Ingenieure verwenden CAD-Software, um alle erforderlichen Teile und Komponenten für ein Projekt zu entwerfen. In der digitalen Welt ist es einfach, Perfektion zu erreichen. Im wirklichen Leben ist die Fertigung nie 100%ig genau.
Manchmal können Abweichungen von wenigen Millimetern von den Grundmaßen absolut in Ordnung sein. Gleichzeitig können zwei zusammenpassende Komponenten eine extrem hohe Genauigkeit erfordern.
Um die erwartete Abweichung in einem vordefinierten Bereich zu halten, ist es möglich, technische Toleranzen zu verwenden. Maßtoleranzen sind sehr gebräuchlich, aber es fehlen Möglichkeiten, einige sehr wichtige Aspekte der Fertigung zu kommunizieren. Hier kommt GD&T, oder geometrische Bemessung &Toleranz, ins Spiel.
Es handelt sich um eine Form der Beschreibung von Maßen und Toleranzen auf eine völlig neue Weise. Durch die Verwendung einer gemeinsamen Sprache von technischen Symbolen können alle notwendigen Informationen leicht ermittelt werden.
- Was ist GD&T?
- Warum wird GD&T eingeführt?
- Perfekte Montage
- Gemeinsames System zur Erläuterung der Konstruktionsabsicht
- Spart Zeit und Geld
- Was ist zu beachten?
- Verständlichkeit der Zeichnung
- Genaue Toleranzen nur wenn nötig
- GD&T Merkmale & Symbole
- Nennmaße
- Funktionskontrollrahmen
- Führungspfeil
- Geometrisches Merkmalssymbol
- Merkmalstoleranzfach
- Bezugspunkte
- Materialbedingungsmodifikatoren
- Maximaler Materialbedingungsmodifikator
- Modifikator für die kleinste Materialbedingung
- Unabhängig von der Merkmalsgröße (RFS)
- Daten und Feature Callouts
- GD&T-Symbole
- Formkontrolle
- Geradheit
- Ebenheit
- Rundheit
- Zylindrizität
- Profilsteuerungen
- Linienprofil
- Oberflächenprofil
- Orientierungssteuerungen
- Winkeligkeit
- Parallelität
- Senkrechtstellung
- Lokalisierungssteuerungen
- Konzentrizität
- Symmetrie
- Wahre Position
- Wie man GD&T-Positionstoleranz auf eine Bohrung anwendet
- Runout-Steuerelemente
- Kreisförmiger Rundlauf
- Gesamtschlag
- Prüfung
Was ist GD&T?
Es handelt sich um ein System von Symbolen und Normen, das von Ingenieuren verwendet wird, um dem Produktionsteam Fertigungsinformationen zu liefern.
Die Gründe für die Verwendung von Geometric Dimensioning and Tolerancing (GD&T) sind:
- Sie stellt sicher, dass zusammengehörige Teile gut zusammenpassen
- Die universelle Sprache funktioniert unabhängig davon, mit wem man zusammenarbeitet
- Toleranzen geben eine Grenze für den ungünstigsten Fall vor
- Definiert Produktions- und Inspektionsprozesse
Stanley Parker gilt als der Ingenieur, der 1938 das GD&T-System entwickelte.
Vor diesem Zeitpunkt wurden bei allen Merkmalen nur X-Y-Achsen verwendet, um beispielsweise die Position eines Lochs zu bestimmen. Die Angabe einer Positionstoleranz auf dieser Skala bedeutet, dass die Position des kreisförmigen Lochs in einem rechteckigen Muster von der vorgesehenen Stelle abweichen kann.
Allerdings würde man eigentlich wollen, dass die Toleranzzone ein Kreis ist, da dies eine gleichmäßige Messung in allen Winkeln ermöglicht, während ein Rechteck zu den Ecken hin länger und zu den Seiten hin kürzer ist.
Als Parker dies erkannte, begann er mit der Arbeit an einem neuen Konzept, das in den 50er Jahren als militärischer technischer Standard übernommen wurde.
Heute ist GD&T ein wichtiger Bestandteil des Ingenieurwesens, vor allem bei der Herstellung von Teilen, die CNC-Bearbeitungsdienste erfordern. Die amerikanische Norm zur Beschreibung der Merkmale ist ASME Y14.5-2018 und das europäische Äquivalent ist ISO 1101-2017.
GD&T konzentriert sich ausschließlich auf die Geometrie des Produkts. Lineare Abmessungen, Oberflächenrauhigkeit, Gewinde usw. sind nicht Teil dieser Norm.
Warum wird GD&T eingeführt?
Wir haben traditionelle Methoden zur Angabe von Abmessungen und Toleranzen. Wozu also geometrische Bemaßung und Tolerierung?
Geometrische Bemaßung und Tolerierung (GD&T) bietet einige einzigartige Vorteile gegenüber herkömmlichen Methoden. Lassen Sie uns sehen, welche das sind.
Perfekte Montage
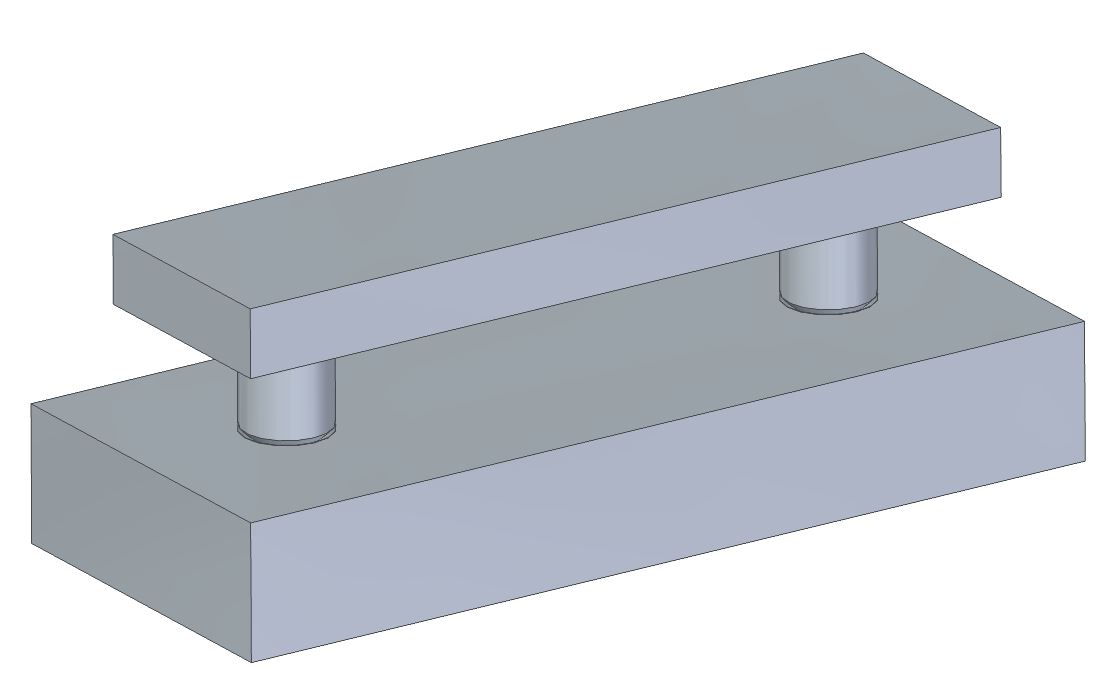
Der wichtigste Nachteil der herkömmlichen Bemaßung und Tolerierung ist, dass sie Informationen über einzelne Teile und Teilemerkmale angeben. Sie garantieren nicht, wie gut unsere Teile auf der Baugruppenebene passen und funktionieren werden.
Dies ist wichtig, weil die meisten Teile für sich genommen nicht nützlich sind. Nehmen wir das Beispiel einer Pleuelstange. Für sich genommen bietet sie uns keinen Nutzen. Aber wenn wir sie mit der Kurbelwelle und dem Kolben verbinden, wird sie etwas nützlicher, da sie die lineare Bewegung des Kolbens in eine Drehbewegung der Kurbelwelle umwandelt.
Wenn diese Baugruppe Teil einer größeren Baugruppe wie einem Dieselmotor wird, kann sie als Teil eines Generators enden, der uns viele Verwendungsmöglichkeiten bietet.
Daher ist es entscheidend, dass unsere Teile gut zueinander passen. Deshalb brauchen wir GD&T. Damit können wir 100-prozentig sicher sein, dass unsere Teile zusammenpassen und genau so funktionieren, wie sie gebraucht werden.
