Gli ingegneri usano il software CAD per progettare tutte le parti e i componenti necessari per il progetto. Nel regno digitale, è facile raggiungere la perfezione. Nella vita reale, la produzione non è mai precisa al 100%.
A volte, deviazioni di pochi millimetri dalle dimensioni di base possono essere assolutamente perfette. Allo stesso tempo, due componenti che si accoppiano potrebbero richiedere una precisione estremamente elevata.
Per mantenere la deviazione prevista in un intervallo predefinito, è possibile utilizzare le tolleranze ingegneristiche. Le tolleranze dimensionali sono molto comuni ma mancano di modi per comunicare alcuni aspetti molto importanti della produzione. È qui che entra in gioco la GD&T, o dimensionamento geometrico & tolleranza.
È una forma di descrizione di dimensioni e tolleranze in un modo completamente nuovo. Usando un linguaggio comune di simboli ingegneristici, aiuta a individuare facilmente tutte le informazioni necessarie.
- Che cos’è la GD&T?
- Perché implementare GD&T?
- Assemblaggio perfetto
- Sistema comune per spiegare l’intento di progettazione
- Risparmia tempo e denaro
- Cosa considerare?
- Intelligibilità del disegno
- Tolleranze strette solo quando necessario
- Caratteristiche GD&T &Simboli
- Dimensioni nominali
- Feature control frame
- Freccia leader
- Simbolo della caratteristica geometrica
- Comparto di tolleranza delle caratteristiche
- Datums
- Modificatori di condizione del materiale
- Modificatore condizione massima di materiale
- Modificatore della condizione di minimo materiale
- A prescindere dalla dimensione della caratteristica (RFS)
- Datum e Feature Callout
- Simboli GD&T
- Controllo di forma
- Straightness
- Piattezza
- Circolarità
- Cilindricità
- Controlli di profilo
- Profilo di linea
- Profilo della superficie
- Controlli di orientamento
- Angolarità
- Parallelismo
- Perpendicolarità
- Controlli di posizione
- Concentricità
- Simmetria
- Posizione reale
- Come applicare la tolleranza di posizione GD&T a un foro
- Controlli di runout
- Routing circolare
- Routing totale
- Ispezione
Che cos’è la GD&T?
È un sistema di simboli e standard usati dagli ingegneri per fornire informazioni di produzione al team di produzione.
Le ragioni per usare il dimensionamento geometrico e la tolleranza (GD&T) sono:
- Assicura che le parti combaciano bene
- Il linguaggio universale funziona indipendentemente dalla persona con cui si lavora
- Le tolleranze danno un limite alle condizioni peggiori
- Definisce i processi di produzione e ispezione
Stanley Parker è considerato l’ingegnere che ha sviluppato il sistema GD&T nel 1938.
Prima di allora, tutte le caratteristiche utilizzavano solo gli assi X-Y per determinare la posizione di un foro, per esempio. Dare una tolleranza di posizione su quella scala significa che la posizione del foro circolare può deviare in modo rettangolare dal punto previsto.
In realtà vorremmo che la zona di tolleranza fosse un cerchio, perché questo permette una misura uniforme in tutti gli angoli, mentre un rettangolo è più lungo verso gli angoli e più corto verso i lati.
Così, quando Parker se ne rese conto, iniziò a lavorare sul nuovo concetto che fu adottato come standard di ingegneria militare negli anni ’50.
Oggi la GD&T è una parte importante dell’ingegneria, specialmente quando si creano parti che richiedono servizi di lavorazione CNC. Lo standard americano che descrive le caratteristiche è ASME Y14.5-2018 e l’equivalente europeo è ISO 1101-2017.
GD&T si concentra esclusivamente sulla geometria del prodotto. Dimensioni lineari, rugosità superficiale, filettature, ecc. non fanno parte di questo standard.
Perché implementare GD&T?
Abbiamo metodi tradizionali per indicare dimensioni e tolleranze. Allora che bisogno c’è di dimensionamento e tolleranza geometrici?
