Les ingénieurs utilisent des logiciels de CAO pour concevoir toutes les pièces et composants nécessaires au projet. Dans le domaine numérique, il est facile d’atteindre la perfection. Dans la vie réelle, la fabrication n’est jamais précise à 100%.
Parfois, des écarts de quelques millimètres par rapport aux dimensions de base peuvent être absolument parfaits. Dans le même temps, deux composants s’accouplant pourraient nécessiter une précision extrêmement élevée.
Pour maintenir l’écart attendu dans une plage prédéfinie, il est possible d’utiliser des tolérances d’ingénierie. Les tolérances dimensionnelles sont très courantes mais il manque des moyens pour communiquer certains aspects très importants de la fabrication. C’est là qu’intervient le GD&T, ou dimensionnement géométrique &tolérance.
C’est une forme de description des dimensions et des tolérances d’une manière totalement nouvelle. En utilisant un langage commun de symboles d’ingénierie, il permet de repérer facilement toutes les informations nécessaires.
- Qu’est-ce que le GD&T ?
- Pourquoi mettre en œuvre la GD&T ?
- Un assemblage parfait
- Système commun pour expliquer l’intention de conception
- Economie de temps et d’argent
- Que prendre en considération ?
- Intelligibilité du dessin
- Tolérances serrées uniquement lorsque cela est nécessaire
- GD&T Caractéristiques &Symboles
- Dimensions nominales
- Cadre de contrôle des caractéristiques
- Flèche de tête
- Symbole de caractéristique géométrique
- Chambre de tolérance des caractéristiques
- Datums
- Modificateurs de condition matérielle
- Modificateur de condition matérielle maximale
- Modificateur de condition de moindre matériau
- Qu’importe la taille de la caractéristique (RFS)
- Datums et Feature Callouts
- Symboles GD&T
- Contrôle de forme
- Droite
- Platitude
- Circularité
- Cylindricité
- Contrôles de profil
- Profil de ligne
- Profil de surface
- Contrôles d’orientation
- Angularité
- Parallélisme
- Perpendicularité
- Contrôles de localisation
- Concentricité
- Symétrie
- Position réelle
- Comment appliquer la tolérance de position GD&T à un trou
- Contrôles de faux-rond
- Le faux-rond circulaire
- Flux total
- Inspection
Qu’est-ce que le GD&T ?
C’est un système de symboles et de normes utilisé par les ingénieurs pour fournir des informations de fabrication à l’équipe de production.
Les raisons d’utiliser le dimensionnement et le tolérancement géométriques (GD&T) sont :
- Il garantit que les pièces qui s’accouplent s’emboîtent bien
- Le langage universel fonctionne peu importe avec qui vous travaillez
- Les tolérances donnent une limite aux conditions les plus défavorables
- Définit les processus de production et d’inspection
Stanley Parker est crédité d’être l’ingénieur à l’origine du développement du système GD&T en 1938.
Avant cela, toutes les fonctionnalités n’utilisaient que les axes X-Y pour déterminer la position d’un trou, par exemple. Donner une tolérance de position à cette échelle signifie que la position du trou circulaire peut s’écarter de manière rectangulaire de l’endroit prévu.
Pour autant, nous voudrions en fait que la zone de tolérance soit un cercle, car cela permet une mesure uniforme dans tous les angles, alors qu’un rectangle est plus long vers les coins et plus court vers les côtés.
Alors que Parker s’en est rendu compte, il a commencé à travailler sur le nouveau concept qui a été adopté comme norme d’ingénierie militaire dans les années 50.
Aujourd’hui, le GD&T est une partie importante de l’ingénierie, en particulier lors de la création de pièces qui nécessitent des services d’usinage CNC. La norme américaine décrivant les caractéristiques est ASME Y14.5-2018 et l’équivalent européen est ISO 1101-2017.
GD&T se concentre uniquement sur la géométrie du produit. Les dimensions linéaires, la rugosité de surface, les filetages, etc. ne font pas partie de cette norme.
Pourquoi mettre en œuvre la GD&T ?
Nous disposons effectivement de méthodes traditionnelles pour désigner les dimensions et les tolérances. Alors, quel est le besoin de dimensionnement et de tolérancement géométrique ?
Le dimensionnement et le tolérancement géométrique (GD&T) offre des avantages uniques par rapport aux méthodes régulières. Voyons quels sont ces avantages.
Un assemblage parfait
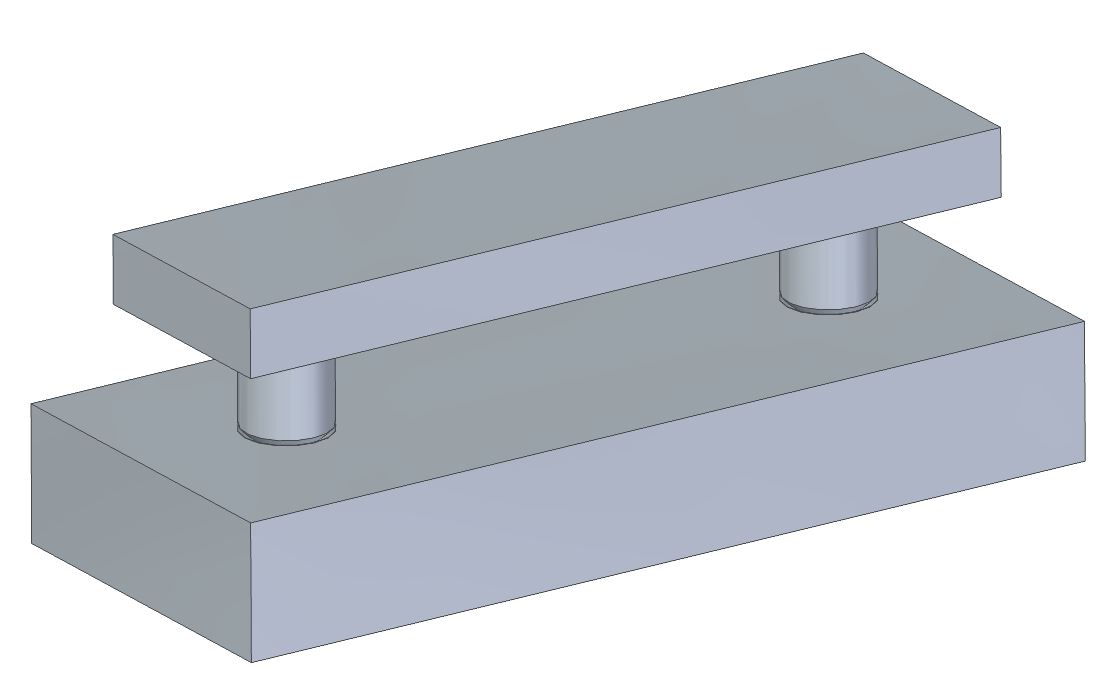
L’inconvénient le plus important de l’utilisation de la cotation et du tolérancement traditionnels est qu’ils dénotent des informations individuelles sur les pièces et leurs caractéristiques. Cela ne garantit pas la façon dont nos pièces s’adapteront et fonctionneront au niveau de l’assemblage.
Ceci est important car la plupart des pièces ne sont pas utiles par elles-mêmes. Prenons l’exemple d’une bielle. En soi, elle ne nous apporte aucun avantage. Mais lorsque nous la connectons au vilebrequin et au piston, elle devient un peu plus utile, car elle convertit le mouvement linéaire du piston en un mouvement de rotation du vilebrequin.
Lorsque cet ensemble devient une partie d’un ensemble plus grand comme un moteur diesel, il peut finir comme une partie d’un générateur qui nous fournit de nombreuses utilisations.
Il est donc crucial que nos pièces s’accouplent bien entre elles. C’est pourquoi nous avons besoin de GD&T. En l’utilisant, nous pouvons être sûrs à 100 % que nos pièces s’adapteront les unes aux autres et fonctionneront exactement comme il faut.