Gemeinsames System zur Erläuterung der Konstruktionsabsicht
GD&T bietet dem Konstrukteur auch eine Plattform, um seine Konstruktionsabsicht allen relevanten Abteilungen zu vermitteln. Dazu gehören:
- Fertigung
- Prüfung
- Nachfolgende Konstrukteure in der Konstruktionsabteilung, die die Arbeit übernehmen, wenn das ursprüngliche Konstruktionsteam nicht verfügbar ist
Die Definitionen, das Vokabular und die Regeln sind einfach und allgemein verständlich. Dadurch sind die Symbole für jeden Ingenieur leicht zu übersetzen und eine großartige Möglichkeit, die Absicht des Konstrukteurs zu vermitteln.
Spart Zeit und Geld
Das ist der wichtigste Vorteil der Verwendung von GD&T. Die Verwendung dieses Systems reduziert die Verschwendung, da es die Anzahl der Zyklen zwischen Entwurf, Herstellung und Testpassung verringert.
Das liegt daran, dass die hergestellten Teile beim ersten Versuch gut passen und folglich die Anzahl der Ausschüsse gering ist. Die Verwendung einer gemeinsamen Sprache reduziert auch den Aufwand für die Prüfung.
Erhalten Sie Ihr Fertigungsangebot in Sekunden
-
Angebot in Sekunden
-
Kurze Vorlaufzeiten
-
Lieferung durch Fractory
Angebot anfordern
Was ist zu beachten?
Geometrische Bemaßung und Tolerierung ist ein leistungsfähigeres System als die traditionellen Toleranzen. Es funktioniert jedoch nur, wenn alle Abteilungen (Design, Konstruktion, Fertigung) die Informationen gut lesen und interpretieren können.
Daher ist es wichtig, bei der Erstellung von technischen Zeichnungen und der Tolerierung verschiedener Teilemerkmale die empfohlenen Richtlinien/Konventionen zu befolgen, damit alle, die in irgendeiner Phase der Produktentwicklung mit der Zeichnung zu tun haben, davon profitieren können.
Die Einhaltung dieser Richtlinien gewährleistet, dass die Zeichnung standardisiert ist und alle Beteiligten bei den Zeichnungsspezifika auf derselben Seite stehen. Einige dieser guten Praktiken sind die folgenden.
Verständlichkeit der Zeichnung
Dies ist wohl die wichtigste Qualität einer Zeichnung. Die Verständlichkeit bezieht sich auf die Klarheit, mit der Teilemerkmale gezeichnet und Toleranzen in der Zeichnung dargestellt werden. Einige Möglichkeiten zur Verbesserung der Verständlichkeit einer Zeichnung sind:
- Zeichnen Sie echte Profile für alle Teilemerkmale.
- Beschriften Sie Maße und Toleranzen außerhalb der Zeichnung (nicht oben). Verwenden Sie Leerraum effektiv.
- Die Leserichtung muss konstant sein. Ein Leser sollte in der Lage sein, alle Bemaßungen zu lesen, während er die Zeichnung aufrecht hält.
- Bemaßungen von parallelen Teilemerkmalen aussparen.
- Das Teil und seine Funktion kurz erläutern.
- Winkel nur angeben, wenn sie nicht rechtwinklig (90°) sind.
Genaue Toleranzen nur wenn nötig
Wenn es die Passform/Funktion des Teils nicht erfordert, müssen die Toleranzen so locker wie möglich gehalten werden. Das reduziert die Herstellungskosten und die Durchlaufzeit. Wir empfehlen, die Wahl der Fertigungsmethode den Maschinenbauern zu überlassen.
Der Konstrukteur muss auch die allgemeine Toleranz für eine Zeichnung angeben. Diese dient als Standardtoleranz für alle Teilemerkmale. Für Teilemerkmale mit einer anderen Toleranzgrenze muss der Konstrukteur diese an den entsprechenden Stellen angeben.
Diese speziellen Toleranzgrenzen haben Vorrang vor den Allgemeintoleranzen. Bei der Angabe spezieller Toleranzgrenzen sind funktionale Merkmale gegenüber anderen Merkmalen zu bevorzugen.
GD&T Merkmale & Symbole
Die GD&T-Sprache ist in der Lage, so ziemlich alle Eigenschaften zu definieren, die für die Gewährleistung einer perfekten Baugruppe notwendig sind.
Das System verwendet zu diesem Zweck eine Reihe von Symbolen. Um diese technischen Symbole auf Zeichnungen korrekt zu verwenden, müssen wir zunächst mit einigen grundlegenden Bausteinen dieses Systems vertraut sein.
Wir können mit den verschiedenen Definitionen, Terminologien und Regeln beginnen, bevor wir zu den GD&T-Symbolen kommen.
Nennmaße
Ein Nennmaß ist die Merkmalsgröße des echten Profils. Es ist das genaue Maß, das man idealerweise erreichen möchte. Merkmalsspezifika wie Größe, Ausrichtung, Lage zu einem Bezugspunkt haben eine Nenngröße, die von den Bearbeitern angestrebt wird.
Auf einer Zeichnung werden sie in einem Kasten dargestellt. Sie kann als Zahl oder aus einer gängigen Norm wie ASME dargestellt werden.
Funktionskontrollrahmen
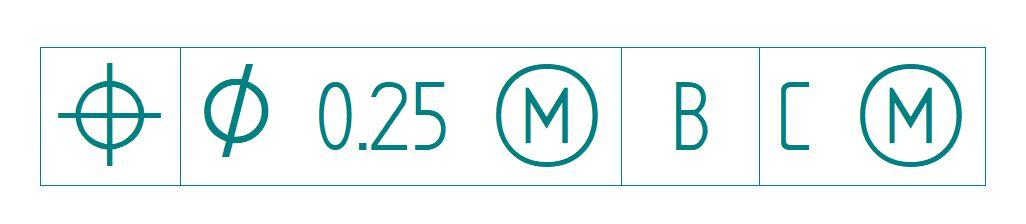
Dieser Rahmen enthält Informationen über Teilespezifika. Er enthält verschiedene Abteilungen, wobei jede Abteilung ein bestimmtes Attribut des Teilemerkmals definiert. Auf einen Blick vermittelt der Merkmalskontrollrahmen die für die Bearbeitung und Prüfung erforderlichen Informationen.
Der Merkmalskontrollrahmen kann wie folgt in 4 Hauptteile unterteilt werden.
Führungspfeil
Dieser Pfeil markiert das zu kontrollierende Teilemerkmal. Führt er zu einer Fläche, ist die Fläche unter geometrischer Kontrolle. Wenn er eine diametrale Abmessung markiert, dann steuert GD&T die Achse. Dieser Pfeil kann in manchen Fällen nicht vorhanden sein.
Geometrisches Merkmalssymbol
Das erste Fach (von links beginnend) enthält das geometrische Merkmalssymbol. Hier wird das geometrische Merkmal angegeben. Insgesamt gibt es 14 Arten von geometrischen Toleranzen, wenn man die Anzahl der Symbole zugrunde legt, und 15, wenn man sie klassifiziert.
Die verschiedenen Arten von geometrischen Merkmalen sind Formkontrolle, Profilkontrolle, Lagekontrolle, Orientierungskontrolle usw. Wir werden später auf jede Kategorie näher eingehen.
Merkmalstoleranzfach
Der 2. Block enthält maximal 3 (manchmal 2 oder 1) verschiedene Symbole.
Das erste Symbol zeigt die Art des Toleranzfeldes an. Ein Durchmessersymbol (⌀) steht für eine diametrale Zone (zylindrische Toleranzzone). Um eine kugelförmige Zone anzugeben, ist das Symbol der Buchstabe „S“, gefolgt von dem Durchmessersymbol (⌀). Fehlt ein Symbol, so wird eine ganz breite Zone angenommen.
Das zweite Symbol im zweiten Block gibt den Wert der Toleranzzone in mm an. Dieser Wert muss im 2. Block immer vorhanden sein.
Das dritte Symbol in diesem Block ist der Modifikator für die Toleranz. Dieser Materialmodifikator ist nur vorhanden, wenn das Feature eine Größe hat, z. B. ein Loch. Beispiele für Materialmodifikatoren sind MMC (Maximum material condition) und LMC (Least material condition). Weitere Informationen über die verschiedenen verfügbaren Modifikatoren werden im weiteren Verlauf des Artikels erörtert.
