A mérnökök CAD-szoftverrel tervezik meg a projekthez szükséges alkatrészeket és komponenseket. A digitális birodalomban könnyű elérni a tökéletességet. A való életben a gyártás soha nem 100%-os pontosságú.
Néha az alapméretektől való néhány milliméteres eltérés is teljesen rendben lehet. Ugyanakkor két egymáshoz illeszkedő alkatrész rendkívül nagy pontosságot igényelhet.
Az elvárt eltérés egy előre meghatározott tartományban tartásához mérnöki tűréseket lehet alkalmazni. A mérettűrések nagyon elterjedtek, de hiányoznak a gyártás néhány nagyon fontos szempontjának közlésére szolgáló módszerek. Itt lép be a GD&T, vagy geometriai méretezés & tolerancia.
Ez a méretek és tűrések teljesen új módon történő leírásának egy formája. A mérnöki szimbólumok közös nyelvét használva segít minden szükséges információt könnyen meghatározni.
- Mi a GD&T?
- Miért alkalmazzuk a GD&T-t?
- Tökéletes összeszerelés
- Közös rendszer a tervezési szándék kifejtésére
- Idő és pénz megtakarítása
- Mit kell figyelembe venni?
- A rajz érthetősége
- Szoros tűrések csak akkor, ha szükséges
- GD&T jellemzők & Szimbólumok
- Névleges méretek
- Jellemző vezérlő keret
- Vezető nyíl
- Geometriai jellemző szimbólum
- Tulajdonságtűrés rekesz
- Datumok
- Az anyagállapot-módosítók
- Maximális anyagfeltétel módosító
- Legkisebb anyagállapot módosító
- Függetlenül a jellemző méretétől (RFS)
- Datumok és Feature Callouts
- GD&T szimbólumok
- Formavezérlés
- Egyenesedés
- Síkosság
- Körkörösség
- Hengeresség
- Profilvezérlés
- Vonalprofil
- Felületi profil
- Orientációs vezérlés
- Szögeltség
- Párhuzamosság
- Perpendicularity
- Helyzetvezérlés
- Központosság
- Szimmetria
- A valódi pozíció
- How to Apply GD&T Position Tolerance to a Hole
- Runout Controls
- Körkörös kifutás
- Teljes kifutás
- Kontroll
Mi a GD&T?
Ez egy szimbólumokból és szabványokból álló rendszer, amelyet a mérnökök arra használnak, hogy gyártási információkat szolgáltassanak a gyártócsapatnak.
A geometriai méretezés és tűrésrendszer (GD&T) használatának okai a következők:
- Ez biztosítja, hogy az illeszkedő alkatrészek jól illeszkedjenek egymáshoz
- Az univerzális nyelv attól függetlenül működik, hogy kivel dolgozol
- A tűrések határt adnak a legrosszabb esetekre
- meghatározza a gyártási és ellenőrzési folyamatokat
Stanley Parkert tartják a GD&T rendszer 1938-as kifejlesztése mögött álló mérnöknek.
Előtte minden funkció csak X-Y tengelyeket használt például egy furat helyzetének meghatározására. A pozíciótolerancia megadása ezen a skálán azt jelenti, hogy a kör alakú lyuk pozíciója téglalap alakban eltérhet a tervezett helytől.
Viszont valójában azt szeretnénk, ha a toleranciazóna egy kör lenne, mivel ez minden szögben egységes mérést tesz lehetővé, míg egy téglalap a sarkok felé hosszabb, az oldalak felé pedig rövidebb.
Amint Parker ezt felismerte, elkezdett dolgozni az új koncepción, amelyet az 50-es években katonai mérnöki szabványként fogadtak el.
Most a GD&T a mérnöki munka fontos része, különösen a CNC megmunkálási szolgáltatásokat igénylő alkatrészek létrehozásakor. A jellemzőket leíró amerikai szabvány az ASME Y14.5-2018, az európai megfelelője pedig az ISO 1101-2017.
A GD&T kizárólag a termék geometriájára összpontosít. A lineáris méretek, a felületi érdesség, a menetek stb. nem részei ennek a szabványnak.
Miért alkalmazzuk a GD&T-t?
A méretek és tűrések jelölésére vannak hagyományos módszereink. Mi szükség van tehát a geometriai méretezésre és tűrésre?
A geometriai méretezés és tűrés (GD&T) néhány egyedülálló előnyt kínál a hagyományos módszerekkel szemben. Lássuk, melyek ezek.
Tökéletes összeszerelés
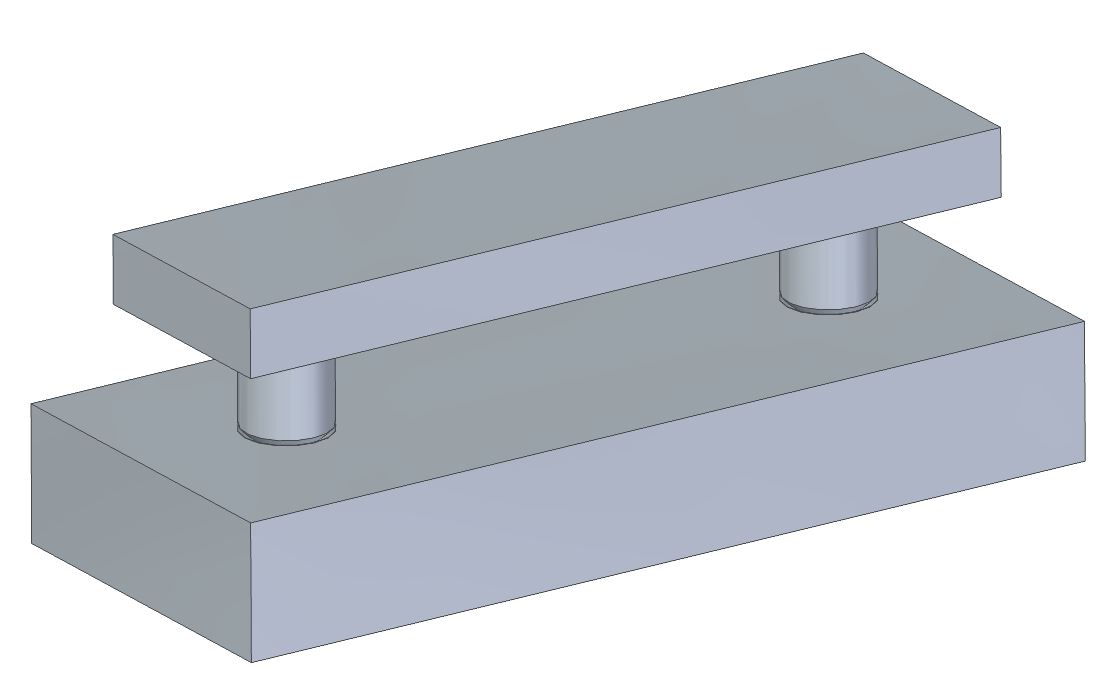
A hagyományos méretezés és tűrésmeghatározás alkalmazásának legfontosabb hátránya, hogy egyedi alkatrész- és alkatrészjellemző információkat jelöl. Nem garantálja, hogy az alkatrészeink mennyire fognak illeszkedni és működni az összeszerelés szintjén.
Ez azért fontos, mert a legtöbb alkatrész önmagában nem használható. Vegyük például a csatlakozó rudat. Önmagában semmilyen hasznot nem nyújt számunkra. De amikor a forgattyús tengelyhez és a dugattyúhoz csatlakoztatjuk, egy kicsit hasznosabbá válik, mivel a dugattyú lineáris mozgását a forgattyús tengely forgómozgásává alakítja át.
Ha ez az összeállítás egy nagyobb összeállítás, például egy dízelmotor részévé válik, akkor egy generátor részévé válhat, amely számos felhasználási lehetőséget biztosít számunkra.
Ezért létfontosságú, hogy alkatrészeink jól illeszkedjenek egymáshoz. Ezért van szükségünk a GD&T-re. Használatával 100 százalékig biztosak lehetünk abban, hogy alkatrészeink pontosan illeszkednek egymáshoz, és pontosan úgy működnek, ahogyan arra szükség van.
