Gineers gebruiken CAD software om alle benodigde onderdelen en componenten voor het project te ontwerpen. In de digitale wereld is het gemakkelijk om perfectie te bereiken. In het echte leven is fabricage nooit 100% nauwkeurig.
Soms kunnen afwijkingen van enkele millimeters van de basisafmetingen absoluut in orde zijn. Tegelijkertijd kunnen twee op elkaar passende componenten een extreem hoge nauwkeurigheid vereisen.
Om de verwachte afwijking binnen een vooraf bepaald bereik te houden, is het mogelijk gebruik te maken van engineeringtoleranties. Dimensietoleranties zijn heel gebruikelijk, maar missen manieren om enkele zeer belangrijke aspecten van de fabricage te communiceren. Dit is waar GD&T, of geometrische dimensionering & tolerantie, in het spel komt.
Het is een vorm van het beschrijven van afmetingen en toleranties op een geheel nieuwe manier. Met behulp van een gemeenschappelijke taal van engineering symbolen, helpt het om alle benodigde informatie gemakkelijk te vinden.
- Wat is GD&T?
- Waarom GD&T implementeren?
- Perfecte assemblage
- Gemeenschappelijk systeem om de ontwerpintentie uit te leggen
- Bespaart tijd en geld
- Waarop te letten?
- Intelligibility of the drawing
- Nauwkeurige toleranties alleen indien nodig
- GD&T Kenmerken & Symbolen
- Nominale afmetingen
- Feature control frame
- Leader pijl
- Geometrisch karakteristiek symbool
- Feature tolerance compartment
- Datums
- Materiaalconditie modifiers
- Maximale materiaaltoestand modifier
- Least material condition modifier
- Regardless of Feature Size (RFS)
- Datums en Feature Callouts
- GD&T Symbolen
- Vormcontrole
- Rechtheid
- vlakheid
- Circulariteit
- Cylindriciteit
- Profile Controls
- Lijnprofiel
- Zuidprofiel
- Orientatiebesturingselementen
- Angulariteit
- Parallelliteit
- Perpendiculariteit
- Location Controls
- Concentriciteit
- Symmetrie
- True position
- Hoe pas je GD&T Positietolerantie toe op een gat
- Uitloopcontroles
- Circulaire uitloop
- Totale uitloop
- Inspectie
Wat is GD&T?
Het is een systeem van symbolen en normen die worden gebruikt door ingenieurs om productie-informatie te verstrekken aan het productieteam.
De redenen voor het gebruik van Geometric Dimensioning and Tolerancing (GD&T) zijn:
- Het zorgt ervoor dat passende onderdelen goed op elkaar passen
- De universele taal werkt ongeacht met wie je werkt
- Toleranties geven een limiet aan de slechtst denkbare omstandigheden
- Bepaalt productie- en inspectieprocessen
Stanley Parker wordt gecrediteerd als de ingenieur achter de ontwikkeling van het GD&T-systeem in 1938.
Voor die tijd gebruikten alle functies alleen X-Y assen om bijvoorbeeld de positie van een gat te bepalen. Het geven van een positietolerantie op die schaal betekent dat de positie van het cirkelvormige gat in een rechthoekig patroon kan afwijken van de bedoelde plaats.
Hoewel we eigenlijk zouden willen dat de tolerantiezone een cirkel zou zijn, omdat dit een uniforme meting in alle hoeken mogelijk maakt, terwijl een rechthoek langer is naar de hoeken en korter naar de zijden.
Dus toen Parker zich dat realiseerde, begon hij te werken aan het nieuwe concept dat in de jaren ’50 werd aangenomen als militaire engineeringstandaard.
Heden ten dage is GD&T een belangrijk onderdeel van engineering, vooral bij het maken van onderdelen die CNC-bewerkingsdiensten vereisen. De Amerikaanse norm die de kenmerken beschrijft is ASME Y14.5-2018 en het Europese equivalent is ISO 1101-2017.
GD&T richt zich uitsluitend op de geometrie van het product. Lineaire afmetingen, oppervlakteruwheid, schroefdraad, enz. maken geen deel uit van deze norm.
Waarom GD&T implementeren?
We hebben wel traditionele methoden om afmetingen en toleranties aan te duiden. Dus wat is de noodzaak van geometrische dimensionering en toleranties?
Geometrische dimensionering en toleranties (GD&T) biedt een aantal unieke voordelen ten opzichte van reguliere methoden. Laten we eens kijken welke dat zijn.
Perfecte assemblage
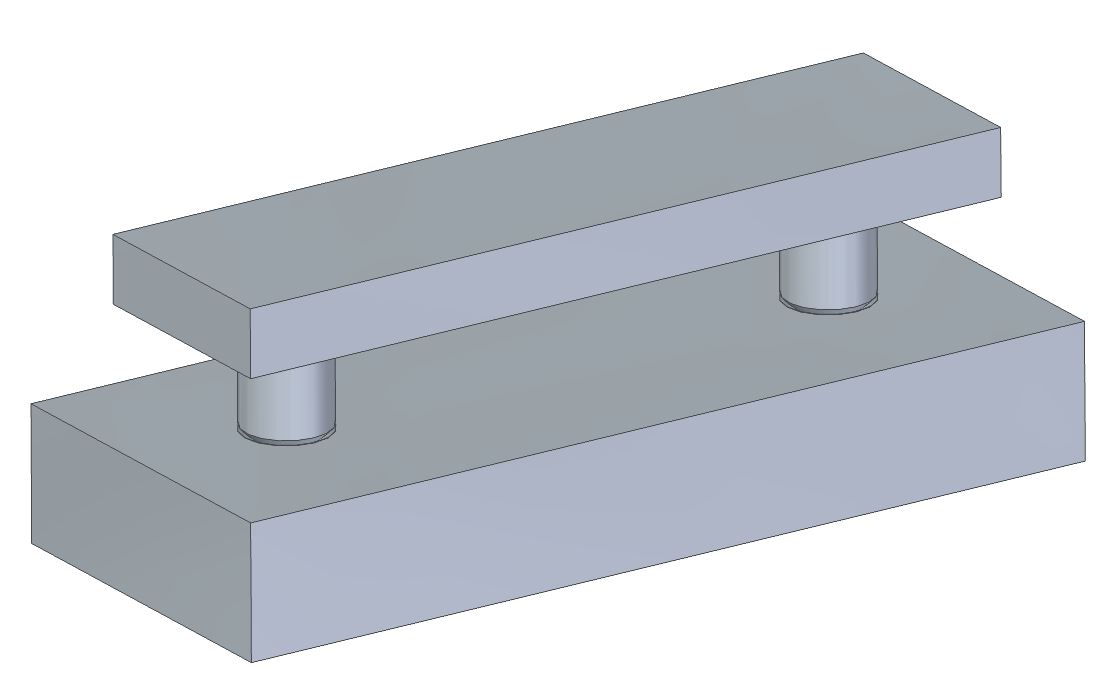
Het belangrijkste nadeel van het gebruik van traditionele dimensionering en toleranties is dat ze informatie over individuele onderdelen en onderdeelkenmerken aanduiden. Het garandeert niet hoe goed onze onderdelen zullen passen en functioneren op het assemblageniveau.
Dit is belangrijk omdat de meeste onderdelen op zichzelf niet bruikbaar zijn. Neem het voorbeeld van een drijfstang. Op zichzelf levert het ons geen voordeel op. Maar wanneer we hem verbinden met de krukas en de zuiger, wordt hij wat nuttiger, omdat hij de lineaire beweging van de zuiger omzet in een draaiende beweging van de krukas.
Wanneer deze assemblage een onderdeel wordt van een grotere assemblage, zoals een dieselmotor, kan hij eindigen als onderdeel van een generator die ons vele toepassingen biedt.
Het is dus van cruciaal belang dat onze onderdelen goed op elkaar aansluiten. Daarom hebben we GD&T nodig. Door het te gebruiken, kunnen we er 100 procent zeker van zijn dat onze onderdelen bij elkaar passen en precies zo functioneren als nodig is.