Bezugspunkte
Der dritte Block enthält Informationen über den/die Bezugspunkt(e) mit einem Minimum von 1 und einem Maximum von 3 Bezugspunkten. Bei drei Bezugspunkten werden sie als primäre, sekundäre und tertiäre Bezugspunkte bezeichnet, wobei jeder in einem anderen Kästchen dargestellt wird (in der obigen Abbildung sind es zum Beispiel zwei). Dieser Block kann auch einen Materialmodifikator enthalten.
Alle oben genannten Informationen helfen uns zu verstehen, wie man einen Feature-Kontrollrahmen liest. Um besser zu verstehen, wie die Toleranz mit Hilfe von Materialbedingungsmodifikatoren angepasst werden kann, müssen wir mit den verschiedenen Optionen vertraut sein.
Materialbedingungsmodifikatoren
Materialbedingungsmodifikatoren vermitteln die Absicht, wenn die Toleranz für ein Feature mit einer bestimmten Featuregröße gilt. Wenn wir einem Merkmal Toleranzen zuweisen, werden zwei Materialbedingungen festgelegt
- Maximale Materialbedingung
- Mindeste Materialbedingung
Betrachten wir eine Welle mit einem Durchmesser von 100 mm. Wenn wir bei der Herstellung eine Toleranz von ±0,2 mm einräumen, dann enthält die Welle bei 100,2 mm die maximale Menge an Material. Das ist der maximale Materialzustand.
Andererseits wird die gleiche Welle bei einem Durchmesser von 99,8 mm die geringste Menge an Material enthalten. Diese Grenzen werden als Materialbedingungen bezeichnet.
Die geometrischen Toleranzen können auf 3 verschiedene Arten auf ein Merkmal angewendet werden. Diese sind wie folgt:
- Maximale Materialbedingung
- Mindeste Materialbedingung
- Unabhängig von der Featuregröße
Maximaler Materialbedingungsmodifikator
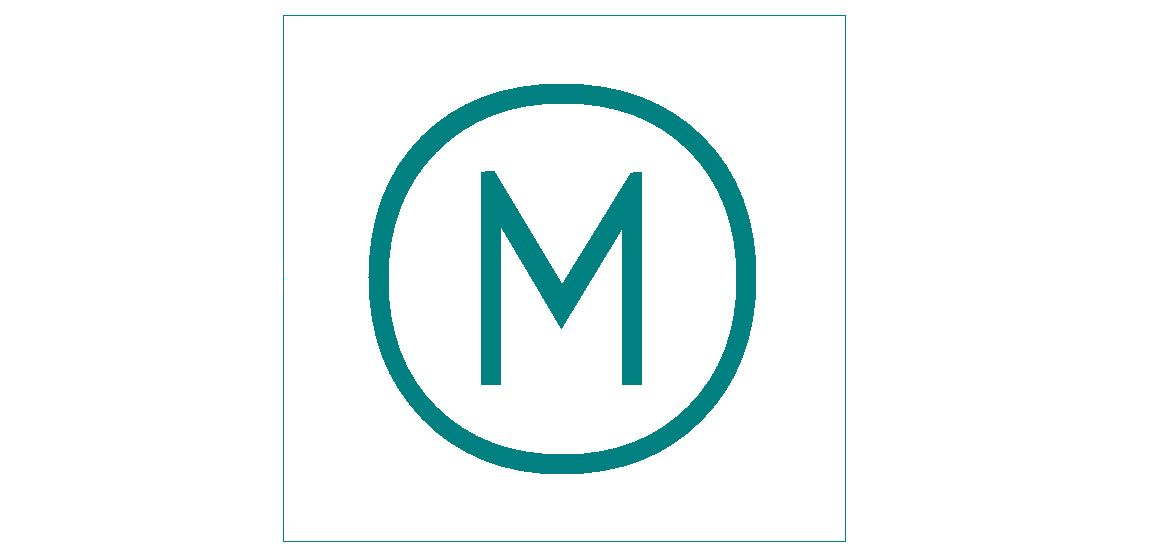
Wir stellen diese Bedingung durch ein eingekreistes „M“ hinter dem Toleranzwert im Featurekontrollfach dar. Das Feature enthält das maximale Material bei dieser Featuregröße.
Für externe FOS (Feature Of Size), wie z.B. der Durchmesser einer Welle, stellt MMC die größte Größe dar. Für interne FOS, wie z.B. den Durchmesser einer Bohrung, stellt MMC die kleinstmögliche Größe innerhalb der angegebenen Toleranzgrenzen dar, da bei einer kleineren Bohrung mehr Material übrig bleibt.
Wenn wir eine geometrische Toleranz bei der maximalen Materialbedingung anwenden müssen, erwähnen wir diese Bedingung im Kontrollrahmen des Features.
Modifikator für die kleinste Materialbedingung
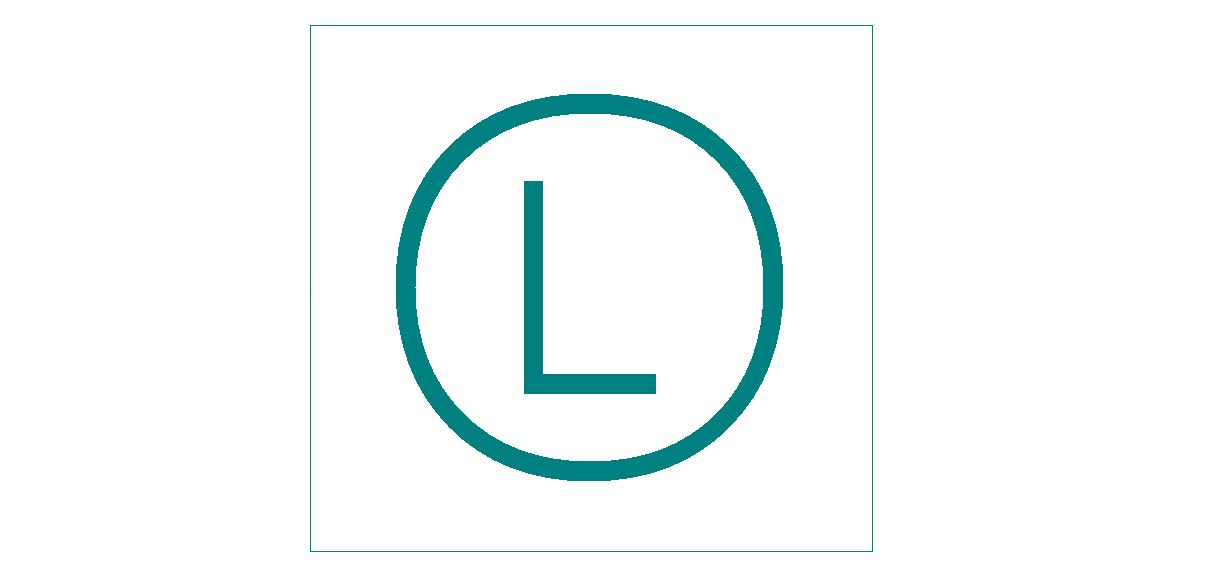
LMC ist die Bedingung, bei der das Material die geringste Menge an Material enthält.
Für externe FOS ist es die kleinstmögliche Größe innerhalb der angegebenen Grenzen. Für interne FOS ist es die größtmögliche Größe.
Wir stellen diesen Modifikator mit dem Buchstaben „L“ in einem Kreis dar. Mit diesem Merkmal wird überflüssiges Material und damit Gewicht entfernt. Um geometrische Toleranzen unter dieser Bedingung anzuwenden, verwenden wir sein Symbol im Kontrollrahmen des Merkmals.