Közös rendszer a tervezési szándék kifejtésére
A GD&T egy olyan platformot is biztosít a tervező számára, amellyel a tervezési szándékát az összes érintett részleg felé közvetítheti. Ezek közé tartoznak:
- A gyártás
- Az ellenőrzés
- A tervezési részleg jövőbeli tervezői, akik átveszik a munkát, ha az eredeti tervezőcsoport nem áll rendelkezésre
A definíciók, a szókincs és a szabályok egyszerűek és általánosan érthetők. Ezáltal a szimbólumok minden mérnök számára könnyen lefordíthatók, és nagyszerűen közvetítik a tervezői szándékot.
Idő és pénz megtakarítása
Ez a GD&T használatának legfontosabb előnye. A rendszer használata csökkenti a pazarlást, mivel csökkenti a tervezési-gyártási-próbaszerelési-illesztési ciklusok számát.
Ez azért van, mert a legyártott alkatrészek első próbálkozásra jól illeszkednek, és ennek következtében a selejtek száma alacsony lesz. A közös nyelv használata csökkenti az ellenőrzéshez szükséges erőfeszítéseket is.
Kérje gyártási árajánlatát másodpercek alatt
-
Árajánlat másodpercek alatt
-
Rövid átfutási idő
-
Töredékszállítás
Kérjen ajánlatot
Mit kell figyelembe venni?
A geometriai méretezés és tűrés egy erősebb rendszer a hagyományos tűrésekhez képest. De csak akkor működik, ha minden részleg (tervezés, mérnöki munka, gyártás) jól ismeri az információk olvasását és értelmezését.
Ezért a mérnöki rajzok készítése és a különböző alkatrészjellemzők tűrése során fontos, hogy a termékfejlesztés bármely szakaszában mindenki érdekében, aki a rajzzal kapcsolatba kerül, kövesse az ajánlott irányelveket/egyezményeket.
Ezek betartása biztosítja, hogy a rajz szabványosított legyen, és mindenki egy oldalon álljon, amikor a rajz sajátosságairól van szó. E jó gyakorlatok közül néhány a következő.
A rajz érthetősége
Ez vitathatatlanul a rajz legfontosabb tulajdonsága. Az érthetőség arra utal, hogy az alkatrészjellemzők és a tűrések milyen világossággal vannak megrajzolva a rajzon. A rajz érthetőségének javításának néhány módja:
- Rajzoljon valódi profilokat minden alkatrészjellemzőhöz.
- A méreteket és tűréseket a rajzon kívül (nem felül) jelölje. Használja hatékonyan a fehér teret.
- Az olvasási iránynak állandónak kell lennie. Az olvasónak képesnek kell lennie arra, hogy a rajzot függőlegesen tartva minden méretet el tudjon olvasni.
- A párhuzamos alkatrészjellemzők méreteit térben kell elhelyezni.
- Röviden magyarázza el az alkatrészt és annak funkcióját.
- A szögeket csak akkor adja meg, ha azok nem derékszögűek (90°).
Szoros tűrések csak akkor, ha szükséges
Hacsak az alkatrész illeszkedése/funkciója nem követeli meg, a tűréseket a lehető leglazábban kell tartani. Ez csökkenti a gyártási költségeket és az átfutási időt. Javasoljuk, hogy a gyártási módszer kiválasztását bízzuk a gépészekre.
A tervezőnek meg kell említenie a rajz általános tűréshatárát is. Ez az összes alkatrészjellemzőre vonatkozó szabványos tűrésként működik. Az eltérő tűréshatárral rendelkező alkatrészjellemzők esetében a tervezőnek a megfelelő pozíciókban meg kell említenie azokat.
Ezek a speciális tűréshatárok felülírják az általános tűréseket. A speciális tűréshatárok megadásakor részesítse előnyben a funkcionális jellemzőket más jellemzőkkel szemben.
GD&T jellemzők & Szimbólumok
A GD&T nyelv nagyjából minden olyan tulajdonságot képes definiálni, amely a tökéletes összeszerelés biztosításához szükséges.
A rendszer számos szimbólumot használ erre a célra. Ahhoz, hogy ezeket a mérnöki szimbólumokat helyesen használhassuk a rajzokon, először meg kell ismernünk e rendszer néhány alapvető építőelemét.
A különböző definíciókkal, terminológiákkal és szabályokkal kezdhetjük, mielőtt rátérnénk a GD&T szimbólumokra.
Névleges méretek
A névleges méret a valódi profil jellemző mérete. Ez az a pontos méret, amelyet ideális esetben szeretnénk elérni. Az olyan sajátosságoknak, mint a méret, a tájolás, a referenciaponttól való elhelyezkedés, van egy névleges mérete, amelyet a gépészek megcéloznak.
A rajzon ezek egy keretben jelennek meg. Ez megjelenhet számként vagy egy népszerű szabványból, például az ASME-ből.
Jellemző vezérlő keret
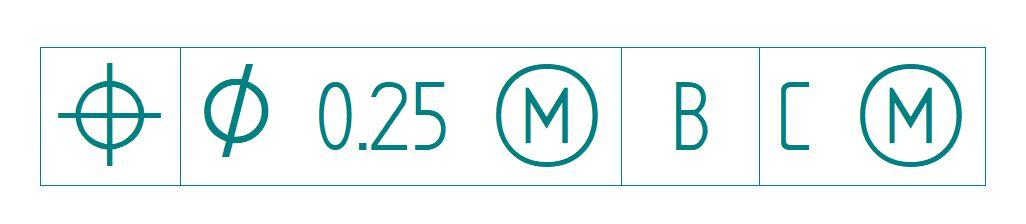
Ez a keret az alkatrészspecifikumokról tartalmaz információkat. Különböző rekeszeket tartalmaz, ahol minden rekesz az alkatrészjellemző egy adott attribútumát határozza meg. A jellemzővezérlő keret egy pillantással közvetíti a megmunkáláshoz és az ellenőrzéshez szükséges információkat.
A jellemzővezérlő keret az alábbiak szerint 4 fő részre osztható.
Vezető nyíl
Ez a nyíl az ellenőrzött alkatrészjellemzőt jelöli. Ha egy felülethez vezet, akkor a felület geometriai ellenőrzés alatt áll. Ha átmérőmérőt jelöl, akkor a GD&T vezérli a tengelyt. Ez a nyíl egyes esetekben nem feltétlenül van jelen.
Geometriai jellemző szimbólum
Az első rekesz (balról kezdve) tartalmazza a geometriai jellemző szimbólumot. Itt adjuk meg a geometriai jellemzőt. A szimbólumok száma alapján összesen 14, osztályozáskor 15 geometriai jellemzőtípus létezik.
A geometriai jellemzők különböző típusai a következők: formakontroll, profilkontroll, helykontroll, tájoláskontroll stb. Az egyes kategóriákba később mélyebben belemerülünk.
Tulajdonságtűrés rekesz
A 2. blokk maximum 3 (néha 2 vagy 1) különböző szimbólumot tartalmaz.
Az első szimbólum a toleranciazóna típusát mutatja. Az átmérő szimbólum (⌀) átmérőjű zónát (hengeres toleranciazónát) jelöl. Gömb alakú zóna megadásához a szimbólum az “S” betű, amelyet az átmérő szimbólum (⌀) követ. Szimbólum hiányában teljes széles zónát feltételezünk.
A 2. blokk második szimbóluma a tűréshatár értékét adja meg mm-ben. Ennek az értéknek mindig jelen kell lennie a 2. blokkban.
A harmadik szimbólum ebben a blokkban a tolerancia módosítója. Ez az anyagmódosító csak akkor van jelen, ha a jellemzőnek van mérete, például egy furat. Az anyagmódosítókra példa az MMC (Maximum material condition) és az LMC (Least material condition). A rendelkezésre álló különböző módosítókkal kapcsolatos további információkat a cikk további részében tárgyaljuk.
Datumok
A harmadik blokk a dátum(ok)ra vonatkozó információkat adja meg, legalább 1 és legfeljebb 3 dátummal. A 3 dátum esetében elsődleges, másodlagos és harmadlagos dátumként hivatkoznak rájuk, és mindegyik más-más dobozba zárva jelenik meg (a fenti képen például 2 van). Ez a blokk tartalmazhat egy anyagmódosítót is.
A fenti információk segítenek abban, hogy megértsük, hogyan kell egy feature vezérlőkeretet olvasni. Ahhoz, hogy jobban megértsük, hogyan lehet a tűrést az anyagállapot-módosítók segítségével beállítani, ismernünk kell a különböző lehetőségeket.
