Inżynierowie używają oprogramowania CAD do projektowania wszystkich niezbędnych części i komponentów dla projektu. W sferze cyfrowej łatwo jest osiągnąć perfekcję. W prawdziwym życiu, produkcja nigdy nie jest w 100% dokładna.
Czasami, odchylenia kilku milimetrów od podstawowych wymiarów mogą być absolutnie w porządku. W tym samym czasie, dwa współpracujące elementy mogą wymagać niezwykle wysokiej dokładności.
Aby utrzymać oczekiwaną odchyłkę w określonym zakresie, możliwe jest zastosowanie tolerancji inżynierskich. Tolerancje wymiarowe są bardzo powszechne, ale brakuje sposobów na komunikowanie niektórych bardzo ważnych aspektów produkcji. To jest miejsce, gdzie GD&T, lub geometryczne wymiarowanie &tolerancji, wkracza.
Jest to forma opisywania wymiarów i tolerancji w zupełnie nowy sposób. Używając wspólnego języka symboli inżynierskich, pomaga łatwo wskazać wszystkie niezbędne informacje.
- Co to jest GD&T?
- Dlaczego warto wdrożyć GD&T?
- Perfekcyjny montaż
- Wspólny system do wyjaśniania intencji projektowych
- Oszczędność czasu i pieniędzy
- Co należy wziąć pod uwagę?
- Zrozumiałość rysunku
- Ciasne tolerancje tylko wtedy, gdy jest to konieczne
- GD&T Cechy & Symbole
- Wymiary nominalne
- Ramka kontroli właściwości
- Strzałka prowadząca
- Symbol cechy geometrycznej
- Przedział tolerancji cech
- Datumy
- Modyfikatory stanu materiału
- Modyfikator maksymalnego warunku materiałowego
- Modyfikator najmniejszego stanu materiału
- Regardardless of Feature Size (RFS)
- Datumy i Wywołania funkcji
- GD&T Symbole
- Kontrola formy
- Prostość
- Płaskość
- Krągłość
- Cylindryczność
- Kontrole profilu
- Profil liniowy
- Profil powierzchni
- Kontrola orientacji
- Kątowość
- Paralelizm
- Perpendicularity
- Kontrole położenia
- Współśrodkowość
- Symetria
- Pozycja prawdziwa
- How to Apply GD&T Position Tolerance to a Hole
- Runout Controls
- Bieg okrężny
- Bicie całkowite
- Inspekcja
Co to jest GD&T?
Jest to system symboli i standardów używanych przez inżynierów do dostarczania informacji produkcyjnych zespołowi produkcyjnemu.
Przyczyny stosowania Geometrycznego Wymiarowania i Tolerowania (GD&T) są następujące:
- Zapewnia, że współpracujące części dobrze do siebie pasują
- Uniwersalny język działa niezależnie od tego, z kim pracujesz
- Tolerancje dają ograniczenie dla najgorszych warunków
- Definiuje procesy produkcji i kontroli
Stanleyowi Parkerowi przypisuje się bycie inżynierem stojącym za rozwojem systemu GD&T w 1938 roku.
Przedtem wszystkie elementy wykorzystywały tylko osie X-Y do określania położenia np. otworu. Podanie tolerancji położenia w tej skali oznacza, że położenie okrągłego otworu może odbiegać w prostokątnym wzorze od zamierzonego miejsca.
Chcielibyśmy jednak, aby strefa tolerancji była w rzeczywistości okręgiem, ponieważ pozwala to na jednolity pomiar we wszystkich kątach, podczas gdy prostokąt jest dłuższy w kierunku narożników i krótszy w kierunku boków.
Więc gdy Parker zdał sobie z tego sprawę, rozpoczął pracę nad nową koncepcją, która została przyjęta jako standard inżynierii wojskowej w latach 50-tych.
Dzisiaj GD&T jest ważną częścią inżynierii, szczególnie przy tworzeniu części wymagających usług obróbki CNC. Amerykańska norma opisująca te cechy to ASME Y14.5-2018, a europejski odpowiednik to ISO 1101-2017.
GD&T skupia się wyłącznie na geometrii produktu. Wymiary liniowe, chropowatość powierzchni, gwinty, itp. nie są częścią tej normy.
Dlaczego warto wdrożyć GD&T?
Mamy tradycyjne metody oznaczania wymiarów i tolerancji. Jakie jest więc zapotrzebowanie na geometryczne wymiarowanie i tolerowanie?
Geometryczne wymiarowanie i tolerowanie (GD&T) oferuje kilka unikalnych zalet w stosunku do zwykłych metod. Zobaczmy jakie to zalety.
Perfekcyjny montaż
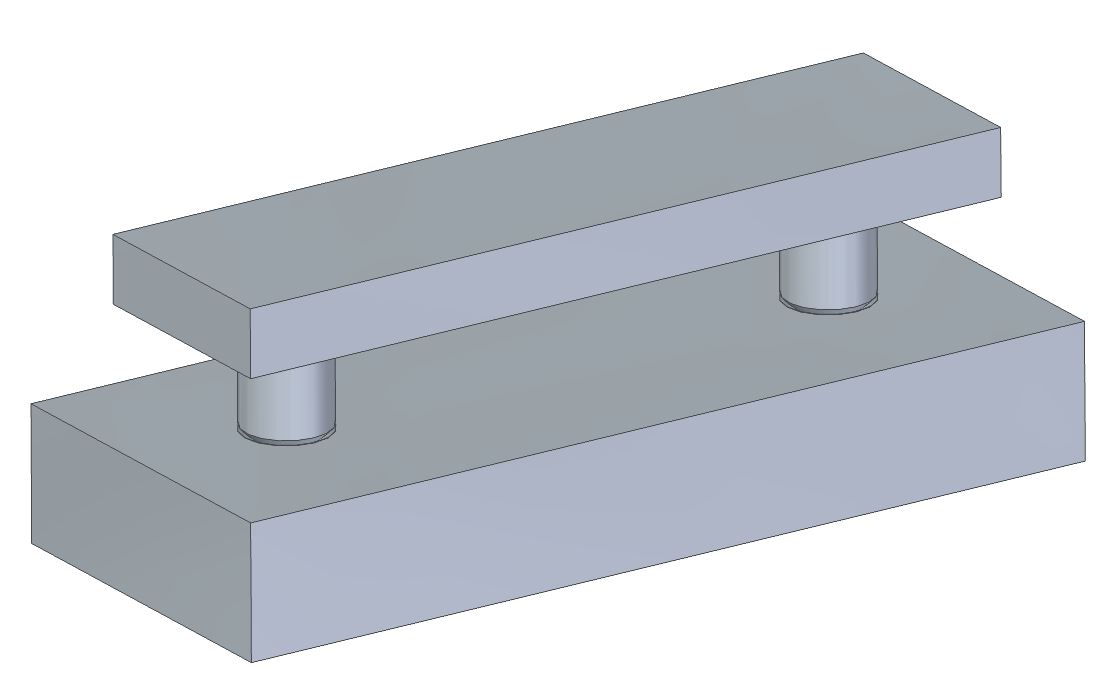
Najważniejszą wadą stosowania tradycyjnego wymiarowania i tolerowania jest to, że oznaczają one pojedyncze części i informacje o cechach części. Nie gwarantuje to, jak dobrze nasze części będą pasować i funkcjonować na poziomie montażu.
Jest to ważne, ponieważ większość części nie jest użyteczna sama w sobie. Weźmy pod uwagę przykład korbowodu. Sam w sobie nie zapewnia nam żadnych korzyści. Ale kiedy połączymy go z wałem korbowym i tłokiem, staje się nieco bardziej użyteczny, ponieważ przekształca ruch liniowy tłoka w ruch obrotowy wału korbowego.
Gdy ten zespół staje się częścią większego zespołu, takiego jak silnik wysokoprężny, może skończyć jako część generatora, który zapewnia nam wiele zastosowań.
W związku z tym ważne jest, aby nasze części dobrze do siebie pasowały. Dlatego właśnie potrzebujemy GD&T. Używając go, możemy być w 100 procentach pewni, że nasze części będą do siebie pasować i działać dokładnie tak, jak trzeba.