Unabhängig von der Merkmalsgröße (RFS)
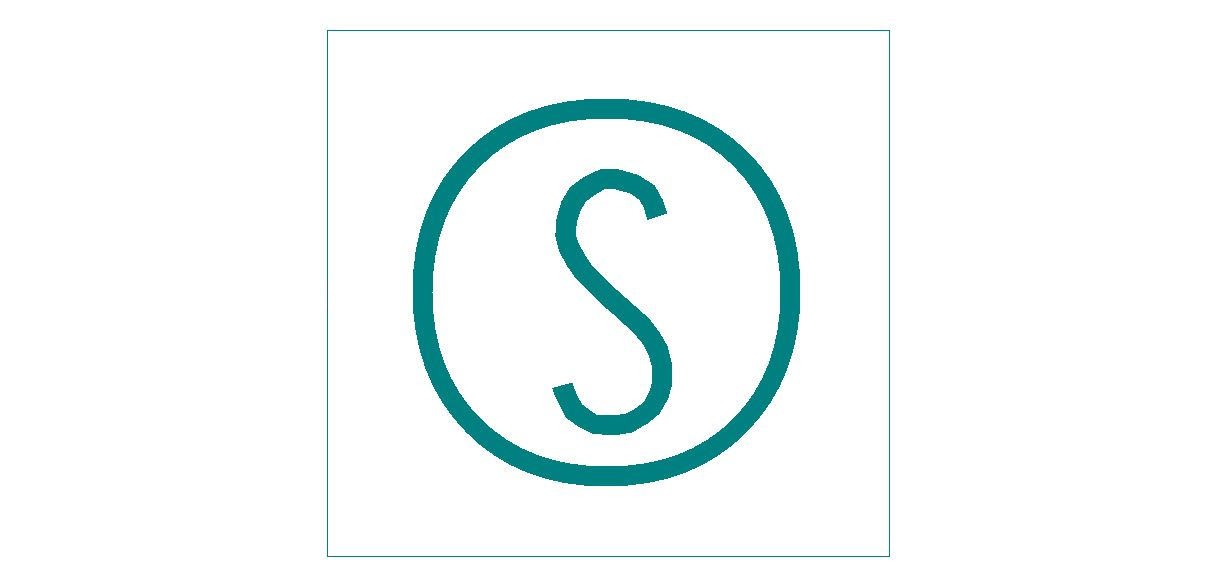
Wenn die angegebenen geometrischen Toleranzen bei jedem Größeninkrement von FOS angewendet werden, geben wir dies durch RFS an. Das Symbol für RFS war der Buchstabe „S“ in einem Kreis, aber es wird nicht mehr benötigt, da RFS jetzt als Standardbedingung gilt und kein Symbol benötigt.
Daten und Feature Callouts
Daten sind Bezugspunkte zur Messung von Maßtoleranzen. Das kann ein Punkt, eine Linie oder eine Ebene sein. Mit Hilfe eines Bezugspunkts werden Bezugsrahmen (DRF) festgelegt. Der DRF ist im Grunde ein 3D-Koordinatensystem, das uns hilft, die Positionen aller anderen Merkmale in Bezug auf den DRF zu definieren.
Es gibt 6 Freiheitsgrade (3 translatorische und 3 rotatorische), die wir kontrollieren müssen, um Teile effektiv herzustellen und zu prüfen. Wir verwenden DRF, um diese Freiheitsgrade zu bestimmen.
Datum-Features sind die tatsächlichen Teile-Features wie Löcher und Schlitze. Sie können Abweichungen von den gewünschten Positionen aufweisen.
Unter allen Bezugsmerkmalen geben wir denjenigen den Vorzug, die mit anderen Teilen in der Baugruppe zusammenpassen. Wir können mehr als einen Bezugspunkt in unserem Feature Control Frame angeben. Entsprechend der Reihenfolge der DRFs im Feature-Kontrollrahmen werden die Teile mit den DRFs in abnehmender Reihenfolge ihrer Wichtigkeit verknüpft.
GD&T-Symbole
Bis zu 14 GD- und T-Symbole sind verfügbar, um verschiedene geometrische Merkmale von Features darzustellen. Diese Symbole helfen uns, diese Merkmale als Anforderungen für das Endprodukt zu spezifizieren.
Wir platzieren diese Symbole im ersten Fach des Feature-Kontrollrahmens. Wir werden uns diese Arten der Toleranzkontrolle ansehen.
Formkontrolle
Wie der Name schon sagt, bezieht sich die Formkontrolle auf die endgültige Form oder Gestalt des Features. Wir definieren Formkontrollen, um die Abweichung der geometrischen Toleranz von ihrer Idealform zu begrenzen.
Geradheit
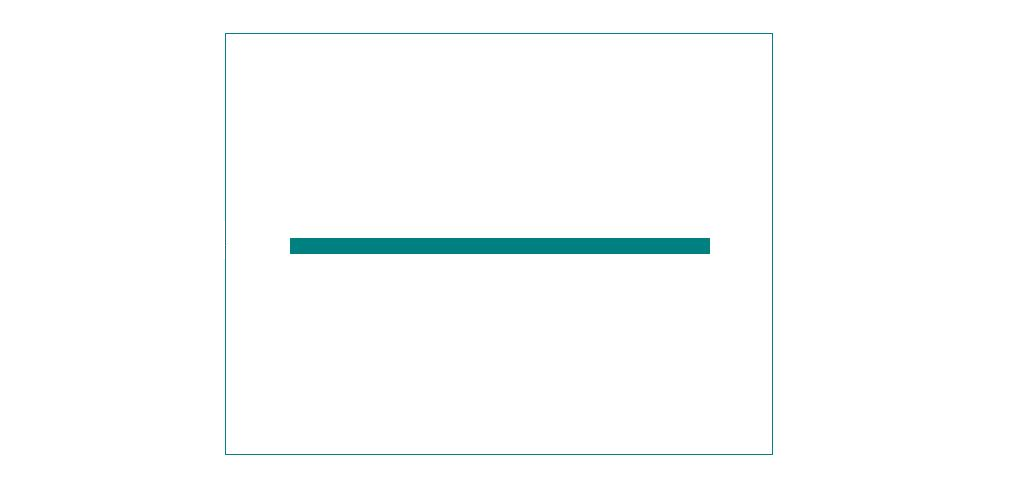
Um die Geradheitscharakteristik eines Merkmals (z. B. einer Achse oder einer Fläche) anzugeben, verwenden wir ihr Symbol (eine gerade horizontale Linie) in der ersten Abteilung.
Die Geradheit einer Fläche kann sich auf flache Flächen wie die Seite eines Blocks oder auf gekrümmte Flächen wie die Seite eines Zylinders in Richtung der Achse beziehen. Sie definiert die zulässige Abweichung einer Linie (2 Dimensionen) auf der Oberfläche innerhalb einer bestimmten Toleranz.
Die axiale Geradheit gilt zum Beispiel für die Achse einer Welle oder einer Bohrung. Go/no go gauge ist das Prüfwerkzeug, das verwendet wird, um sicherzustellen, dass das Teil den Anforderungen entspricht.
Ebenheit
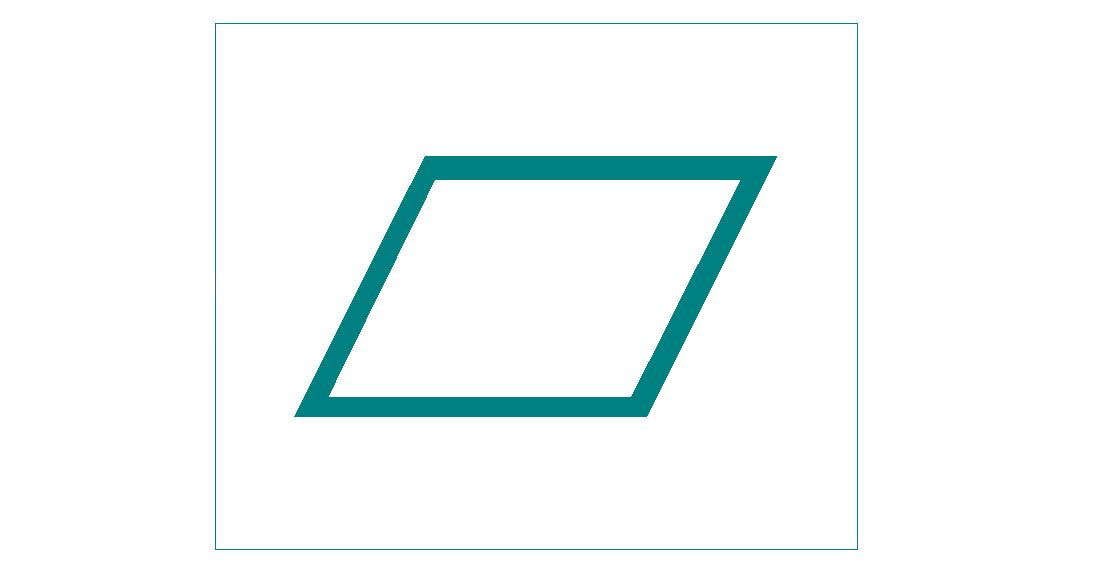
Wir verwenden dieses Merkmal für Merkmale wie die Oberfläche eines Teils. Das Symbol für die Ebenheit ist ein nach rechts gekipptes Parallelogramm. Die Differenz zwischen dem höchsten und dem niedrigsten Punkt einer ebenen Fläche ist ihre Ebenheit.
Das Ebenheitssymbol benötigt keine Bezugspunkte, da es nur einen Toleranzbereich angibt, innerhalb dessen die gesamte Oberfläche eines Teils in drei Dimensionen liegen muss.
