Inginerii folosesc software CAD pentru a proiecta toate piesele și componentele necesare pentru proiect. În domeniul digital, este ușor să atingi perfecțiunea. În viața reală, fabricația nu este niciodată 100% exactă.
Câteodată, abateri de câțiva milimetri de la dimensiunile de bază pot fi absolut bune. În același timp, două componente care se împerechează ar putea necesita o precizie extrem de mare.
Pentru a menține abaterea așteptată într-un interval predefinit, este posibil să se utilizeze toleranțe tehnice. Toleranțele dimensionale sunt foarte comune, dar nu dispun de modalități de comunicare a unor aspecte foarte importante ale fabricației. Aici intervine GD&T, sau toleranța de dimensionare geometrică &.
Este o formă de descriere a dimensiunilor și toleranțelor într-un mod cu totul nou. Folosind un limbaj comun de simboluri inginerești, ajută la identificarea cu ușurință a tuturor informațiilor necesare.
- Ce este GD&T?
- De ce să implementăm GD&T?
- Asamblare perfectă
- Sistem comun pentru a explica intenția de proiectare
- Economisește timp și bani
- Ce trebuie luat în considerare?
- Inteligibilitatea desenului
- Toleranțe strânse numai atunci când este necesar
- Caracteristici GD&T & Simboluri
- Dimensiuni nominale
- Cadrul de control al caracteristicilor
- Săgeata conducătoare
- Simbol caracteristic geometric
- Compartimentul toleranței caracteristicilor
- Datums
- Material Condition Modifiers
- Modificator condiție maximă de material
- Modificatorul condiției de cel mai mic material
- Indiferent de mărimea caracteristicii (RFS)
- Date și caracteristici de identificare
- Simboluri GD&T
- Controlul formei
- Dreptate
- Planeitate
- Circularitate
- Cilindricitate
- Controale de profil
- Profil liniar
- Profilul suprafeței
- Controale de orientare
- Angularity
- Paralelism
- Perpendicularitatea
- Controale de localizare
- Concentricitate
- Simetrie
- Poziția reală
- Cum se aplică toleranța de poziție GD&T la un orificiu
- Controale de rulare
- Circular runout
- Runningul total
- Inspecție
Ce este GD&T?
Este un sistem de simboluri și standarde folosite de ingineri pentru a furniza informații de fabricație echipei de producție.
Motivele pentru utilizarea Dimensionării și Toleranțelor Geometrice (GD&T) sunt:
- Se asigură că piesele care se potrivesc între ele se potrivesc bine
- Limbajul universal funcționează indiferent cu cine lucrați
- Toleranțele oferă o limită pentru cele mai nefavorabile condiții
- Define procesele de producție și inspecție
Stanley Parker este creditat ca fiind inginerul care a dezvoltat sistemul GD&T în 1938.
Până atunci, toate caracteristicile foloseau doar axele X-Y pentru a determina poziția unei găuri, de exemplu. A da o toleranță de poziție pe această scală înseamnă că poziția găurii circulare poate devia într-un model dreptunghiular de la locul prevăzut.
Cu toate acestea, am dori de fapt ca zona de toleranță să fie un cerc, deoarece aceasta permite o măsurare uniformă în toate unghiurile, în timp ce un dreptunghi este mai lung spre colțuri și mai scurt spre laturi.
Atunci când Parker și-a dat seama de acest lucru, a început să lucreze la noul concept care a fost adoptat ca standard de inginerie militară în anii ’50.
Astăzi, GD&T este o parte importantă a ingineriei, în special atunci când se creează piese care necesită servicii de prelucrare CNC. Standardul american care descrie caracteristicile este ASME Y14.5-2018, iar echivalentul european este ISO 1101-2017.
GD&T se concentrează exclusiv pe geometria produsului. Dimensiunile liniare, rugozitatea suprafeței, filetele etc. nu fac parte din acest standard.
De ce să implementăm GD&T?
Avem metode tradiționale de denotare a dimensiunilor și toleranțelor. Atunci de ce este nevoie de dimensionare geometrică și toleranță?
Dimensionarea geometrică și toleranța (GD&T) oferă câteva avantaje unice față de metodele obișnuite. Să vedem care sunt acestea.
Asamblare perfectă
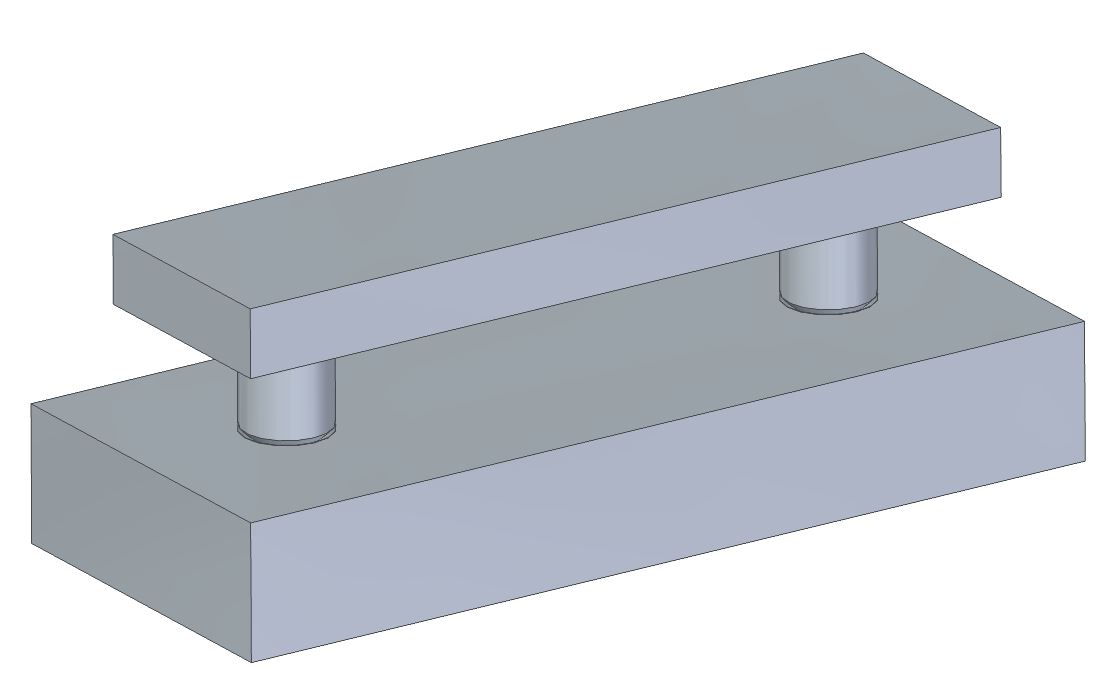
Cel mai important dezavantaj al utilizării cotelor și toleranțelor tradiționale este că acestea denotă informații individuale despre piese și caracteristici ale pieselor. Nu garantează cât de bine se vor potrivi și vor funcționa piesele noastre la nivelul ansamblului.
Acest lucru este important deoarece majoritatea pieselor nu sunt utile prin ele însele. Luați în considerare exemplul unei bielete. Prin ea însăși, nu ne oferă niciun beneficiu. Dar atunci când o conectăm la arborele cotit și la piston, devine puțin mai utilă, deoarece transformă mișcarea liniară a pistonului în mișcare de rotație a arborelui cotit.
Când acest ansamblu devine parte a unui ansamblu mai mare, cum ar fi un motor diesel, poate ajunge să fie o parte a unui generator care ne oferă multe utilizări.
De aceea, este crucial ca piesele noastre să se potrivească bine între ele. Acesta este motivul pentru care avem nevoie de GD&T. Utilizându-l, putem fi 100% siguri că piesele noastre se vor potrivi între ele și vor funcționa exact așa cum este necesar.
Sistem comun pentru a explica intenția de proiectare
GD&T oferă, de asemenea, proiectantului o platformă pentru a transmite intenția sa de proiectare tuturor departamentelor relevante. Printre acestea se numără:
- Fabricarea
- Inspecția
- Futurii proiectanți din departamentul de proiectare care vor prelua munca în cazul în care echipa de proiectare inițială nu este disponibilă
Definițiile, vocabularul și regulile sunt simple și universal ușor de înțeles. Acest lucru face ca simbolurile să fie ușor de tradus pentru fiecare inginer și reprezintă o modalitate excelentă de a transmite intenția proiectantului.