Système commun pour expliquer l’intention de conception
GD&T fournit également au concepteur une plateforme pour transmettre son intention de conception à tous les départements concernés. Ceux-ci comprennent :
- Fabrication
- Inspection
- Futurs concepteurs du département de conception qui reprendront le travail si l’équipe de conception initiale n’est pas disponible
Les définitions, le vocabulaire et les règles sont simples et universellement compréhensibles. Cela rend les symboles faciles à traduire pour chaque ingénieur et constitue un excellent moyen de transmettre l’intention du concepteur.
Economie de temps et d’argent
C’est l’avantage le plus important de l’utilisation de GD&T. L’utilisation de ce système réduit le gaspillage car il réduit le nombre de cycles de conception-fabrication-test d’ajustement.
C’est parce que les pièces fabriquées s’ajustent bien dès la première tentative et par conséquent, le nombre de rejets sera faible. L’utilisation d’un langage commun réduit également l’effort nécessaire à l’inspection.
Obtenez votre devis de fabrication en quelques secondes
-
Demande de devis en quelques secondes
-
Délais courts
-
Livraison par Fractory
Obtenez un devis
Que prendre en considération ?
La cotation et le tolérancement géométriques sont un système plus puissant par rapport aux tolérances traditionnelles. Mais il ne fonctionne que si tous les départements (conception, ingénierie, fabrication) sont bien versés dans la lecture et l’interprétation de l’information.
Par conséquent, lors de la création de dessins d’ingénierie et du tolérancement de diverses caractéristiques de pièces, il est important de suivre les directives/conventions recommandées pour le bénéfice de tous ceux qui interagiront avec le dessin à n’importe quelle étape du développement du produit.
L’observation de celles-ci garantit que le dessin est standardisé et que tout le monde est sur la même page lorsqu’il s’agit des spécificités du dessin. Certaines de ces bonnes pratiques sont les suivantes.
Intelligibilité du dessin
C’est sans doute la qualité la plus importante d’un dessin. L’intelligibilité fait référence à la clarté avec laquelle les caractéristiques des pièces sont dessinées et les tolérances sont indiquées dans le dessin. Voici quelques façons d’améliorer l’intelligibilité d’un dessin :
- Dessinez de vrais profils pour toutes les caractéristiques de la pièce.
- Indiquez les dimensions et les tolérances à l’extérieur du dessin (pas en haut). Utilisez efficacement les espaces blancs.
- Le sens de lecture doit être constant. Un lecteur doit pouvoir lire toutes les dimensions en tenant le dessin à la verticale.
- Espacez les dimensions des caractéristiques parallèles de la pièce.
- Expliquez brièvement la pièce et sa fonction.
- Spécifier les angles uniquement lorsqu’ils ne sont pas des angles droits (90°).
Tolérances serrées uniquement lorsque cela est nécessaire
Sauf si l’ajustement ou la fonction d’une pièce l’exige, les tolérances doivent être aussi lâches que possible. Cela permet de réduire le coût de fabrication et le délai d’exécution. Nous recommandons de laisser le choix de la méthode de fabrication aux machinistes.
Le concepteur doit également mentionner la tolérance générale pour un dessin. Celle-ci fait office de tolérance standard pour toutes les caractéristiques de la pièce. Pour les caractéristiques de la pièce ayant une limite de tolérance différente, le concepteur doit les mentionner aux positions appropriées.
Ces limites de tolérance spécifiques prévaudront sur les tolérances générales. Lorsque vous spécifiez des limites de tolérance spéciales, préférez les caractéristiques fonctionnelles aux autres caractéristiques.
GD&T Caractéristiques &Symboles
Le langage GD&T est capable de définir à peu près toutes les qualités nécessaires pour assurer un assemblage parfait.
Le système utilise un certain nombre de symboles à cette fin. Pour utiliser correctement ces symboles d’ingénierie sur les dessins, nous devons d’abord nous familiariser avec certains éléments de base de ce système.
Nous pouvons commencer par les différentes définitions, terminologies et règles avant d’en venir aux symboles GD&T.
Dimensions nominales
Une dimension nominale est la taille caractéristique du vrai profil. C’est la dimension exacte que l’on voudrait atteindre idéalement. Les spécificités des caractéristiques telles que la taille, l’orientation, l’emplacement par rapport à un point de référence ont une dimension nominale que les machinistes ciblent.
Sur un dessin, elles sont représentées dans une boîte. Elle peut être représentée sous la forme d’un numéro ou d’une norme populaire comme l’ASME.
Cadre de contrôle des caractéristiques
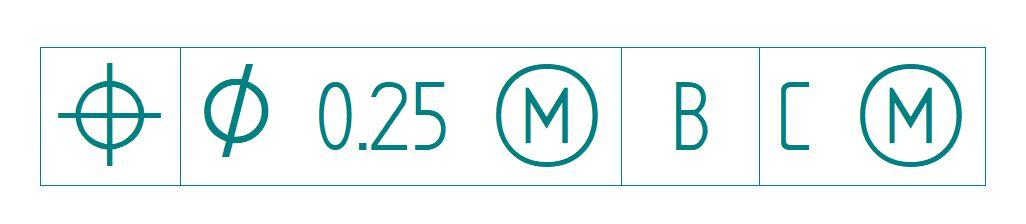
Ce cadre contient des informations sur les spécificités de la pièce. Il contient différents compartiments où chaque compartiment définit un attribut spécifique de la caractéristique de la pièce. D’un seul coup d’œil, le cadre de contrôle des caractéristiques transmet les informations requises pour l’usinage et le contrôle.
Le cadre de contrôle des caractéristiques peut être divisé en 4 parties principales comme suit.
Flèche de tête
Cette flèche marque la caractéristique de la pièce sous contrôle. Si elle mène à une surface, la surface est sous contrôle géométrique. Si elle marque une dimension diamétrale, alors GD&T contrôle l’axe. Cette flèche peut ne pas être présente dans certains cas.
Symbole de caractéristique géométrique
Le premier compartiment (en partant de la gauche) contient le symbole de caractéristique géométrique. C’est ici que l’on spécifie la caractéristique géométrique. Au total, il existe 14 types de tolérances géométriques en fonction du nombre de symboles, et 15 lorsqu’elles sont classées.
Les différents types de caractéristiques géométriques sont le contrôle de forme, le contrôle de profil, le contrôle d’emplacement, le contrôle d’orientation, etc. Nous allons plonger plus profondément dans chaque catégorie plus tard.
Chambre de tolérance des caractéristiques
Le 2e bloc contient un maximum de 3 (parfois 2 ou 1) symboles différents.
Le premier symbole indique le type de zone de tolérance. Un symbole de diamètre (⌀) signifie une zone diamétrale (zone de tolérance cylindrique). Pour spécifier une zone sphérique, le symbole est la lettre ‘S’ suivie du symbole de diamètre (⌀). En l’absence de symbole, on suppose une zone large totale.
Le deuxième symbole du 2ème bloc donne la valeur de la zone de tolérance en mm. Cette valeur doit toujours être présente dans le 2e bloc.
Le troisième symbole de ce bloc est le modificateur de la tolérance. Ce modificateur de matériau n’est présent que lorsque la caractéristique a une taille, par exemple, un trou. Des exemples de modificateurs de matériau sont MMC (Maximum material condition) et LMC (Least material condition). De plus amples informations sur les différents modificateurs disponibles seront abordées plus loin dans l’article.
Datums
Le troisième bloc donne des informations sur le ou les datums avec un minimum de 1 et un maximum de 3 datums. Dans le cas de 3 datums, ils sont appelés datums primaires, secondaires et tertiaires, chacun étant représenté enfermé dans une case différente (l’image ci-dessus en compte 2, par exemple). Ce bloc peut également contenir un modificateur de matériau.
Toutes les informations ci-dessus nous aident à comprendre comment lire un cadre de contrôle de caractéristiques. Afin de mieux comprendre comment la tolérance peut être ajustée à l’aide de modificateurs de condition matérielle, nous devons nous familiariser avec les différentes options.