Zur Überprüfung der Ergebnisse wird ein Höhenmessgerät verwendet. Es berührt verschiedene Bereiche der Oberfläche, um festzustellen, ob alle Punkte innerhalb der Toleranzzone liegen.
Rundheit
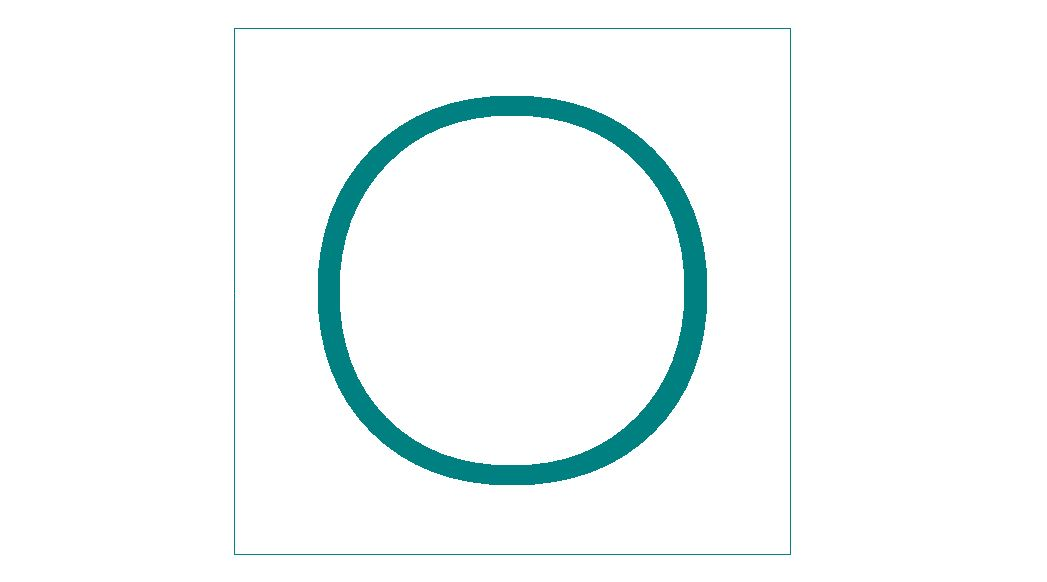
Die Rundheit eines Merkmals zeigt, wie nahe der Umfang des Teils an einem perfekten Kreis sein sollte. Es werden 2 konzentrische Kreise auf einer Ebene senkrecht zur Teileachse verwendet, um den geeigneten Toleranzbereich in 2D zu definieren. Jeder Punkt der endgültigen Messungen muss zwischen den Kreisen liegen.
Dieses Merkmal wird als Kreis im ersten Fach des Feature-Kontrollrahmens angezeigt.
Zylindrizität
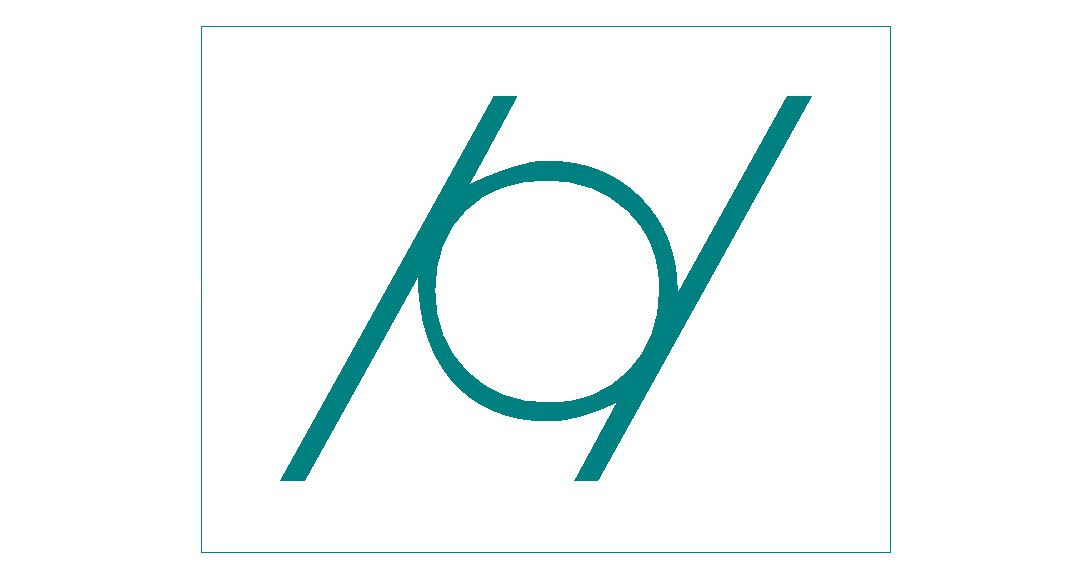
Die Zylindrizität ist im Grunde genommen die Kreisform in 3D, d.h. sie verläuft über die gesamte Länge des Teils.
Dieses Merkmal beschreibt auch andere zylindrische Merkmale wie die Verjüngung, die Geradheit und die Rundheit. Deshalb ist dieses Merkmal auch teuer in der Prüfung.
Profilsteuerungen
Wir verwenden Profilsteuerungen, um die 3D-Toleranzzone um das Merkmal zu steuern. Diese Funktion hilft uns dabei, Toleranzgrenzen für erweiterte Kurven und Formen festzulegen.
Ein Feature, das sich gut für komplexe Kurven eignet, muss natürlich auch mit einfacheren Kurven funktionieren. Das macht Profilkontrollen extrem vielseitig. Deshalb empfehlen einige Designer, alle anderen Steuerelemente aufzugeben und nur mit Profilsteuerelementen zu arbeiten.
Diese Steuerelemente bilden eine Toleranzgrenze um die erweiterte Kurve, indem sie sie auf beiden Seiten nachahmen. Dadurch wird verhindert, dass ein Punkt auf der Feature-Kurve außerhalb der Toleranzgrenze liegt. Es gibt zwei Arten von Profilsteuerungen.
Linienprofil
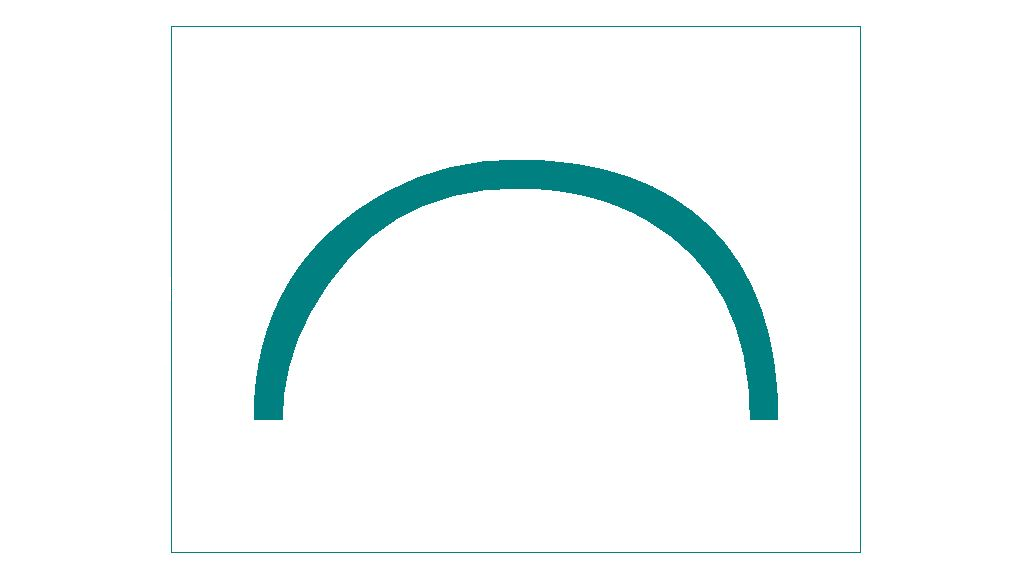
Das Linienprofil legt eine Toleranzzone um unterschiedliche 2D-Querschnitte des Teils fest. Es steuert einzelne Linienelemente eines Teilemerkmals.
Die Linienprofilsteuerung zeichnet die Idealkurve an den Toleranzgrenzen auf beiden Seiten nach. Alle Punkte auf der Kurve des Teils müssen innerhalb dieser Grenzen liegen.