Wspólny system do wyjaśniania intencji projektowych
GD&T zapewnia również projektantowi platformę do przekazania jego intencji projektowych wszystkim odpowiednim działom. Należą do nich:
- Produkcja
- Inspekcja
- Przyszli projektanci w dziale projektowym, którzy podejmą pracę, jeśli początkowy zespół projektowy nie będzie dostępny
Definicje, słownictwo i zasady są proste i powszechnie zrozumiałe. To sprawia, że symbole są łatwe do przetłumaczenia dla każdego inżyniera i są doskonałym sposobem na przekazanie intencji projektanta.
Oszczędność czasu i pieniędzy
To najważniejsza korzyść z używania GD&T. Użycie tego systemu zmniejsza marnotrawstwo, ponieważ redukuje liczbę cykli projekt-produkcja-testowanie-pasowanie.
Dzieje się tak, ponieważ wyprodukowane części pasują dobrze przy pierwszej próbie i w konsekwencji liczba odrzutów będzie niska. Używanie wspólnego języka zmniejsza również wysiłek potrzebny do kontroli.
Uzyskaj wycenę produkcji w kilka sekund
-
Wycena w kilka sekund
-
Krótki czas realizacji
-
Dostawa przez Fractory
Uzyskaj wycenę
Co należy wziąć pod uwagę?
Geometryczne wymiarowanie i tolerowanie jest bardziej wydajnym systemem w porównaniu do tradycyjnych tolerancji. Ale działa tylko wtedy, gdy wszystkie działy (projektowanie, inżynieria, produkcja) są dobrze zorientowane w czytaniu i interpretowaniu informacji.
W związku z tym, podczas tworzenia rysunków inżynierskich i tolerowania różnych cech części, ważne jest, aby przestrzegać zalecanych wytycznych/konwencji dla dobra wszystkich, którzy będą wchodzić w interakcję z rysunkiem na każdym etapie rozwoju produktu.
Przestrzeganie ich zapewnia, że rysunek jest znormalizowany i wszyscy są na tej samej stronie, jeśli chodzi o specyfikę rysunku. Niektóre z tych dobrych praktyk są następujące.
Zrozumiałość rysunku
Jest to prawdopodobnie najważniejsza jakość rysunku. Zrozumiałość odnosi się do jasności, z jaką cechy części są rysowane i tolerancje są pokazane na rysunku. Niektóre sposoby poprawy zrozumiałości rysunku są następujące:
- Narysuj prawdziwe profile dla wszystkich cech części.
- Naznacz wymiary i tolerancje poza rysunkiem (nie na górze). Używaj białej przestrzeni efektywnie.
- Kierunek odczytu musi być stały. Czytelnik powinien być w stanie odczytać wszystkie wymiary trzymając rysunek pionowo.
- Wyznacz wymiary równoległych elementów części.
- Objaśnij krótko część i jej funkcję.
- Określ kąty tylko wtedy, gdy nie są one kątami prostymi (90°).
Ciasne tolerancje tylko wtedy, gdy jest to konieczne
Bez dopasowania/funkcji części, tolerancje muszą być tak luźne, jak to tylko możliwe. Zmniejsza to koszty produkcji i czas realizacji. Zalecamy pozostawienie wyboru metody wytwarzania mechanikom.
Projektant musi również wspomnieć o ogólnej tolerancji dla rysunku. Działa ona jako tolerancja standardowa dla wszystkich elementów części. Dla elementów części z inną granicą tolerancji, projektant musi wymienić je w odpowiednich miejscach.
Te specyficzne granice tolerancji będą nadrzędne w stosunku do tolerancji ogólnych. Podczas określania specjalnych limitów tolerancji, preferuj cechy funkcjonalne w stosunku do innych cech.
GD&T Cechy & Symbole
Język GD&T jest w stanie zdefiniować prawie wszystkie cechy, które są niezbędne do zapewnienia doskonałego montażu.
System używa do tego celu szeregu symboli. Aby poprawnie używać tych symboli inżynierskich na rysunkach, musimy najpierw zapoznać się z niektórymi podstawowymi elementami tego systemu.
Możemy zacząć od różnych definicji, terminologii i zasad zanim przejdziemy do symboli GD&T.
Wymiary nominalne
Wymiar nominalny jest wielkością rzeczywistego profilu. Jest to dokładny wymiar, który chcielibyśmy osiągnąć w idealnej sytuacji. Specyfika cech, takich jak rozmiar, orientacja, położenie od punktu odniesienia mają nominalny rozmiar, że machinists cel.
Na rysunku, są one wyświetlane w polu. Może być pokazany jako liczba lub z popularnego standardu, takiego jak ASME.
Ramka kontroli właściwości
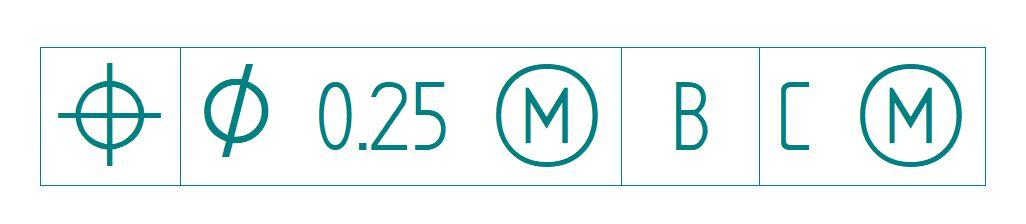
Ta ramka zawiera informacje o specyfice części. Zawiera ona różne przedziały, gdzie każdy przedział definiuje konkretny atrybut cechy części. W jednym spojrzeniu, ramka kontroli cech przekazuje informacje wymagane do obróbki i kontroli.
Ramka kontroli cech może być podzielona na 4 główne części w następujący sposób.
Strzałka prowadząca
Strzałka ta oznacza cechę części pod kontrolą. Jeśli prowadzi do powierzchni, powierzchnia jest pod kontrolą geometryczną. Jeśli oznacza wymiar średnicowy, to GD&T kontroluje oś. Ta strzałka może nie występować w niektórych przypadkach.
Symbol cechy geometrycznej
Pierwszy przedział (licząc od lewej) zawiera symbol cechy geometrycznej. W tym miejscu określamy cechę geometryczną. W sumie istnieje 14 typów tolerancji geometrycznych w oparciu o liczbę symboli, a 15, gdy są sklasyfikowane.
Różne typy cech geometrycznych to kontrola kształtu, kontrola profilu, kontrola położenia, kontrola orientacji itp. Zanurzymy się głębiej w każdą kategorię później.
Przedział tolerancji cech
Drugi blok zawiera maksymalnie 3 (czasami 2 lub 1) różne symbole.
Pierwszy symbol pokazuje typ przedziału tolerancji. Symbol średnicy (⌀) oznacza strefę średnicową (cylindryczna strefa tolerancji). Aby określić strefę sferyczną, symbolem jest litera „S”, po której następuje symbol średnicy (⌀). W przypadku braku symbolu przyjmujemy strefę o całkowitej szerokości.
Drugi symbol w 2. bloku podaje wartość strefy tolerancji w mm. Wartość ta musi być zawsze obecna w 2. bloku.
Trzeci symbol w tym bloku to modyfikator tolerancji. Ten modyfikator materiału występuje tylko wtedy, gdy element ma rozmiar, np. otwór. Przykładami modyfikatorów materiału są MMC (maksymalny stan materiału) i LMC (najmniejszy stan materiału). Więcej informacji na temat różnych dostępnych modyfikatorów zostanie omówionych w dalszej części artykułu.
Datumy
Trzeci blok podaje informacje o datum(ach) z minimalną liczbą 1 i maksymalną 3 datum. W przypadku 3 układów odniesienia są one określane jako pierwszorzędny, drugorzędny i trzeciorzędny, a każdy z nich jest przedstawiony w innym polu (na przykład na powyższym rysunku są 2). Blok ten może również zawierać modyfikator materiału.
Wszystkie powyższe informacje pomagają nam zrozumieć, jak czytać ramkę kontrolną elementu. Aby lepiej zrozumieć, jak tolerancja może być dostosowana przy użyciu modyfikatorów stanu materiału, musimy poznać różne opcje.