Gemeenschappelijk systeem om de ontwerpintentie uit te leggen
GD&T biedt de ontwerper ook een platform om zijn ontwerpintentie aan alle relevante afdelingen over te brengen. Deze omvatten:
- Fabricage
- Inspectie
- Toekomstige ontwerpers in de ontwerpafdeling die het werk zullen oppakken als het oorspronkelijke ontwerpteam niet beschikbaar is
De definities, woordenschat en regels zijn rechttoe rechtaan en universeel te begrijpen. Dit maakt de symbolen gemakkelijk te vertalen voor elke ingenieur en een geweldige manier om de intentie van de ontwerper over te brengen.
Bespaart tijd en geld
Dit is het belangrijkste voordeel van het gebruik van GD&T. Het gebruik van dit systeem vermindert verspilling omdat het het aantal ontwerp-fabricage-test fit cycli vermindert.
Dit komt omdat gefabriceerde onderdelen goed passen bij de eerste poging en bijgevolg zal het aantal afkeuringen laag zijn. Het gebruik van een gemeenschappelijke taal vermindert ook de inspanning die nodig is voor inspectie.
Geef uw productiecitaat in seconden
-
Citaat in seconden
-
Korte doorlooptijden
-
Levering door Fractory
Geef citaat
Waarop te letten?
Geometrische dimensionering en tolerantie is een krachtiger systeem in vergelijking met traditionele toleranties. Maar het werkt alleen als alle afdelingen (ontwerp, engineering, productie) goed onderlegd zijn in het lezen en interpreteren van de informatie.
Daarom is het belangrijk om bij het maken van engineeringtekeningen en het tolereren van verschillende onderdeelkenmerken de aanbevolen richtlijnen/conventies te volgen ten behoeve van iedereen die met de tekening te maken krijgt in elk stadium van de productontwikkeling.
Het naleven van deze richtlijnen zorgt ervoor dat de tekening gestandaardiseerd is en iedereen op dezelfde pagina zit als het gaat om tekeningspecificaties. Enkele van deze goede praktijken zijn als volgt.
Intelligibility of the drawing
Dit is aantoonbaar de belangrijkste kwaliteit van een tekening. De begrijpelijkheid verwijst naar de duidelijkheid waarmee onderdeelkenmerken worden getekend en toleranties in de tekening worden weergegeven. Enkele manieren om de begrijpelijkheid van een tekening te verbeteren zijn:
- Teken echte profielen voor alle onderdeelkenmerken.
- Label afmetingen en toleranties buiten de tekening (niet erboven). Gebruik witruimte effectief.
- Leesrichting moet constant zijn. Een lezer moet in staat zijn om alle afmetingen te lezen terwijl hij de tekening rechtop houdt.
- Spatieer afmetingen van parallelle onderdeelkenmerken.
- Leg het onderdeel en zijn functie kort uit.
- Specificeer hoeken alleen als ze geen rechte hoeken (90°) zijn.
Nauwkeurige toleranties alleen indien nodig
Niet als een onderdeel fit/functie dit vereist, moeten toleranties zo los mogelijk worden gehouden. Dit vermindert de fabricagekosten en de doorlooptijd. Het verdient aanbeveling de keuze van de fabricagemethode aan de machinisten over te laten.
De ontwerper moet ook de algemene tolerantie voor een tekening vermelden. Deze fungeert als de standaardtolerantie voor alle onderdeelkenmerken. Voor productkenmerken met een andere tolerantiegrens, moet de ontwerper deze op de juiste posities vermelden.
Deze specifieke tolerantiegrenzen zullen de algemene toleranties overrulen. Bij het specificeren van speciale tolerantiegrenzen, geef de voorkeur aan functionele kenmerken boven andere kenmerken.
GD&T Kenmerken & Symbolen
De GD&T taal is in staat om vrijwel alle kwaliteiten te definiëren die nodig zijn om een perfecte assemblage te garanderen.
Het systeem gebruikt een aantal symbolen voor dit doel. Om deze engineering symbolen correct op tekeningen te gebruiken, moeten we eerst vertrouwd zijn met een aantal fundamentele bouwstenen van dit systeem.
We kunnen beginnen met de verschillende definities, terminologieën, en regels voordat we aan GD&T symbolen toekomen.
Nominale afmetingen
Een nominale afmeting is de kenmerkgrootte van het werkelijke profiel. Het is de exacte afmeting die we idealiter zouden willen bereiken. Kenmerken zoals grootte, oriëntatie, de locatie ten opzichte van een referentiepunt hebben een nominale maat die machinisten als doel hebben.
Op een tekening worden ze weergegeven in een kader. Het kan worden weergegeven als een nummer of van een populaire standaard zoals ASME.
Feature control frame
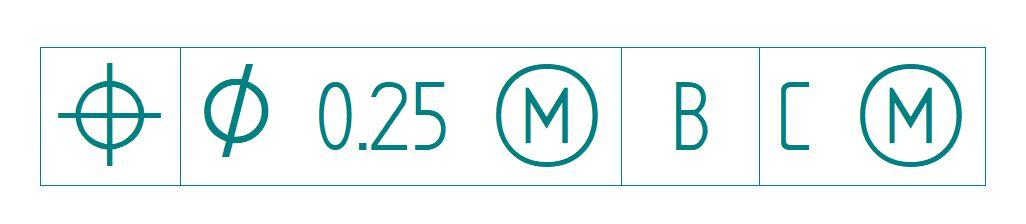
Dit frame bevat informatie over de specifieke kenmerken van het onderdeel. Het bevat verschillende compartimenten waarbij elk compartiment een specifiek kenmerk van het part feature definieert. In één oogopslag geeft het feature control frame de informatie die nodig is voor bewerking en inspectie.
Het feature control frame kan als volgt worden onderverdeeld in 4 hoofdonderdelen.
Leader pijl
Deze pijl markeert het te controleren part feature. Als het leidt tot een oppervlak, het oppervlak is onder geometrische controle. Als het markeert een diametrische dimensie, dan GD&T controleert de as. Deze pijl kan in sommige gevallen niet aanwezig zijn.
Geometrisch karakteristiek symbool
Het eerste compartiment (beginnend van links) bevat het geometrisch karakteristiek symbool. Hier wordt de geometrische eigenschap gespecificeerd. In totaal zijn er 14 soorten geometrische toleranties op basis van het aantal symbolen, en 15 bij classificatie.
De verschillende soorten geometrische karakteristieken zijn vormcontrole, profielcontrole, plaatscontrole, oriëntatiecontrole, enz. We zullen later dieper in elke categorie duiken.
Feature tolerance compartment
Het 2e blok bevat maximaal 3 (soms 2 of 1) verschillende symbolen.
Het eerste symbool geeft het type tolerantiezone aan. Een diametersymbool (⌀) betekent een diametrische zone (cilindrische tolerantiezone). Voor een sferische zone is het symbool de letter “S” gevolgd door het diametersymbool (⌀). Als er geen symbool is, gaan we uit van een totale brede zone.
Het tweede symbool in het tweede blok geeft de waarde van de tolerantiezone in mm. Deze waarde moet altijd aanwezig zijn in het 2e blok.
Het derde symbool in dit blok is de modifier voor de tolerantie. Deze materiaal modifier is alleen aanwezig als de feature een afmeting heeft, bijvoorbeeld een gat. Voorbeelden van materiaal modifiers zijn MMC (Maximum materiaal conditie) en LMC (Minste materiaal conditie). Meer informatie over de verschillende beschikbare modifiers wordt verderop in het artikel besproken.
Datums
Het derde blok geeft informatie over de datum(s) met een minimum van 1 en een maximum van 3 datums. In het geval van 3 datums worden deze aangeduid als primaire, secundaire en tertiaire datums, waarbij elk in een ander kader wordt weergegeven (de afbeelding hierboven heeft er bijvoorbeeld 2). Dit blok kan ook een materiaalmodifier bevatten.
Alle bovenstaande informatie helpt ons te begrijpen hoe we een feature control frame moeten lezen. Om beter te begrijpen hoe tolerantie kan worden aangepast met behulp van materiaalconditie modifiers, moeten we bekend zijn met de verschillende opties.