Oberflächenprofil
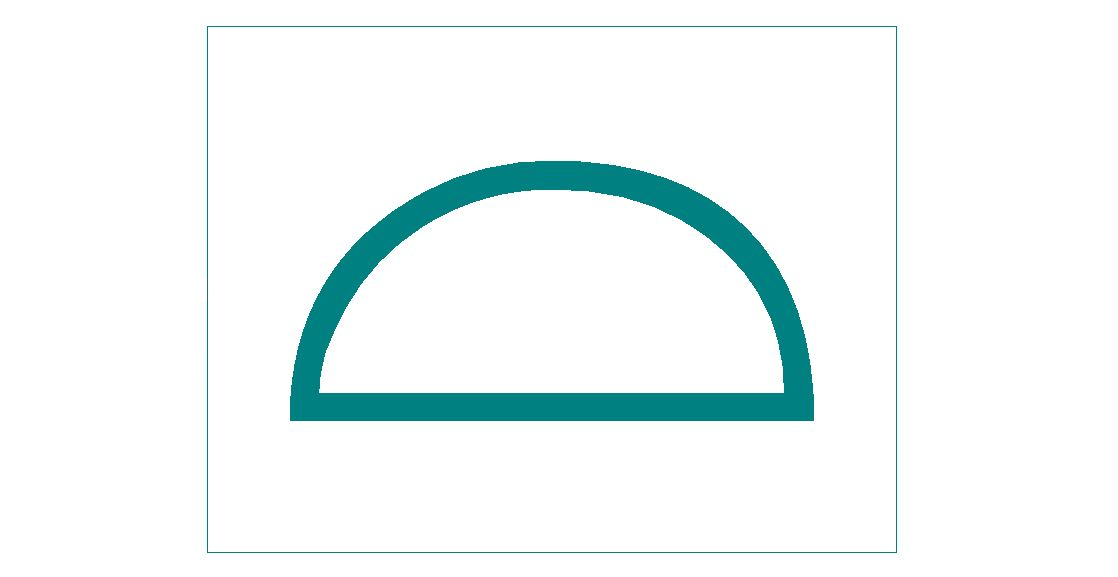
Die Oberflächenprofilkontrolle ist im Vergleich zur Linienkontrolle beliebter. Anstelle einer zweidimensionalen Toleranzzone erzeugt die Oberflächenprofilsteuerung eine 3D-Zone um eine Oberfläche.
Alle Punkte auf der Oberfläche der Tabelle müssen innerhalb der beiden virtuellen Ebenen liegen.
Orientierungssteuerungen
Die Orientierungstoleranz steuert die Ausrichtung eines Features in Bezug auf einen definierten Bezugspunkt. Es gibt drei Arten von Ausrichtungssteuerungen in GD&T.
Winkeligkeit
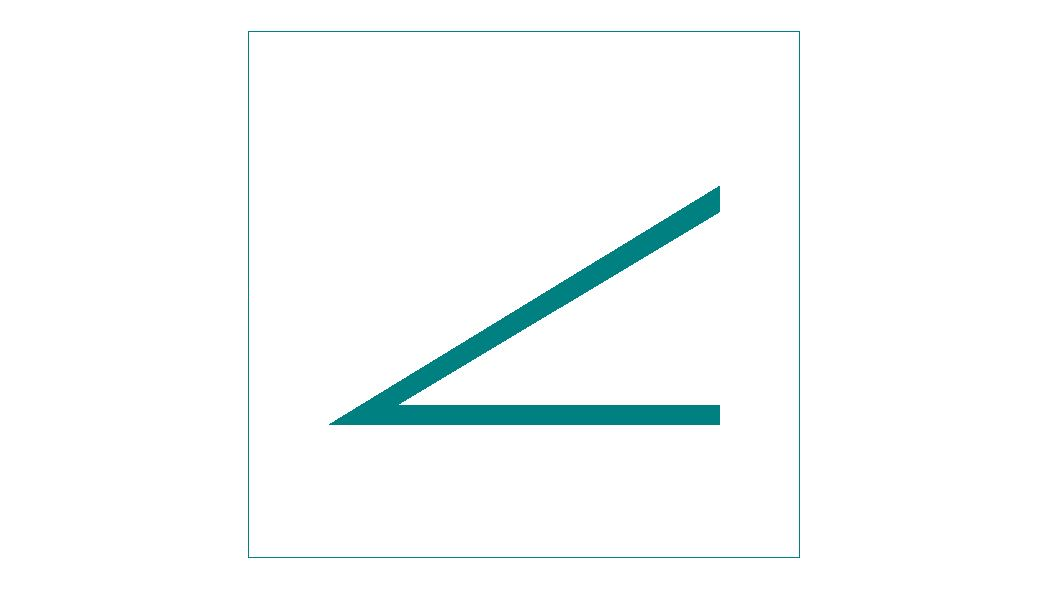
Die Winkeligkeitssteuerung hält den Winkel eines Merkmals in Bezug auf den Bezugspunkt in Schach. Man kann damit eine 2D-Linie kontrollieren, aber es ist beliebter, um Oberflächen (3D) unter Kontrolle zu halten.
Diese Art der strengen Kontrolle hält den Winkel und die Ebenheit der Oberfläche unter Kontrolle und wird für Teile-Features empfohlen, die durch die abgewinkelte Oberfläche mit anderen Teilen zusammenpassen.
Es ist wichtig zu beachten, dass das Winkeligkeits-Feature den Winkel indirekt steuert und nicht im Wesentlichen dasselbe ist wie eine Winkeltoleranz (z. B. +/- 2°). Vielmehr ergibt sich der erforderliche Winkel aus der Einhaltung der durch diese Kontrolle festgelegten Maßanforderungen.
Parallelität
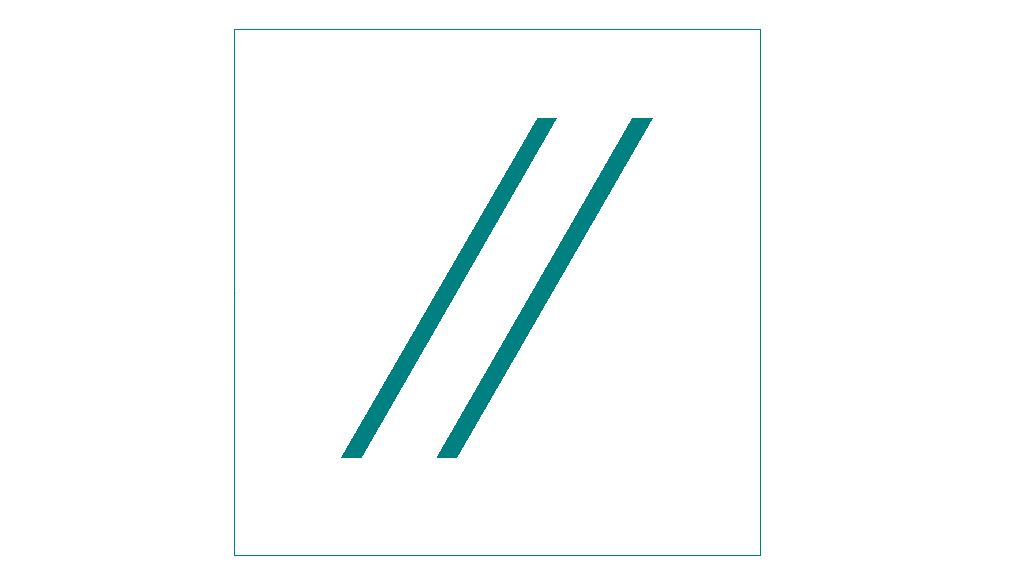
Parallelität ist eine verfeinerte Form der Winkligkeit. Hier ist der Bezugspunkt die zu imitierende Fläche und der Winkel wird auf 0° gesetzt. Es gibt 2 Arten von Parallelität: Flächenparallelität und Achsenparallelität.
Wir können eine Achse oder eine Fläche als Bezugspunkt wählen. Dies wird unser Bezugspunkt und wir referenzieren ihn im 3. Block des Feature-Kontrollrahmens als Bezugspunkt für das Feature.
Ähnlich wie bei der Winkeligkeit wird hier nicht der tatsächliche Winkel kontrolliert, sondern er wird gesichert, indem die Anforderungen in Form einer Toleranzzone festgelegt werden.