Modificateurs de condition matérielle
Les modificateurs de condition matérielle transmettent l’intention lorsque la tolérance s’applique à une caractéristique à une taille de caractéristique spécifique. Chaque fois que nous donnons des tolérances à une caractéristique quelconque, cela établit deux conditions matérielles
- Condition matérielle maximale
- Condition matérielle minimale
Considérez un arbre de diamètre 100 mm. Lors de la fabrication, si nous lui donnons une tolérance de ±0,2 mm, alors à 100,2 mm, l’arbre contiendra la quantité maximale de matière. C’est ce que nous entendons par condition matérielle maximale.
En revanche, le même arbre, lorsqu’il est fabriqué avec un diamètre de 99,8 mm, contiendra la plus petite quantité de matière. Ces limites sont appelées conditions matérielles.
Les tolérances géométriques peuvent être appliquées à une caractéristique de 3 façons différentes. Ce sont les suivantes :
- Condition matérielle maximale
- Condition matérielle minimale
- Qu’importe la taille de la caractéristique
Modificateur de condition matérielle maximale
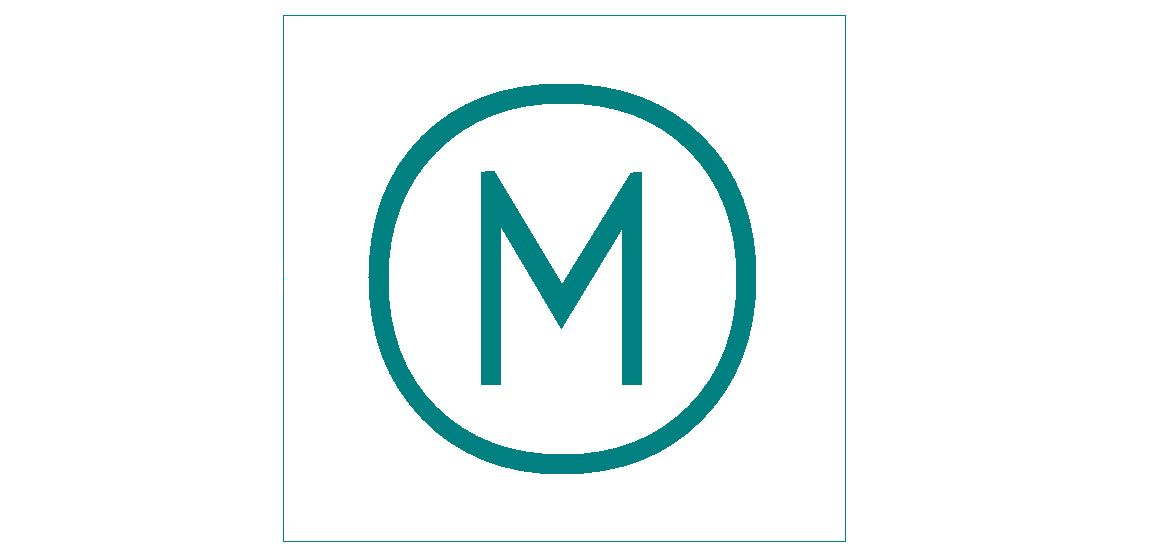
Nous représentons cette condition par un « M » encerclé après la valeur de la tolérance dans le compartiment de contrôle de la caractéristique. La caractéristique contient le matériau maximal à cette taille de caractéristique.
Pour les FOS (Feature Of Size) externes, comme le diamètre d’un arbre, MMC représente la plus grande taille. Pour les FOS internes, comme le diamètre d’un trou, MMC représente la plus petite taille possible dans les limites de tolérance indiquées, car un trou plus petit signifie qu’il restera plus de matière.
Lorsque nous devons appliquer une tolérance géométrique à la condition de matériau maximale, nous mentionnons cette condition dans le cadre de contrôle de la caractéristique.
Modificateur de condition de moindre matériau
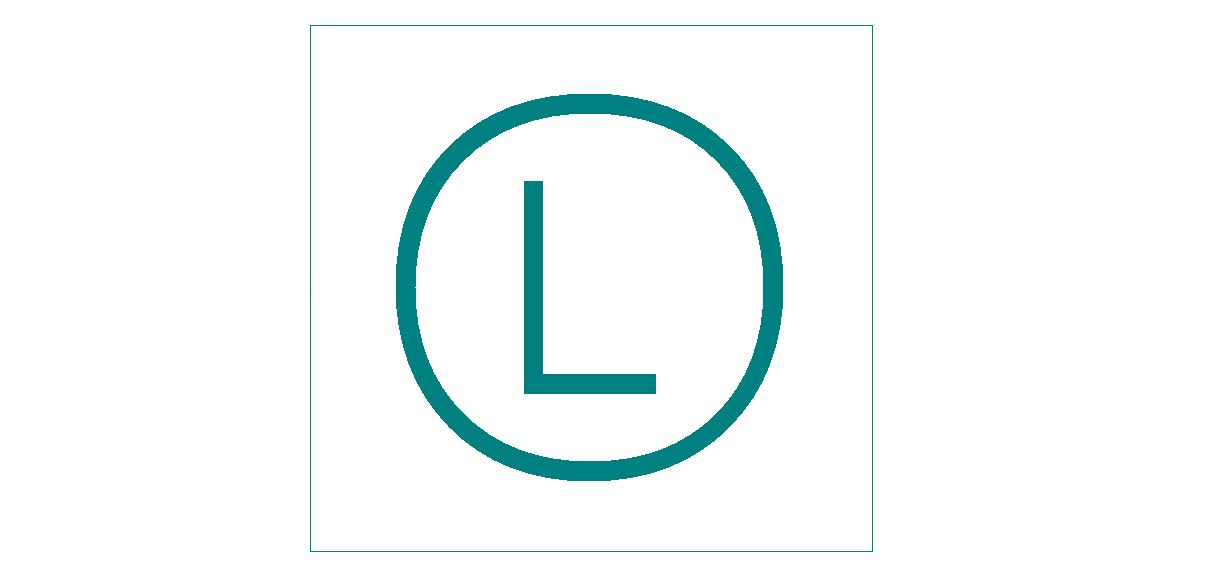
LMC est la condition où le matériau contient la plus petite quantité de matériau.
Pour les FOS externes, ce sera la plus petite taille possible dans les limites indiquées. Et pour le FOS interne, ce sera la plus grande taille possible.
Nous représentons ce modificateur par la lettre « L » dans un cercle. Cette caractéristique supprime un excès de matière et donc de poids. Pour appliquer des tolérances géométriques à cette condition, nous utilisons son symbole dans le cadre de contrôle des caractéristiques.
Qu’importe la taille de la caractéristique (RFS)
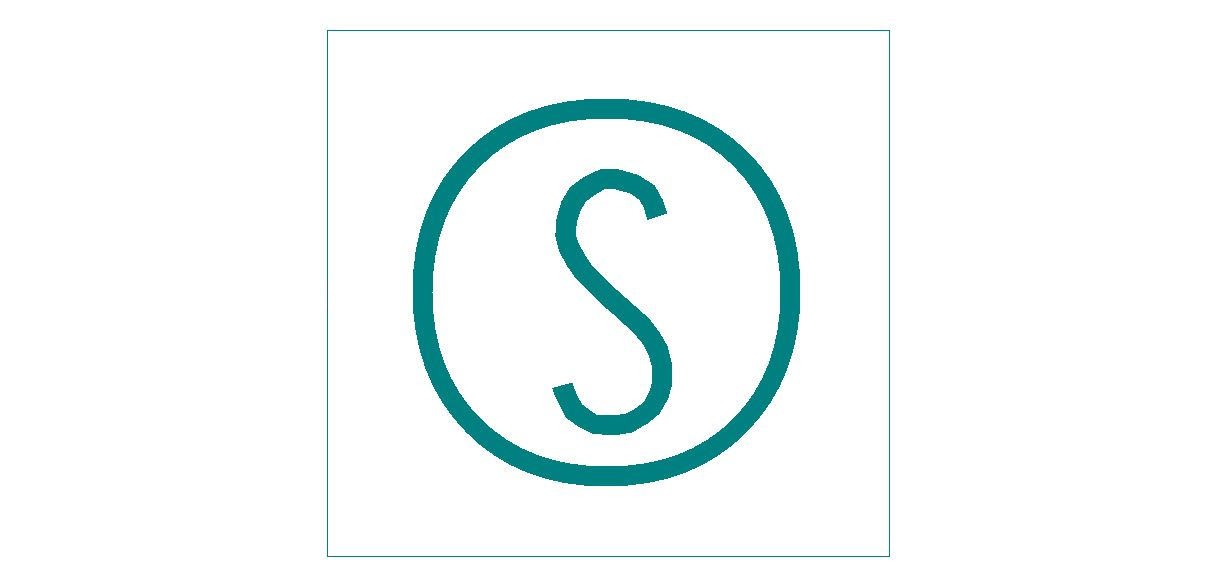
Lorsque les tolérances géométriques données sont appliquées à n’importe quel incrément de taille de FOS, nous l’indiquons par RFS. Le symbole pour RFS était la lettre « S » enfermée dans un cercle, mais il n’est plus nécessaire car RFS est considéré comme la condition par défaut maintenant, et n’a pas besoin d’un symbole.