Materiaalconditie modifiers
Materiaalconditie modifiers geven de intentie aan wanneer tolerantie van toepassing is op een feature bij een specifieke feature grootte. Wanneer we toleranties toekennen aan een vorm, legt dat twee materiaalcondities vast
- Maximale materiaalconditie
- Lage materiaalconditie
Neem een as met een diameter van 100 mm. Als we bij de fabricage een tolerantie van ±0,2 mm aanhouden, dan zal de as bij 100,2 mm de maximale hoeveelheid materiaal bevatten. Dit is wat we bedoelen met de maximale materiaaltoestand.
Aan de andere kant zal dezelfde as, bij fabricage met een diameter van 99,8 mm, de minste hoeveelheid materiaal bevatten. Deze grenzen worden materiaalcondities genoemd.
De geometrische toleranties kunnen op 3 verschillende manieren op een element worden toegepast. Deze zijn als volgt:
- Maximale materiaaltoestand
- Lage materiaaltoestand
- Gelijk aan de afmetingen van de vorm
Maximale materiaaltoestand modifier
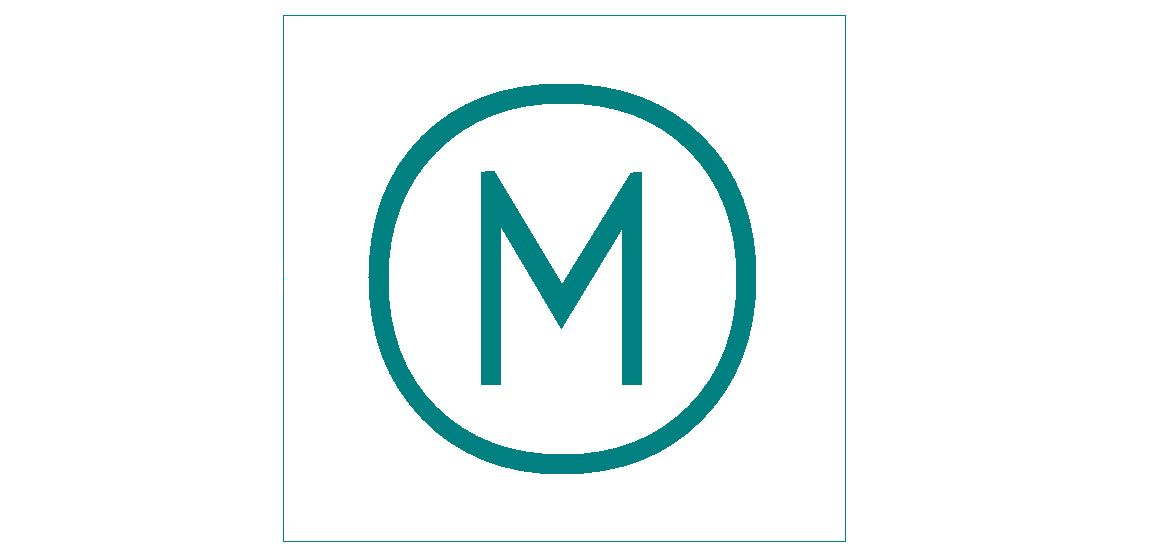
We geven deze toestand weer met een omcirkelde “M” na de tolerantiewaarde in het functiecontrolevak. De feature bevat het maximale materiaal bij deze feature-grootte.
Voor externe FOS (Feature Of Size), zoals de diameter van een as, vertegenwoordigt MMC de grootste grootte. Voor interne FOS, zoals de diameter van een gat, vertegenwoordigt MMC de kleinst mogelijke grootte binnen de opgegeven tolerantiegrenzen, omdat een kleiner gat betekent dat er meer materiaal overblijft.
Wanneer we geometrische tolerantie moeten toepassen op de maximale materiaalconditie, vermelden we deze conditie in het feature control frame.
Least material condition modifier
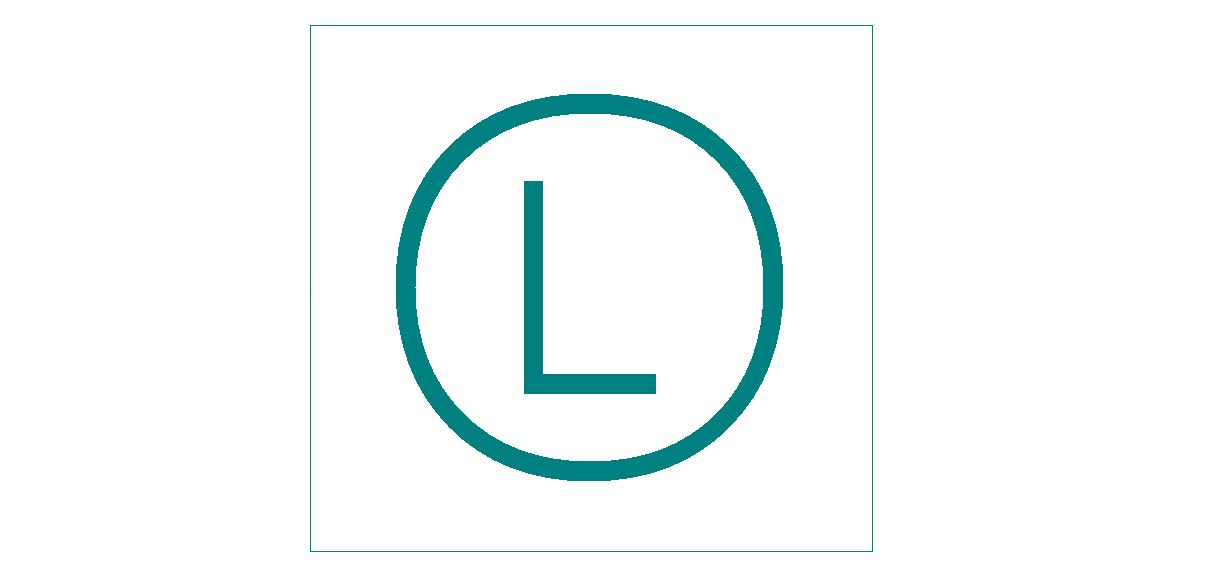
LMC is de conditie waarin het materiaal de minste hoeveelheid materiaal bevat.
Voor externe FOS is dit de kleinst mogelijke omvang binnen de aangegeven grenzen. En voor interne FOS, zal het de grootst mogelijke grootte zijn.
We geven deze modifier weer met de letter “L” in een cirkel. Deze eigenschap verwijdert overtollig materiaal en dus gewicht. Om geometrische toleranties toe te passen op deze conditie, gebruiken we het symbool ervan in het feature control frame.
Regardless of Feature Size (RFS)
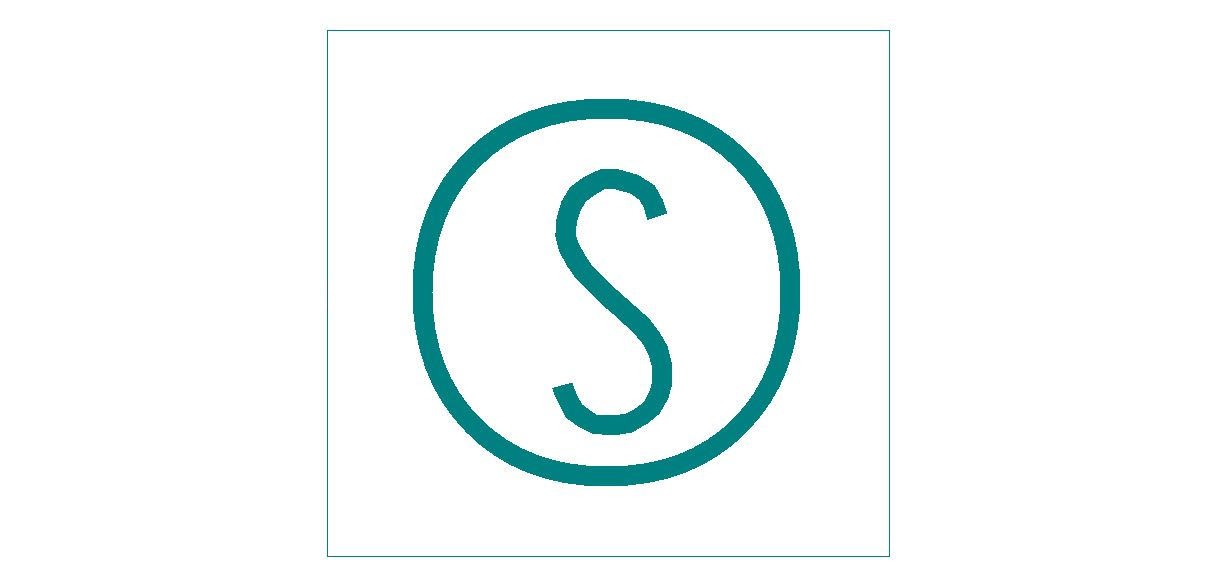
Wanneer de gegeven geometrische toleranties worden toegepast op elke toename van de grootte van FOS, geven we dit aan met RFS. Het symbool voor RFS was de letter “S” omsloten door een cirkel, maar is niet langer nodig omdat RFS nu wordt beschouwd als de standaardconditie, en geen symbool nodig heeft.