Modyfikatory stanu materiału
Modyfikatory stanu materiału przekazują intencję, gdy tolerancja dotyczy elementu przy określonym rozmiarze elementu. Kiedykolwiek nadajemy tolerancje jakiemukolwiek elementowi, ustanawia to dwa warunki materiałowe
- Maksymalny warunek materiałowy
- Najmniejszy warunek materiałowy
Rozważmy wał o średnicy 100 mm. Podczas produkcji, jeśli damy mu tolerancję ±0,2 mm, to przy 100,2 mm, wał będzie zawierał maksymalną ilość materiału. To właśnie rozumiemy pod pojęciem maksymalnego stanu materiału.
Z drugiej strony ten sam wał, gdy zostanie wykonany o średnicy 99,8 mm, będzie zawierał najmniejszą ilość materiału. Te ograniczenia nazywamy warunkami materiałowymi.
Tolerancje geometryczne mogą być stosowane do elementu na 3 różne sposoby. Są to następujące sposoby:
- Maksymalny warunek materiałowy
- Najmniejszy warunek materiałowy
- Bez względu na rozmiar elementu
Modyfikator maksymalnego warunku materiałowego
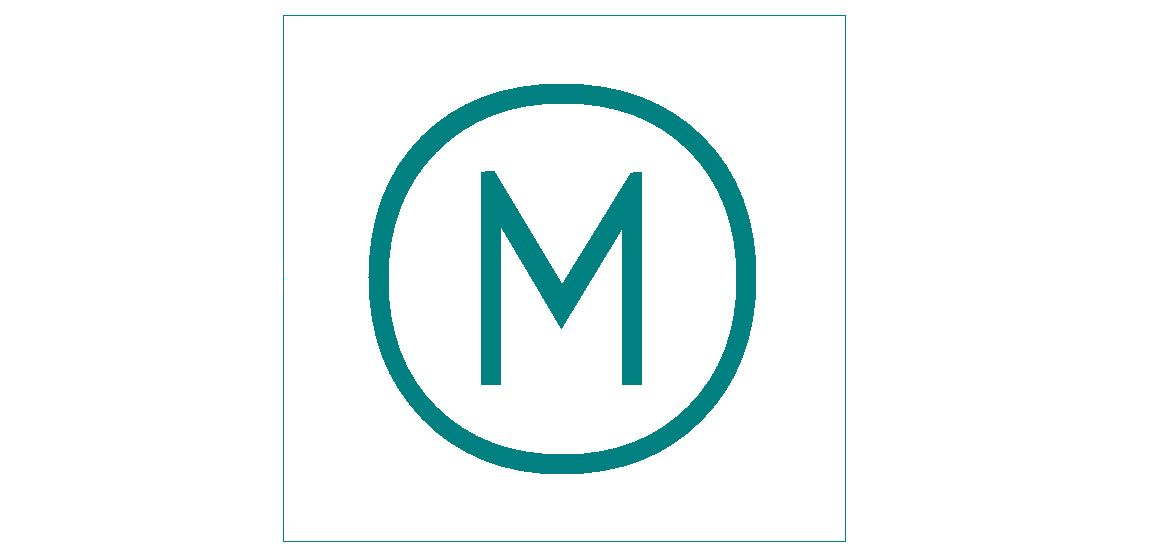
Oprezentujemy ten warunek za pomocą zakreślonego „M” po wartości tolerancji w przedziale kontroli elementu. Element zawiera maksymalny materiał przy tym rozmiarze elementu.
Dla zewnętrznych FOS (Feature Of Size), takich jak średnica wału, MMC reprezentuje największy rozmiar. Dla wewnętrznych FOS, takich jak średnica otworu, MMC reprezentuje najmniejszy możliwy rozmiar w podanych granicach tolerancji, ponieważ mniejszy otwór oznacza, że więcej materiału zostanie.
Gdy musimy zastosować tolerancję geometryczną przy maksymalnym stanie materiału, wymieniamy ten stan w ramce sterowania elementem.
Modyfikator najmniejszego stanu materiału
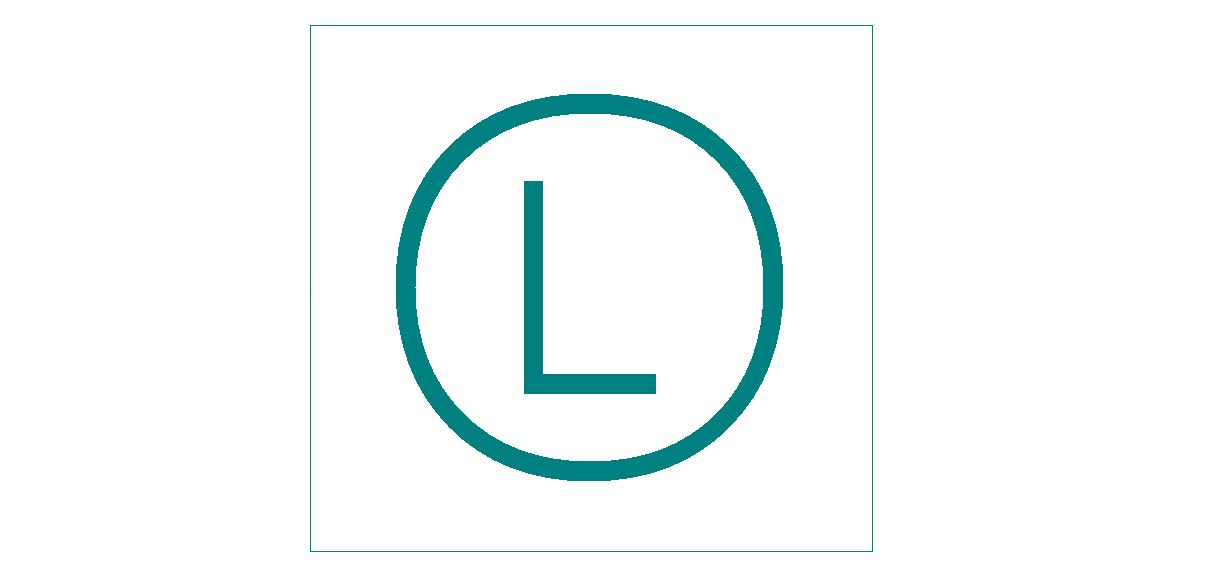
LMC to stan, w którym materiał zawiera najmniej materiału.
Dla zewnętrznych FOS, będzie to najmniejszy możliwy rozmiar w określonych granicach. A dla wewnętrznego FOS, będzie to największy możliwy rozmiar.
Przedstawiamy ten modyfikator za pomocą litery „L” w kółku. Cecha ta usuwa nadmiar materiału, a tym samym wagę. Aby zastosować tolerancje geometryczne przy tym warunku, stosujemy jej symbol w ramce sterującej cechą.
Regardardless of Feature Size (RFS)
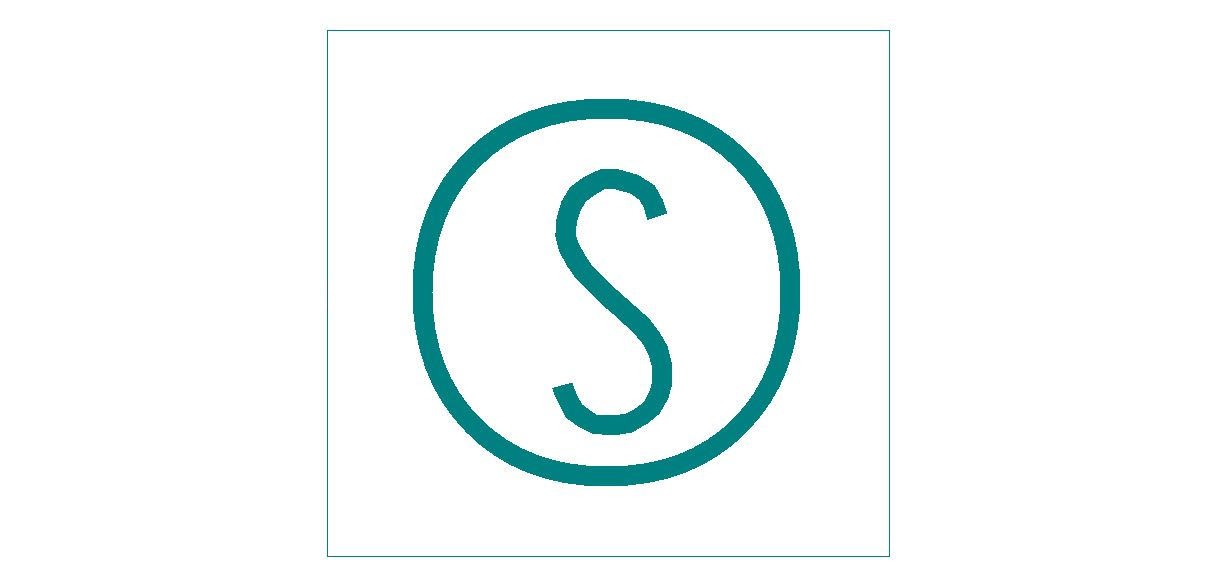
Gdy dane tolerancje geometryczne stosujemy przy dowolnym przyroście wielkości FOS, oznaczamy to przez RFS. Symbolem dla RFS była litera „S” zamknięta w okręgu, ale nie jest już potrzebna, ponieważ RFS jest teraz uważana za stan domyślny i nie potrzebuje symbolu.