Datums et Feature Callouts
Les datums sont des points de référence pour mesurer les tolérances dimensionnelles. Il peut s’agir d’un point, d’une ligne ou d’un plan. À l’aide d’un datum, nous établissons des cadres de référence de datum (DRF). Le DRF est essentiellement un système de coordonnées 3D qui nous aide à définir les positions de toutes les autres caractéristiques par rapport au DRF.
Il existe 6 degrés de liberté (3 translationnels et 3 rotationnels) que nous devons contrôler pour fabriquer et inspecter les pièces efficacement. Nous utilisons le DRF pour établir ces degrés de liberté.
Les caractéristiques du datum sont les caractéristiques réelles de la pièce telles que les trous et les fentes. Ils peuvent présenter des variations par rapport aux positions souhaitées.
Parmi tous les éléments de référence, nous accordons la plus grande préférence à ceux qui s’accouplent avec d’autres pièces de l’assemblage. Nous pouvons mentionner plus d’une caractéristique de référence dans notre cadre de contrôle des caractéristiques. Selon la séquence des DRF dans le cadre de contrôle des caractéristiques, les pièces sont accouplées aux DRF par ordre décroissant d’importance.
Symboles GD&T
Plus de 14 symboles GD et T sont disponibles pour représenter différentes caractéristiques géométriques des caractéristiques. Ces symboles nous aident à spécifier ces caractéristiques comme des exigences pour le produit final.
Nous plaçons ces symboles dans le premier compartiment du cadre de contrôle de la caractéristique. Nous allons examiner ces types de contrôle de tolérance.
Contrôle de forme
Comme son nom l’indique, le contrôle de forme concerne la forme finale ou la forme de la caractéristique. Nous définissons les contrôles de forme pour limiter l’écart de la tolérance géométrique par rapport à sa forme idéale. Voici quelques caractéristiques populaires de contrôle de forme.
Droite
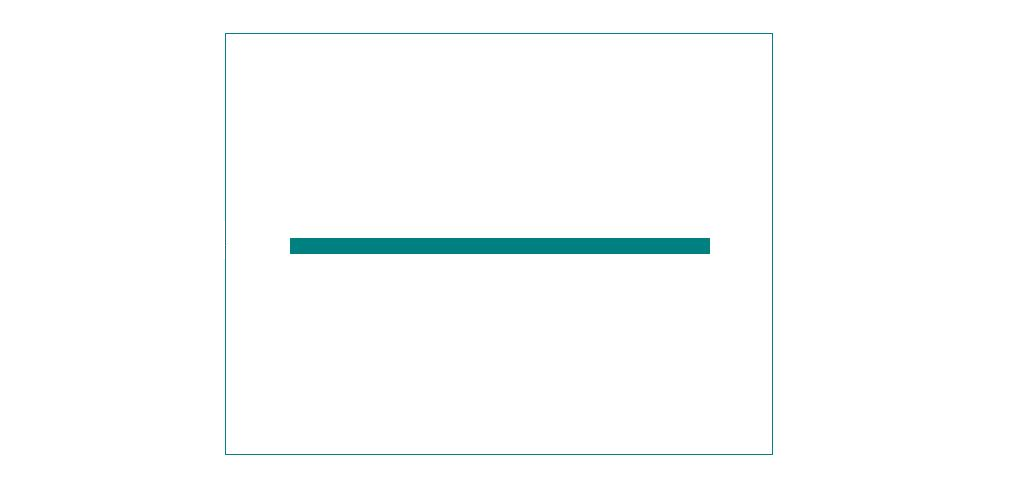
Pour indiquer la caractéristique de rectitude d’une caractéristique (comme un axe ou une surface), nous utilisons son symbole (une ligne droite horizontale) dans le premier compartiment.
La rectitude de surface peut s’appliquer à des surfaces planes comme le côté d’un bloc ou à des surfaces courbes comme le côté d’un cylindre dans la direction de l’axe. Elle définit la variation admissible d’une ligne (2 dimensions) sur la surface dans une tolérance spécifiée.
La rectitude axiale s’applique généralement à l’axe d’un arbre ou d’un trou, par exemple. La jauge go/no go est l’outil d’inspection utilisé dans le processus de vérification de la conformité de la pièce aux exigences.
Platitude
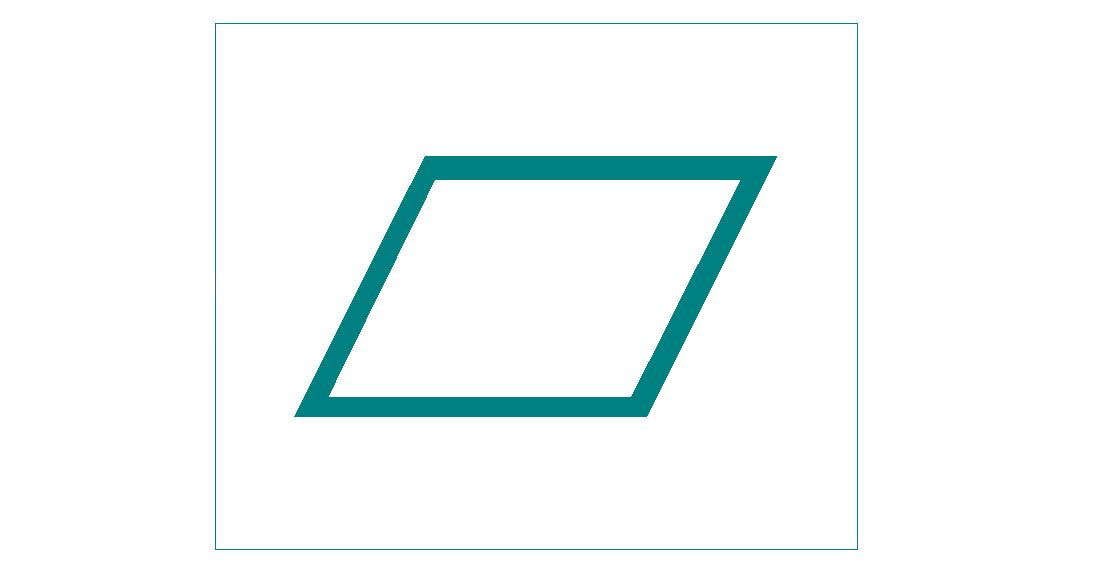
On utilise cette caractéristique pour des caractéristiques telles que la face d’une pièce. Le symbole de la planéité est un parallélogramme incliné vers la droite. La différence entre le point le plus haut et le point le plus bas d’une surface plane est sa planéité.
Le symbole de planéité ne nécessite pas de points de référence, car il indique seulement une plage de tolérance à l’intérieur de laquelle toute la surface d’une pièce doit se conformer en 3 dimensions.
Une jauge de hauteur est utilisée pour vérifier les résultats. Elle touche différentes zones de la surface pour déterminer que tous les points sont à l’intérieur de la zone de tolérance.