Datums en Feature Callouts
Datums zijn referentiepunten voor het meten van dimensionale toleranties. Het kan een punt, een lijn, of een vlak zijn. Met behulp van een nulpunt leggen we referentiekaders (DRF) vast. De DRF is in feite een 3D-coördinatensysteem dat ons helpt de posities van alle andere elementen ten opzichte van de DRF te bepalen.
Er zijn 6 vrijheidsgraden (3 translatie- en 3 rotatiegraden) die wij moeten beheersen om onderdelen effectief te kunnen vervaardigen en inspecteren. Wij gebruiken DRF om deze vrijheidsgraden vast te stellen.
Datum kenmerken zijn de werkelijke onderdeelkenmerken zoals gaten en sleuven. Zij kunnen afwijken van de gewenste posities.
Van alle nulpuntkenmerken, geven wij de hoogste voorkeur aan die welke paren met andere delen in de assemblage. We kunnen meer dan één nulpunt in ons kenmerksturingskader vermelden. Volgens de volgorde van de DRF’s in het element control frame, worden de onderdelen gekoppeld aan de DRF’s in afnemende volgorde van belangrijkheid.
GD&T Symbolen
Er zijn maximaal 14 GD en T symbolen beschikbaar om verschillende geometrische kenmerken van elementen weer te geven. Deze symbolen helpen ons om deze kenmerken te specificeren als vereisten voor het eindproduct.
We plaatsen deze symbolen in het eerste compartiment van het feature control frame. We zullen deze soorten tolerantiecontrole bekijken.
Vormcontrole
Zoals de naam al aangeeft, heeft vormcontrole betrekking op de uiteindelijke vorm van de vorm van het kenmerk. We definiëren vormcontroles om de afwijking van de geometrische tolerantie ten opzichte van de ideale vorm te beperken. Enkele populaire vormcontrole-eigenschappen zijn als volgt.
Rechtheid
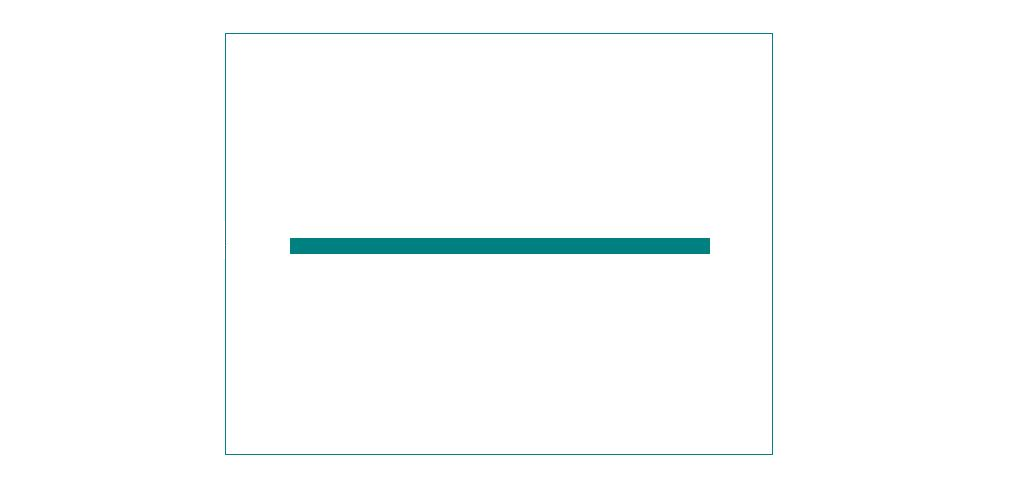
Om de rechtheidseigenschap van een vorm (zoals een as of een oppervlak) aan te geven, gebruiken we het symbool ervan (een rechte horizontale lijn) in het eerste vak.
Rechtheid van het oppervlak kan van toepassing zijn op vlakke oppervlakken zoals een zijde van een blok of gebogen oppervlakken zoals een zijde van een cilinder langs de richting van de as. Zij bepaalt de toelaatbare variatie van een lijn (2 dimensies) op het oppervlak binnen een gespecificeerde tolerantie.
Axiale rechtheid is gewoonlijk van toepassing op de as van een as of een gat, bijvoorbeeld. Go/no go gauge is het inspectie-instrument dat wordt gebruikt in het proces om ervoor te zorgen dat het onderdeel voldoet aan de eisen.
vlakheid
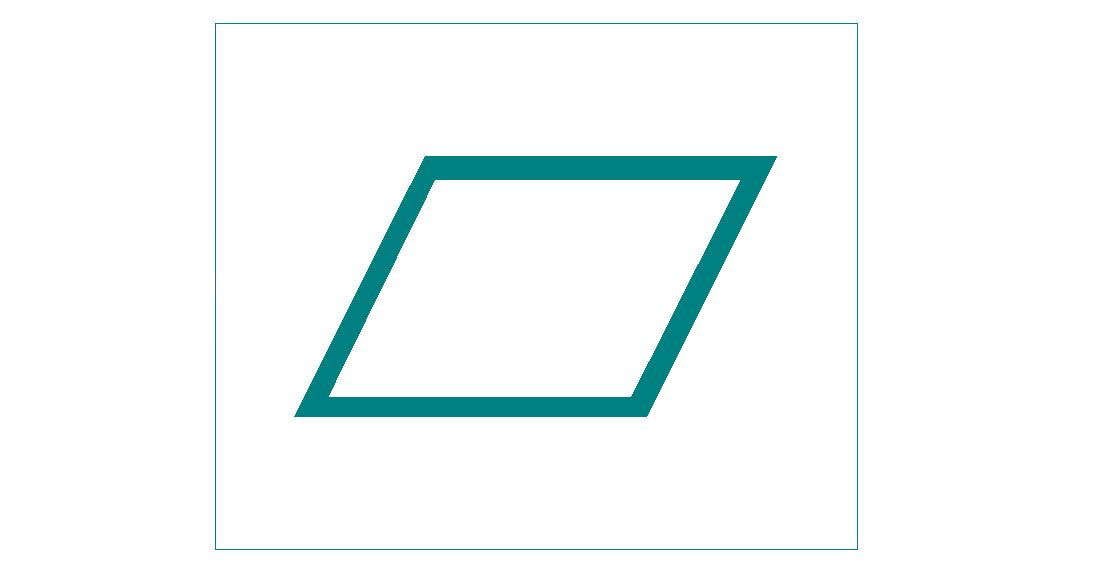
We gebruiken deze eigenschap voor kenmerken zoals het aangezicht van een onderdeel. Het symbool voor vlakheid is een naar rechts gekanteld parallellogram. Het verschil tussen het hoogste en laagste punt van een vlak oppervlak is de vlakheid.
Het vlakheidssymbool heeft geen nulpunten nodig, omdat het alleen een tolerantiebereik aangeeft waarbinnen het gehele oppervlak van een onderdeel in 3 dimensies moet voldoen.
Een hoogtemaat wordt gebruikt om de resultaten te controleren. Het raakt verschillende gebieden van het oppervlak aan om te bepalen of alle punten binnen de tolerantiezone liggen.