Economisește timp și bani
Acesta este cel mai important beneficiu al utilizării GD&T. Utilizarea acestui sistem reduce risipa, deoarece reduce numărul de cicluri de proiectare-fabricare-testare-ajustare.
Acest lucru se datorează faptului că piesele fabricate se potrivesc bine de la prima încercare și, în consecință, numărul de rebuturi va fi scăzut. Utilizarea unui limbaj comun reduce, de asemenea, efortul necesar pentru inspecție.
Obțineți o ofertă de fabricație în câteva secunde
-
Ofertă în câteva secunde
-
Timpuri de execuție scurte
-
Livrare prin fractură
Obțineți o ofertă
Ce trebuie luat în considerare?
Dimensionarea și toleranța geometrică este un sistem mai puternic în comparație cu toleranțele tradiționale. Dar funcționează numai dacă toate departamentele (proiectare, inginerie, producție) sunt bine versate în citirea și interpretarea informațiilor.
De aceea, în timp ce creați desene de inginerie și tolerați diverse caracteristici ale pieselor, este important să respectați liniile directoare/convenții recomandate, în beneficiul tuturor celor care vor interacționa cu desenul în orice etapă a dezvoltării produsului.
Observarea acestora asigură standardizarea desenului și faptul că toată lumea este pe aceeași lungime de undă atunci când vine vorba de specificațiile desenului. Unele dintre aceste bune practici sunt următoarele.
Inteligibilitatea desenului
Aceasta este, fără îndoială, cea mai importantă calitate a unui desen. Inteligibilitatea se referă la claritatea cu care sunt desenate caracteristicile piesei și cu care sunt prezentate toleranțele în desen. Unele modalități de îmbunătățire a inteligibilității unui desen sunt:
- Desenați profile adevărate pentru toate caracteristicile piesei.
- Etichetați dimensiunile și toleranțele în afara desenului (nu în partea de sus). Utilizați eficient spațiul alb.
- Direcția de citire trebuie să fie constantă. Un cititor trebuie să fie capabil să citească toate dimensiunile în timp ce ține desenul în poziție verticală.
- Spatizați dimensiunile caracteristicilor paralele ale piesei.
- Explicați pe scurt piesa și funcția sa.
- Specificați unghiurile numai atunci când acestea nu sunt unghiuri drepte (90°).
Toleranțe strânse numai atunci când este necesar
Dacă nu o cere o potrivire/funcție a piesei, toleranțele trebuie menținute cât mai laxe posibil. Acest lucru reduce costurile de fabricație și timpul de execuție. Se recomandă să se lase alegerea metodei de fabricație în seama mecanizatorilor.
Proiectantul trebuie să menționeze, de asemenea, toleranța generală pentru un desen. Aceasta acționează ca toleranță standard pentru toate caracteristicile piesei. Pentru caracteristicile piesei cu o limită de toleranță diferită, proiectantul trebuie să le menționeze în pozițiile corespunzătoare.
Aceste limite de toleranță specifice vor prevala asupra toleranțelor generale. Atunci când specificați limite de toleranță speciale, preferați caracteristicile funcționale în detrimentul altor caracteristici.
Caracteristici GD&T & Simboluri
Limbajul GD&T este capabil să definească aproape orice calități care sunt necesare pentru a asigura un ansamblu perfect.
Sistemul utilizează un număr de simboluri în acest scop. Pentru a utiliza corect aceste simboluri inginerești pe desene, trebuie mai întâi să ne familiarizăm cu câteva elemente de bază ale acestui sistem.
Potem începe cu diversele definiții, terminologii și reguli înainte de a ajunge la simbolurile GD&T.
Dimensiuni nominale
O dimensiune nominală este dimensiunea caracteristică a profilului real. Este dimensiunea exactă pe care am dori să o obținem în mod ideal. Particularitățile caracteristicilor, cum ar fi dimensiunea, orientarea, locația față de un punct de referință, au o dimensiune nominală pe care mecanizatorii o vizează.
Pe un desen, acestea sunt reprezentate în interiorul unei cutii. Poate fi afișată ca un număr sau dintr-un standard popular, cum ar fi ASME.
Cadrul de control al caracteristicilor
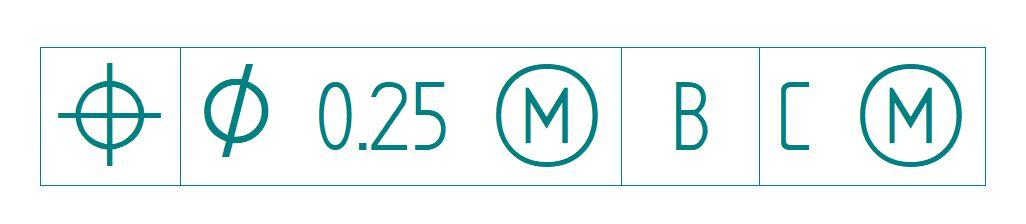
Acest cadru conține informații despre specificul piesei. Acesta conține diverse compartimente în care fiecare compartiment definește un atribut specific al caracteristicii piesei. Dintr-o singură privire, cadrul de control al caracteristicilor transmite informațiile necesare pentru prelucrare și inspecție.
Cadrul de control al caracteristicilor poate fi împărțit în 4 părți principale, după cum urmează.
Săgeata conducătoare
Această săgeată marchează caracteristica piesei care face obiectul controlului. Dacă aceasta duce la o suprafață, suprafața este sub control geometric. Dacă ea marchează o dimensiune diametrală, atunci GD&T controlează axa. Este posibil ca această săgeată să nu fie prezentă în unele cazuri.
Simbol caracteristic geometric
Primul compartiment (începând din stânga) conține simbolul caracteristic geometric. Acesta este locul unde se specifică caracteristica geometrică. În total, există 14 tipuri de toleranțe geometrice în funcție de numărul de simboluri și 15 atunci când sunt clasificate.
Diferitele tipuri de caracteristici geometrice sunt controlul formei, controlul profilului, controlul locației, controlul orientării etc. Vom aprofunda mai târziu fiecare categorie.
Compartimentul toleranței caracteristicilor
Cel de-al 2-lea bloc conține maximum 3 (uneori 2 sau 1) simboluri diferite.
Primul simbol arată tipul de zonă de toleranță. Un simbol de diametru (⌀) semnifică o zonă diametrală (zonă de toleranță cilindrică). Pentru a specifica o zonă sferică, simbolul este litera „S” urmată de simbolul diametrului (⌀). În absența unui simbol, se presupune o zonă de lățime totală.
Cel de-al doilea simbol din cel de-al doilea bloc indică valoarea zonei de toleranță în mm. Această valoare trebuie să fie întotdeauna prezentă în al 2-lea bloc.
Cel de-al treilea simbol din acest bloc este modificatorul pentru toleranță. Acest modificator de material este prezent numai atunci când caracteristica are o dimensiune, de exemplu, o gaură. Exemple de modificatori de material sunt MMC (Maximum material condition) și LMC (Least material condition). Mai multe informații despre diferiții modificatori disponibili vor fi discutate în continuare în articol.
Datums
Cel de-al treilea bloc oferă informații despre datum(uri) cu un minim de 1 și un maxim de 3 date. În cazul în care există 3 date, acestea sunt denumite date primare, secundare și terțiare, fiecare dintre ele fiind prezentată închisă într-o casetă diferită (imaginea de mai sus are 2, de exemplu). Acest bloc poate conține, de asemenea, un modificator de material.
Toate informațiile de mai sus ne ajută să înțelegem cum se citește un cadru de control al unei entități. Pentru a înțelege mai bine modul în care toleranța poate fi ajustată cu ajutorul modificatorilor de stare a materialului, trebuie să ne familiarizăm cu diferitele opțiuni.
