen välinen ero on sen tasaisuus.
Tasaisuuden symboli ei vaadi mitään nollapisteitä, sillä se osoittaa vain toleranssialueen, jonka sisällä osan koko pinnan on oltava kolmen ulottuvuuden mukainen.
Tulosten tarkistamiseen käytetään korkeusmittaria. Se koskettaa pinnan eri alueita sen määrittämiseksi, että kaikki pisteet ovat toleranssialueen sisällä.
Ympyrämäisyys
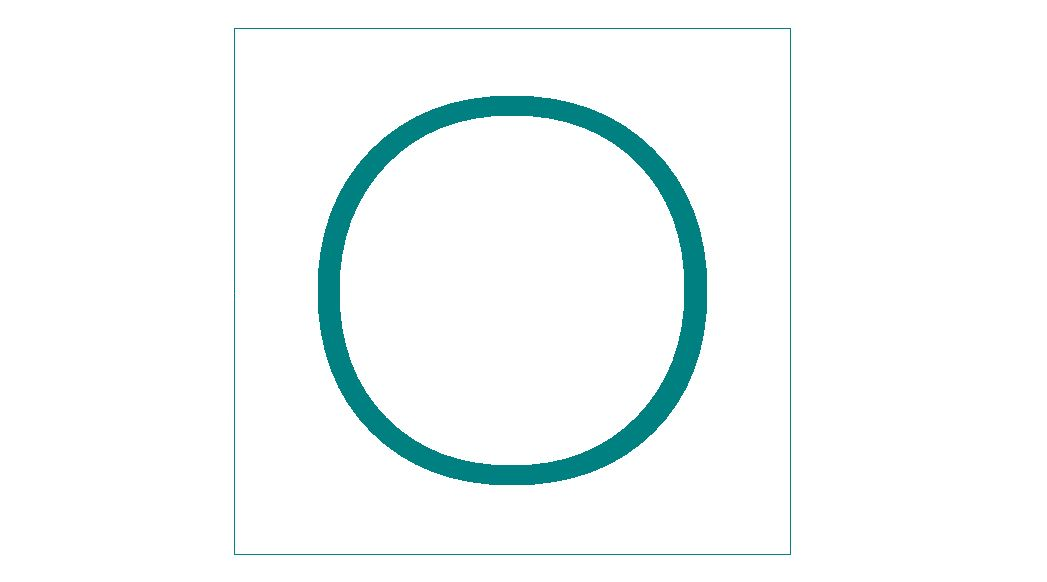
Ominaisuuden ympyrämäisyys ilmaisee, kuinka lähellä kappaleen kehän tulisi olla täydellistä ympyrää. Se käyttää 2 samankeskistä ympyrää osan akselia vastaan kohtisuorassa olevassa tasossa sopivan toleranssialueen määrittämiseen 2D:ssä. Lopullisten mittausten jokaisen pisteen on osuttava ympyröiden väliin.
Tämä ominaisuus näkyy ympyränä piirteen ohjauskehyksen ensimmäisessä lokerossa.