Circulariteit
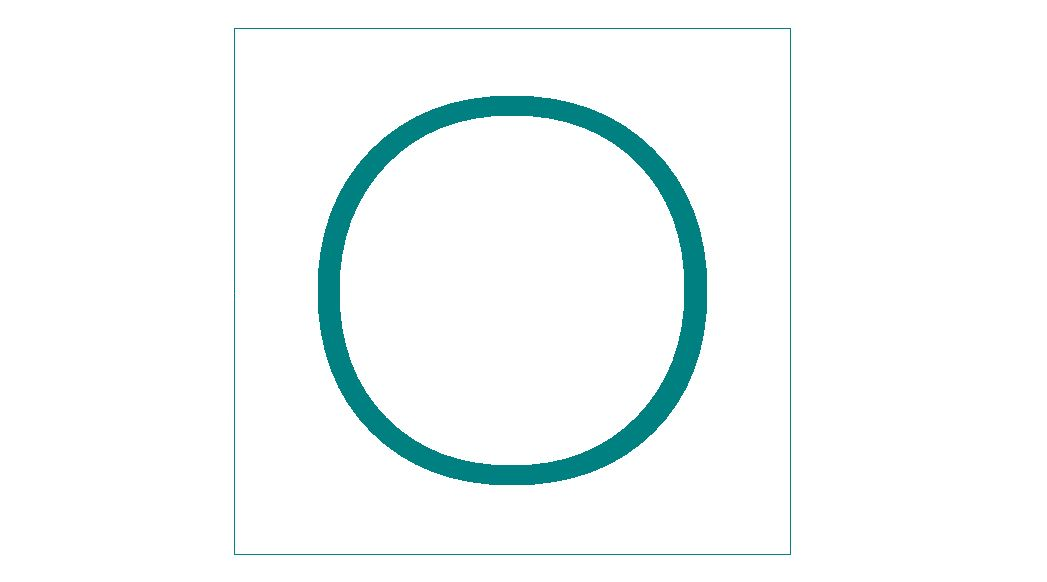
De circulariteit van een kenmerk geeft aan hoe dicht de omtrek van het onderdeel bij een perfecte cirkel moet liggen. Er wordt gebruik gemaakt van 2 concentrische cirkels op een vlak loodrecht op de as van het onderdeel om het geschikte tolerantiebereik in 2D te definiëren. Elk punt van de eindmetingen moet tussen de cirkels vallen.
Dit kenmerk wordt weergegeven als een cirkel in het eerste compartiment van het feature control frame.
Cylindriciteit
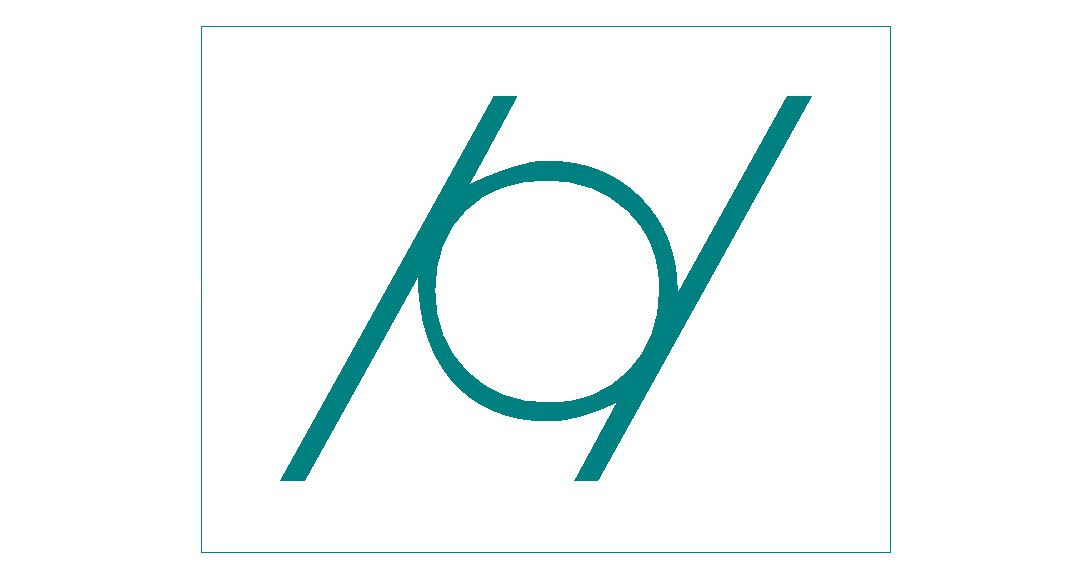
Cylindriciteit is in feite circulariteit in 3D, wat betekent dat het over de gehele lengte van het onderdeel loopt.
Deze eigenschap beschrijft ook andere cilindrische kenmerken, zoals de tapsheid, rechtheid en rondheid. Daarom is deze eigenschap ook duur om te inspecteren.
Profile Controls
We gebruiken profile controls om de 3D tolerantiezone rond de eigenschap te controleren. Deze functie helpt ons om tolerantiegrenzen te geven aan geavanceerde curven en vormen.
Een functie die goed is voor geavanceerde krommen moet natuurlijk ook goed werken met eenvoudigere krommen. Dit maakt profielcontroles uiterst veelzijdig. Dit is de reden waarom sommige ontwerpers aanbevelen om alle andere controles te laten vallen en alleen met profiel controles te werken.
Deze controles vormen een tolerantiegrens rond de geavanceerde kromme door deze aan beide zijden na te bootsen. Het voorkomt dan dat een punt op de feature curve buiten de tolerantiegrens komt. Profielcontroles zijn er in twee soorten.
Lijnprofiel
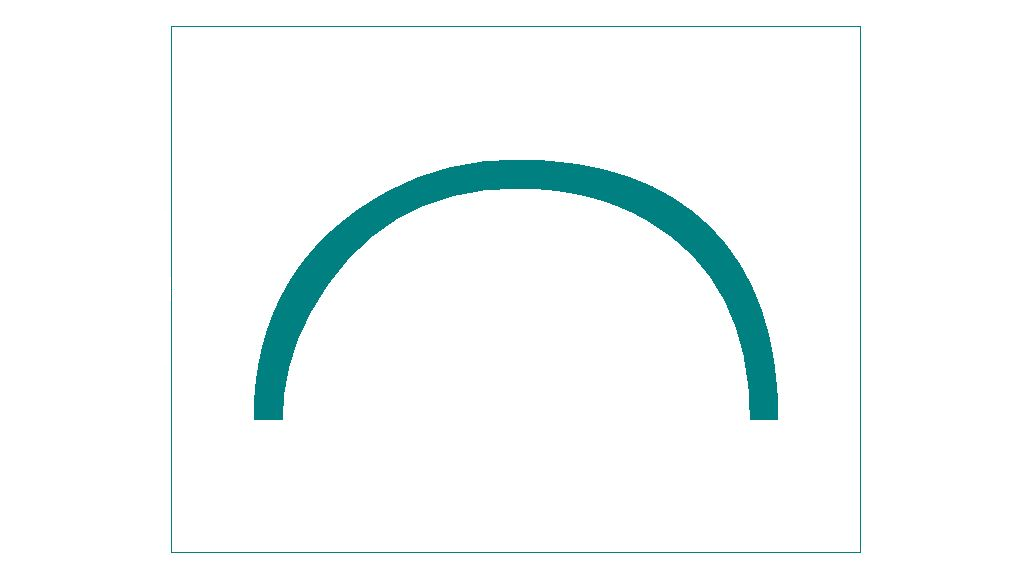
Lijnprofiel legt een tolerantiezone aan rond variërende 2D-doorsneden van het onderdeel. Hiermee worden afzonderlijke lijnelementen van een onderdeelelement gecontroleerd.
De lijnprofielcontrole traceert de ideale curve aan de tolerantiegrenzen aan beide zijden. Alle punten op de kromme van het onderdeel moeten binnen deze grenzen liggen.