Material Condition Modifiers
Modificatorii de stare a materialului transmit intenția atunci când toleranța se aplică unei caracteristici la o anumită dimensiune a acesteia. Ori de câte ori acordăm toleranțe oricărei caracteristici, se stabilesc două condiții de material
- Condiția maximă a materialului
- Condiția minimă a materialului
Considerăm un arbore cu diametrul de 100 mm. La fabricație, dacă îi acordăm o toleranță de ±0,2 mm, atunci la 100,2 mm, arborele va conține cantitatea maximă de material. Aceasta este ceea ce înțelegem prin starea maximă de material.
Pe de altă parte, același arbore, atunci când este fabricat cu un diametru de 99,8 mm, va conține cea mai mică cantitate de material. Aceste limite se numesc condiții de material.
Toleranțele geometrice pot fi aplicate unei caracteristici în 3 moduri diferite. Acestea sunt următoarele:
- Condiție maximă de material
- Condiție minimă de material
- Indiferent de dimensiunea elementului
Modificator condiție maximă de material
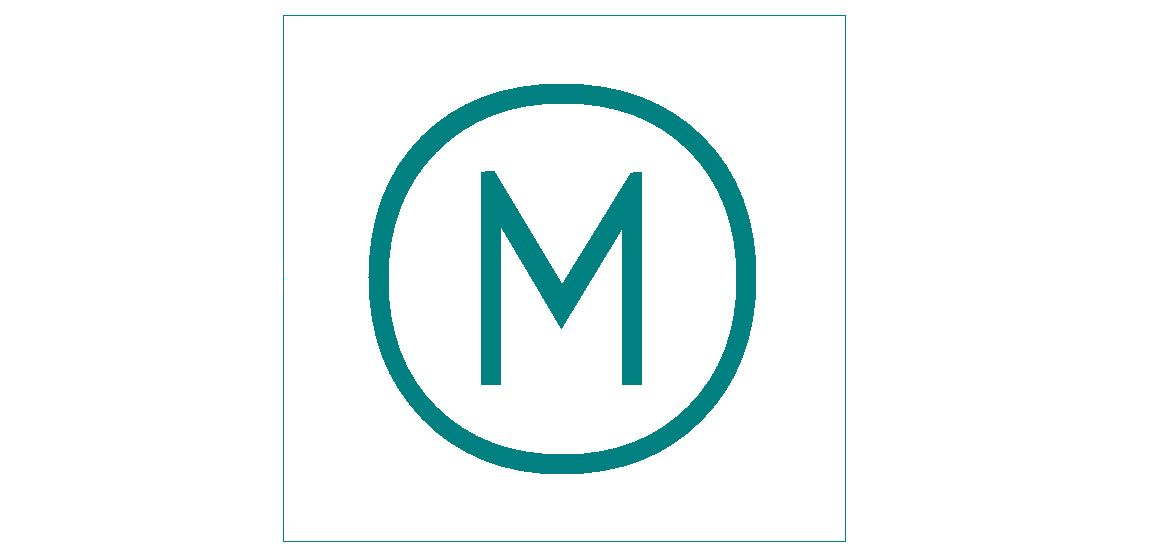
Reprezentăm această condiție printr-un „M” încercuit după valoarea toleranței în compartimentul de control al elementului. Caracteristica conține materialul maxim la această dimensiune a caracteristicii.
Pentru FOS (Feature Of Size) externe, cum ar fi diametrul unui arbore, MMC reprezintă cea mai mare dimensiune. Pentru FOS interne, cum ar fi diametrul unei găuri, MMC reprezintă cea mai mică dimensiune posibilă în limitele de toleranță declarate, deoarece o gaură mai mică înseamnă că va rămâne mai mult material.
Când trebuie să aplicăm o toleranță geometrică la condiția de material maximă, menționăm această condiție în cadrul de control al caracteristicii.
Modificatorul condiției de cel mai mic material
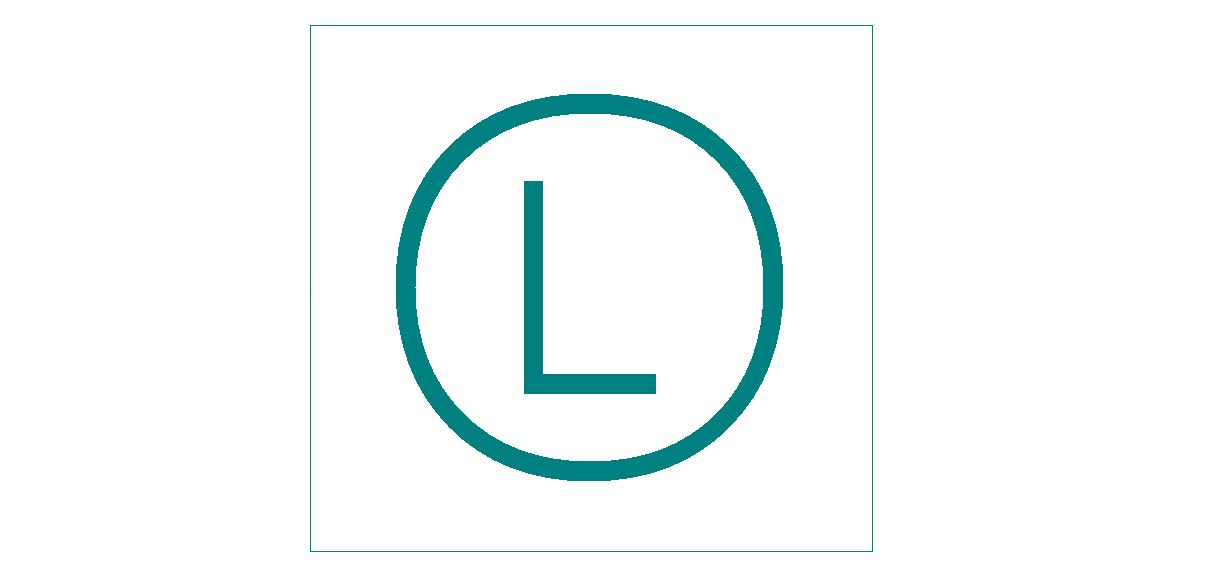
LMC reprezintă condiția în care materialul conține cea mai mică cantitate de material.
Pentru FOS extern, aceasta va fi cea mai mică dimensiune posibilă în limitele declarate. Iar pentru FOS intern, va fi cea mai mare dimensiune posibilă.
Reprezentăm acest modificator cu litera „L” într-un cerc. Această caracteristică elimină materialul excesiv și, prin urmare, greutatea. Pentru a aplica toleranțe geometrice la această condiție, folosim simbolul său în cadrul de control al caracteristicii.
Indiferent de mărimea caracteristicii (RFS)
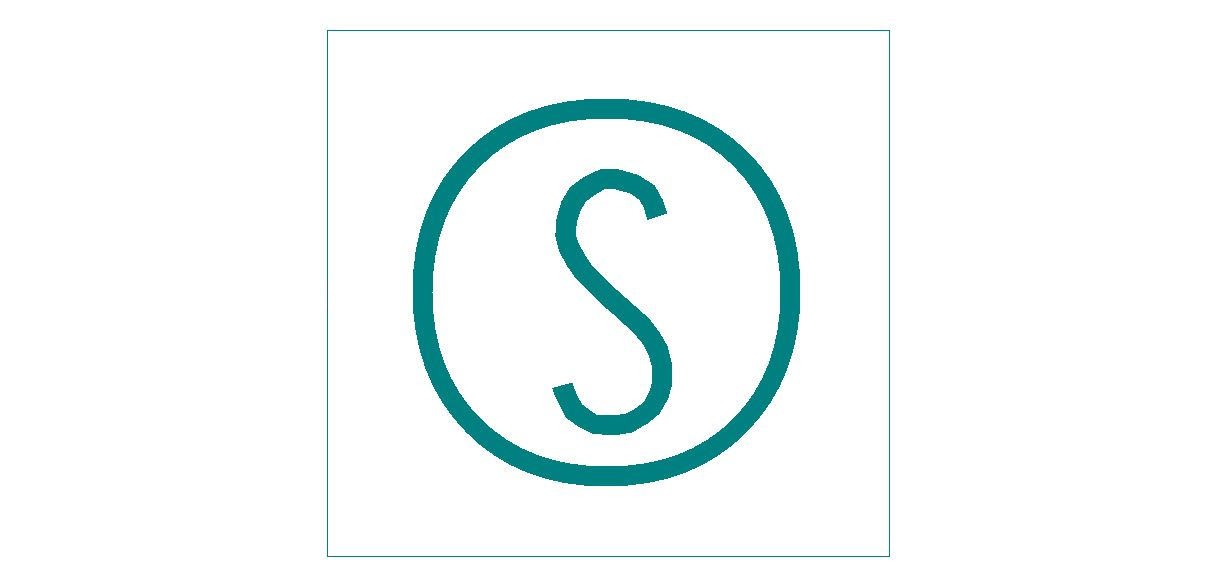
Când toleranțele geometrice date sunt aplicate la orice increment de mărime al FOS, indicăm acest lucru prin RFS. Simbolul pentru RFS era litera „S” închisă într-un cerc, dar nu mai este necesar, deoarece RFS este considerată acum condiția implicită și nu mai are nevoie de un simbol.