Az anyagállapot-módosítók
Az anyagállapot-módosítók azt a szándékot közvetítik, amikor a tűrés egy adott feature méretre vonatkozik. Amikor bármelyik feature-hez tűréseket adunk meg, az két anyagfeltételt állapít meg
- Maximális anyagfeltétel
- Legkisebb anyagfeltétel
Tegyük fel egy 100 mm átmérőjű tengelyt. Ha gyártáskor ±0,2 mm tűrést adunk meg, akkor 100,2 mm-nél a tengely a maximális anyagmennyiséget tartalmazza. Ezt értjük a maximális anyagállapot alatt.
Másrészt ugyanez a tengely, ha 99,8 mm átmérővel gyártjuk, a legkisebb anyagmennyiséget fogja tartalmazni. Ezeket a határértékeket nevezzük anyagállapotoknak.
A geometriai tűréseket 3 különböző módon lehet alkalmazni egy jellemzőre. Ezek a következők:
- Maximális anyagfeltétel
- Legkisebb anyagfeltétel
- A feature méretétől függetlenül
Maximális anyagfeltétel módosító
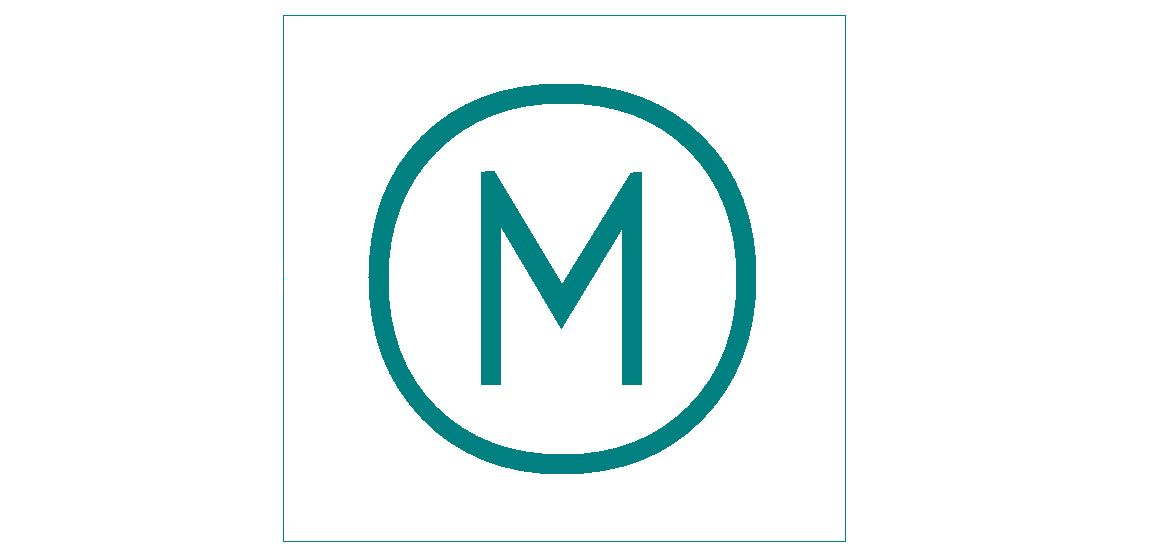
A feature vezérlőrekeszében a tűrésérték után bekarikázott “M”-mel jelöljük ezt a feltételt. A feature a maximális anyagot tartalmazza ennél a feature-méretnél.
A külső FOS (Feature Of Size), például egy tengely átmérője esetén az MMC a legnagyobb méretet jelenti. Belső FOS esetén, mint például egy furat átmérője, az MMC a lehető legkisebb méretet jelenti a megadott tűréshatárokon belül, mivel a kisebb furat azt jelenti, hogy több anyag marad.
Ha geometriai tűrést kell alkalmaznunk a maximális anyagállapotnál, akkor ezt az állapotot megemlítjük a jellemzővezérlő keretben.
Legkisebb anyagállapot módosító
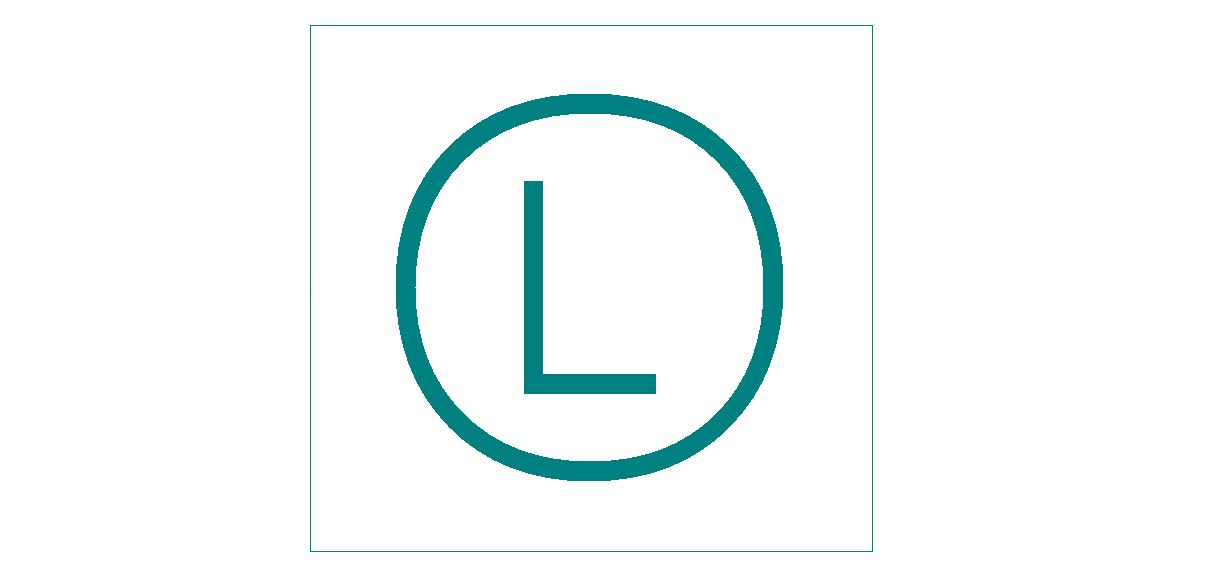
A LMC az az állapot, ahol az anyag a legkevesebb anyagot tartalmazza.
A külső FOS esetében ez lesz a lehető legkisebb méret a megadott határokon belül. Belső FOS esetén pedig a lehető legnagyobb méret lesz.
Ezt a módosítót egy körben lévő “L” betűvel ábrázoljuk. Ez a funkció eltávolítja a felesleges anyagot és ezáltal a súlyt. Ahhoz, hogy a geometriai tűréseket ennél a feltételnél alkalmazzuk, ennek szimbólumát használjuk a jellemzővezérlő keretben.
Függetlenül a jellemző méretétől (RFS)
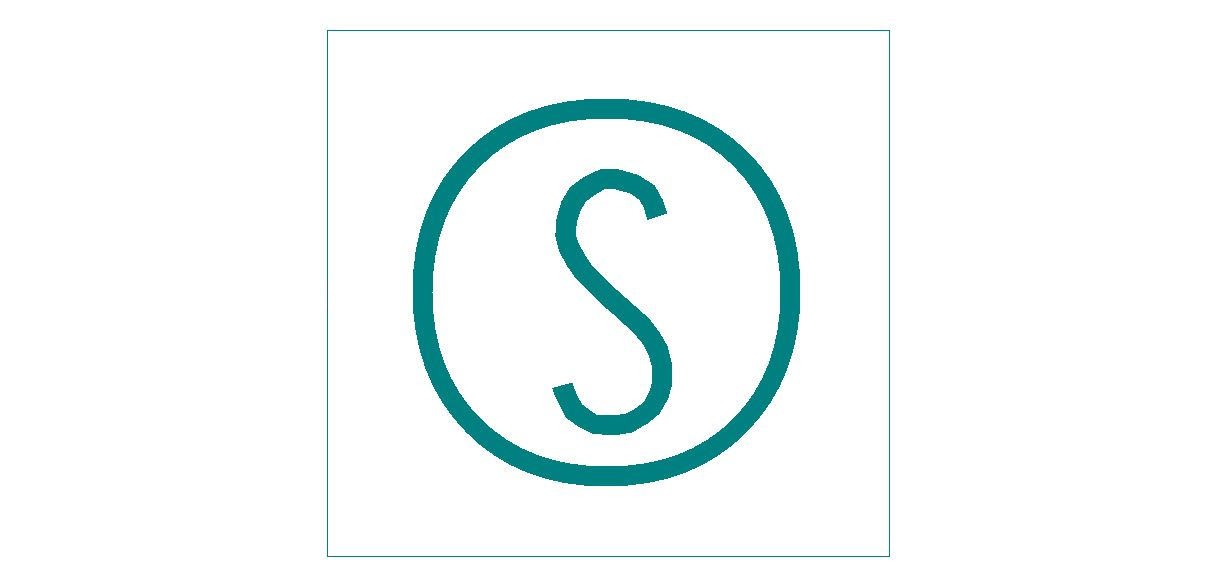
Ha az adott geometriai tűréseket a FOS méretének bármely növekményénél alkalmazzuk, ezt RFS-szel jelöljük. Az RFS szimbóluma a körbe zárt “S” betű volt, de erre már nincs szükség, mivel az RFS ma már alapállapotnak számít, és nincs szükség szimbólumra.