Sylinterimäisyys
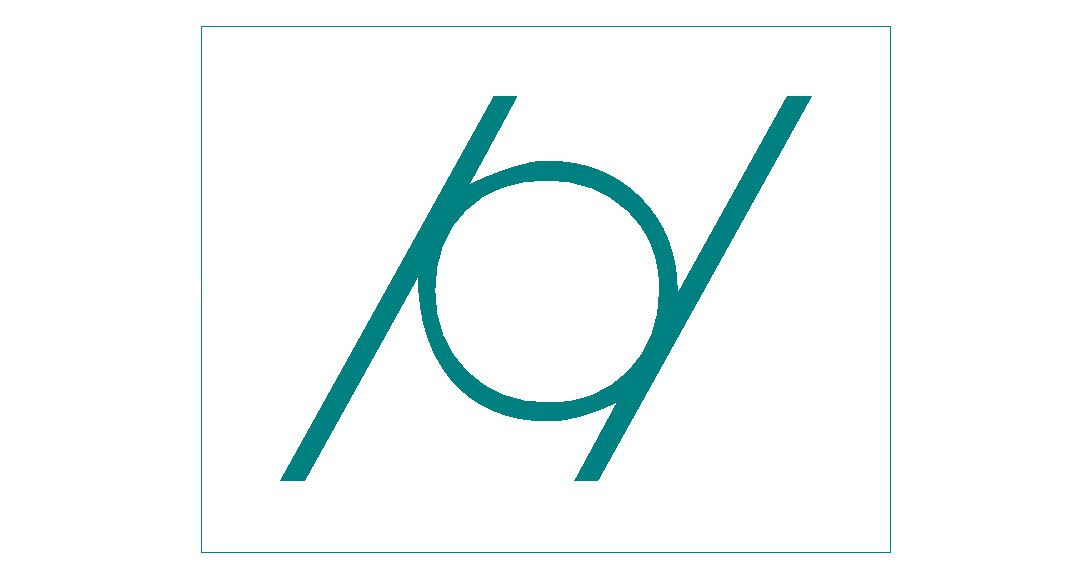
Sylinterimäisyys on pohjimmiltaan ympyrämäisyys 3D:ssä, mikä tarkoittaa sitä, että se kulkee osan koko pituudelta.
Tämä ominaisuus kuvaa myös muita sylinterimäisiä ominaisuuksia, kuten kartiomaisuuttaan, suoruuttaan ja pyöreyttään. Siksi tämän ominaisuuden tarkastaminen on myös kallista.
Profiilinohjaukset
Käytämme profiilinohjauksia ominaisuuden ympärillä olevan 3D-toleranssivyöhykkeen ohjaamiseen. Tämä ominaisuus auttaa meitä antamaan toleranssirajat kehittyneille käyrille ja muodoille.
Ominaisuuden, joka on hyvä edistyneille käyrille, on luonnollisesti toimittava hyvin myös yksinkertaisempien käyrien kanssa. Tämä tekee profiilinohjauksista erittäin monipuolisia. Tämän vuoksi jotkut suunnittelijat suosittelevat luopumaan kaikista muista ohjaimista ja työskentelemään vain profiilinohjaimien kanssa.
Nämä ohjaimet muodostavat toleranssirajan edistyneen käyrän ympärille jäljittelemällä sitä molemmilta puolilta. Sen jälkeen se estää minkä tahansa ominaiskäyrän pisteen siirtymisen toleranssirajan ulkopuolelle. Profiiliohjauksia on kahdenlaisia.
Viivaprofiili
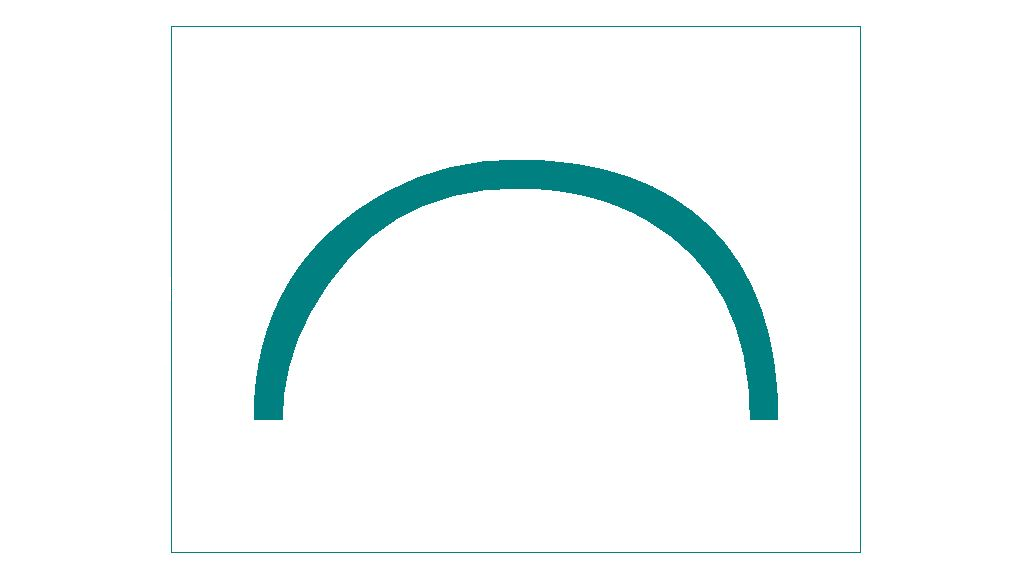
Viivaprofiili muodostaa toleranssialueen kappaleen vaihtelevien 2D-poikkileikkausten ympärille. Se ohjaa osan ominaisuuden yksittäisiä viivaelementtejä.