Datumy i Wywołania funkcji
Datumy są punktami odniesienia do pomiaru tolerancji wymiarowych. Może to być punkt, linia lub płaszczyzna. Z pomocą układu odniesienia, ustanawiamy ramy odniesienia układu odniesienia (DRF). DRF jest w zasadzie układem współrzędnych 3D, który pomaga nam określić pozycje wszystkich innych cech w odniesieniu do DRF.
Istnieje 6 stopni swobody (3 translacyjne i 3 rotacyjne), które musimy kontrolować, aby efektywnie produkować i kontrolować części. Używamy DRF, aby ustalić te stopnie swobody.
Cechy datum są rzeczywistymi cechami części, takimi jak otwory i szczeliny. Mogą one wykazywać odchylenia od pożądanych pozycji.
Wśród wszystkich cech układu odniesienia, dajemy najwyższy priorytet tym, które łączą się z innymi częściami w zespole. Możemy wymienić więcej niż jeden układ odniesienia w naszej ramce kontrolnej cechy. Zgodnie z kolejnością DRF w ramce kontrolnej cechy, części są kojarzone z DRF w kolejności malejącej ważności.
GD&T Symbole
Dostępnych jest do 14 symboli GD i T, aby reprezentować różne charakterystyki geometryczne cech. Symbole te pomagają nam określić te cechy jako wymagania dla produktu końcowego.
Umieszczamy te symbole w pierwszym przedziale ramki kontroli elementu. Przyjrzymy się tym rodzajom kontroli tolerancji.
Kontrola formy
Jak sama nazwa wskazuje, kontrola formy odnosi się do ostatecznej formy lub kształtu cechy. Definiujemy kontrole formy, aby ograniczyć odchylenie tolerancji geometrycznej od jej idealnej formy. Niektóre popularne charakterystyki kontroli kształtu są następujące.
Prostość
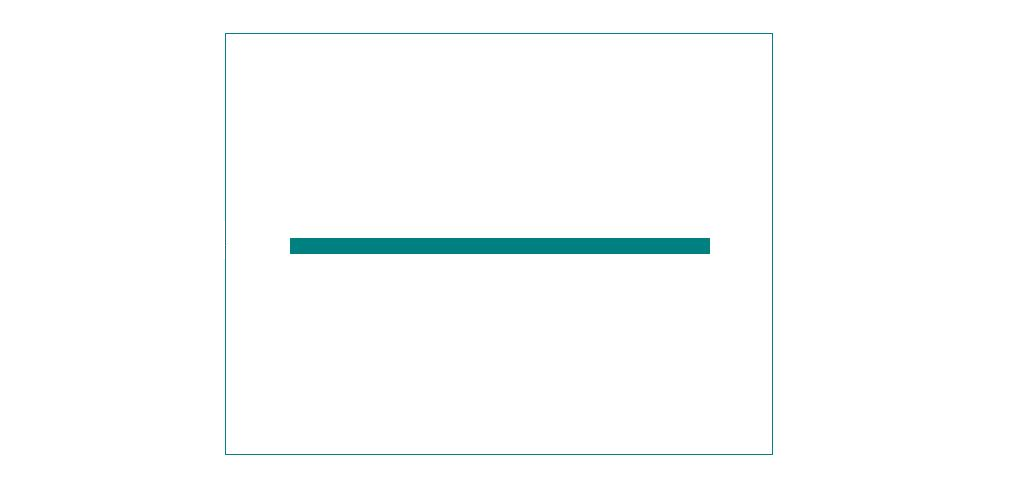
Aby wskazać charakterystykę prostoliniowości cechy (takiej jak oś lub powierzchnia), używamy jej symbolu (prosta linia pozioma) w pierwszym przedziale.
Prostoliniowość powierzchni może dotyczyć powierzchni płaskich, takich jak bok bloku lub powierzchni zakrzywionych, takich jak bok walca wzdłuż kierunku osi. Określa ona dopuszczalną zmienność linii (2 wymiary) na powierzchni w ramach określonej tolerancji.
Prostoliniowość osiowa odnosi się zwykle do osi wału lub otworu, na przykład. Sprawdzian Go/no go jest narzędziem kontroli stosowanym w procesie upewniania się, że część jest zgodna z wymaganiami.
Płaskość
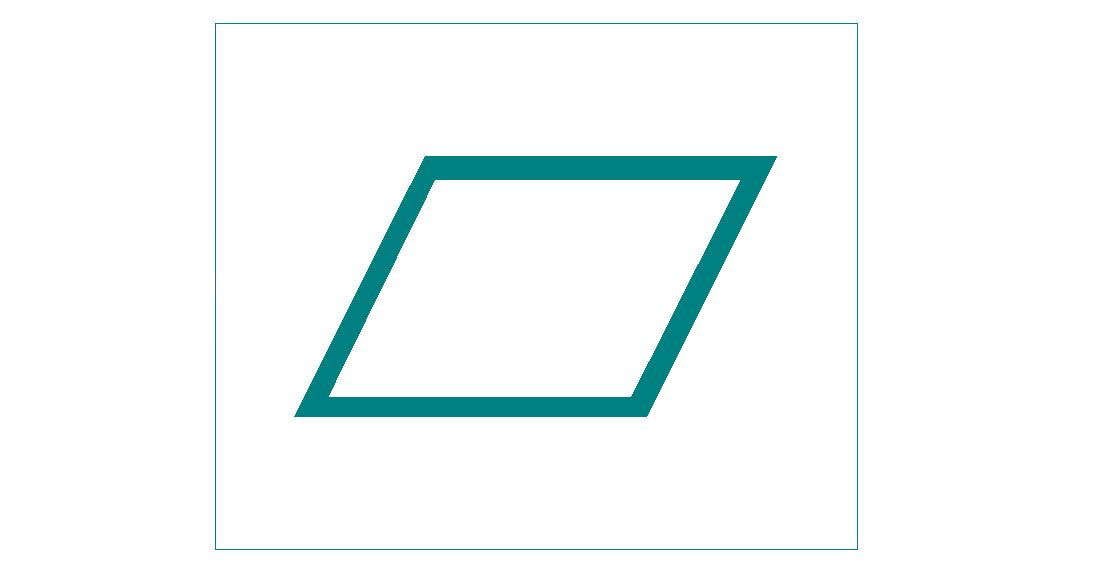
Charakterystyki tej używamy dla takich cech jak powierzchnia czołowa części. Symbolem płaskości jest równoległobok przechylony w prawo. Różnica między najwyższym i najniższym punktem płaskiej powierzchni to jej płaskość.
Symbol płaskości nie wymaga żadnych układów odniesienia, gdyż pokazuje jedynie zakres tolerancji, w którym cała powierzchnia części musi być zgodna w 3 wymiarach.
Do sprawdzania wyników służy wysokościomierz. Dotyka on różnych obszarów powierzchni, aby określić, czy wszystkie punkty znajdują się wewnątrz strefy tolerancji.