Senkrechtstellung
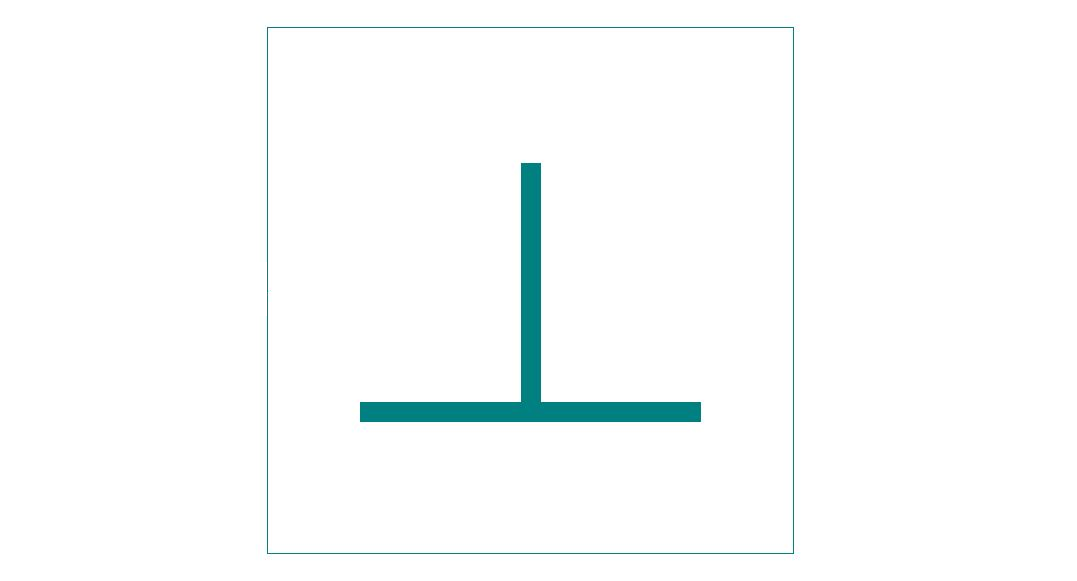
Die Senkrechtstellung ist ebenfalls eine besondere Form der Winkelstellung, bei der der Winkel auf 90° festgelegt wird. Es ist eine knifflige Kontrolle, da sie zwei sehr unterschiedliche Arten von Anforderungen bedeuten kann.
Es gibt die Oberflächenrechtwinkligkeit (Symbol:⟂) und dann gibt es die Achsenrechtwinkligkeit (Symbole: ⟂+⌀).
Flächensenkrechtigkeit gibt an, dass eine Fläche oder Linie senkrecht zu einer Bezugsfläche oder -linie stehen muss, ähnlich wie die Winkligkeit. Zur Kontrolle werden zwei virtuelle Ebenen/Linien um die Zielfläche herum angenommen.
Achsenrechtwinkligkeit gibt an, wie rechtwinklig eine Achse zu dem genannten Bezugspunkt sein muss. Dazu wird ein virtueller Zylinder um die Zielachse auf einer Fläche errichtet, die genau parallel zur Bezugsfläche verläuft.
Lokalisierungssteuerungen
Die Lokalisierungstoleranzsteuerung wird für eine genaue Kontrolle der Position eines Features in Bezug auf einen Bezugspunkt verwendet. Es gibt vier Haupttypen von Lagekontrollen.
Konzentrizität
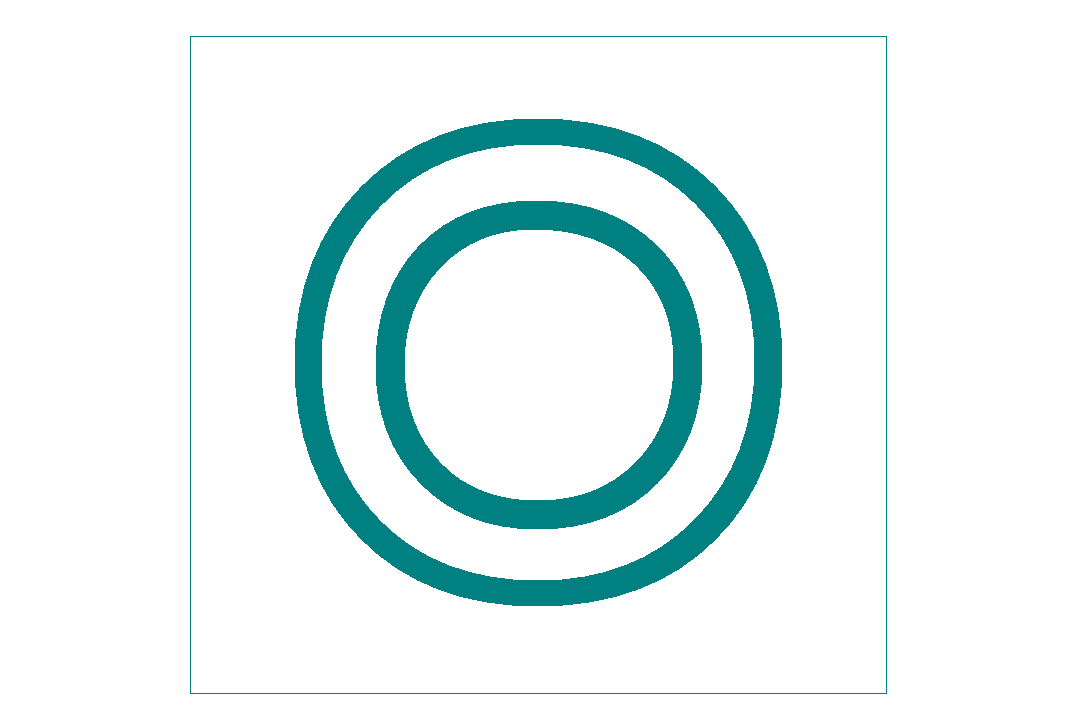
Konzentrizität, auch bekannt als Koaxialität (obwohl nicht genau dasselbe), hält die Konzentrizität von kreisförmigen und zylindrischen Features aufrecht.
Sie fixiert die Achse eines Teils mit der Achse eines referenzierten Features (Bezugsachse). Die Achsen beider Teile werden so bestimmt, dass sie sich in den Mittelpunkten der Teile befinden.
Dieses Steuerelement kann zu Verwirrung führen, da die Achsen von Außenmessungen abgeleitet werden und nicht von ihrer tatsächlichen Position.
Die Koaxialität erstellt eine 3D-Toleranzzone auf der Grundlage von Oberflächenmessungen, in der das Teil liegen muss.
Symmetrie
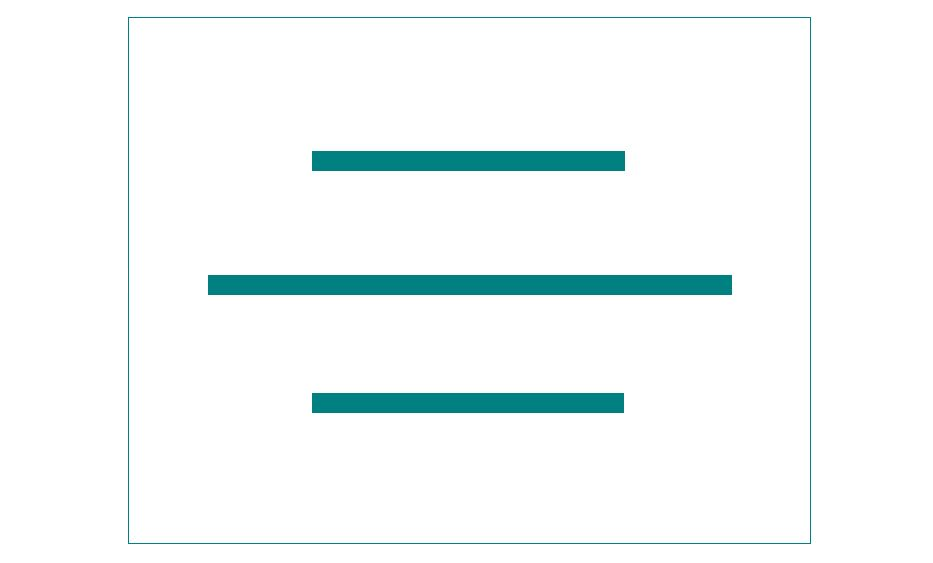
Die Symmetriebeschreibung legt eine zentrale Ebene fest, um die die beiden Teile des Features in gleichem Abstand angeordnet werden. Der Mittelpunkt der beiden Punkte auf beiden Seiten muss innerhalb der Toleranzzone liegen, die um die Mittelebene herum festgelegt wurde.
Die Symmetriebeschreibung ist nicht sehr häufig. Sie ist nur sehr eingeschränkt verwendbar und zudem schwer zu prüfen. Wir benötigen ein KMG, um die endgültige Symmetrie zu prüfen.