Viivaprofiilin ohjaus jäljittää ideaalikäyrän toleranssirajojen molemmin puolin. Kaikkien osan käyrän pisteiden on oltava näiden rajojen sisällä.
Pintaprofiili
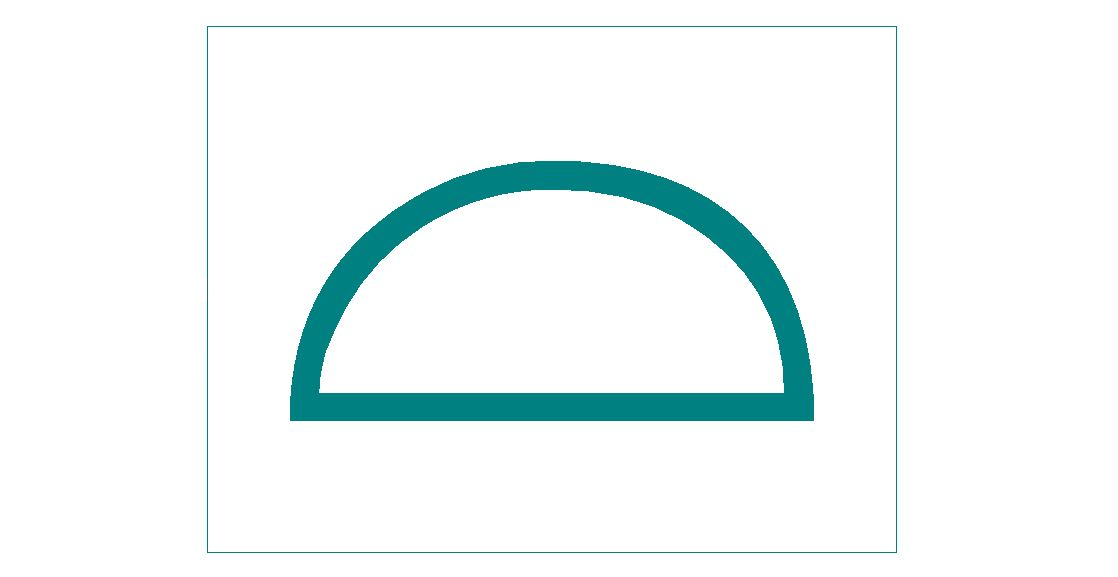
Pintaprofiilin ohjaus on suositumpi verrattuna viivanohjaukseen. Kaksiulotteisen toleranssivyöhykkeen sijaan pintaprofiilin ohjaus luo 3D-vyöhykkeen pinnan ympärille.
Pöydän pinnan kaikkien pisteiden on sijaittava kahden virtuaalisen tason sisällä.
Orientointiohjaukset
Orientointitoleranssilla ohjataan piirteen orientaatiota määritellyn nollapisteen suhteen. GD&T:ssä on kolmenlaisia orientaatiosäätöjä.