Krągłość
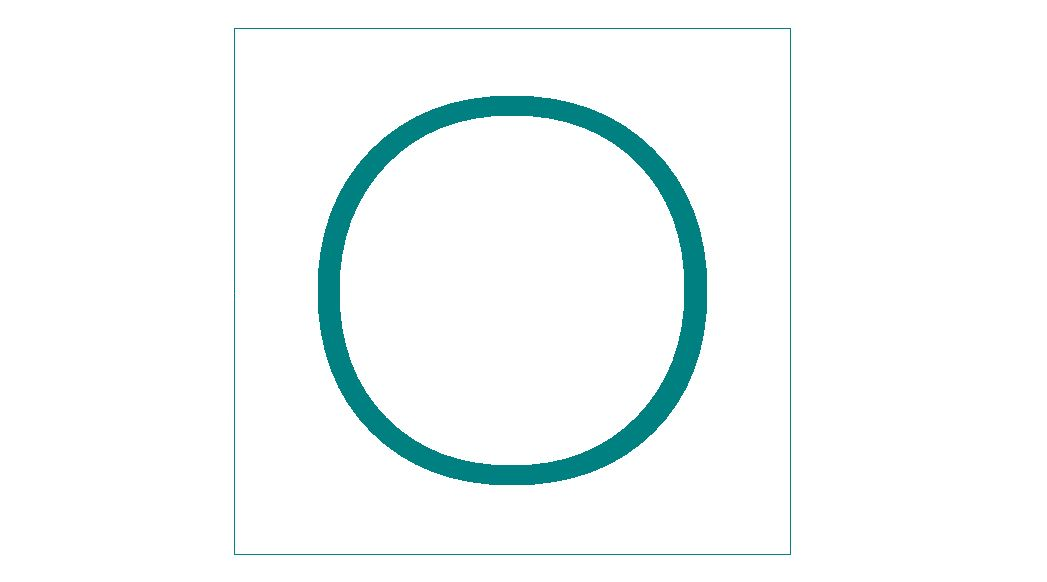
Krągłość cechy pokazuje, jak blisko obwód części powinien być zbliżony do idealnego okręgu. Wykorzystuje 2 koncentryczne okręgi na płaszczyźnie prostopadłej do osi części, aby zdefiniować odpowiedni zakres tolerancji w 2D. Każdy punkt ostatecznych pomiarów musi mieścić się pomiędzy tymi okręgami.
Ta charakterystyka jest pokazana jako okrąg w pierwszym przedziale ramki kontrolnej elementu.
Cylindryczność
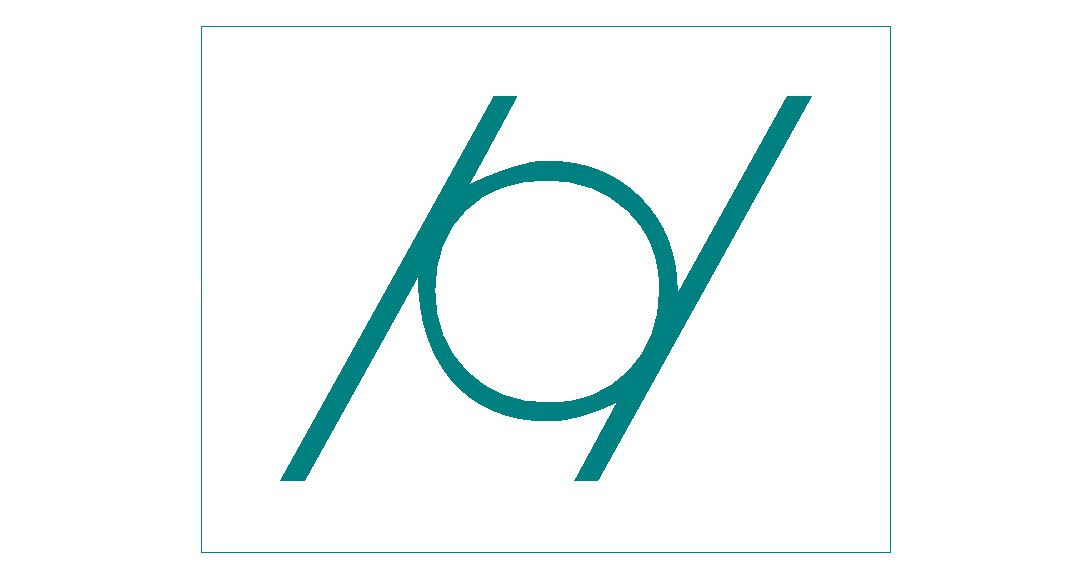
Cylindryczność jest w zasadzie okrągłością w 3D, co oznacza, że przebiega ona na całej długości części.
Cecha ta opisuje również inne cechy cylindryczne, takie jak stożkowość, prostoliniowość i okrągłość. Dlatego ta cecha jest również kosztowna do sprawdzenia.
Kontrole profilu
Używamy kontroli profilu do kontrolowania strefy tolerancji 3D wokół elementu. Ta funkcja pomaga nam nadać limity tolerancji zaawansowanym krzywym i kształtom.
Funkcja, która jest dobra dla zaawansowanych krzywych, musi naturalnie działać dobrze również z prostszymi krzywymi. To czyni kontrole profili niezwykle uniwersalnymi. Dlatego niektórzy projektanci zalecają porzucenie wszystkich innych kontrolek i pracę tylko z kontrolkami profilu.
Te kontrolki tworzą granicę tolerancji wokół zaawansowanej krzywej poprzez naśladowanie jej po obu stronach. Następnie zapobiegają one wyjściu dowolnego punktu na krzywej funkcji poza granicę tolerancji. Elementy sterujące profilu są dwóch typów.
Profil liniowy
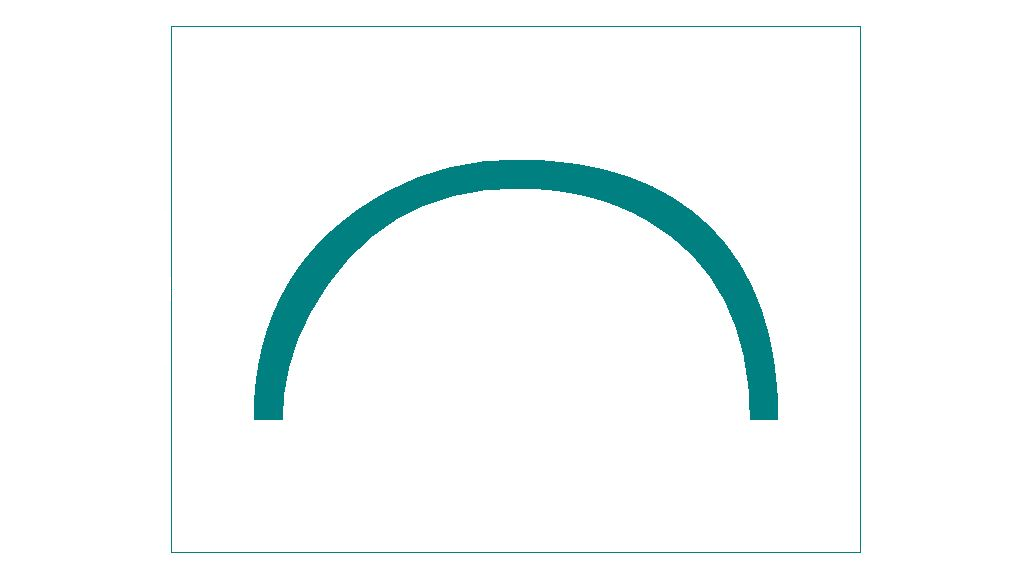
Profil liniowy ustanawia strefę tolerancji wokół zmiennych przekrojów 2D części. Kontroluje poszczególne elementy linii elementu części.
Kontrola profilu linii śledzi idealną krzywą na granicach tolerancji po obu stronach. Wszystkie punkty na krzywej części muszą leżeć w tych granicach.