Zuidprofiel
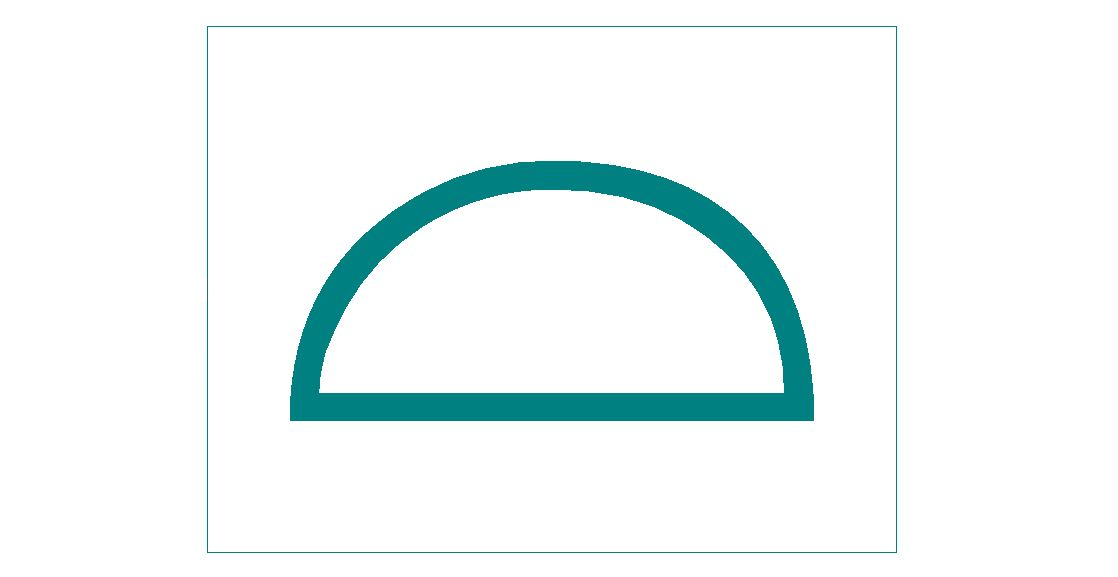
Zuidprofielbesturing is populairder vergeleken met lijnbesturing. In plaats van een tweedimensionale tolerantiezone, creëert de oppervlakteprofielbesturing een 3D-zone rond een oppervlak.
Alle punten op het tafeloppervlak moeten binnen de twee virtuele vlakken liggen.
Orientatiebesturingselementen
Orientatietolerantie regelt de oriëntatie van een element ten opzichte van een gedefinieerd nulpunt. Er zijn drie soorten oriëntatiecontroles in GD&T.
Angulariteit
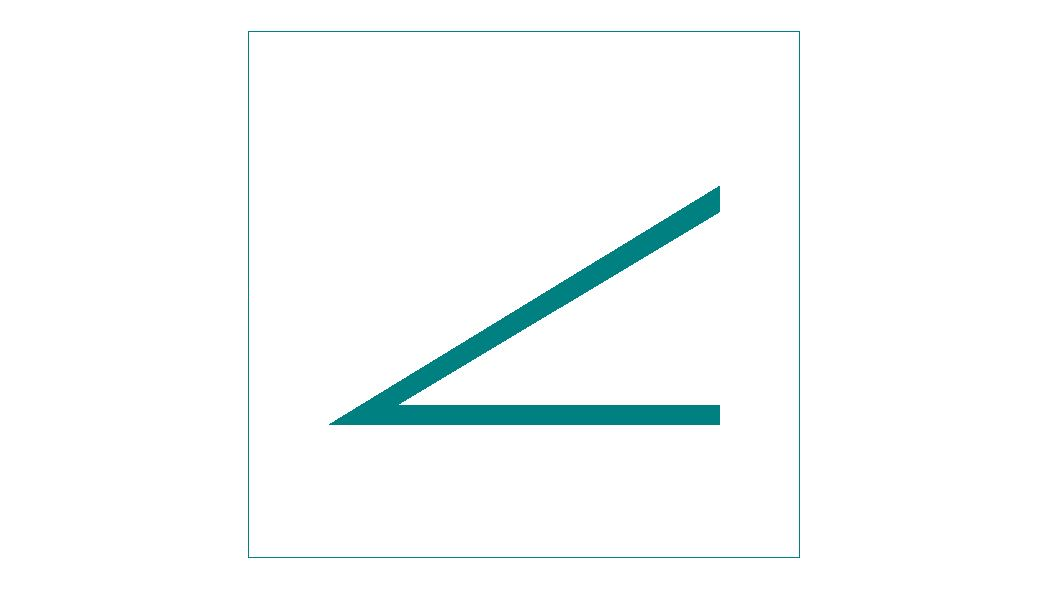
De angulariteitscontrole houdt de hoek van een element ten opzichte van het nulpunt in toom. We kunnen het gebruiken om een 2D lijn te controleren, maar het is populairder om oppervlakken (3D) onder controle te houden.
Dit soort strakke controle houdt de hoek en de vlakheid van het oppervlak onder controle en wordt aanbevolen voor productkenmerken die paren met andere onderdelen door het gehoekte oppervlak.
Het is belangrijk op te merken dat de hoekigheidseigenschap de hoek indirect controleert, en niet in wezen hetzelfde is als een hoektolerantie (b.v. +/- 2°). De vereiste hoek is eerder een resultaat van het voldoen aan de dimensionale eisen die door deze controle zijn vastgelegd.
Parallelliteit
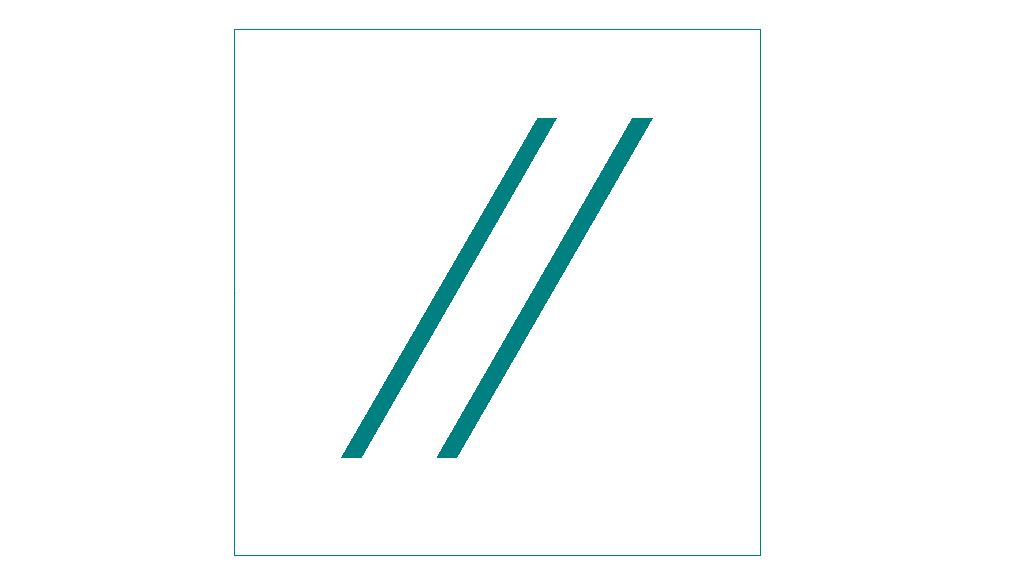
Parallelliteit is een verfijnde vorm van hoekigheid. Hier is het nulpunt het oppervlak dat we moeten nabootsen en wordt de hoek op 0° gesteld. Er zijn 2 soorten parallellisme: oppervlakteparallellisme en asparallellisme.
We kunnen een as of een oppervlak als referentie kiezen. Dit wordt ons nulpunt en we refereren het in het 3de blok van het feature control frame als het nulpunt voor de feature.
Gelijk aan hoekparallellisme, controleert het niet de eigenlijke hoek, maar beveiligt het door de eisen vast te leggen in de vorm van een tolerantie zone.