Kulmikkuus
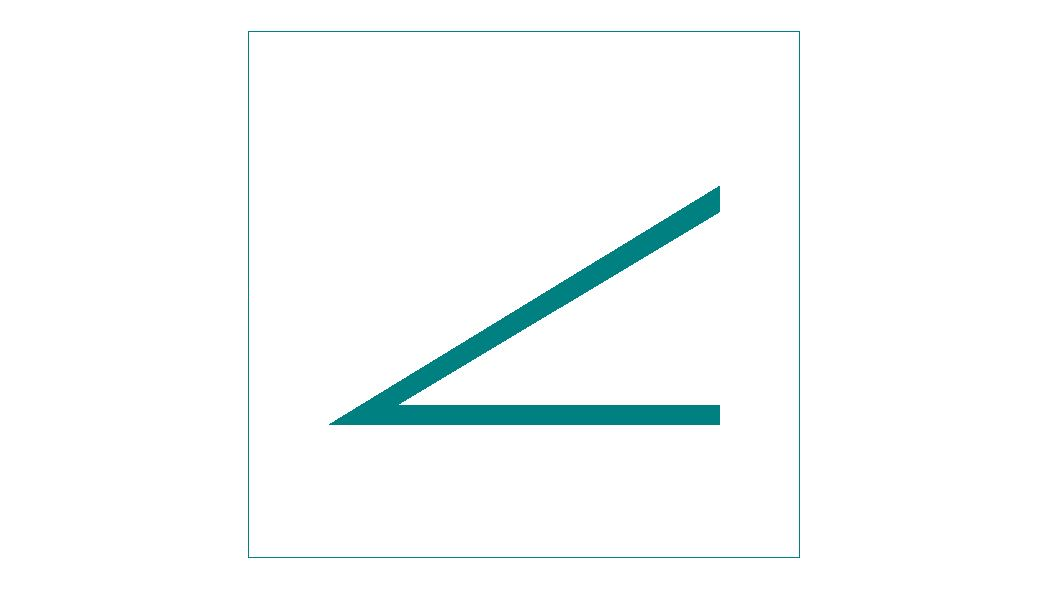
Kulmikkuus-säätö pitää aisoissa piirteen kulman datumiin nähden. Voimme käyttää sitä 2D-viivan hallintaan, mutta se on suositumpi pintojen (3D) hallinnassa pitämisessä.
Tällainen tiukka ohjaus pitää kulman ja pinnan tasaisuuden kurissa, ja sitä suositellaan osaominaisuuksille, jotka sopivat toisiin osiin kulmikkaan pinnan kautta.
On tärkeää huomata, että kulmikkuusominaisuus ohjaa kulmaa epäsuorasti, eikä se ole olennaisesti sama kuin kulmatoleranssi (esim. +/- 2°). Pikemminkin tarvittava kulma on seurausta tämän ohjauksen asettamien mittavaatimusten noudattamisesta.
Paralllisuus
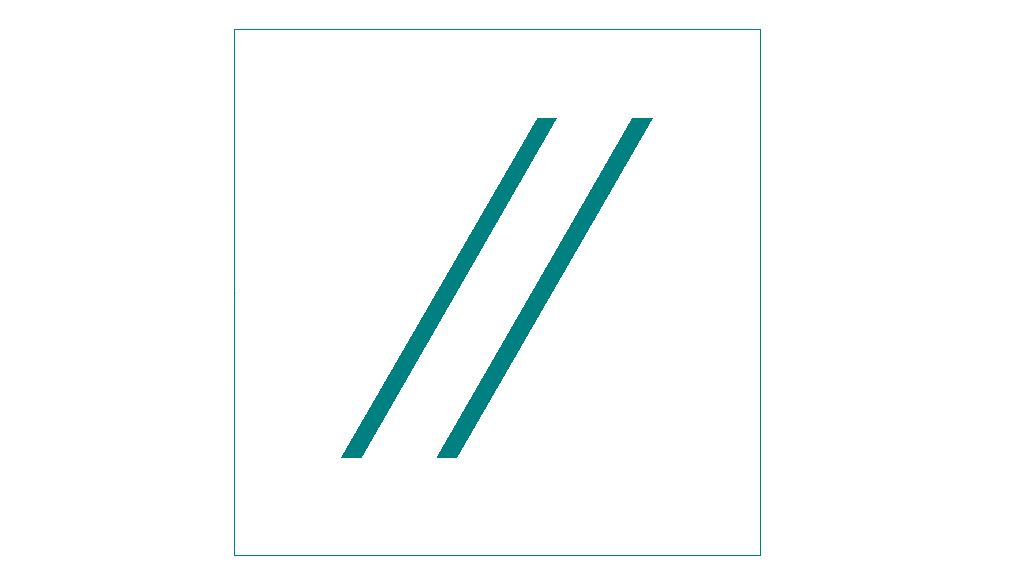
Paralllisuus on kulmikkuuden hienostunut muoto. Tässä vertailukohtana on pinta, jota halutaan jäljitellä, ja kulmaksi asetetaan 0°. On olemassa 2 erilaista parallelismia: pinta- ja akseliparallalismia.