Circularité
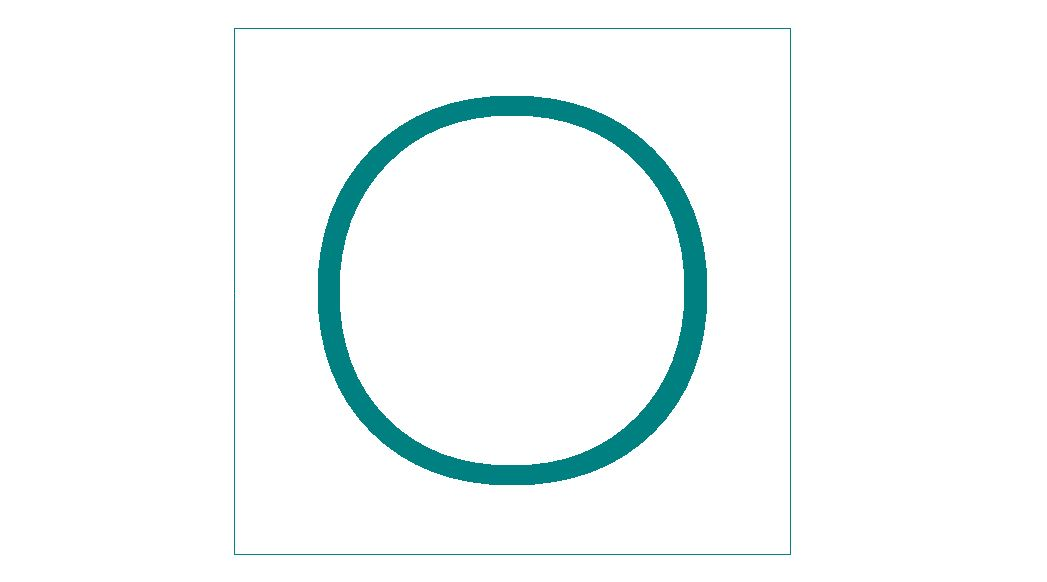
La circularité d’une caractéristique montre à quel point la circonférence de la pièce doit être proche d’un cercle parfait. Il utilise 2 cercles concentriques sur un plan perpendiculaire à l’axe de la pièce pour définir la plage de tolérance appropriée en 2D. Chaque point des mesures finales doit se situer entre les cercles.
Cette caractéristique est représentée par un cercle dans le premier compartiment du cadre de contrôle des caractéristiques.
Cylindricité
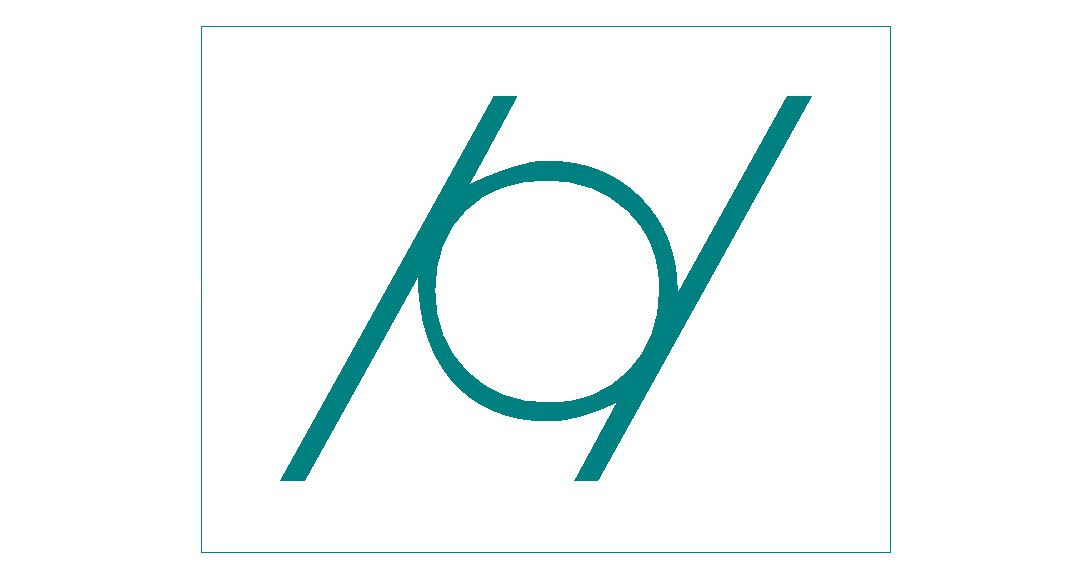
La cylindricité est essentiellement la circularité en 3D, ce qui signifie qu’elle s’étend sur toute la longueur de la pièce.
Cette caractéristique décrit également d’autres caractéristiques cylindriques telles que son effilement, sa rectitude et son arrondi. C’est pourquoi cette caractéristique est également coûteuse à inspecter.
Contrôles de profil
Nous utilisons des contrôles de profil pour contrôler la zone de tolérance 3D autour de la caractéristique. Cette fonctionnalité nous aide à donner des limites de tolérance aux courbes et formes avancées.
Une fonctionnalité qui est bonne pour les courbes avancées doit naturellement fonctionner aussi bien avec des courbes plus simples. Cela rend les contrôles de profil extrêmement polyvalents. C’est pourquoi certains concepteurs recommandent d’abandonner tous les autres contrôles et de ne travailler qu’avec des contrôles de profil.
Ces contrôles forment une limite de tolérance autour de la courbe avancée en la mimant des deux côtés. Il empêche alors tout point de la courbe caractéristique de sortir de la limite de tolérance. Les contrôles de profil sont de deux types.
Profil de ligne
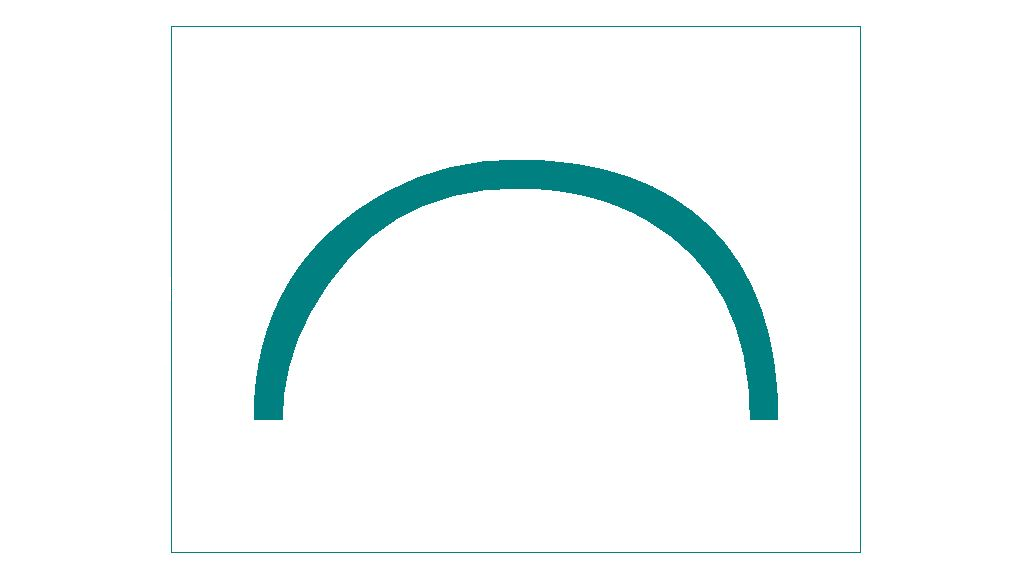
Le profil de ligne établit une zone de tolérance autour de sections 2D variables de la pièce. Il contrôle les éléments de ligne individuels d’une caractéristique de la pièce.
Le contrôle du profil de ligne trace la courbe idéale aux limites de tolérance des deux côtés. Tous les points de la courbe de la pièce doivent se situer dans ces limites.