Datumok és Feature Callouts
A datumok a mérettűrések mérésének referenciapontjai. Ez lehet egy pont, egy vonal vagy egy sík. Az adatpontok segítségével határozzuk meg a dátum-referenciakereteket (DRF). A DRF alapvetően egy 3D koordinátarendszer, amely segít meghatározni az összes többi jellemző helyzetét a DRF-hez képest.
Az alkatrészek hatékony gyártásához és ellenőrzéséhez 6 szabadságfokot (3 transzlációs és 3 rotációs) kell szabályoznunk. Ezeket a szabadságfokokat a DRF segítségével állapítjuk meg.
A dátummegjelenések a tényleges alkatrészmegjelenések, mint például a furatok és a hornyok. Ezek eltérést mutathatnak a kívánt pozíciókhoz képest.
A datum-featurek közül azokat részesítjük előnyben, amelyek a szerelvényben lévő más alkatrészekkel illeszkednek. Egynél több vonatkozási pontot is megemlíthetünk a jellemzővezérlő keretünkben. A DRF-ek sorrendje szerint a feature vezérlőkeretben az alkatrészek a DRF-ekkel csökkenő fontossági sorrendben párosíthatók.
GD&T szimbólumok
A feature-ek különböző geometriai jellemzőinek ábrázolására legfeljebb 14 GD és T szimbólum áll rendelkezésre. Ezek a szimbólumok segítenek abban, hogy ezeket a jellemzőket a végtermékkel szemben támasztott követelményekként megadjuk.
Ezeket a szimbólumokat a funkcióvezérlő keret első rekeszében helyezzük el. A tűrésvezérlés ezen típusait fogjuk megvizsgálni.
Formavezérlés
Amint a neve is mutatja, a formavezérlés a jellemző végső formájára vagy alakjára vonatkozik. A formavezérlést úgy határozzuk meg, hogy a geometriai tűrésnek az ideális formától való eltérését korlátozzuk. Néhány népszerű formavezérlési jellemző a következő.
Egyenesedés
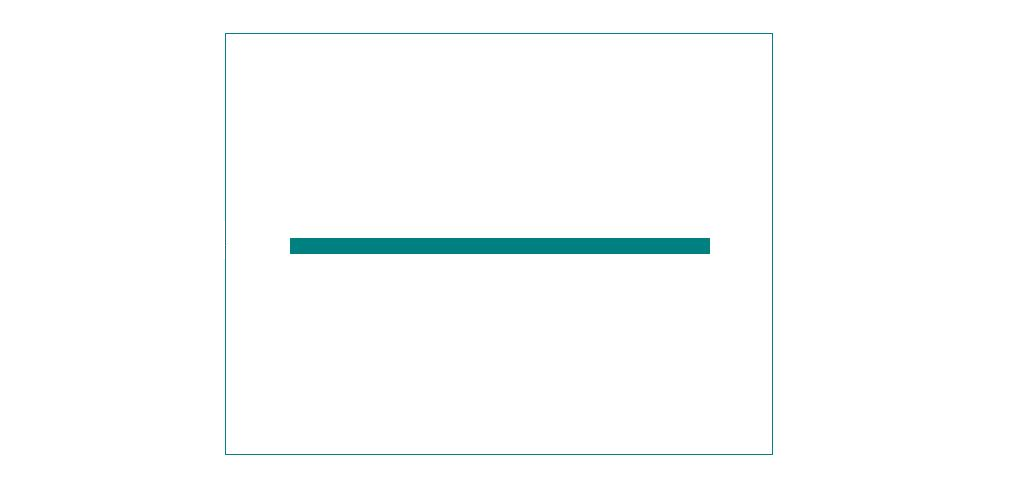
Egy jellemző (például egy tengely vagy egy felület) egyenességjellemzőjének jelölésére az első rekeszben annak szimbólumát (egy egyenes vízszintes vonal) használjuk.
A felület egyenessége vonatkozhat sík felületekre, például egy blokk oldalára, vagy ívelt felületekre, például egy henger oldalára a tengely irányában. Meghatározza egy egyenes (2 dimenzió) megengedett eltérését a felületen egy meghatározott tűrésen belül.
A tengelyes egyenesség általában például egy tengely vagy egy furat tengelyére vonatkozik. A go/no go mérőeszköz az a vizsgálati eszköz, amellyel meggyőződhetünk arról, hogy az alkatrész megfelel-e az elvárásoknak.
Síkosság
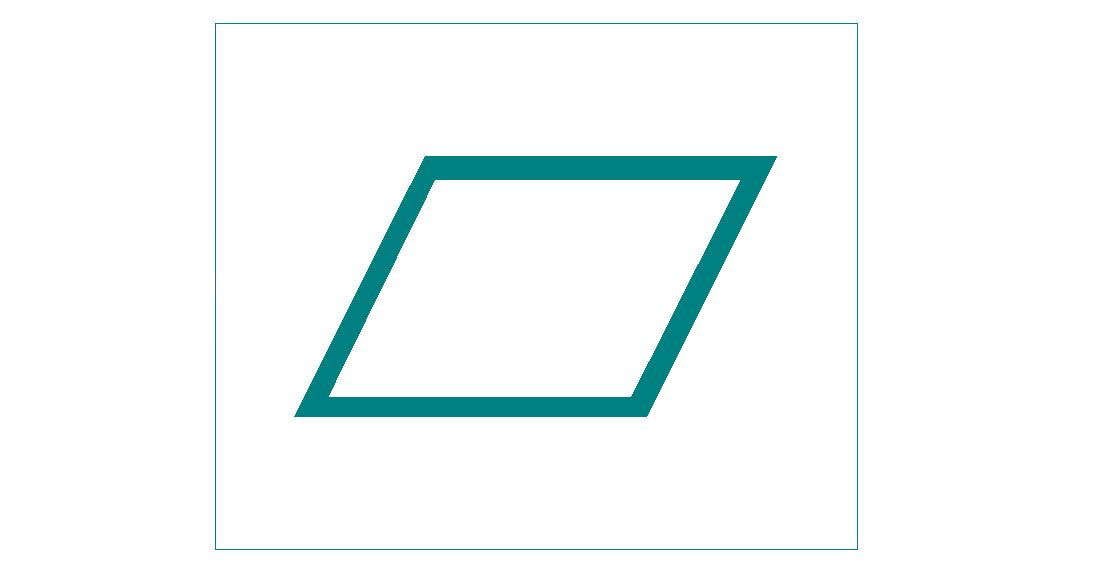
Ezt a jellemzőt olyan jellemzőkre használjuk, mint például az alkatrész felülete. A laposság szimbóluma egy jobbra dőlő paralelogramma. Egy sík felület legmagasabb és legalacsonyabb pontja közötti különbség a síkossága.
A síkosság szimbólumhoz nincs szükség viszonyítási pontokra, mivel csak egy tűréshatárt mutat, amelyen belül az alkatrész teljes felületének 3 dimenzióban meg kell felelnie.