Date și caracteristici de identificare
Datele sunt puncte de referință pentru măsurarea toleranțelor dimensionale. Poate fi un punct, o linie sau un plan. Cu ajutorul unui punct de referință, stabilim cadrele de referință ale punctului de referință (DRF). DRF este practic un sistem de coordonate 3D care ne ajută să definim pozițiile tuturor celorlalte caracteristici în raport cu DRF.
Există 6 grade de libertate (3 de translație și 3 de rotație) pe care trebuie să le controlăm pentru a fabrica și inspecta eficient piesele. Folosim DRF pentru a stabili aceste grade de libertate.
Caracteristicile de date sunt caracteristicile reale ale piesei, cum ar fi găurile și fantele. Ele pot prezenta variații față de pozițiile dorite.
Printre toate caracteristicile de referință, acordăm cea mai mare preferință celor care se potrivesc cu alte piese din ansamblu. Putem menționa mai mult de un datum în cadrul nostru de control al caracteristicilor. Conform secvenței DRF-urilor din cadrul de control al caracteristicilor, piesele sunt împerecheate cu DRF-urile în ordinea descrescătoare a importanței.
Simboluri GD&T
Sunt disponibile până la 14 simboluri GD și T pentru a reprezenta diferite caracteristici geometrice ale caracteristicilor. Aceste simboluri ne ajută să specificăm aceste caracteristici ca cerințe pentru produsul final.
Punem aceste simboluri în primul compartiment al cadrului de control al caracteristicilor. Vom examina aceste tipuri de control al toleranțelor.
Controlul formei
După cum sugerează și numele, controlul formei se referă la forma sau forma finală a elementului. Definim controlul formei pentru a limita abaterea toleranței geometrice de la forma sa ideală. Unele caracteristici populare de control al formei sunt următoarele.
Dreptate
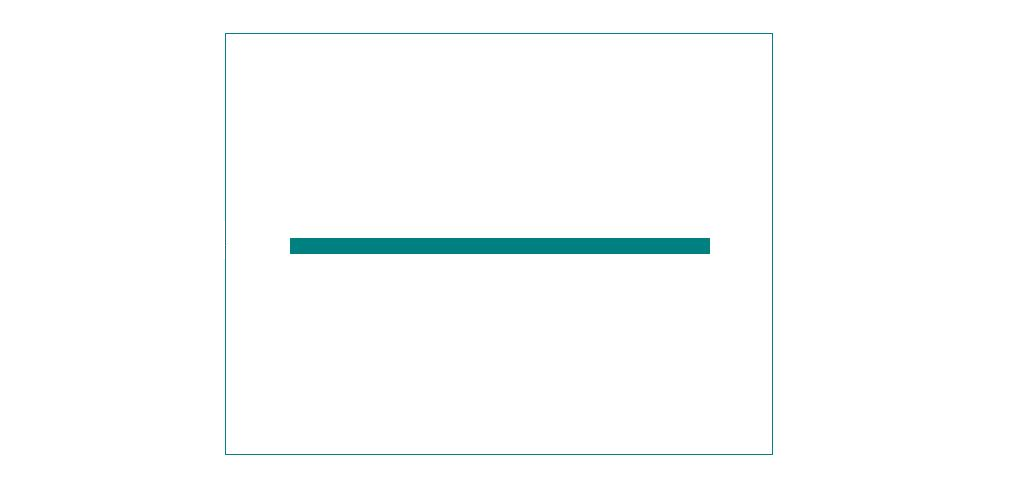
Pentru a indica caracteristica de rectitudine a unei entități (cum ar fi o axă sau o suprafață), folosim simbolul acesteia (o linie dreaptă orizontală) în primul compartiment.
Dreptatea suprafeței se poate aplica suprafețelor plane, cum ar fi o latură a unui bloc, sau suprafețelor curbe, cum ar fi o latură a unui cilindru, de-a lungul direcției axei. Ea definește variația admisibilă a unei linii (2 dimensiuni) pe suprafață în cadrul unei toleranțe specificate.
Dreptatea axială se aplică de obicei la axa unui arbore sau a unei găuri, de exemplu. Gabaritul go/no go este instrumentul de inspecție utilizat în procesul de verificare a conformității piesei cu cerințele.
Planeitate
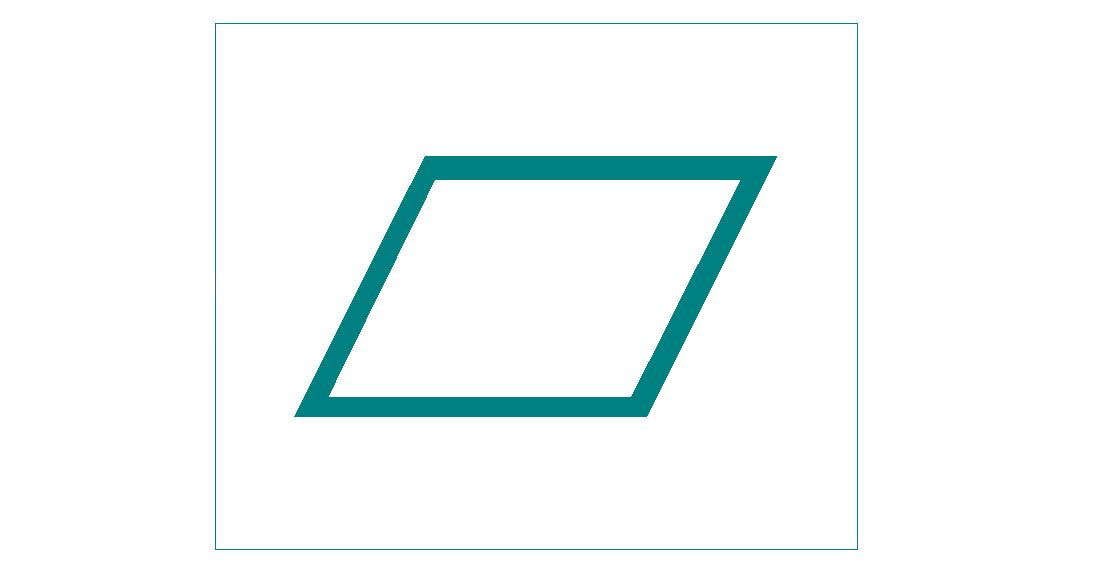
Utilizăm această caracteristică pentru caracteristici precum fața unei piese. Simbolul pentru planeitate este un paralelogram înclinat spre dreapta. Diferența dintre punctul cel mai înalt și cel mai jos al unei suprafețe plane este planeitatea acesteia.
Simbolul de planeitate nu necesită date de referință, deoarece arată doar un interval de toleranță în interiorul căruia trebuie să se încadreze întreaga suprafață a unei piese în 3 dimensiuni.
Pentru verificarea rezultatelor se utilizează un indicator de înălțime. Acesta atinge diferite zone ale suprafeței pentru a determina dacă toate punctele se află în interiorul zonei de toleranță.