Profil de surface
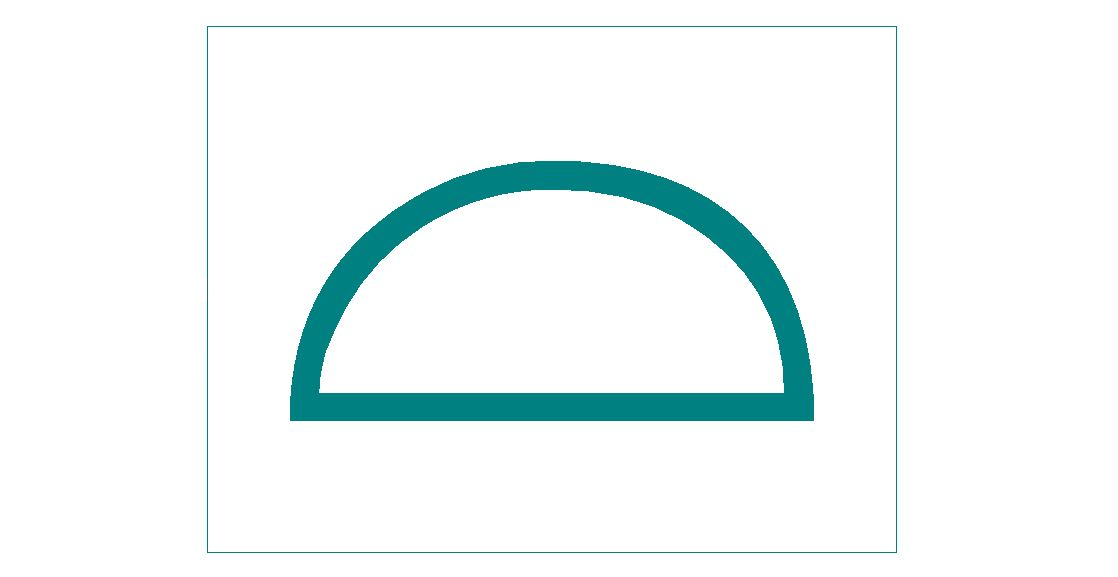
Le contrôle du profil de surface est plus populaire par rapport au contrôle de ligne. Au lieu d’une zone de tolérance bidimensionnelle, le contrôle de profil de surface crée une zone 3D autour d’une surface.
Tous les points sur la surface de la table doivent se trouver dans les deux plans virtuels.
Contrôles d’orientation
La tolérance d’orientation contrôle l’orientation d’une caractéristique par rapport à un point de référence défini. Il existe trois types de contrôles d’orientation dans GD&T.
Angularité
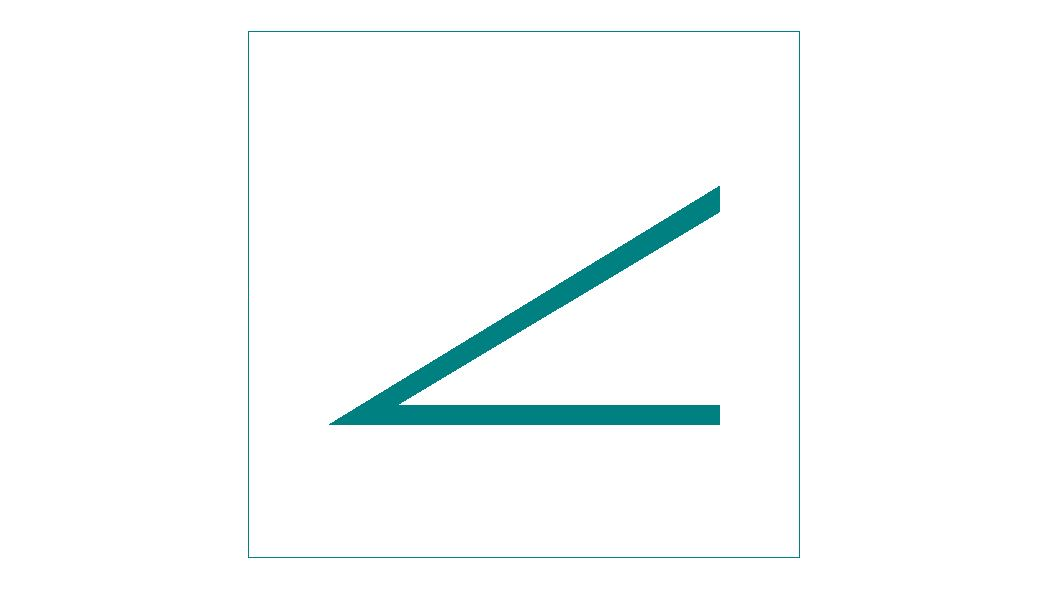
Le contrôle de l’angularité permet de contrôler l’angle d’une caractéristique par rapport au point de référence. Nous pouvons l’utiliser pour contrôler une ligne 2D, mais il est plus populaire pour garder les surfaces (3D) sous contrôle.
Ce type de contrôle serré maintient l’angle et la planéité de la surface et est recommandé pour les caractéristiques de pièces qui s’accouplent avec d’autres pièces à travers la surface angulaire.
Il est important de noter que la fonction d’angularité contrôle l’angle indirectement, n’étant pas essentiellement la même chose qu’une tolérance angulaire (par exemple +/- 2°). Plutôt, l’angle nécessaire est le résultat du respect des exigences dimensionnelles établies par ce contrôle.
Parallélisme
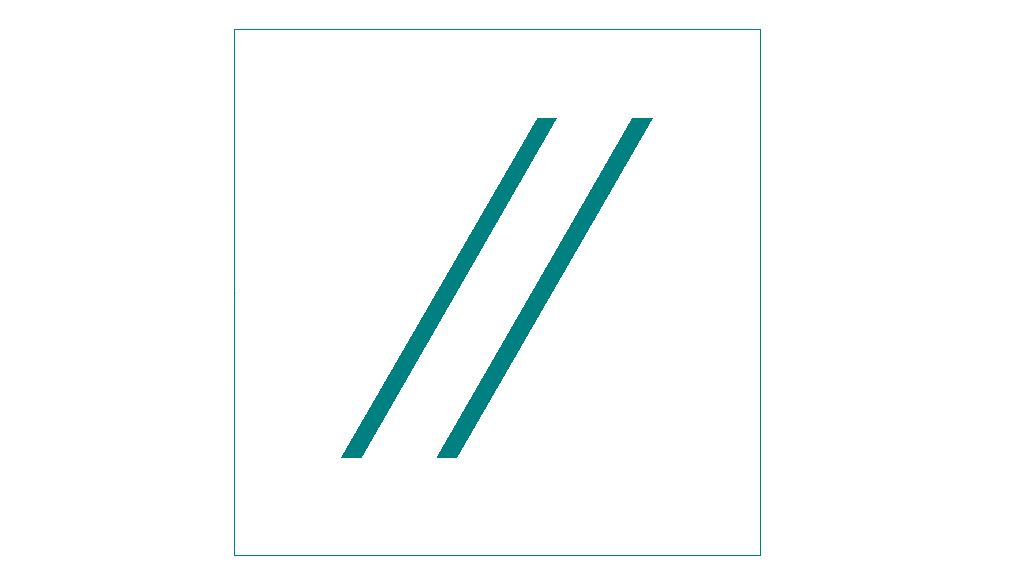
Le parallélisme est une forme raffinée de l’angularité. Ici, le point de référence est la surface que nous devons imiter et l’angle est fixé à 0°. Il existe 2 types de parallélisme : le parallélisme de surface et le parallélisme d’axe.
Nous pouvons choisir un axe ou une surface comme référence. Cela devient notre point de référence et nous le référençons dans le 3e bloc du cadre de contrôle de la caractéristique comme point de référence pour la caractéristique.
De manière similaire à l’angularité, elle ne contrôle pas l’angle réel mais le sécurise en posant les exigences sous la forme d’une zone de tolérance.