Profil powierzchni
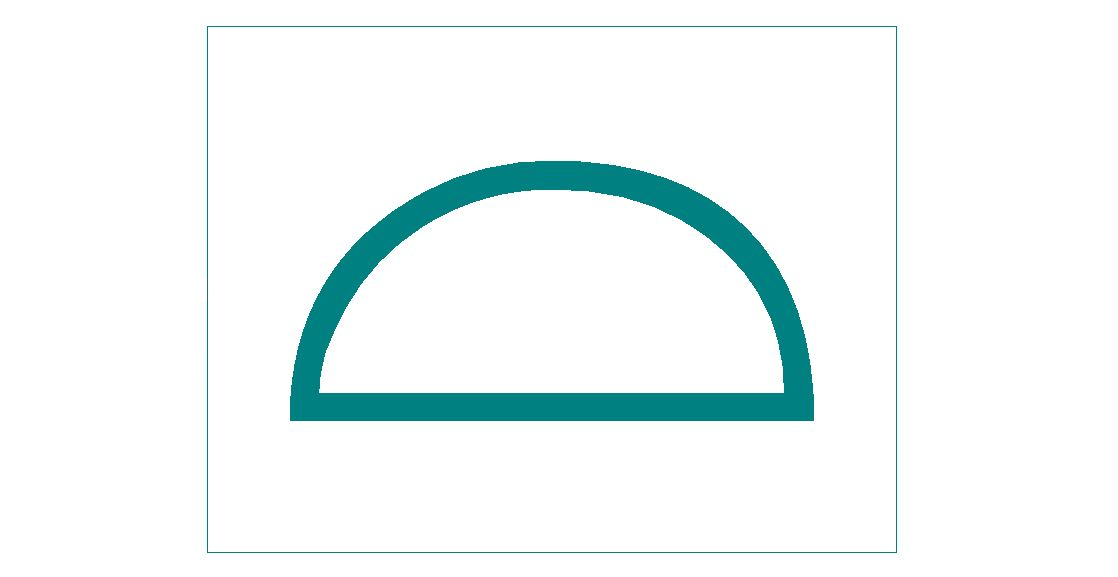
Kontrola profilu powierzchni jest bardziej popularna w porównaniu z kontrolą linii. Zamiast dwuwymiarowej strefy tolerancji, kontrola profilu powierzchni tworzy strefę 3D wokół powierzchni.
Wszystkie punkty na powierzchni stołu muszą leżeć wewnątrz dwóch wirtualnych płaszczyzn.
Kontrola orientacji
Tolerancja orientacji kontroluje orientację elementu względem zdefiniowanego punktu odniesienia. Istnieją trzy rodzaje kontroli orientacji w GD&T.
Kątowość
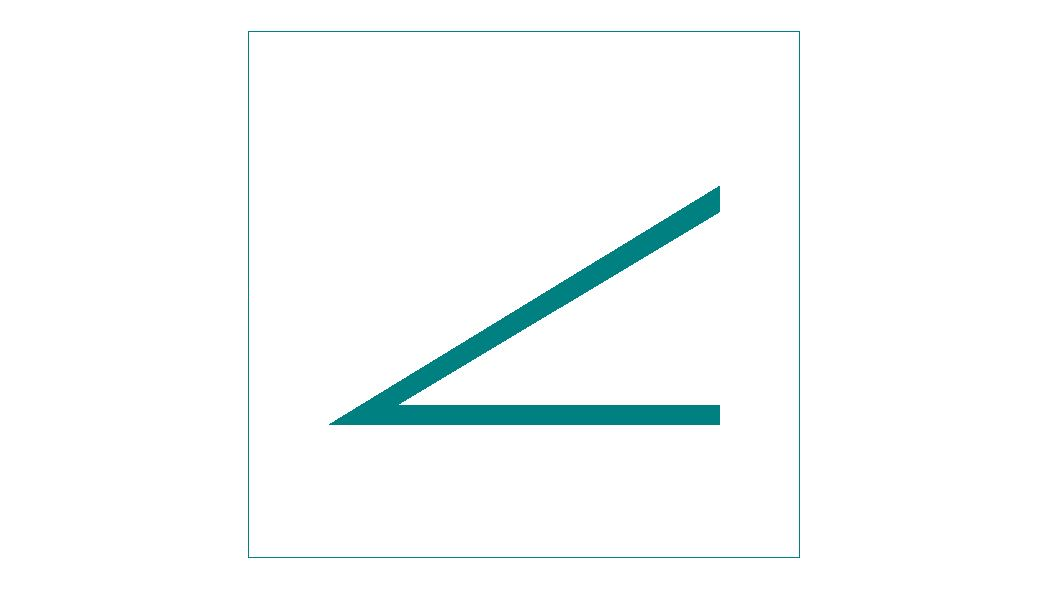
Kontrola kątowości utrzymuje w ryzach kąt elementu względem układu odniesienia. Możemy jej użyć do kontrolowania linii 2D, ale jest ona bardziej popularna przy utrzymywaniu powierzchni (3D) pod kontrolą.
Ten rodzaj ścisłej kontroli utrzymuje kąt i płaskość powierzchni w ryzach i jest zalecany dla elementów części, które łączą się z innymi częściami poprzez kątową powierzchnię.
Ważne jest, aby zauważyć, że cecha kątowości kontroluje kąt pośrednio, nie będąc zasadniczo tym samym co tolerancja kąta (np. +/- 2°). Raczej, niezbędny kąt jest wynikiem przestrzegania wymagań wymiarowych określonych przez tę kontrolę.
Paralelizm
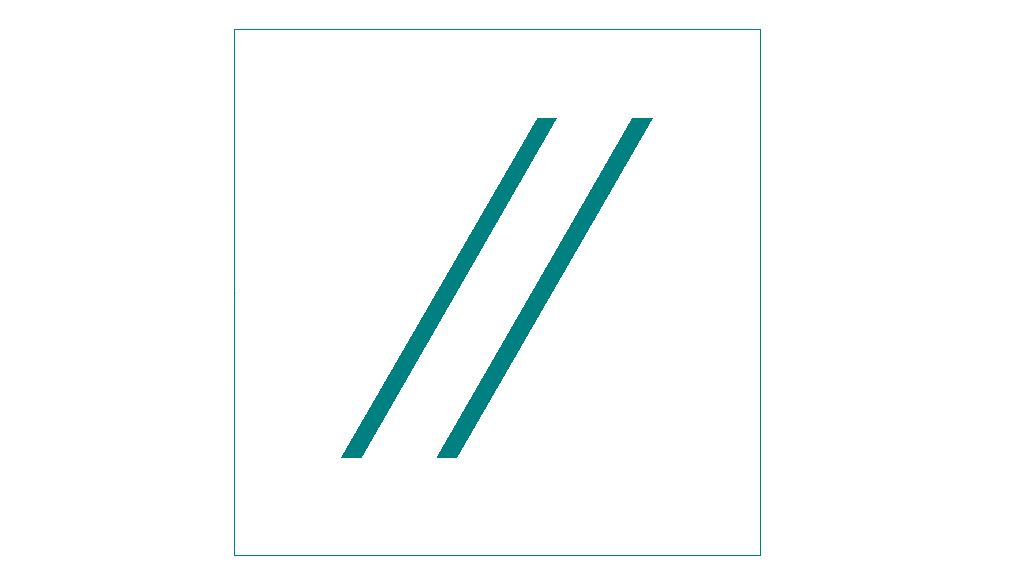
Paralelizm jest wyrafinowaną formą kątowości. Tutaj punktem odniesienia jest powierzchnia, którą musimy naśladować, a kąt jest ustawiony na 0°. Istnieją 2 rodzaje równoległości: równoległość powierzchni i równoległość osi.
Możemy wybrać oś lub powierzchnię jako punkt odniesienia. To staje się naszym punktem odniesienia i odnosimy się do niego w 3 bloku ramki kontrolnej elementu jako do punktu odniesienia dla elementu.
Podobnie jak kątowość, nie kontroluje ona rzeczywistego kąta, ale raczej zabezpiecza go poprzez określenie wymagań w postaci strefy tolerancji.