Az eredmények ellenőrzésére magasságmérőt használunk. A felület különböző területeit érinti, hogy megállapítsa, minden pont a tűréshatáron belül van-e.
Körkörösség
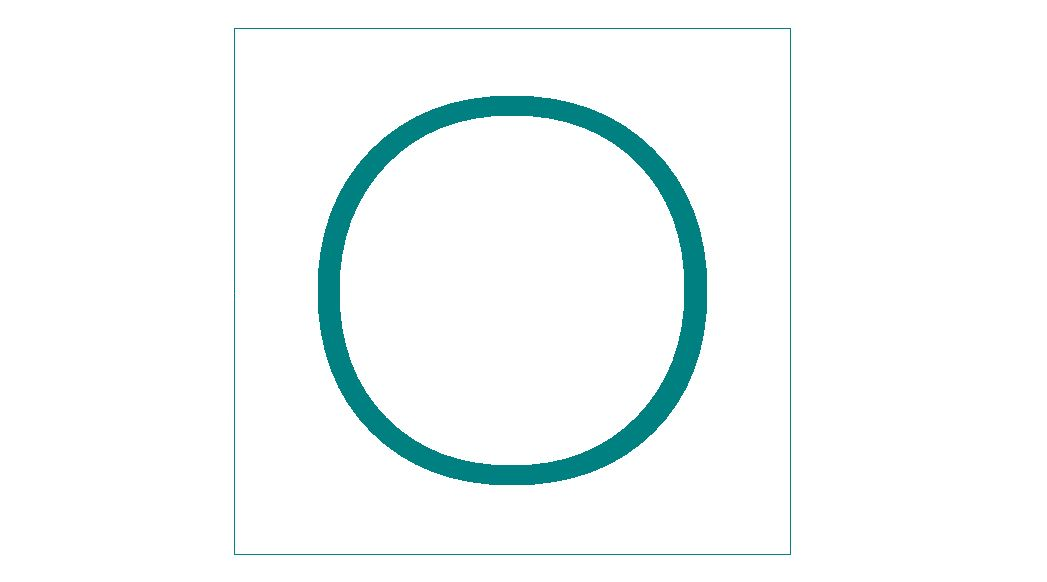
A jellemző körkörössége megmutatja, hogy az alkatrész kerületének milyen közel kell lennie a tökéletes körhöz. Az alkatrész tengelyére merőleges síkban lévő 2 koncentrikus kör segítségével határozza meg a megfelelő tűréstartományt 2D-ben. A végső mérések minden pontjának a körök közé kell esnie.
Ez a jellemző körként jelenik meg a jellemző vezérlőkeretének első rekeszében.
Hengeresség
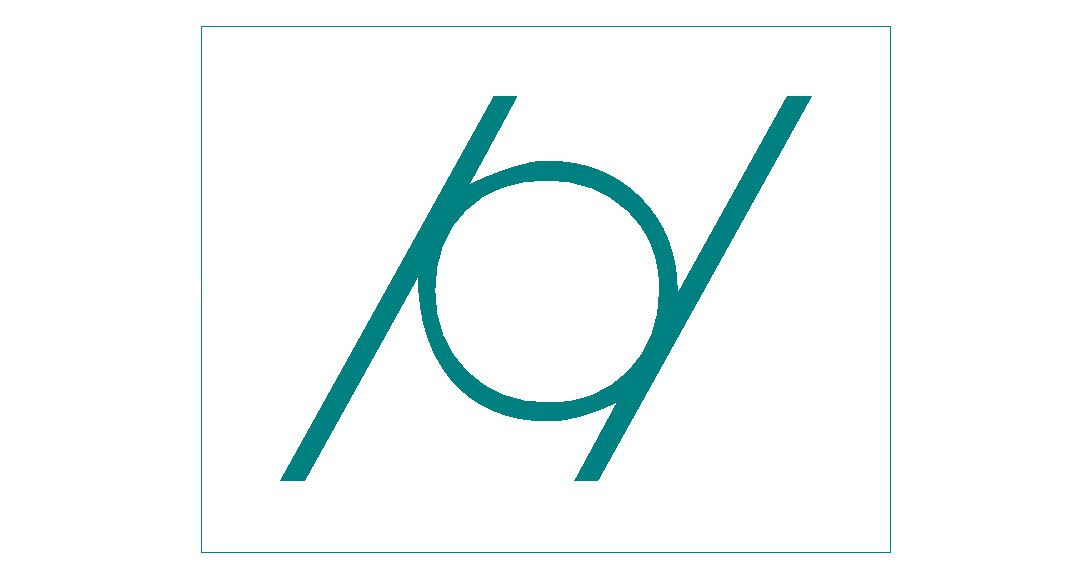
A hengeresség alapvetően kör alakú 3D-ben, ami azt jelenti, hogy az alkatrész teljes hosszában végigfut.
Ez a jellemző más hengeres jellemzőket is leír, például a kúposságát, egyenességét és kerekességét. Ezért ennek a jellemzőnek az ellenőrzése is költséges.
Profilvezérlés
Profilvezérléssel szabályozzuk a jellemző körüli 3D tűrésövezetet. Ez a funkció segít nekünk abban, hogy toleranciahatárokat adjunk a fejlett görbéknek és alakzatoknak.
Egy olyan funkciónak, amely jó a fejlett görbékhez, természetesen az egyszerűbb görbékkel is jól kell működnie. Ez teszi a profilvezérlést rendkívül sokoldalúvá. Ezért egyes tervezők azt javasolják, hogy hagyjunk fel minden más vezérlőelemmel, és csak a profilvezérlőkkel dolgozzunk.
Ezek a vezérlők a fejlett görbe körül tűréshatárt képeznek azáltal, hogy mindkét oldalon utánozzák azt. Ezután megakadályozza, hogy a jellemzőgörbe bármely pontja a tűréshatáron kívülre kerüljön. A profilvezérléseknek két típusa van.
Vonalprofil
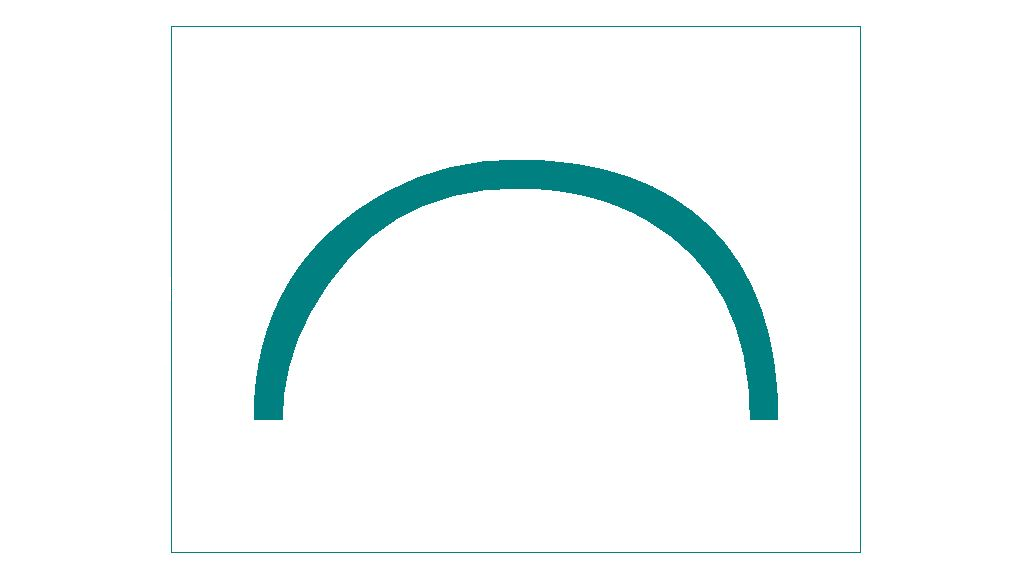
A vonalprofil az alkatrész változó 2D keresztmetszetei körül egy tűréshatárt hoz létre. Egy alkatrészjellemző egyes vonalelemeit vezérli.
A vonalprofil-vezérlés az ideális görbét a tűréshatárok mindkét oldalán követi. Az alkatrész görbéjének minden pontjának ezeken a határokon belül kell lennie.