Perpendicularité
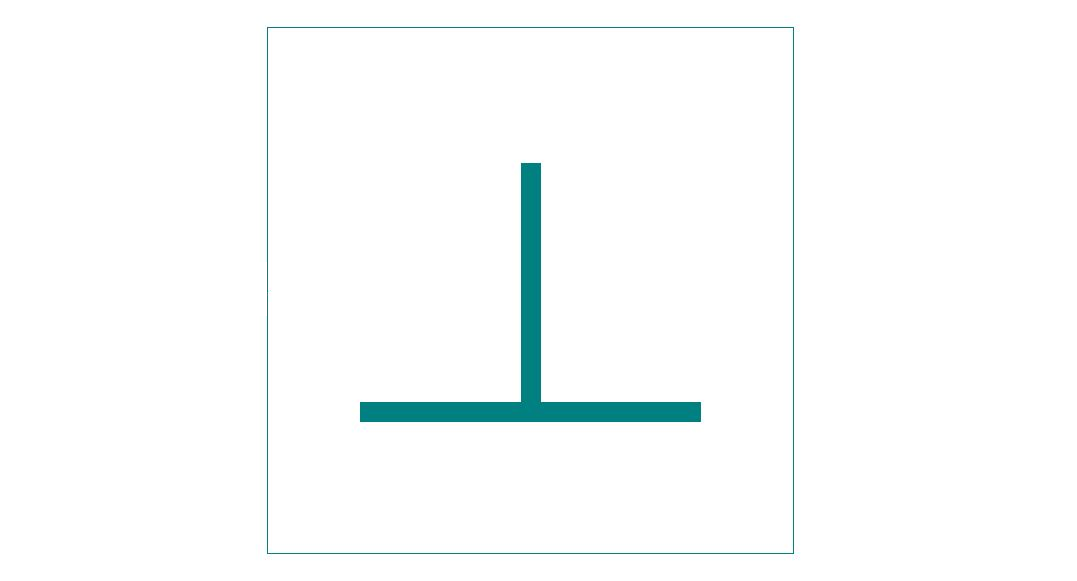
La perpendicularité est également une forme spécifique d’angularité où l’angle est fixé à 90°. C’est un contrôle délicat car il peut signifier deux types d’exigences très différentes.
Il y a la perpendicularité de surface ( Symbole:⟂), et puis il y a la perpendicularité d’axe (Symboles : ⟂+⌀).
La perpendicularité de surface spécifie qu’une surface ou une ligne doit être perpendiculaire à une surface ou une ligne de référence un peu comme l’angularité. Deux plans/lignes virtuels sont supposés autour de la surface cible pour le contrôle.
La perpendicularité de l’axe spécifie à quel point un axe doit être perpendiculaire au point de référence mentionné. Ceci est fait en érigeant un cylindre virtuel autour de l’axe cible sur une surface exactement parallèle à la surface du datum.
Contrôles de localisation
Le contrôle de tolérance de localisation est utilisé pour un contrôle serré de la position d’une caractéristique par rapport à un datum. Il existe quatre principaux types de contrôles d’emplacement.
Concentricité
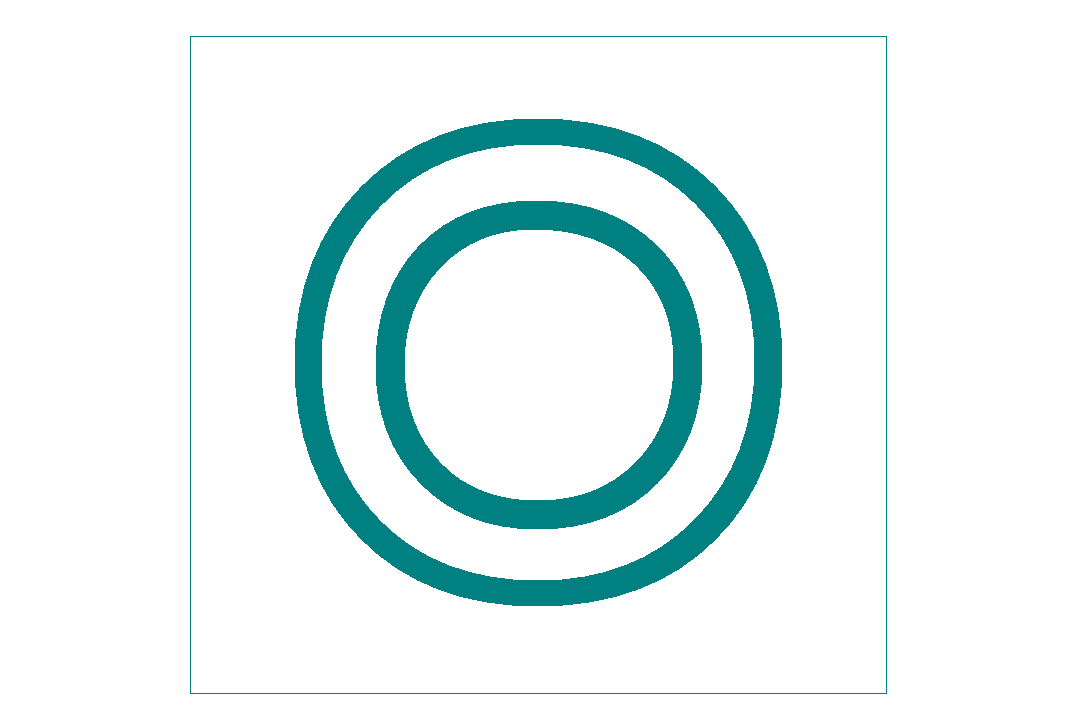
Le contrôle de concentricité, également appelé coaxialité (même si ce n’est pas exactement la même chose), maintient la concentricité des caractéristiques circulaires ainsi que des caractéristiques cylindriques.
Il fixe l’axe d’une pièce à l’axe d’une caractéristique référencée (axe de référence). Les axes des deux pièces sont déterminés comme étant aux points médians des pièces.
Cette commande peut entraîner une certaine confusion car les axes dérivent de mesures extérieures, plutôt que de leur placement réel.
La coaxialité crée une zone de tolérance 3D basée sur des mesures de surface dans laquelle la pièce doit se trouver.
Symétrie
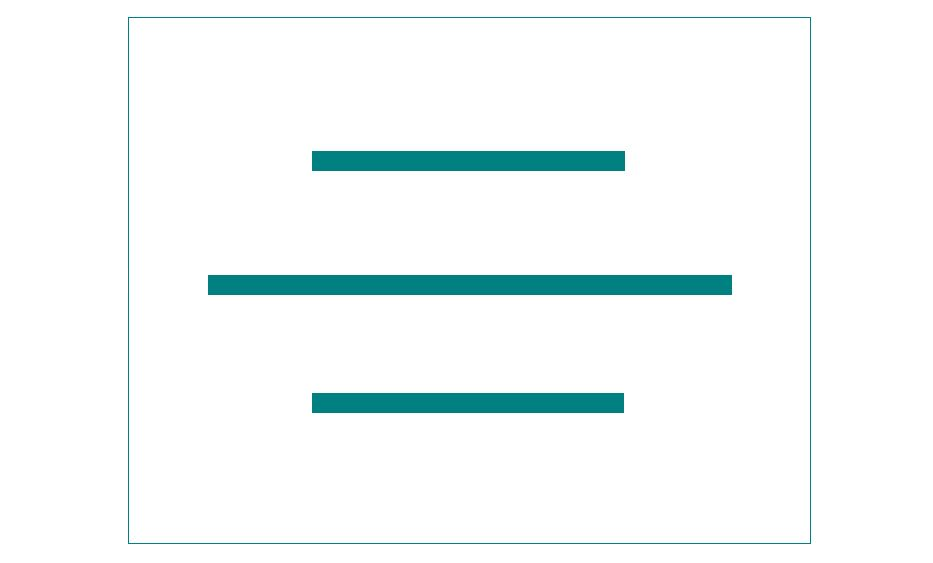
Le callout de symétrie établit un plan central autour duquel les deux parties de la caractéristique sont placées à distance égale. Le point médian des deux points de chaque côté doit se trouver dans la zone de tolérance établie autour du plan central.
Le callout de symétrie n’est pas très courant. Il a des utilisations très limitées et est également difficile à inspecter. Nous avons besoin d’une MMT pour inspecter la symétrie finale.