Voidaan valita referenssiksi akseli tai pinta. Tästä tulee referenssikohteemme, ja viittaamme siihen piirteen ohjauskehyksen 3. lohkossa piirteen referenssikohteena.
Samoin kuin kulmikkuus, se ei kontrolloi varsinaista kulmaa, vaan pikemminkin turvaa sen asettamalla vaatimukset toleranssialueen muodossa.
Perpendicularity
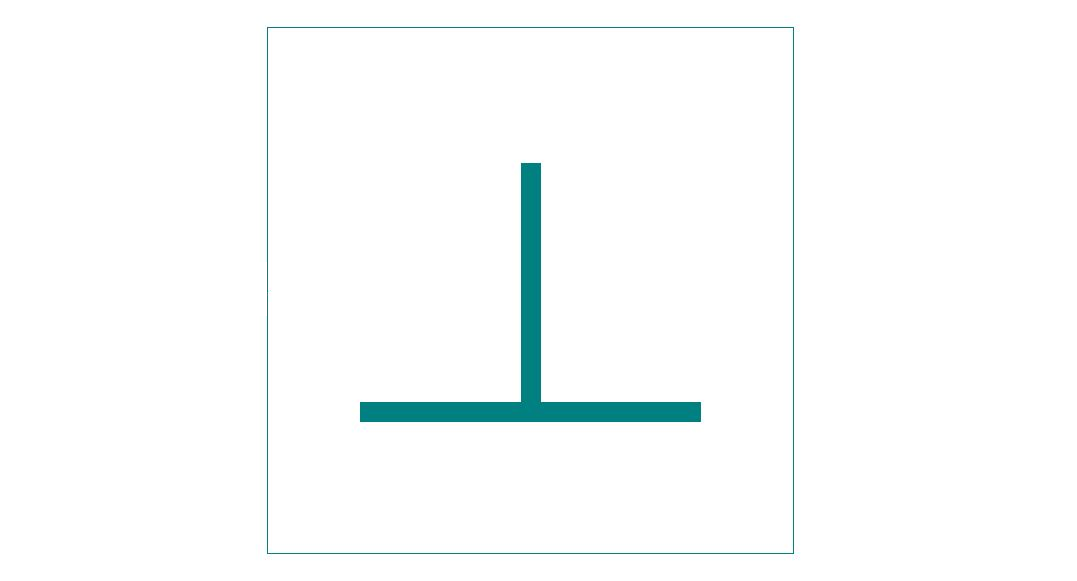
Perpendicularity on myös kulmikkuuden erityinen muoto, jossa kulma asetetaan 90°:een. Se on hankala säätö, koska se voi tarkoittaa kahta hyvin erityyppistä vaatimusta.
On olemassa pinnan kohtisuoruus ( Symboli:⟂) ja sitten on olemassa akselin kohtisuoruus (Symbolit: ⟂+⌀).
Pinnan kohtisuoruus määrittää, että pinnan tai viivan on oltava kohtisuorassa vertailupintaan tai -viivaan nähden samaan tapaan kuin kulmikkuus. Ohjausta varten oletetaan kaksi virtuaalista tasoa/viivaa kohdepinnan ympärille.
Axis perpendicularity määrittelee, kuinka kohtisuorassa akselin on oltava mainittuun datumiin nähden. Tämä tehdään pystyttämällä virtuaalinen sylinteri kohdeakselin ympärille pinnalle, joka on täsmälleen samansuuntainen nollapisteen pinnan kanssa.