Felületi profil
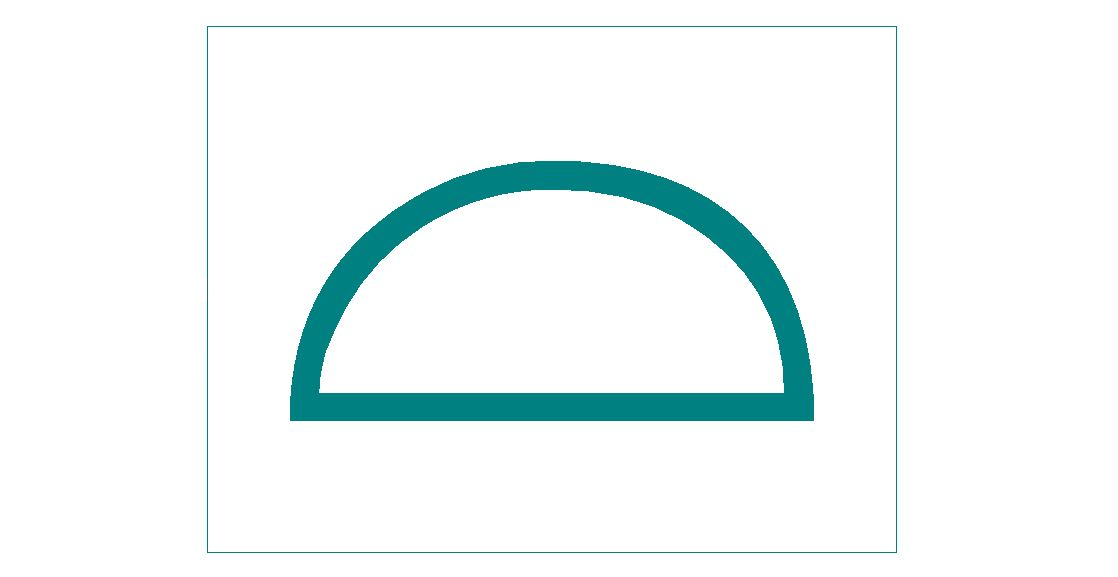
A felületi profilvezérlés népszerűbb a vonalvezérléshez képest. A kétdimenziós tűréshatár helyett a felületprofil-vezérlés egy 3D-s zónát hoz létre a felület körül.
A táblázat felületének minden pontjának a két virtuális síkon belül kell lennie.
Orientációs vezérlés
Arientációs tűréshatár egy meghatározott viszonyítási ponthoz viszonyítva szabályozza a jellemző tájolását. A GD&T-ben háromféle orientációvezérlés létezik.
Szögeltség
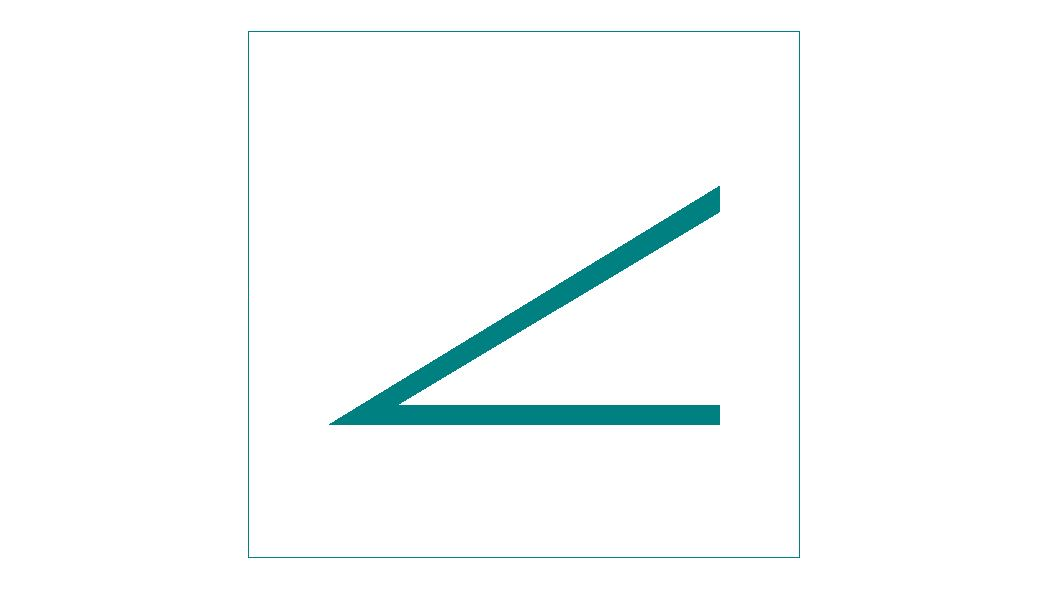
A szögeltségvezérlés egy jellemzőnek az alapponthoz viszonyított szögét tartja kordában. Használhatjuk egy 2D-s vonal szabályozására, de népszerűbb a felületek (3D-s) ellenőrzés alatt tartására.
Ez a fajta szoros szabályozás a szöget és a felület síkosságát tartja ellenőrzés alatt, és olyan alkatrészjellemzőkhöz ajánlott, amelyek a szögletes felületen keresztül illeszkednek más alkatrészekhez.
Fontos megjegyezni, hogy a szögletesség jellemző közvetve szabályozza a szöget, lényegében nem azonos a szögtűréssel (pl. +/- 2°). A szükséges szög inkább az e vezérlés által meghatározott méretkövetelmények betartásának eredménye.
Párhuzamosság
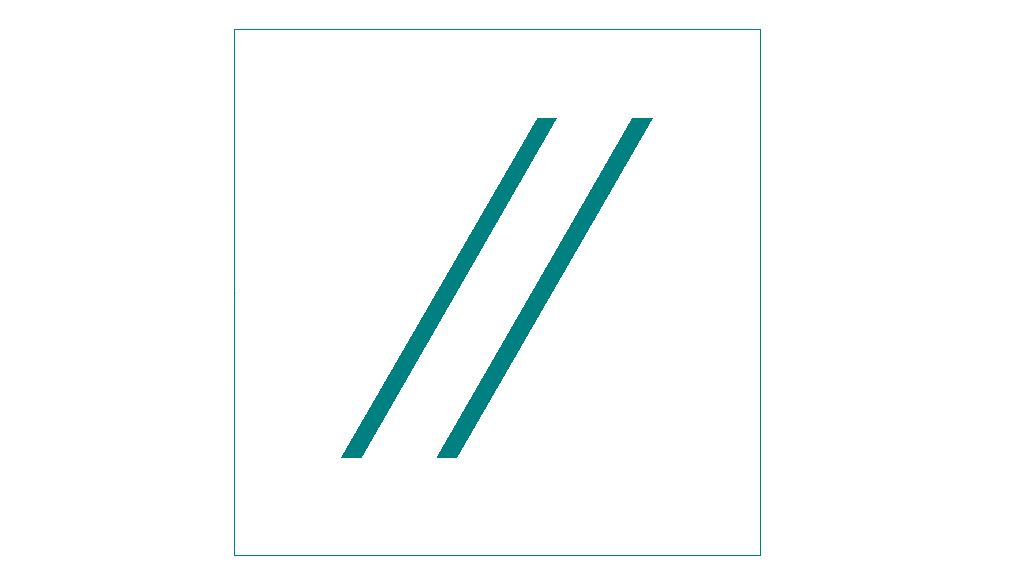
A párhuzamosság a szögletesség egy kifinomult formája. Itt az adatpont az a felület, amelyet utánoznunk kell, a szöget pedig 0°-ra állítjuk. A párhuzamosságnak 2 típusa van: a felületi párhuzamosság és a tengelypárhuzamosság.
Választhatunk egy tengelyt vagy egy felületet viszonyítási pontként. Ez lesz a viszonyítási pontunk, és a feature vezérlőkeret 3. blokkjában hivatkozunk rá, mint a feature viszonyítási pontjára.
A szögpárhuzamossághoz hasonlóan nem a tényleges szöget szabályozza, hanem a követelmények tűréshatár formájában történő lefektetésével biztosítja azt.