Perpendiculariteit
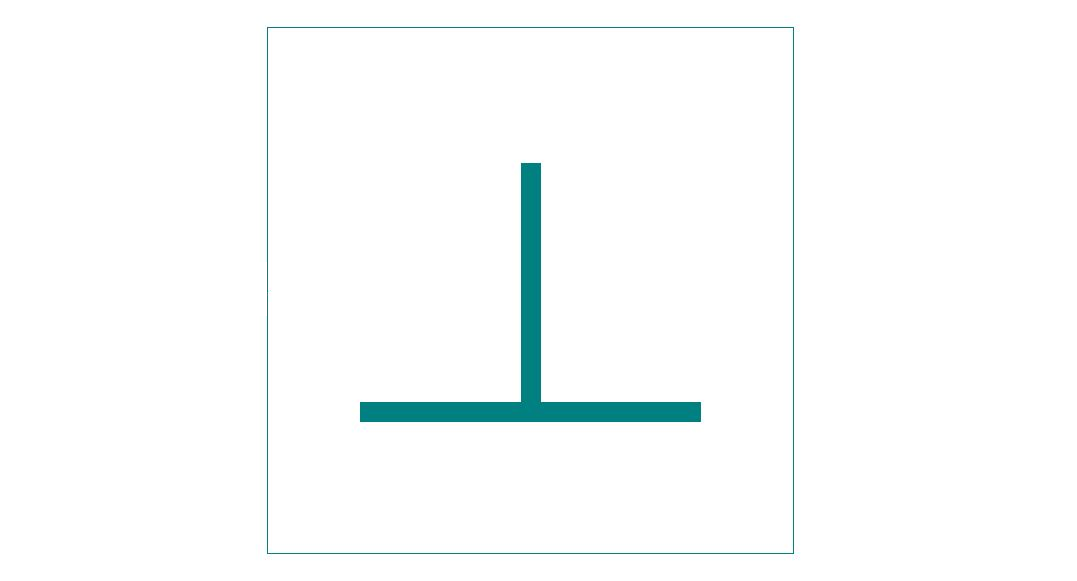
Perpendiculariteit is ook een specifieke vorm van angulariteit waarbij de hoek op 90° wordt gesteld. Het is een lastige controle omdat het twee heel verschillende soorten eisen kan betekenen.
Er is oppervlakte loodrechtheid ( Symbool:⟂), en dan is er as loodrechtheid (Symbolen: ⟂+⌀).
Loodrechtheid specificeert dat een oppervlak of lijn loodrecht op een nulpuntoppervlak of -lijn moet staan, net als hoekloodrechtheid. Twee virtuele vlakken/lijnen worden verondersteld rond het doeloppervlak voor controle.
Loodrechtheid van een as specificeert hoe loodrecht een as moet staan op het genoemde nulpunt. Dit wordt gedaan door het oprichten van een virtuele cilinder rond de doel-as op een oppervlak precies evenwijdig aan het nulpunt oppervlak.
Location Controls
De Location tolerance control wordt gebruikt voor een strakke controle op de positie van een kenmerk ten opzichte van een nulpunt. Er zijn vier hoofdtypen locatiecontroles.
Concentriciteit
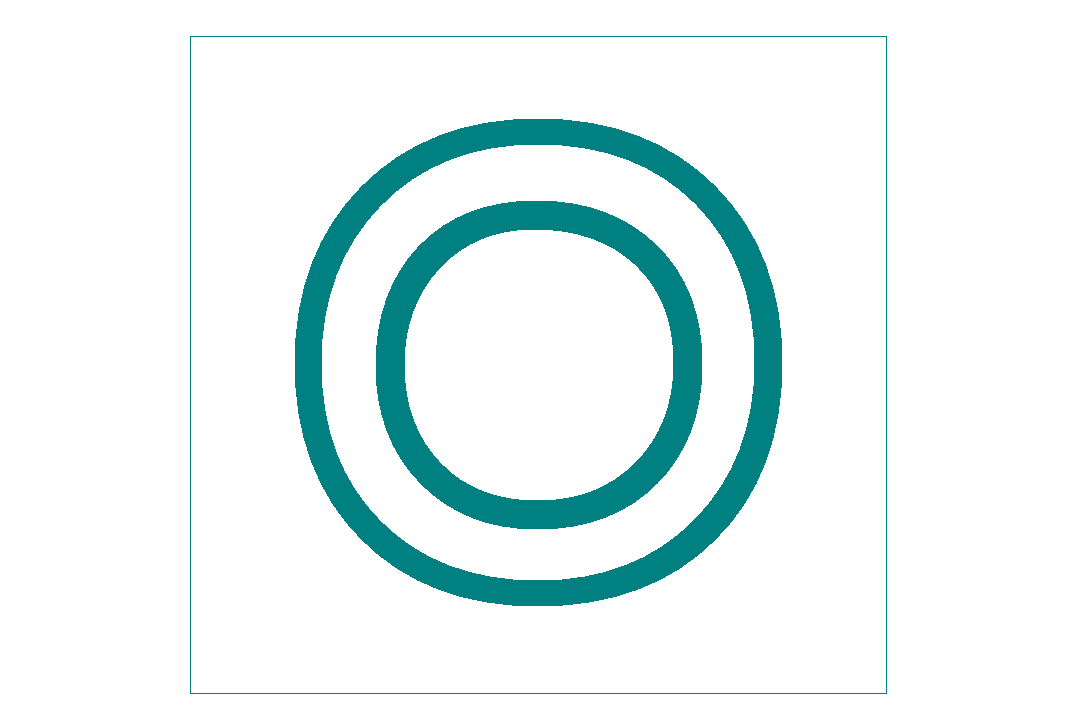
Concentriciteit, ook bekend als coaxialiteit (hoewel niet precies hetzelfde), controleert de concentriciteit van zowel cirkelvormige als cilindrische elementen.
Het fixeert de as van een onderdeel naar de as van een gerefereerd element (nulpuntas). De assen van beide onderdelen worden bepaald op de middenpunten van de onderdelen.
Deze controle kan leiden tot enige verwarring, omdat de assen worden afgeleid van metingen aan de buitenkant, in plaats van hun werkelijke plaatsing.
Coaxialiteit creëert een 3D-tolerantiezone op basis van oppervlaktemetingen waarin het onderdeel moet liggen.
Symmetrie
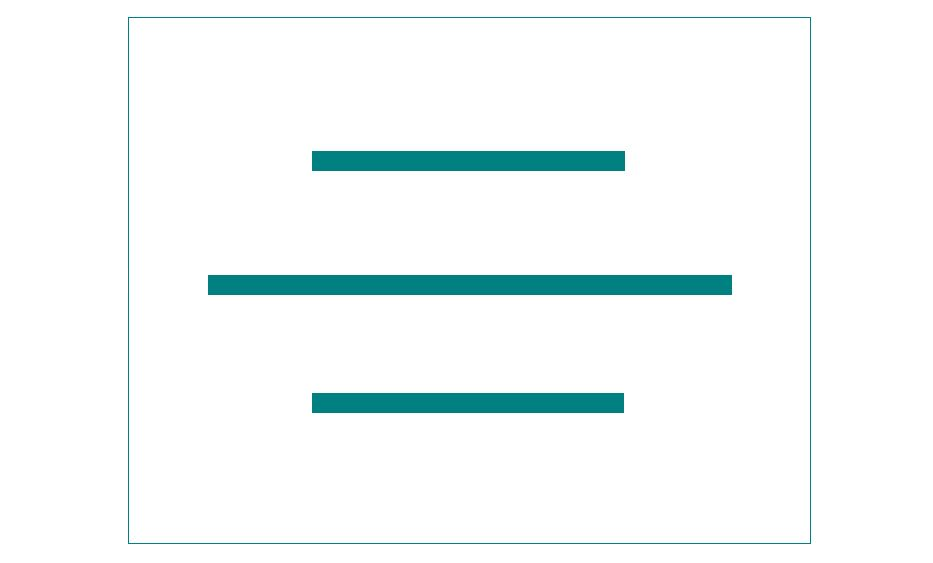
De symmetrie callout legt een centraal vlak vast waaromheen de twee onderdelen van het kenmerk op gelijke afstand worden geplaatst. Het middelpunt van de twee punten aan weerszijden moet binnen de tolerantiezone liggen die rond het centrale vlak is ingesteld.
De symmetrie-callout komt niet vaak voor. Het heeft zeer beperkte toepassingen en is ook moeilijk te inspecteren. We hebben een CMM nodig om de uiteindelijke symmetrie te inspecteren.