Circularitate
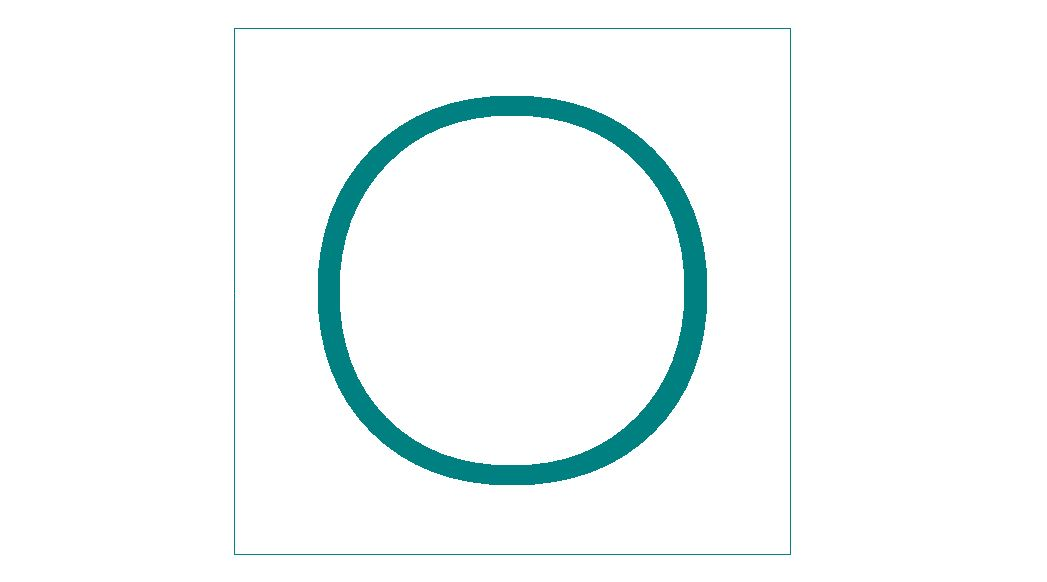
Circularitatea unei caracteristici arată cât de aproape trebuie să fie circumferința piesei de un cerc perfect. Se utilizează 2 cercuri concentrice pe un plan perpendicular pe axa piesei pentru a defini intervalul de toleranță adecvat în 2D. Fiecare punct al măsurătorilor finale trebuie să se încadreze între aceste cercuri.
Această caracteristică este afișată sub forma unui cerc în primul compartiment al cadrului de control al caracteristicii.
Cilindricitate
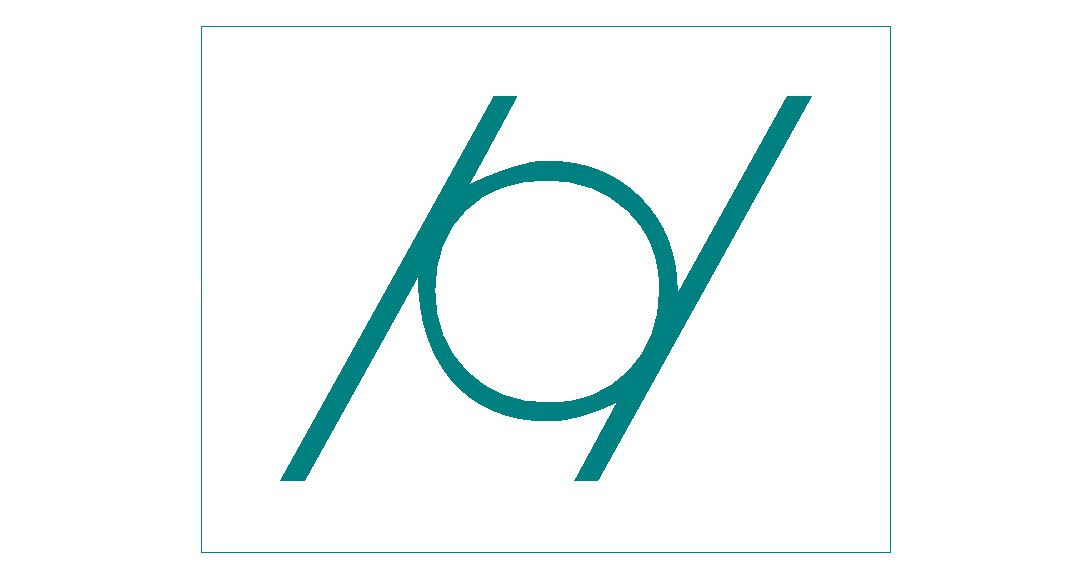
Cilindricitatea este practic circularitatea în 3D, ceea ce înseamnă că se desfășoară pe toată lungimea piesei.
Această caracteristică descrie și alte caracteristici cilindrice, cum ar fi conicitatea, rectitudinea și rotunjimea acesteia. Acesta este motivul pentru care această caracteristică este, de asemenea, costisitoare de inspectat.
Controale de profil
Utilizăm controale de profil pentru a controla zona de toleranță 3D din jurul caracteristicii. Această caracteristică ne ajută să dăm limite de toleranță la curbe și forme avansate.
O caracteristică care este bună pentru curbe avansate trebuie, în mod natural, să funcționeze bine și cu curbe mai simple. Acest lucru face ca comenzile de profil să fie extrem de versatile. Acesta este motivul pentru care unii proiectanți recomandă să se renunțe la toate celelalte controale și să se lucreze numai cu controale de profil.
Aceste controale formează o limită de toleranță în jurul curbei avansate, imitând-o pe ambele părți. Apoi împiedică orice punct de pe curba caracteristică să iasă în afara limitei de toleranță. Controalele de profil sunt de două tipuri.
Profil liniar
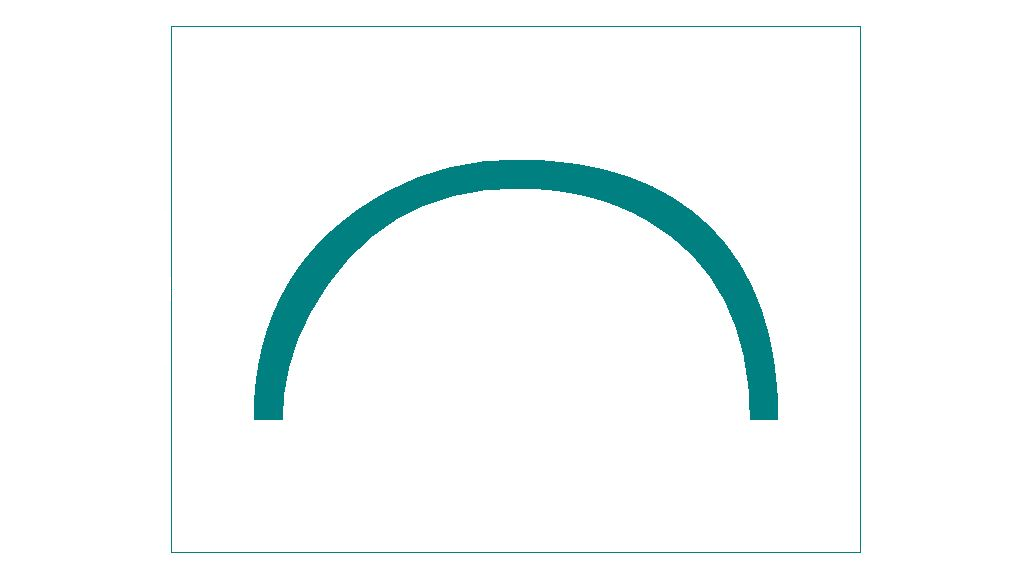
Profil liniar stabilește o zonă de toleranță în jurul unor secțiuni transversale 2D variabile ale piesei. Acesta controlează elementele de linie individuale ale unei caracteristici a piesei.
Controlul profilului de linie trasează curba ideală la limitele de toleranță pe ambele părți. Toate punctele de pe curba piesei trebuie să se încadreze în aceste limite.