Perpendicularity
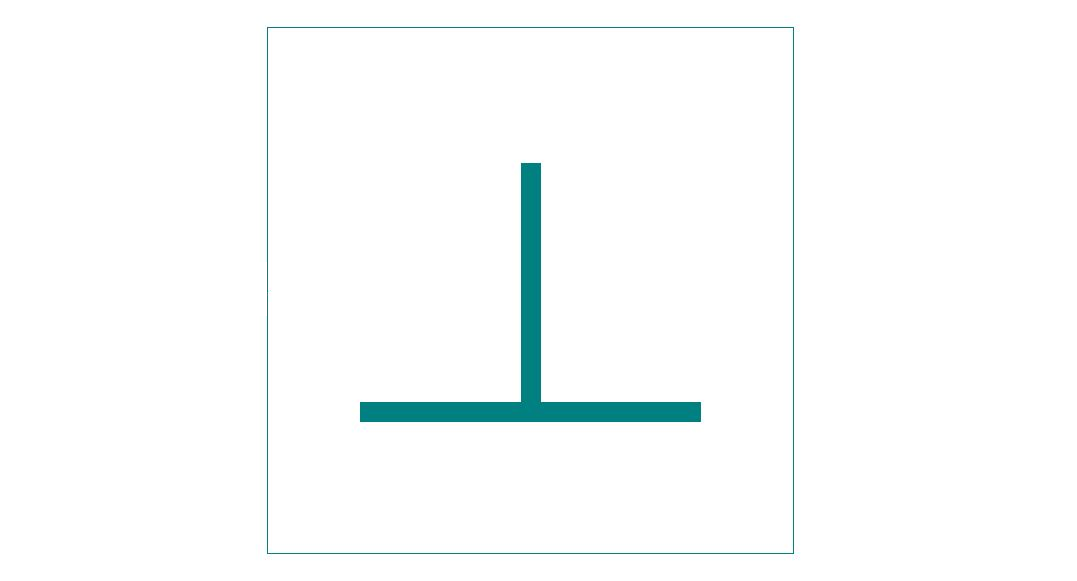
A perpendicularity szintén a szögletesség egy speciális formája, ahol a szöget 90°-ban határozzák meg. Ez egy trükkös szabályozás, mivel két nagyon különböző típusú követelményt jelenthet.
Van a felületi merőlegesség ( Szimbólum:⟂), és van a tengelyre merőlegesség (Szimbólumok: ⟂+⌀).
A felület merőlegessége azt adja meg, hogy egy felületnek vagy vonalnak merőlegesnek kell lennie egy vonatkozási felületre vagy vonalra, hasonlóan a szögletességhez. Az ellenőrzéshez két virtuális síkot/vonalat feltételezünk a célfelület körül.
A tengely merőlegessége megadja, hogy egy tengelynek mennyire kell merőlegesnek lennie az említett viszonyítási pontra. Ez úgy történik, hogy a céltengely körül egy virtuális hengert állítunk fel egy olyan felületen, amely pontosan párhuzamos az alapfelülettel.
Helyzetvezérlés
A helytűrésvezérlés egy jellemzőnek az alapponthoz viszonyított helyzetének szoros ellenőrzésére szolgál. A helytűrés-szabályozásnak négy fő típusa van.
Központosság
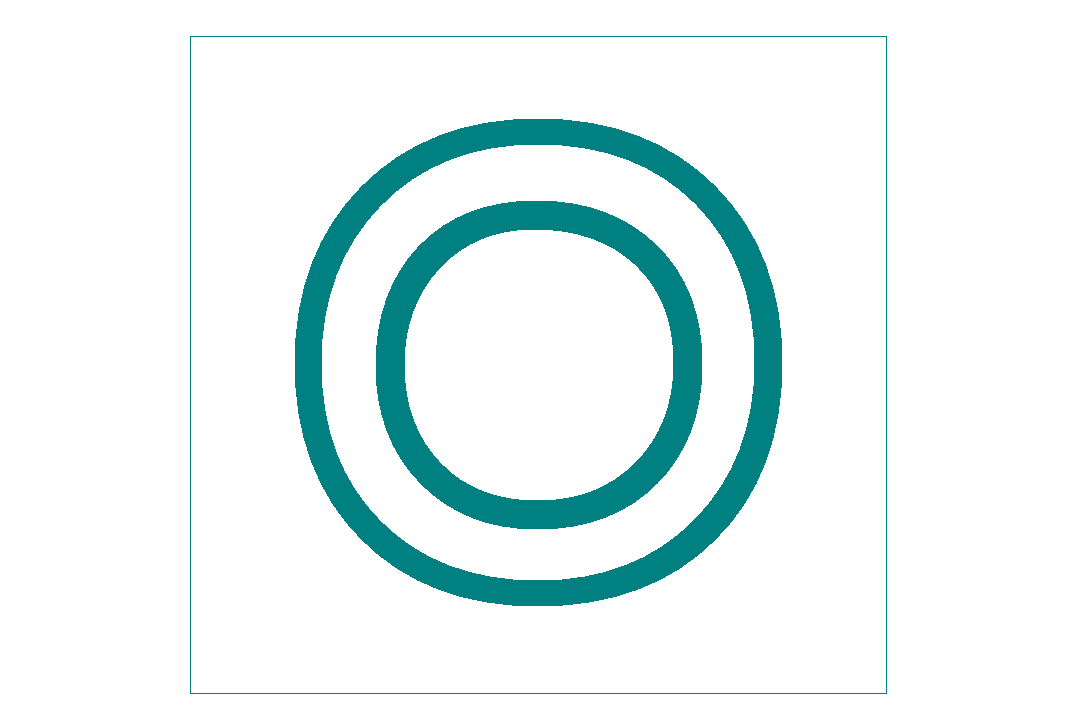
A központosság, más néven koaxialitás (bár nem pontosan ugyanaz) szabályozása fenntartja a kör alakú, valamint a hengeres jellemzők koncentricitását.
Az alkatrész tengelyét egy hivatkozott jellemző tengelyéhez (vonatkoztatási tengely) rögzíti. Mindkét alkatrész tengelyét úgy határozza meg, hogy azok az alkatrészek középpontjaiban legyenek.
Ez a vezérlés némi zavart okozhat, mivel a tengelyek külső mérésekből származnak, nem pedig a tényleges elhelyezésükből.
A koaxialitás a felületi méréseken alapuló 3D tűrésövezetet hoz létre, amelyen belül az alkatrésznek feküdnie kell.
Szimmetria
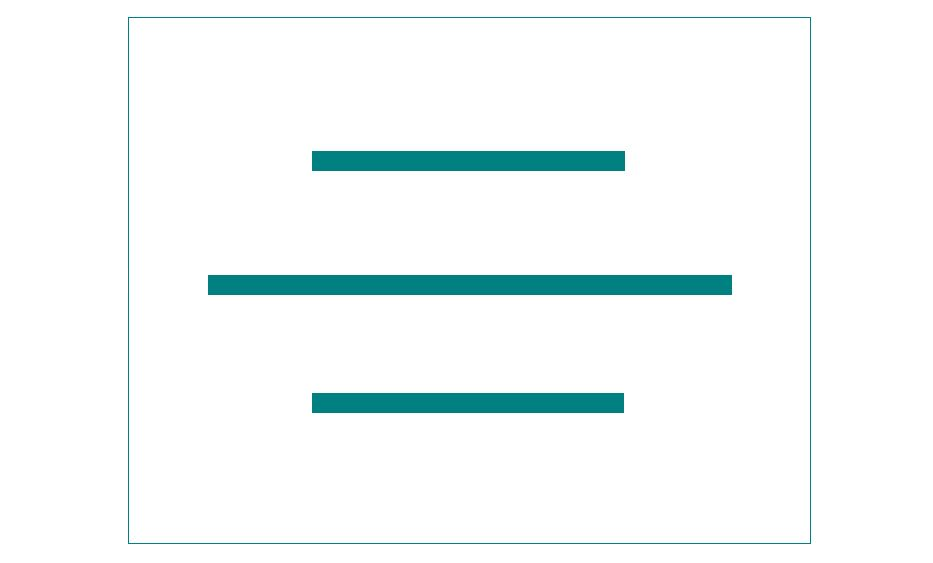
A szimmetriahívás egy középsíkot határoz meg, amely körül a jellemző két része egyenlő távolságra helyezkedik el. A két oldali két pont középpontjának a központi sík körül meghatározott tűréshatáron belül kell lennie.
A szimmetriakihívás nem túl gyakori. Nagyon korlátozottan használható, és az ellenőrzése is nehézkes. Szükségünk van egy CMM-re a végső szimmetria ellenőrzéséhez.