Sijainnin ohjaukset
Sijainnin toleranssin ohjausta käytetään piirteen sijainnin tiukkaan ohjaukseen nollapisteeseen nähden. Sijainninohjauksia on neljää päätyyppiä.
Keskeisyys
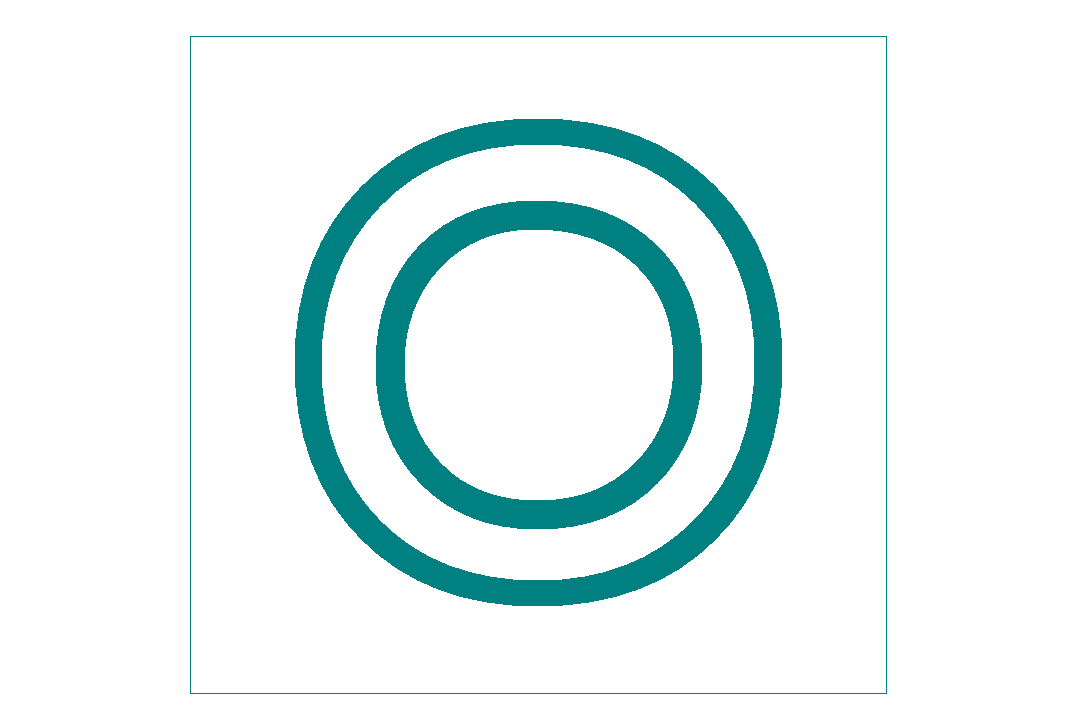
Keskeisyys, joka tunnetaan myös nimellä koaksiaalisuus (vaikkei se olekaan täsmälleen sama asia), ohjauksella ylläpidetään ympyränmuotoisten sekä sylinterimäisten piirteiden keskipisteiden keskipisteellisyys.
Se kiinnittää kappaleen akselin referoidun piirteen akseliin (nollapisteakseliin). Molempien osien akselit määritetään osien keskipisteisiin.
Tämä ohjaus voi aiheuttaa jonkin verran sekaannusta, koska akselit saadaan ulkoisista mittauksista, eikä niiden todellisesta sijainnista.
Koaksiaalisuus luo pintamittauksiin perustuvan 3D-toleranssivyöhykkeen, jonka sisällä osan on sijaittava.