Profilul suprafeței
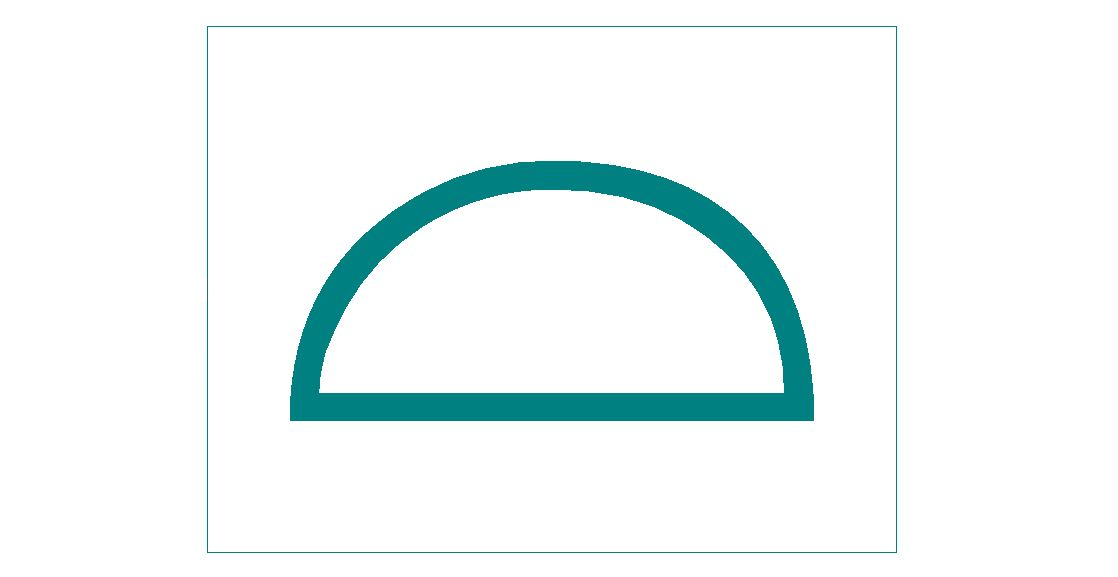
Controlul profilului suprafeței este mai popular în comparație cu controlul liniei. În loc de o zonă de toleranță bidimensională, controlul profilului de suprafață creează o zonă 3D în jurul unei suprafețe.
Toate punctele de pe suprafața mesei trebuie să se afle în interiorul celor două planuri virtuale.
Controale de orientare
Toleranța de orientare controlează orientarea unei entități în raport cu un punct de referință definit. Există trei tipuri de controale de orientare în GD&T.
Angularity
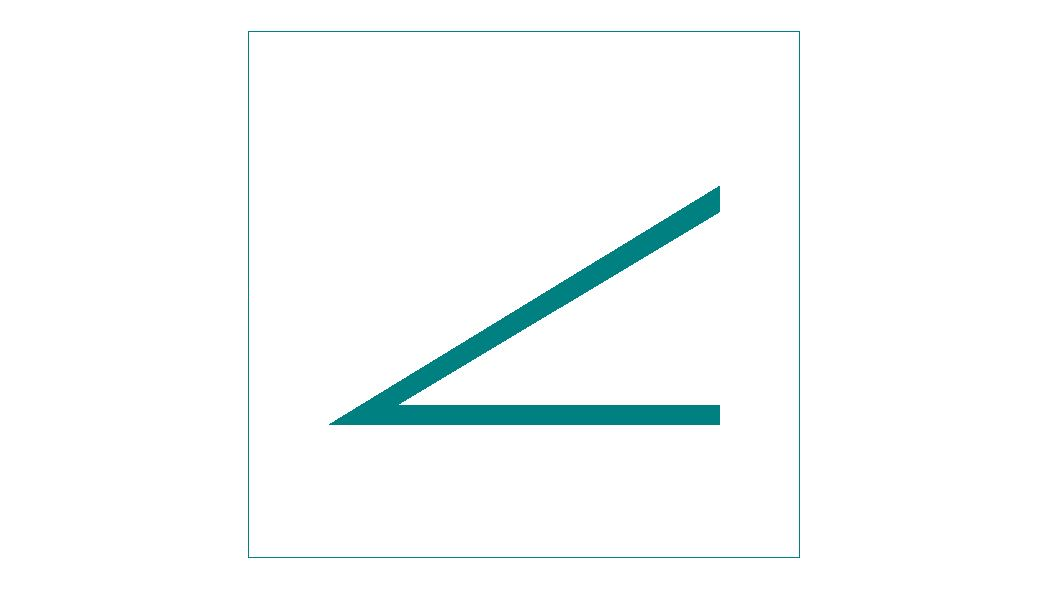
Controlul de angularitate menține sub control unghiul unei entități în raport cu data de referință. Îl putem folosi pentru a controla o linie 2D, dar este mai popular la menținerea sub control a suprafețelor (3D).
Acest tip de control strâns menține sub control unghiul și planeitatea suprafeței și este recomandat pentru caracteristicile pieselor care se împerechează cu alte piese prin intermediul suprafeței unghiulare.
Este important de reținut că funcția de angularitate controlează unghiul în mod indirect, nefiind în esență același lucru cu o toleranță unghiulară (de exemplu, +/- 2°). Mai degrabă, unghiul necesar este un rezultat al respectării cerințelor dimensionale stabilite de acest control.
Paralelism
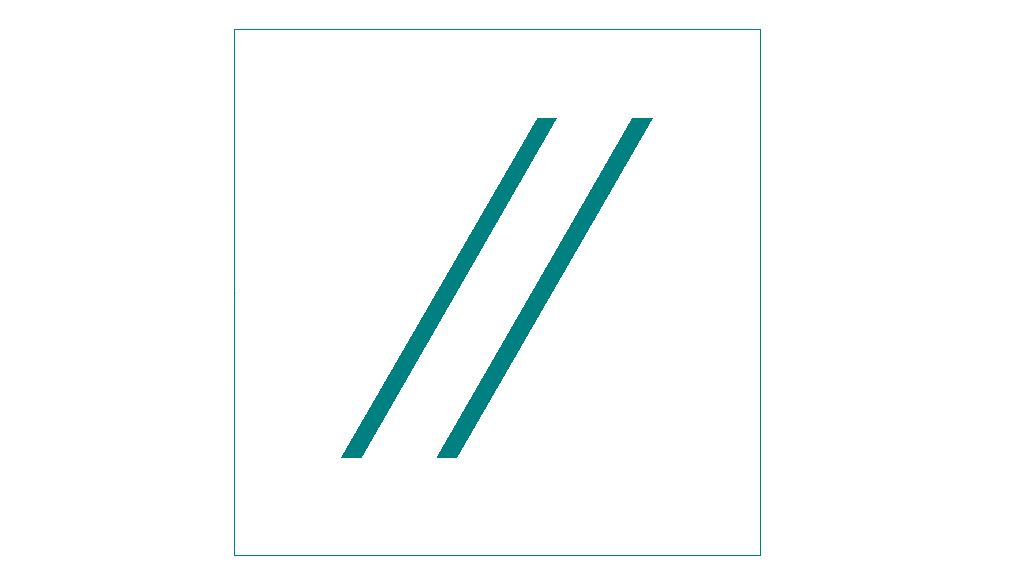
Paralelismul este o formă rafinată de angularitate. Aici, punctul de referință este suprafața pe care trebuie să o imităm, iar unghiul este setat la 0°. Există 2 tipuri de paralelism: paralelismul de suprafață și paralelismul de axă.
Putem alege o axă sau o suprafață ca referință. Aceasta devine referința noastră și o referim în cel de-al 3-lea bloc al cadrului de control al caracteristicii ca referință pentru caracteristica.
În mod similar cu unghiularitatea, nu controlează unghiul real, ci mai degrabă îl securizează prin stabilirea cerințelor sub forma unei zone de toleranță.