Wahre Position
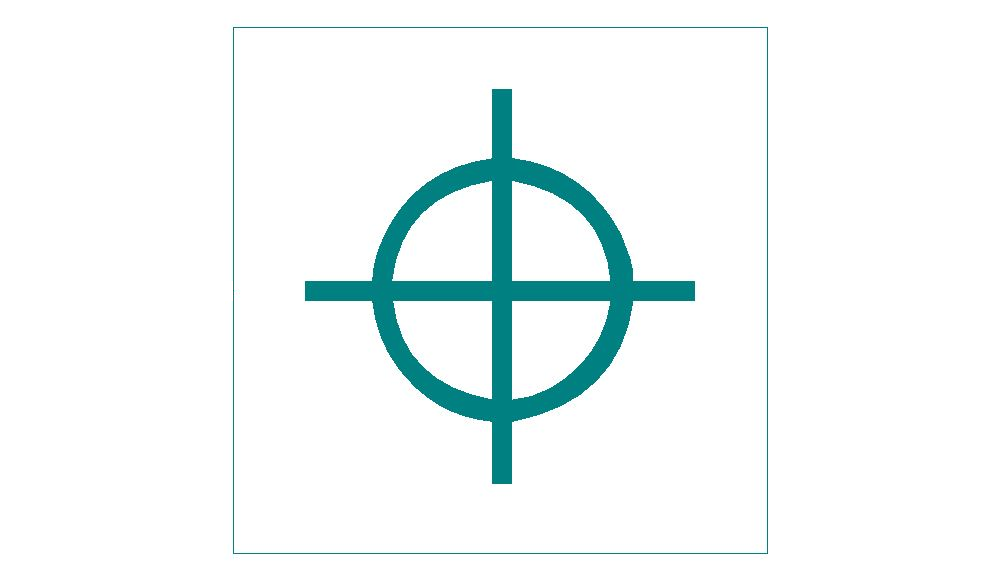
Die wahre Position (allgemein als Position bekannt) ist eine sehr nützliche Angabe und wird in GD&T ausgiebig verwendet.
Die Position definiert, wie stark die tatsächliche Position eines Merkmals von seiner beabsichtigten Position abweichen kann. Die Definition schließt die Bezugsebene ein, auf die sich die Messung bezieht.
Sie enthält oft ein diametrales Zeichen (⌀), um hervorzuheben, dass die Toleranzzone ein Kreis ist und nicht nur die X- und Y-Achse (was wir zu Beginn des Artikels als Grund für die Erstellung von GD&T erwähnt haben).
Hier ist ein großartiges Video, das zeigt, wie man die Toleranzen auf einer Zeichnung unter Verwendung der wahren Position verwendet:
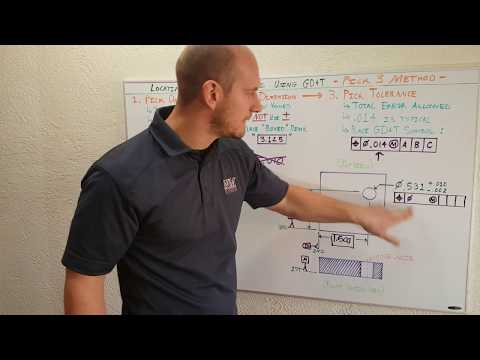
Wie man GD&T-Positionstoleranz auf eine Bohrung anwendet
Runout-Steuerelemente
Wir verwenden die Runout-Steuerelemente, um die Abweichung eines Teile-Features von seiner zugewiesenen Position in Bezug auf einen festgelegten Bezugspunkt zu messen. Diese Kontrolle wird für kreisförmige Features verwendet. Sie misst im Wesentlichen die Taumelbewegung durch Drehen des Features um den festen Bezugspunkt.
Es gibt zwei Arten von Rundlaufkontrollen.
Kreisförmiger Rundlauf

Der kreisförmige Rundlauf funktioniert in zwei Dimensionen, um die Form, Position und Ausrichtung verschiedener Teile-Features zu kontrollieren. Für diese 2D-Kalibrierung müssen wir ihr eine Bezugsachse zuweisen, um diese Merkmale zu prüfen.
Im GD&T-Jargon ist der Rundlauf allgemein als Runout bekannt. Der Rundlauf misst die Abweichung in den Oberflächenelementen durch Rotation.
Das bedeutet, dass z.B. die Welle um ihre Bezugsachse gedreht wird und das gekennzeichnete Element auf Toleranz gemessen wird. Im Wesentlichen begrenzt sie die Schwingungen einer Arbeitswelle, um eine längere Lebensdauer der damit verbundenen Teile wie Lager zu gewährleisten.
Gesamtschlag
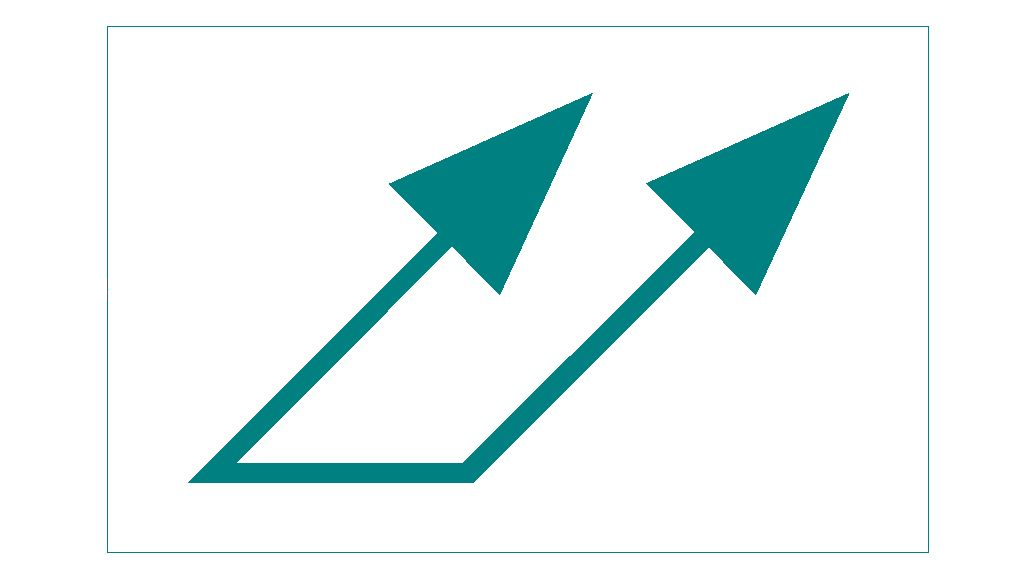
Gesamtschlag ist das 3D-Gegenstück zum Rundschlag. Er kontrolliert ebenfalls Form, Lage und Ausrichtung. Anstatt jedoch einzelne Querschnitte zu prüfen (wie beim Rundlauf), wird die gesamte Oberfläche geprüft. Die Verwendung des Gesamtrundlaufs ermöglicht also eine strengere Kontrolle der Merkmale des Merkmals.
Prüfung
In allen Branchen kann es problematisch sein, wenn der Fertigungsprozess nicht den Konstruktionsspezifikationen entspricht. Während in einigen Fällen das Leben der Kunden gefährdet sein kann, kann in anderen Fällen ein Produktrückruf zu großen finanziellen Verlusten führen.
Selbst wenn die Ergebnisse nicht so schlecht sind, hängt der Ruf eines Unternehmens stark von der Qualität seiner Produkte und Dienstleistungen ab.
GD&T standardisiert den Inspektionsprozess, indem es die Inspektoren auf dieselbe Plattform wie den Konstrukteur bringt. Dadurch werden viele Hindernisse beseitigt. Aber GD&T ist ein umfangreiches Thema.
Wie wir gesehen haben, gibt es eine Reihe verschiedener geometrischer Merkmale, die sich alle stark voneinander unterscheiden und die mit GD&T kontrolliert werden können. Aufgrund dieser Verschiedenheit erfordert die Prüfung jedes Merkmals eine spezifische Methode, ein spezifisches Werkzeug und eine spezifische Fertigkeit.
Einige dieser Merkmale können mit den einfachsten Werkzeugen gemessen werden, während andere ohne fortgeschrittene Ausrüstung, wie z. B. eine Koordinatenmessmaschine (KMG), unmöglich zu messen sind.
Inspektoren benötigen das Wissen und die Fähigkeit, verschiedene Messwerkzeuge wie Messuhren, Mikrometer, Messschieber, Oberflächenplatten und Koordinatenmessmaschinen zu verwenden, um die Genauigkeit von Teilen zufriedenstellend zu prüfen.