Perpendicularity
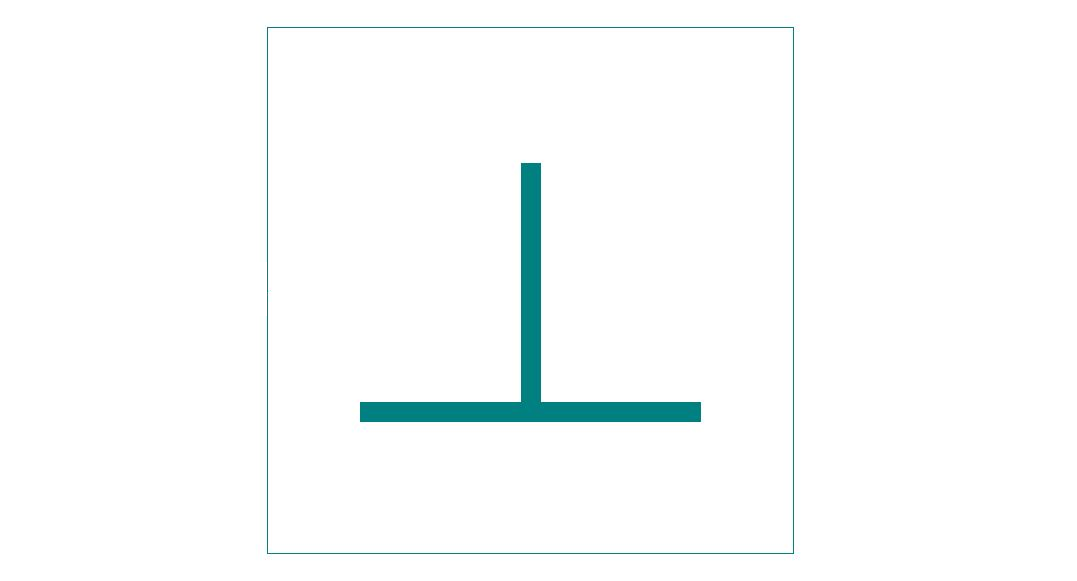
Perpendicularity jest również specyficzną formą kątowości, gdzie kąt jest ustawiony na 90°. Jest to trudna kontrola, ponieważ może oznaczać dwa bardzo różne rodzaje wymagań.
Jest prostopadłość powierzchni (Symbol:⟂), a następnie jest prostopadłość osi (Symbole: ⟂+⌀).
Prostopadłość powierzchniowa określa, że powierzchnia lub linia musi być prostopadła do powierzchni lub linii odniesienia, podobnie jak kątowość. Dwie wirtualne płaszczyzny/linie są zakładane wokół powierzchni docelowej w celu kontroli.
Prostopadłość osi określa jak prostopadła musi być oś do wspomnianego układu odniesienia. Odbywa się to przez utworzenie wirtualnego walca wokół osi docelowej na powierzchni dokładnie równoległej do powierzchni układu odniesienia.
Kontrole położenia
Kontrola tolerancji położenia jest używana do ścisłej kontroli położenia elementu względem układu odniesienia. Istnieją cztery główne typy kontroli położenia.
Współśrodkowość
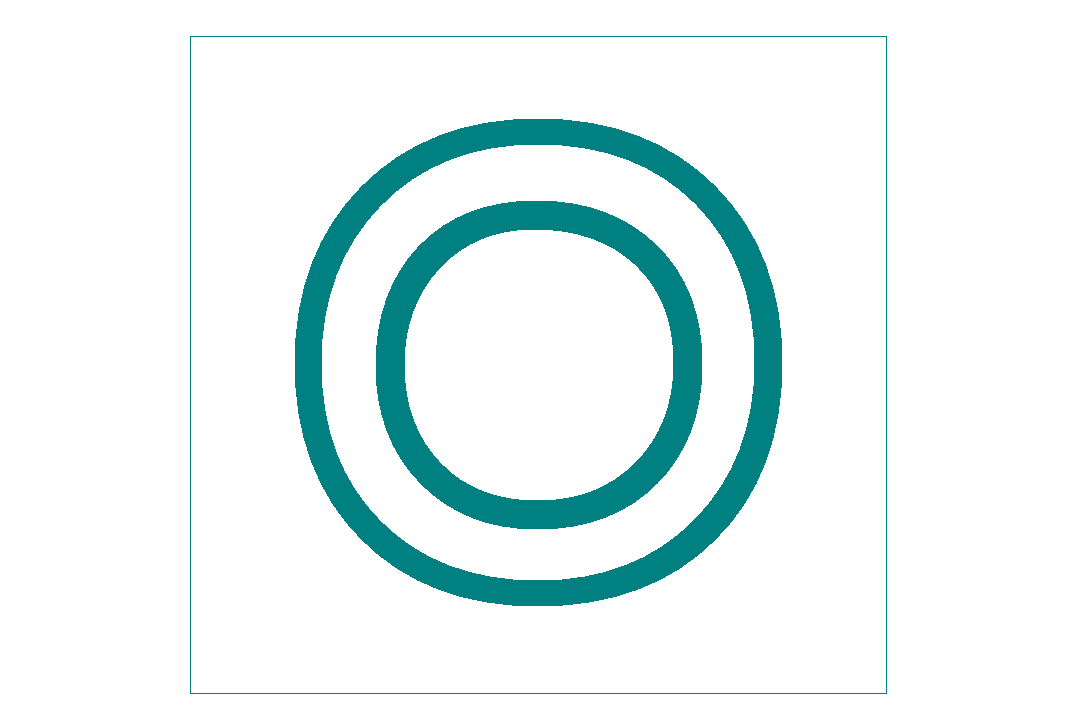
Współśrodkowość, znana również jako współosiowość (chociaż nie jest to dokładnie to samo), kontrola utrzymuje współśrodkowość elementów kołowych, jak również cylindrycznych.
Ustalają one oś części do osi elementu odniesienia (osi układu odniesienia). Osie obu części są określane w punktach środkowych części.
Ta kontrola może prowadzić do pewnych pomyłek, ponieważ osie pochodzą z pomiarów zewnętrznych, a nie z ich rzeczywistego umieszczenia.
Współosiowość tworzy strefę tolerancji 3D na podstawie pomiarów powierzchni, w której musi leżeć część.
Symetria
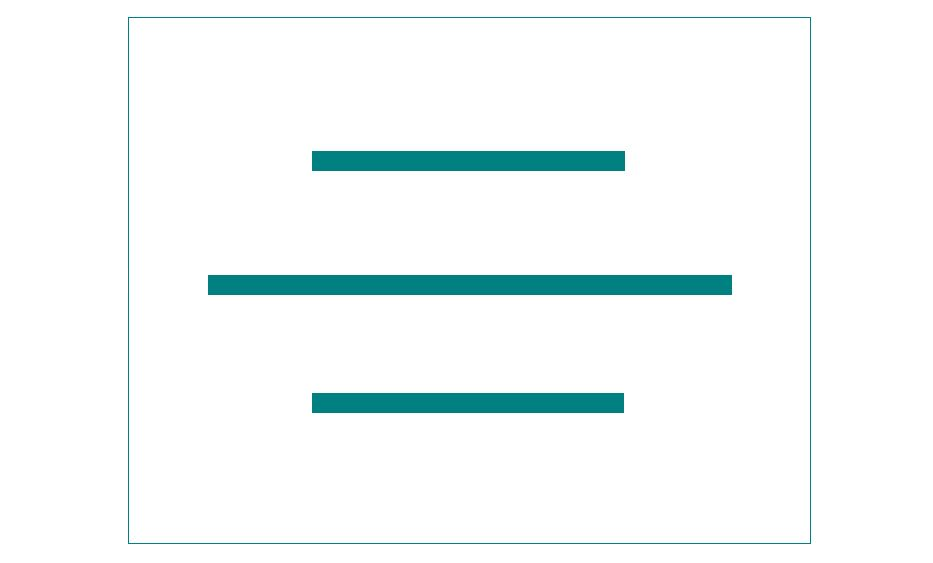
Wywołanie symetrii ustanawia płaszczyznę centralną, wokół której dwie części elementu są umieszczane w równej odległości. Punkt środkowy dwóch punktów po obu stronach musi leżeć w strefie tolerancji ustalonej wokół płaszczyzny centralnej.
Wywołanie symetrii nie jest zbyt często stosowane. Ma bardzo ograniczone zastosowanie i jest również trudne do sprawdzenia. Potrzebujemy maszyny CMM do kontroli ostatecznej symetrii.