Position réelle
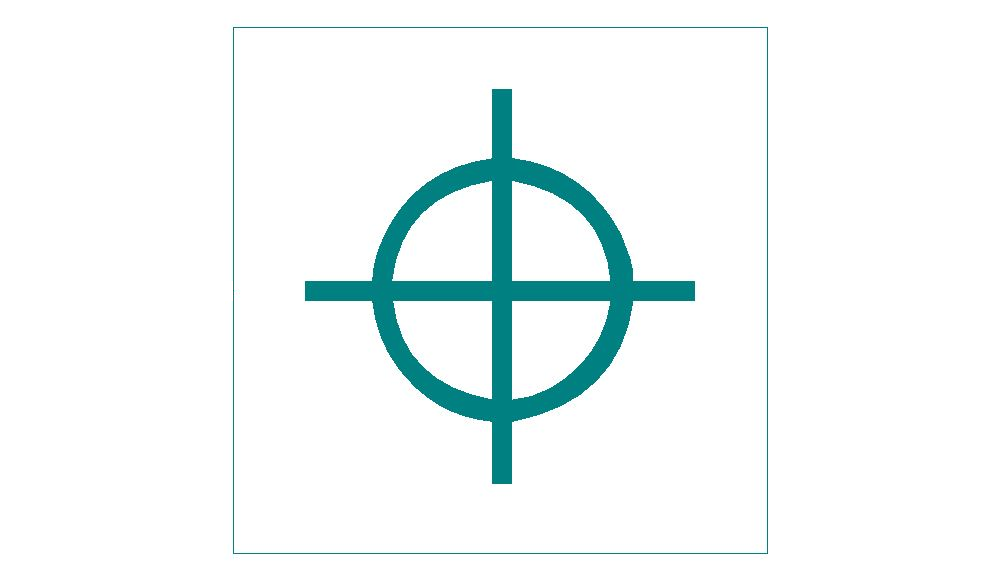
La position réelle (populairement connue sous le nom de position) est un callout très utile et trouve une utilisation extensive dans GD&T.
La position définit de combien la position réelle d’une caractéristique peut varier de sa position prévue. La définition comprend le plan de référence auquel la mesure se rapporte.
Elle comprend souvent un signe diamétral (⌀) pour mettre en évidence que la zone de tolérance est un cercle, plutôt que simplement les axes X et Y (dont nous avons parlé au début de l’article comme étant la raison de la création de GD&T en premier lieu).
Voici une excellente vidéo montrant comment utiliser les tolérances sur un dessin, en utilisant la position réelle :
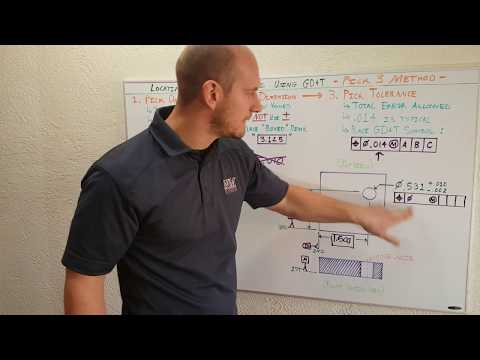
Comment appliquer la tolérance de position GD&T à un trou
Contrôles de faux-rond
Nous utilisons les contrôles de faux-rond pour mesurer la déviation d’une caractéristique de pièce par rapport à sa position assignée par rapport à un point de référence établi. Ce contrôle est utilisé pour les caractéristiques circulaires. Il mesure essentiellement son oscillation en faisant tourner la caractéristique autour du point de référence fixe.
Il existe deux types de contrôle de faux-rond.
Le faux-rond circulaire

Le faux-rond circulaire fonctionne en deux dimensions pour contrôler la forme, l’emplacement et l’orientation de diverses caractéristiques de la pièce. Cette callout 2D nécessite que nous lui attribuions un axe de référence pour contrôler ces caractéristiques.
Dans le jargon GD&T, le faux-rond circulaire est communément appelé faux-rond. Le runout mesure la déviation des éléments de surface par rotation.
Ce qui signifie que l’arbre, par exemple, est tourné par son axe de référence et l’élément caractéristique est mesuré pour la tolérance. Essentiellement, il limite les vibrations d’un arbre de travail pour assurer une plus longue durée de vie aux pièces connectées telles que les roulements.
Flux total
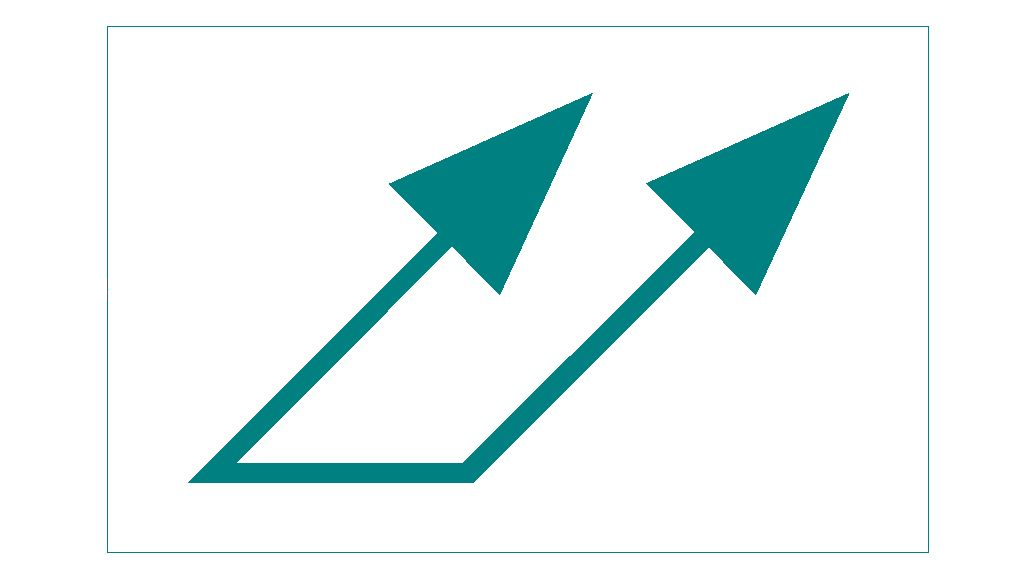
Le flux total est la contrepartie 3D du flux circulaire. Il contrôle également la forme, l’emplacement et l’orientation. Mais au lieu de vérifier les sections transversales individuelles (comme dans le faux-rond circulaire), il vérifie la surface entière. Ainsi, l’utilisation du faux-rond total nous donne un contrôle plus strict des caractéristiques de l’élément.
Inspection
Dans toutes les industries, l’incapacité du processus de fabrication à répondre aux spécifications de conception peut être problématique. Alors que dans certains cas, la vie des clients peut être en danger, dans d’autres cas, un rappel de produit pourrait entraîner d’énormes pertes monétaires.
Même si les résultats ne sont pas si mauvais, la réputation d’une entreprise repose fortement sur la qualité de ses produits et services.
GD&T standardise le processus d’inspection en faisant intervenir les inspecteurs sur la même plateforme que le concepteur. Cela élimine beaucoup d’obstacles. Mais le GD&T est un vaste sujet.
Comme nous l’avons vu, il existe un certain nombre de caractéristiques géométriques différentes, toutes très différentes les unes des autres, qui peuvent être contrôlées avec le GD&T. En raison de cette disparité, le contrôle de chaque caractéristique nécessite une méthode, un outil et une compétence spécifiques.
Certaines de ces caractéristiques peuvent être mesurées avec le plus simple des outils tandis que d’autres sont impossibles à mesurer sans un équipement avancé tel qu’une machine à mesurer tridimensionnelle (MMT).
Les inspecteurs devront avoir les connaissances et les compétences nécessaires pour utiliser divers outils de mesure tels que les comparateurs, les micromètres, les pieds à coulisse, les plaques de surface et les machines à mesurer tridimensionnelles pour inspecter la précision des pièces de manière satisfaisante.