True position
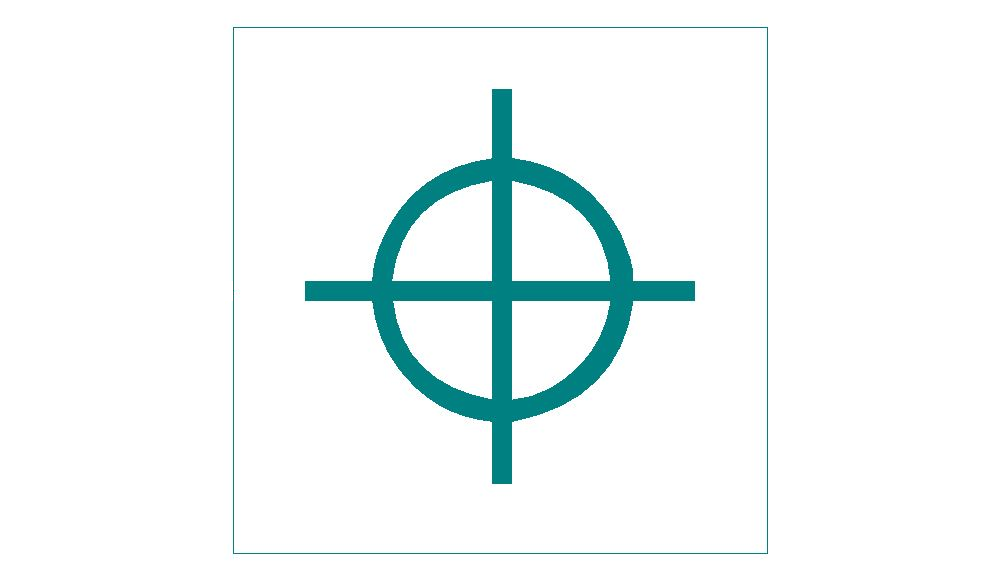
True position (in de volksmond bekend als positie) is een zeer nuttige callout en wordt veel gebruikt in GD&T.
Position definieert hoeveel de werkelijke positie van een element kan afwijken van de beoogde positie. De definitie omvat het nulpunt waarop de meting betrekking heeft.
Het bevat vaak een diameterteken (⌀) om aan te geven dat de tolerantiezone een cirkel is, in plaats van alleen de X- en Y-as (waarover we aan het begin van het artikel spraken als de reden waarom GD&T in de eerste plaats is gemaakt).
Hier is een geweldige video die laat zien hoe je de toleranties op een tekening kunt gebruiken, gebruikmakend van de ware positie:
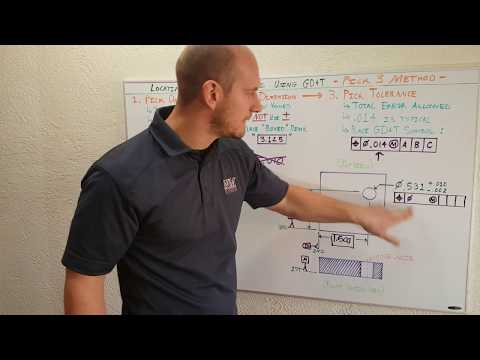
Hoe pas je GD&T Positietolerantie toe op een gat
Uitloopcontroles
We gebruiken de uitloopcontroles om de afwijking te meten van een onderdeel ten opzichte van de toegewezen positie ten opzichte van een vastgesteld nulpunt. Deze controle wordt gebruikt voor cirkelvormige elementen. In wezen wordt de afwijking gemeten door het element om het vaste nulpunt te draaien.
Er zijn twee soorten uitloopcontroles.
Circulaire uitloop

Circulaire uitloop werkt in twee dimensies om de vorm, locatie en oriëntatie van diverse productkenmerken te controleren. Voor deze 2D-callout moeten we een referentie-as toewijzen om deze kenmerken te controleren.
In GD&T-jargon is circulaire uitloop algemeen bekend als runout. Runout meet de afwijking in de oppervlakte-elementen door rotatie.
Dat wil zeggen dat de as, bijvoorbeeld, wordt geroteerd door zijn datum-as en het gekenmerkte element wordt gemeten voor tolerantie. In wezen beperkt het de trilling van een werkende as om een langere levensduur te verzekeren voor verbonden onderdelen zoals lagers.
Totale uitloop
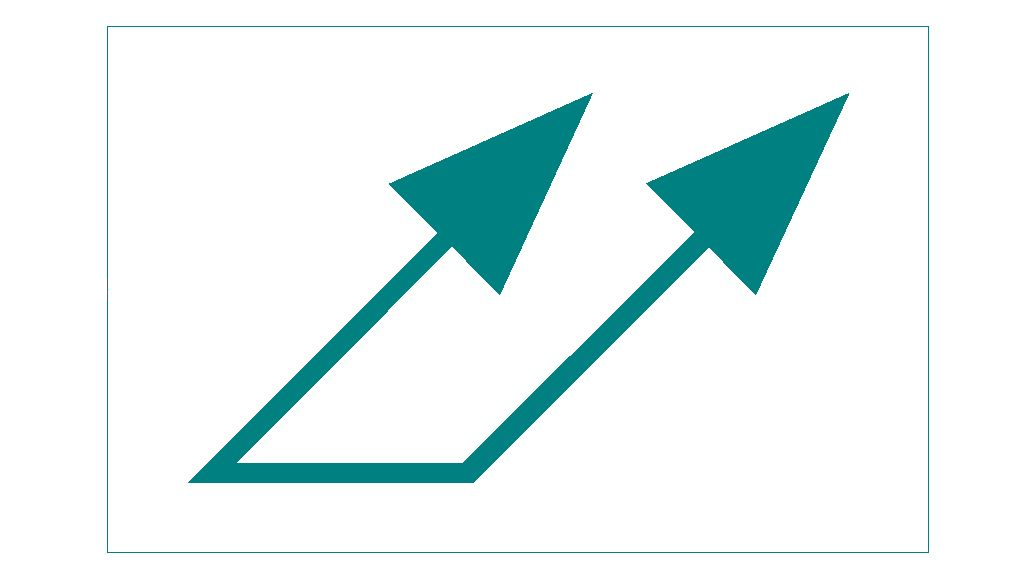
Totale uitloop is de 3D tegenhanger van cirkelvormige uitloop. Het controleert ook vorm, plaats en oriëntatie. Maar in plaats van het controleren van individuele doorsneden (zoals bij de circulaire uitloop), wordt het gehele oppervlak gecontroleerd. Dus, het gebruik van totale uitloop geeft ons een strengere controle op de kenmerken van de eigenschap.
Inspectie
In alle industrieën kan het falen van het fabricageproces om aan de ontwerpspecificaties te voldoen problematisch zijn. Terwijl in sommige gevallen het leven van klanten in gevaar kan zijn, kan in andere gevallen een productterugroeping leiden tot enorme geldelijke verliezen.
Zelfs als de resultaten niet zo slecht zijn, is de reputatie van een bedrijf sterk afhankelijk van de kwaliteit van zijn producten en diensten.
GD&T standaardiseert het inspectieproces door inspecteurs op hetzelfde platform in te brengen als de ontwerper. Dit elimineert een hoop obstakels. Maar GD&T is een omvangrijk onderwerp.
Zoals we hebben gezien, zijn er een aantal verschillende geometrische kenmerken, elk zeer verschillend van elkaar, die met GD&T kunnen worden gecontroleerd. Door deze ongelijkheid vereist de inspectie van elk kenmerk een specifieke methode, gereedschap en vaardigheid.
Sommige van deze kenmerken kunnen worden gemeten met het eenvoudigste gereedschap, terwijl andere onmogelijk te meten zijn zonder geavanceerde apparatuur zoals een coördinaten-meetmachine (CMM).
Inspecteurs hebben de kennis en vaardigheid nodig om verschillende meetinstrumenten te gebruiken, zoals meetklokken, micrometers, schuifmaten, vlakplaten en coördinatenmeetmachines om de nauwkeurigheid van onderdelen naar tevredenheid te inspecteren.