Symmetria
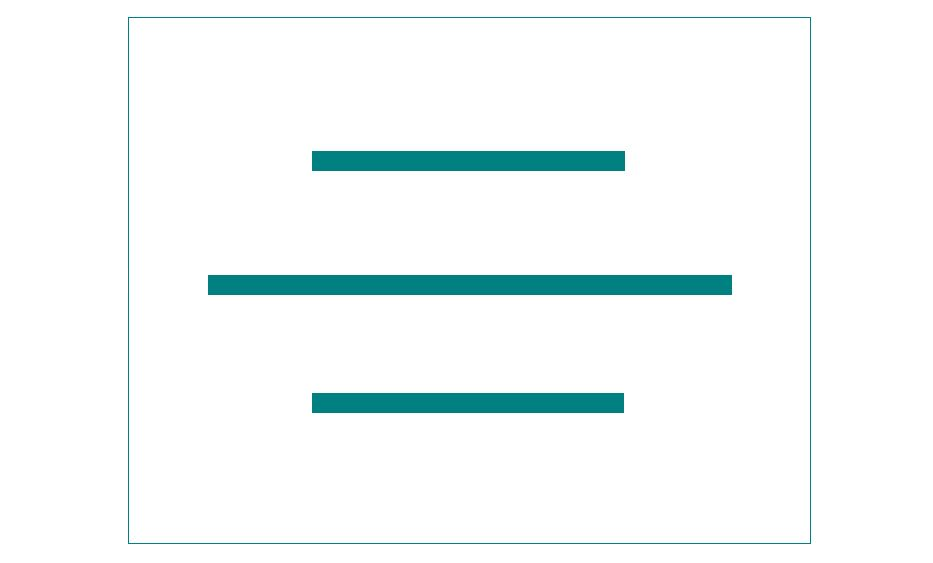
Symmetriakutsu määrittää keskitason, jonka ympärille piirteen molemmat osat sijoitetaan yhtä etäällä. Kummankin puolen kahden pisteen keskipisteen on oltava keskitason ympärille asetetun toleranssialueen sisällä.
Symmetriakutsu ei ole kovin yleinen. Sen käyttömahdollisuudet ovat hyvin rajalliset, ja sitä on myös vaikea tarkastaa. Lopullisen symmetrian tarkastamiseen tarvitaan CMM.
Tosi sijainti
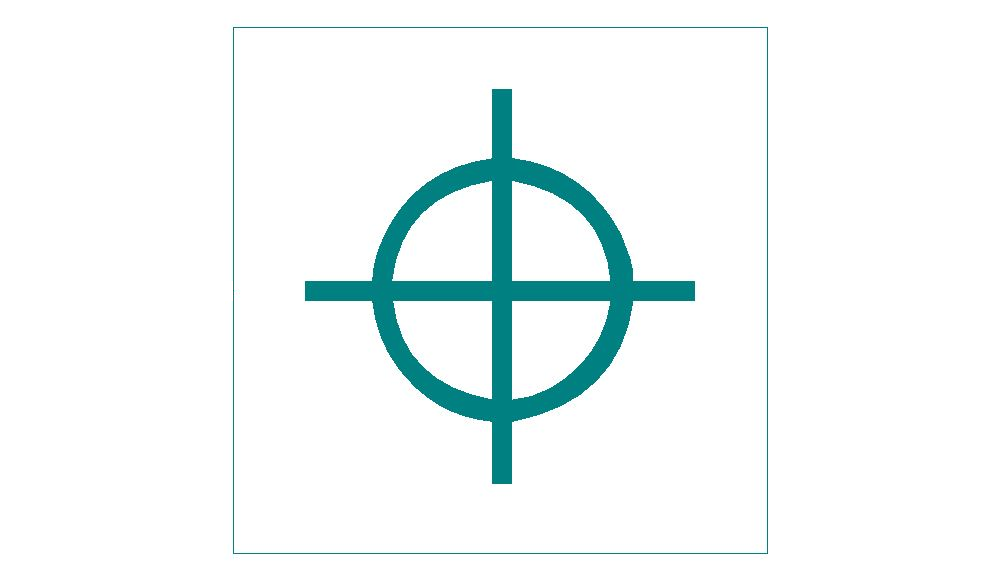
Tosi sijainti (tunnetaan yleisesti nimellä position) on erittäin hyödyllinen callout, ja sitä käytetään laajalti GD&T:ssä.
Positio määrittelee, kuinka paljon piirteen todellinen sijainti voi poiketa sen suunnitellusta sijainnista. Määritelmä sisältää vertailutason, johon mittaus liittyy.