A valódi pozíció
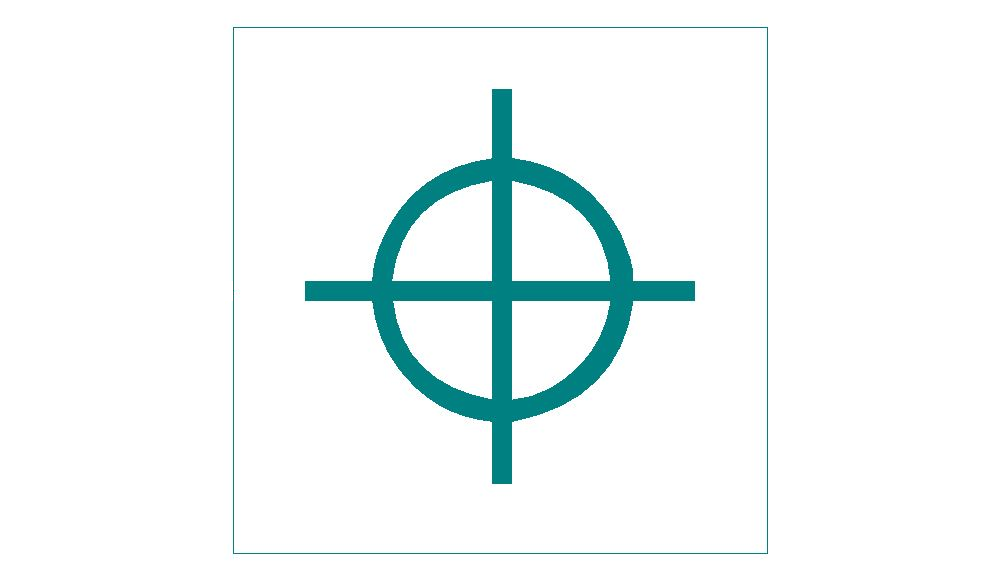
A valódi pozíció (népszerű nevén pozíció) egy nagyon hasznos hívószó, és széleskörű használatra talál a GD&T-ben.
A pozíció meghatározza, hogy egy jellemző tényleges pozíciója mennyire térhet el a tervezett pozíciójától. A definíció tartalmazza a vonatkoztatási síkot, amelyre a mérés vonatkozik.
A definíció gyakran tartalmaz egy átmérő jelet (⌀), hogy kiemelje, hogy a tűréshatár egy kör, nem pedig csak az X és Y tengely (amiről a cikk elején beszéltünk, hogy ez volt az oka a GD&T létrehozásának).
Itt egy nagyszerű videó, amely bemutatja, hogyan használjuk a tűréseket egy rajzon, a valós pozíció használatával:
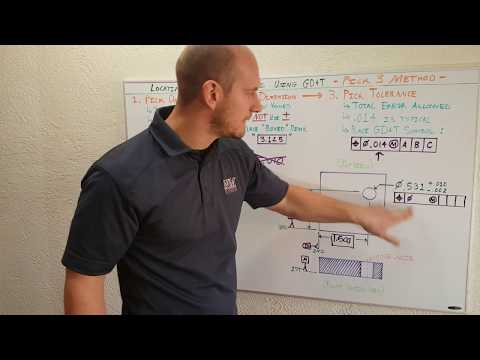
How to Apply GD&T Position Tolerance to a Hole
Runout Controls
A kifutásvezérlőkkel mérjük egy alkatrészjellemző eltérését a kijelölt pozíciójától egy meghatározott viszonyítási ponthoz képest. Ezt a vezérlést kör alakú jellemzőknél használjuk. Lényegében annak imbolygását méri a jellemzőnek a rögzített vonatkozási pont körüli elforgatásával.
A kifutásszabályozásnak két típusa van.
Körkörös kifutás

A körkörös kifutás két dimenzióban működik a különböző alkatrészjellemzők alakjának, helyének és tájolásának ellenőrzésére. Ehhez a 2D-s kifutáshoz egy vonatkoztatási tengelyt kell hozzárendelnünk, hogy ellenőrizhessük ezeket a jellemzőket.
A GD&T szakzsargonban a körkörös kifutást általában kifutásként ismerik. A kifutás a felületi elemek elforgatás általi eltérését méri.
Ez azt jelenti, hogy például a tengelyt elforgatjuk a vonatkoztatási tengelye körül, és a jellemző elemet megmérjük a tűrés szempontjából. Lényegében korlátozza a működő tengely rezgését, hogy hosszabb élettartamot biztosítson a csatlakozó alkatrészeknek, például a csapágyaknak.
Teljes kifutás
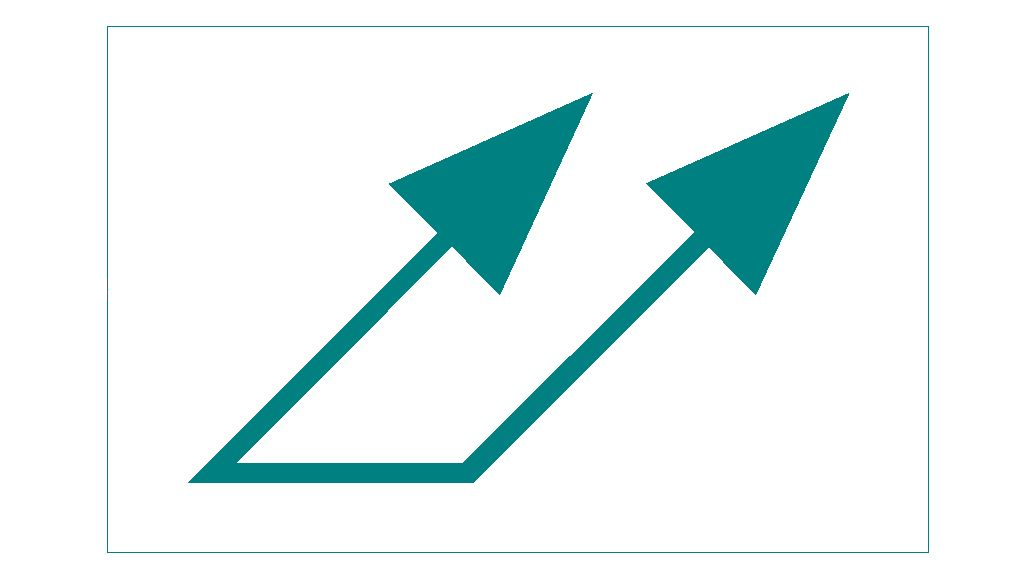
A teljes kifutás a körkörös kifutás 3D-s megfelelője. Ez szabályozza a formát, az elhelyezkedést és a tájolást is. De az egyes keresztmetszetek ellenőrzése helyett (mint a körfutásnál) a teljes felületet ellenőrzi. Így a teljes kifutás használata szigorúbb ellenőrzést biztosít a jellemzőkre vonatkozóan.
Kontroll
Minden iparágban problémát jelenthet, ha a gyártási folyamat nem felel meg a tervezési előírásoknak. Míg egyes esetekben az ügyfelek élete kerülhet veszélybe, más esetekben a termékvisszahívás hatalmas anyagi veszteségekhez vezethet.
Még ha az eredmények nem is olyan rosszak, egy vállalat hírneve nagyban függ a termékek és szolgáltatások minőségétől.
A DDR&T szabványosítja az ellenőrzési folyamatot azáltal, hogy az ellenőrök a tervezővel egy platformra kerülnek. Ez sok akadályt kiküszöböl. A GD&T azonban egy hatalmas téma.
Mint láttuk, számos, egymástól nagyon eltérő geometriai jellemző létezik, amelyek a GD&T-vel ellenőrizhetők. E különbözőség miatt az egyes jellemzők ellenőrzése sajátos módszert, eszközt és szakértelmet igényel.
Ezek közül néhány jellemző a legegyszerűbb eszközökkel is mérhető, míg másokat lehetetlen mérni fejlett berendezések, például koordináta-mérőgép (CMM) nélkül.
Az ellenőröknek tudásra és készségre van szükségük a különböző mérőeszközök, például a mérőórák, mikrométerek, nóniuszok, felületi mérőlemezek és koordináta-mérőgépek használatához, hogy az alkatrészek pontosságát kielégítően ellenőrizhessék.