Perpendicularitatea
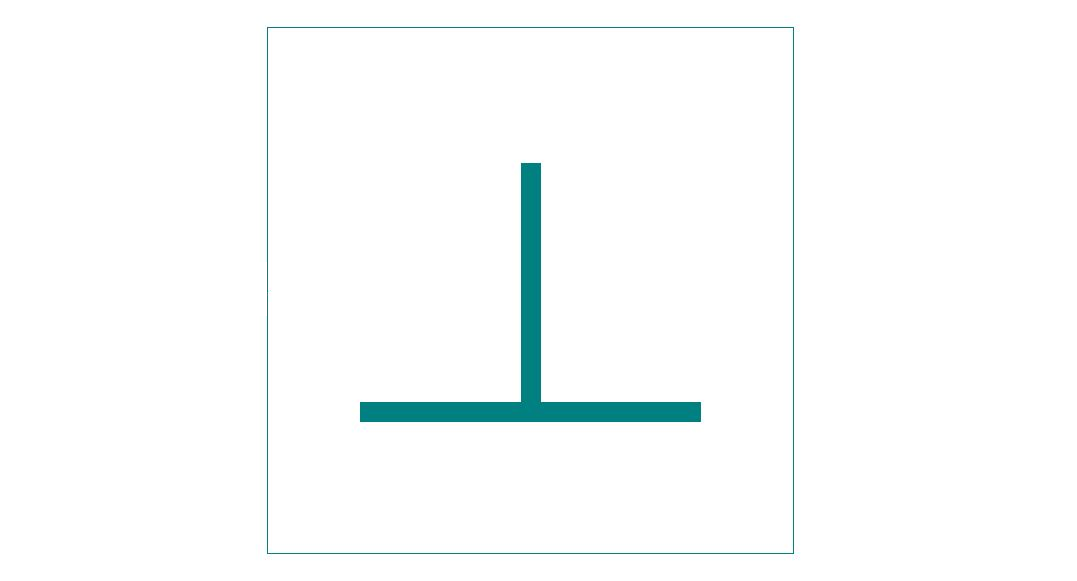
Perpendicularitatea este, de asemenea, o formă specifică de unghiularitate în care unghiul este stabilit la 90°. Este un control complicat, deoarece poate însemna două tipuri de cerințe foarte diferite.
Există perpendicularitatea de suprafață ( Simbol:⟂), iar apoi există perpendicularitatea de axă (Simboluri: ⟂+⌀).
Perpendicularitatea suprafeței specifică faptul că o suprafață sau o linie trebuie să fie perpendiculară pe o suprafață sau o linie de referință, la fel ca angularitatea. Se presupun două planuri/linii virtuale în jurul suprafeței țintă pentru control.
Perpendicularitatea axei specifică cât de perpendiculară trebuie să fie o axă față de punctul de referință menționat. Acest lucru se realizează prin ridicarea unui cilindru virtual în jurul axei țintă pe o suprafață exact paralelă cu suprafața de referință.
Controale de localizare
Controlul de toleranță de localizare este utilizat pentru un control strâns al poziției unei entități în raport cu o referință. Există patru tipuri principale de controale de locație.
Concentricitate
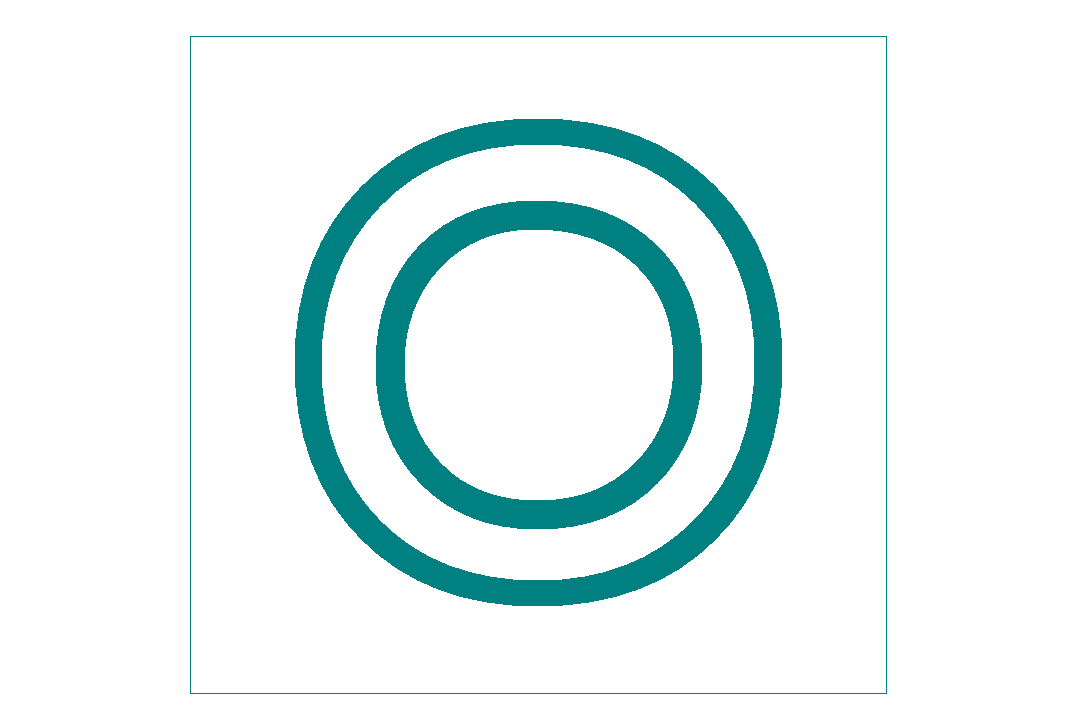
Controlul de concentricitate, cunoscut și sub numele de coaxialitate (chiar dacă nu este exact același lucru), menține concentricitatea elementelor circulare, precum și a celor cilindrice.
Acesta fixează axa unei piese pe axa unei elemente de referință (axa de referință). Axele ambelor piese sunt determinate ca fiind în punctele mediane ale pieselor.
Acest control poate duce la unele confuzii deoarece axele derivă din măsurători exterioare, mai degrabă decât din plasarea lor reală.
Coaxialitatea creează o zonă de toleranță 3D bazată pe măsurătorile de suprafață în care trebuie să se situeze piesa.
Simetrie
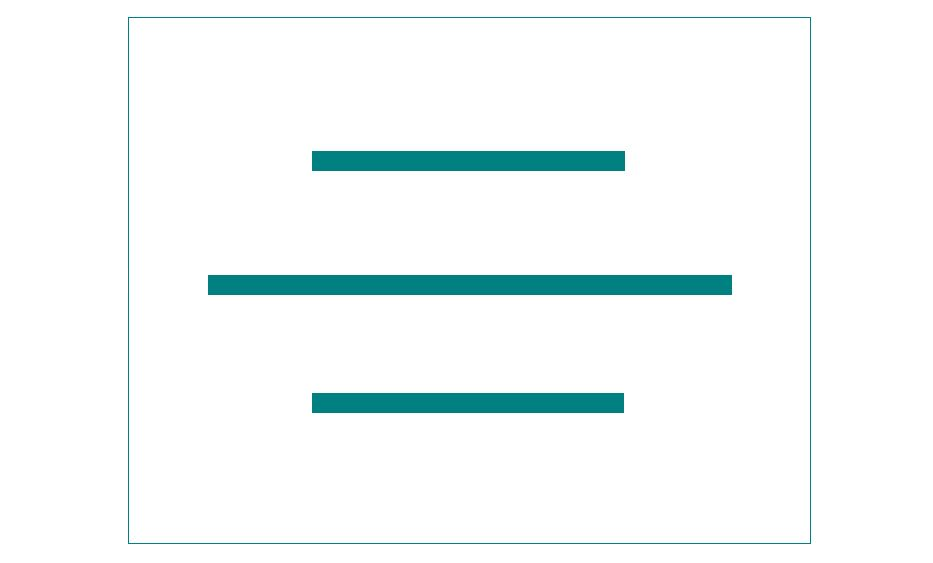
Călăuza de simetrie stabilește un plan central în jurul căruia cele două părți ale elementului sunt plasate la distanță egală. Punctul median al celor două puncte de o parte și de alta trebuie să se situeze în zona de toleranță stabilită în jurul planului central.