Pozycja prawdziwa
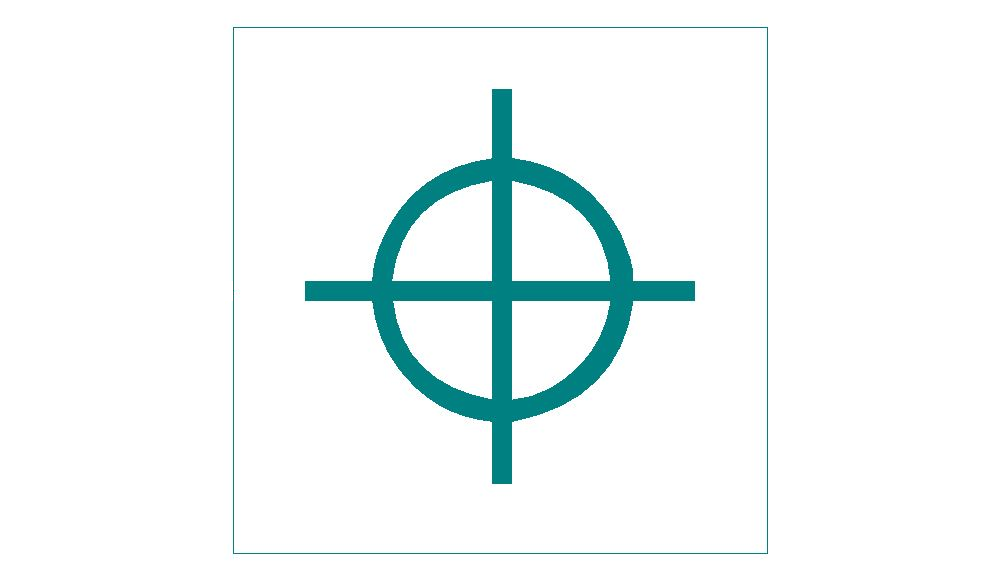
Pozycja prawdziwa (popularnie zwana pozycją) jest bardzo użytecznym wywołaniem i znajduje szerokie zastosowanie w GD&T.
Pozycja określa, jak bardzo rzeczywista pozycja elementu może różnić się od jego pozycji zamierzonej. Definicja zawiera płaszczyznę odniesienia, do której odnosi się pomiar.
Często zawiera znak rombu (⌀), aby podkreślić, że strefa tolerancji jest okręgiem, a nie tylko osią X i Y (o czym mówiliśmy na początku artykułu jako o przyczynie stworzenia GD&T w pierwszej kolejności).
Tutaj znajduje się świetny film pokazujący, jak używać tolerancji na rysunku, używając true position:
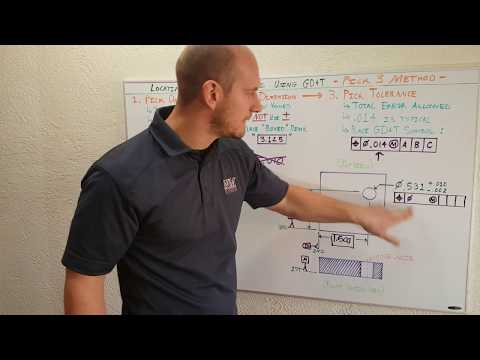
How to Apply GD&T Position Tolerance to a Hole
Runout Controls
Kontroli bicia używamy do pomiaru odchylenia elementu części od jego przypisanej pozycji względem ustalonego układu odniesienia. Ta kontrola jest używana dla elementów okrągłych. Zasadniczo mierzy ona jego chybotliwość poprzez obrót elementu wokół ustalonego punktu odniesienia.
Są dwa typy kontroli bicia.
Bieg okrężny

Bieg okrężny działa w dwóch wymiarach, aby kontrolować formę, położenie i orientację różnych elementów części. To wywołanie 2D wymaga od nas przypisania mu osi odniesienia, aby sprawdzić te cechy.
W żargonie GD&T, bicie kołowe jest powszechnie znane jako bicie. Bicie mierzy odchylenie w elementach powierzchniowych przez obrót.
Mając na myśli, że wał, na przykład, jest obracany przez jego oś odniesienia i wyróżniony element jest mierzony dla tolerancji. W istocie, ogranicza drgania wału roboczego, aby zapewnić dłuższą żywotność połączonych części, takich jak łożyska.
Bicie całkowite
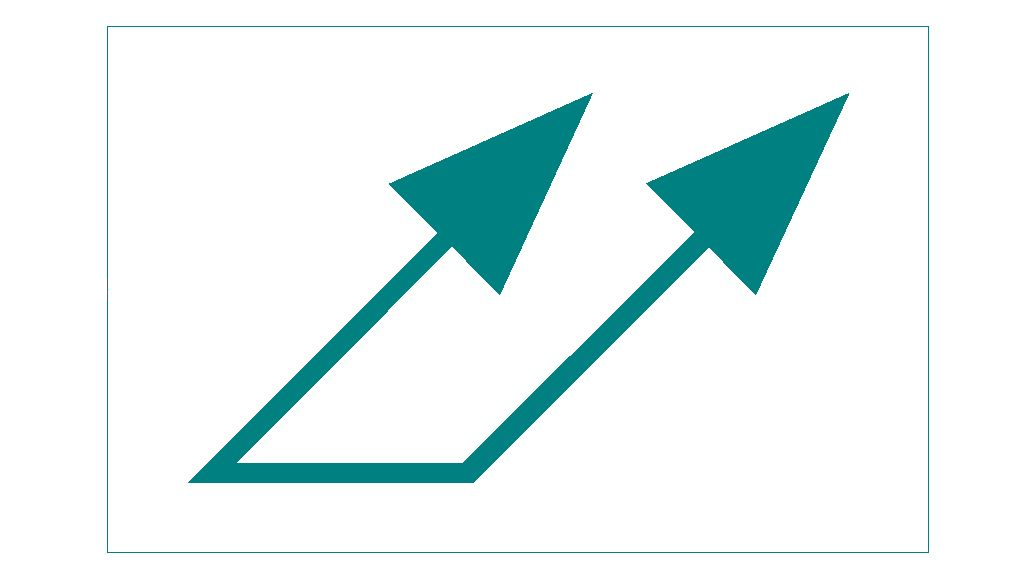
Bicie całkowite jest trójwymiarowym odpowiednikiem bicia kołowego. Kontroluje ono również formę, położenie i orientację. Ale zamiast sprawdzać poszczególne przekroje (jak w przypadku bicia kołowego), sprawdza całą powierzchnię. Tak więc, użycie bicia całkowitego daje nam ściślejszą kontrolę nad charakterystyką elementu.
Inspekcja
W każdej branży, niepowodzenie procesu produkcyjnego w spełnieniu specyfikacji projektu może być problematyczne. Podczas gdy w niektórych przypadkach życie klientów może być zagrożone, w innych przypadkach wycofanie produktu może prowadzić do ogromnych strat pieniężnych.
Nawet jeśli wyniki nie są aż tak złe, reputacja firmy w dużej mierze zależy od jakości jej produktów i usług.
GD&T standaryzuje proces kontroli poprzez wprowadzenie inspektorów na tę samą platformę co projektant. Eliminuje to wiele przeszkód. Ale GD&T to rozległy temat.
Jak widzieliśmy, istnieje wiele różnych cech geometrycznych, z których każda bardzo różni się od innej, które można kontrolować za pomocą GD&T. Ze względu na tę rozbieżność, kontrola każdej cechy wymaga specyficznej metody, narzędzia i umiejętności.
Niektóre z tych cech można zmierzyć za pomocą najprostszych narzędzi, podczas gdy inne są niemożliwe do zmierzenia bez zaawansowanego sprzętu, takiego jak maszyna współrzędnościowa (CMM).
Inspektorzy będą potrzebować wiedzy i umiejętności, aby używać różnych narzędzi pomiarowych, takich jak czujniki zegarowe, mikrometry, suwmiarki noniuszowe, płytki powierzchniowe i maszyny do pomiarów współrzędnościowych w celu zadowalającej kontroli dokładności części.
.