Se sisältää usein vinoneliömerkin (⌀) korostaakseen, että toleranssialue on ympyrä eikä vain X- ja Y-akseli (josta puhuimme artikkelin alussa GD&T:n luomisen syynä alun perin).
Tässä on hieno video, jossa näytetään, miten toleransseja käytetään piirustuksessa käyttäen todellista sijaintia:
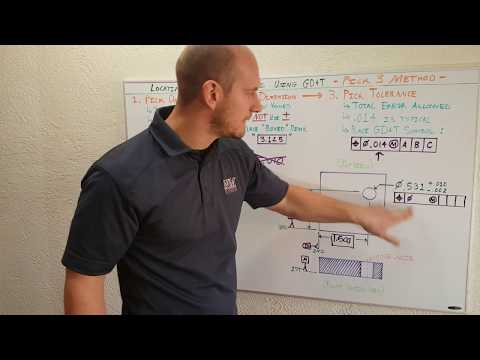
How to Apply GD&T Position Tolerance to a Hole
Runout Controls
Käytämme runout Controls -ohjaimia mittaamaan kappaleen piirteen poikkeamaa sille määritetystä sijainnista suhteessa vahvistettuun datumiin. Tätä ohjausta käytetään pyöreille piirteille. Se mittaa olennaisesti sen aaltoilua pyörittämällä piirrettä kiinteän kiintopisteen ympärillä.
Poikkeaman säätöjä on kahta tyyppiä.
Ympyräpoikkeama

Ympyräpoikkeama toimii kahdessa dimensiossa erilaisten kappaleen piirteiden muodon, sijainnin ja orientaation ohjaamiseksi. Tälle 2D-kutsukierrolle on osoitettava vertailuakseli näiden piirteiden tarkistamiseksi.
GD&T-jargonissa ympyräjuoksu tunnetaan yleisesti nimellä runout. Runout mittaa pintaelementtien poikkeamaa pyörimällä.
Se tarkoittaa, että esimerkiksi akselia pyöritetään sen vertailuakselilla ja esillä oleva elementti mitataan toleranssia varten. Se hallitsee myös muotoa, sijaintia ja orientaatiota. Mutta sen sijaan, että tarkistettaisiin yksittäisiä poikkileikkauksia (kuten ympyräjuoksussa), tarkistetaan koko pinta. Näin ollen kokonaiskierron käyttö antaa meille tiukemman kontrollin piirteen ominaisuuksiin.
Tarkastus
Kaikilla teollisuudenaloilla voi olla ongelmallista, jos valmistusprosessi ei täytä suunnittelumäärityksiä. Joissakin tapauksissa asiakkaiden henki voi olla vaarassa, kun taas toisissa tapauksissa tuotteen takaisinveto voi johtaa valtaviin rahallisiin tappioihin.
Kaikkakaan tulokset eivät ole niin huonoja, yrityksen maine riippuu suuresti sen tuotteiden ja palveluiden laadusta.
GD&T standardoi tarkastusprosessin tuomalla tarkastajat samalle tasolle suunnittelijan kanssa. Tämä poistaa monia esteitä. Mutta GD&T on laaja aihe.
Kuten olemme nähneet, GD&T:llä voidaan valvoa useita erilaisia geometrisia ominaisuuksia, jotka eroavat toisistaan hyvin paljon. Tästä erilaisuudesta johtuen jokaisen ominaisuuden tarkastaminen edellyttää erityistä menetelmää, työkalua ja taitoa.
Joitakin näistä ominaisuuksista voidaan mitata yksinkertaisimmilla työkaluilla, kun taas toisia on mahdotonta mitata ilman kehittyneitä laitteita, kuten koordinaattimittauskonetta (CMM).
Tarkastajat tarvitsevat tietoa ja taitoa käyttää erilaisia mittaustyökaluja, kuten mittakelloja, mikrometrejä, nanometrimittareita, pintalevyjä ja koordinaattimittauskoneita, voidakseen tarkastaa osien tarkkuuden tyydyttävästi.