Clujba de simetrie nu este foarte frecventă. Are utilizări foarte limitate și este, de asemenea, dificil de inspectat. Avem nevoie de o CMM pentru a inspecta simetria finală.
Poziția reală
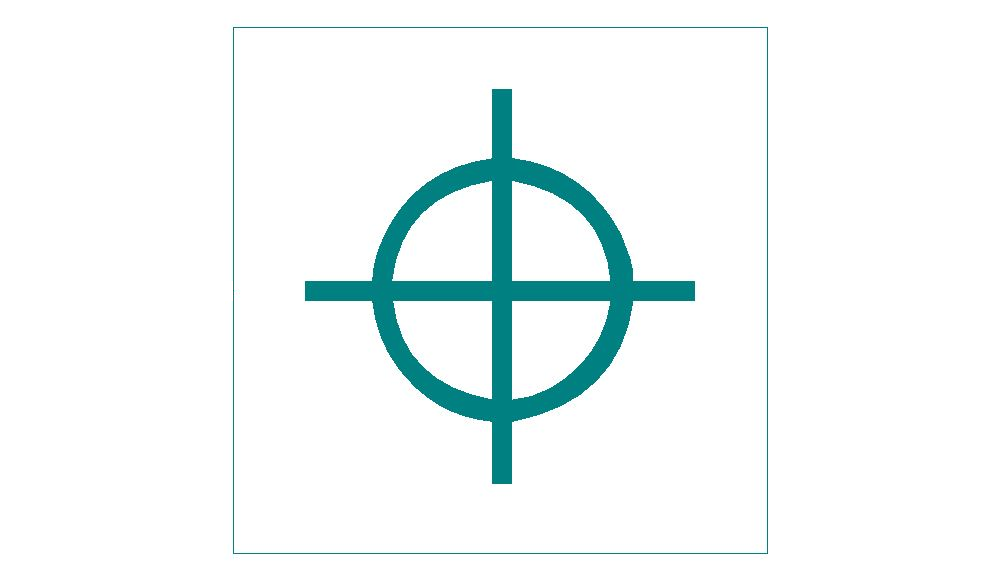
Poziția reală (cunoscută popular sub numele de poziție) este o indicație foarte utilă și își găsește o utilizare extensivă în GD&T.
Poziția definește cât de mult poate varia poziția reală a unei entități față de poziția sa intenționată. Definiția include planul de referință la care se raportează măsurarea.
Acesta include adesea un semn diametral (⌀) pentru a evidenția faptul că zona de toleranță este un cerc, mai degrabă decât doar axele X și Y (despre care am vorbit la începutul articolului ca fiind motivul pentru care a fost creat GD&T în primul rând).
Iată un videoclip excelent care arată cum se utilizează toleranțele pe un desen, folosind poziția reală:
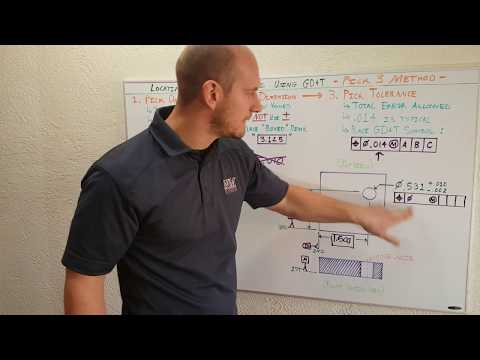
Cum se aplică toleranța de poziție GD&T la un orificiu
Controale de rulare
Utilizăm controalele de rulare pentru a măsura abaterea unei caracteristici a piesei de la poziția sa atribuită în raport cu un punct de referință stabilit. Acest control este utilizat pentru caracteristicile circulare. În esență, acesta măsoară oscilația acesteia prin rotirea elementului în jurul punctului de referință fixat.
Există două tipuri de control al runout-ului.
Circular runout

Circular runout funcționează în două dimensiuni pentru a controla forma, locația și orientarea diferitelor elemente ale piesei. Acest calup 2D are nevoie să îi atribuim o axă de referință pentru a verifica aceste caracteristici.
În jargonul GD&T, rotunjirea circulară este cunoscută în mod obișnuit sub denumirea de runout. Runout măsoară abaterea în elementele de suprafață prin rotație.
Înseamnă că arborele, de exemplu, este rotit de axa sa de referință și elementul prezentat este măsurat pentru toleranță. În esență, limitează vibrațiile unui arbore de lucru pentru a asigura o durată de viață mai lungă pentru piesele conectate, cum ar fi rulmenții.
Runningul total
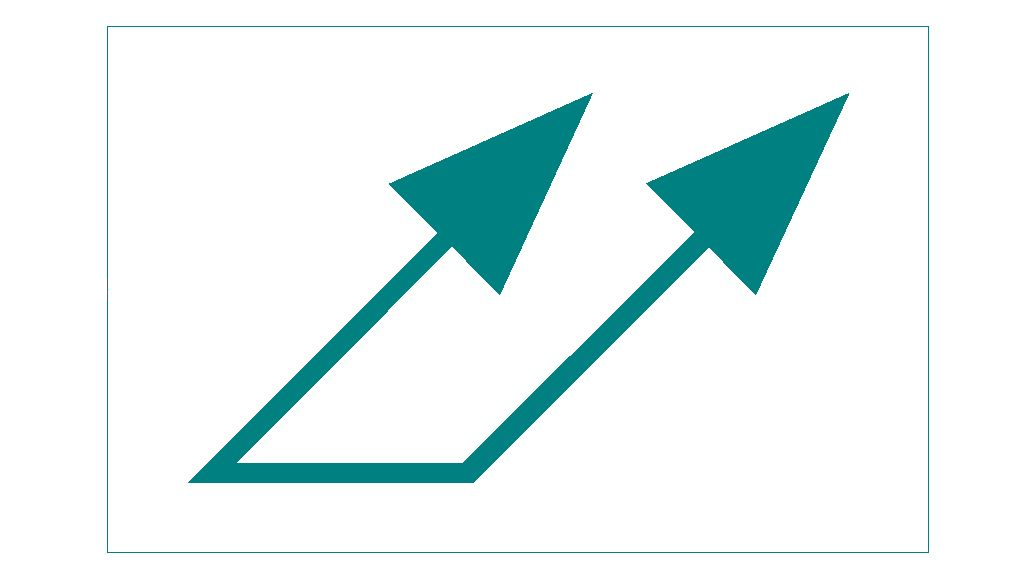
Runningul total este omologul 3D al runout-ului circular. Acesta controlează forma, locația și orientarea, de asemenea. Dar, în loc să verifice secțiuni transversale individuale (ca în cazul runout-ului circular), verifică întreaga suprafață. Astfel, utilizarea runout-ului total ne oferă un control mai strict asupra caracteristicilor elementului.
Inspecție
În toate industriile, nerespectarea de către procesul de fabricație a specificațiilor de proiectare poate fi problematică. În timp ce, în unele cazuri, viețile clienților pot fi puse în pericol, în alte cazuri, o rechemare a unui produs ar putea duce la pierderi monetare uriașe.
Chiar dacă rezultatele nu sunt atât de proaste, reputația unei companii se bazează foarte mult pe calitatea produselor și serviciilor sale.
GD&T standardizează procesul de inspecție prin aducerea inspectorilor pe aceeași platformă cu proiectantul. Acest lucru elimină o mulțime de obstacole. Dar GD&T este un subiect vast.
După cum am văzut, există o serie de caracteristici geometrice diferite, fiecare foarte diferită de alta, care pot fi controlate cu GD&T. Datorită acestei disparități, controlul fiecărei caracteristici necesită o metodă, un instrument și o îndemânare specifice.
Câteva dintre aceste caracteristici pot fi măsurate cu cele mai simple instrumente, în timp ce altele sunt imposibil de măsurat fără un echipament avansat, cum ar fi o mașină de măsurat în coordonate (CMM).
Inspectorii vor avea nevoie de cunoștințe și îndemânare pentru a utiliza diverse instrumente de măsurare, cum ar fi comparatoare, micrometre, calibre vernier, plăci de suprafață și mașini de măsurat în coordonate pentru a inspecta în mod satisfăcător precizia pieselor.
.