Il dimensionamento e tolleranza geometrici (GD&T) offre alcuni vantaggi unici rispetto ai metodi tradizionali. Vediamo quali sono.
Assemblaggio perfetto
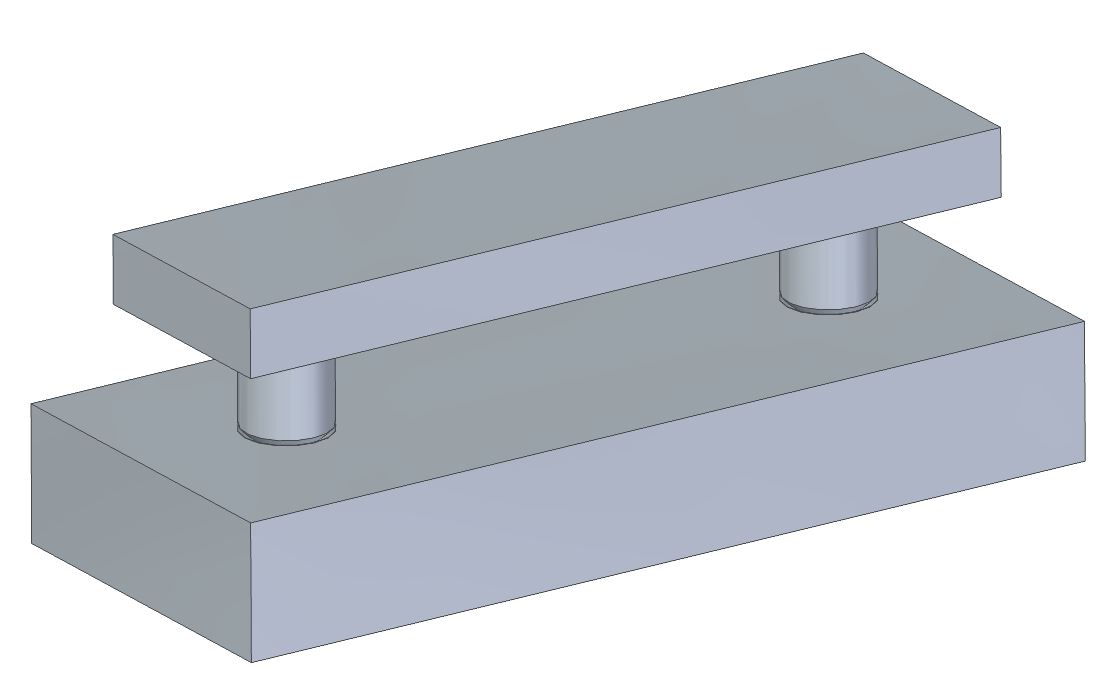
Lo svantaggio più importante dell’uso della quotatura e della tolleranza tradizionali è che denotano informazioni su parti e caratteristiche individuali. Non garantiscono quanto bene le nostre parti si adatteranno e funzioneranno a livello di assemblaggio.
Questo è importante perché molte parti non sono utili da sole. Consideriamo l’esempio di una biella. Da sola, non ci fornisce alcun beneficio. Ma quando la colleghiamo all’albero motore e al pistone, diventa un po’ più utile, perché converte il moto lineare del pistone in moto rotatorio dell’albero motore.
Quando questo gruppo diventa parte di un gruppo più grande come un motore diesel, può finire come parte di un generatore che ci fornisce molti usi.
Quindi, è fondamentale che le nostre parti si accoppino bene tra loro. Questo è il motivo per cui abbiamo bisogno di GD&T. Usandolo, possiamo essere sicuri al 100% che le nostre parti si accoppieranno e funzioneranno esattamente come necessario.
Sistema comune per spiegare l’intento di progettazione
GD&T fornisce anche al progettista una piattaforma per trasmettere il suo intento di progettazione a tutti i reparti interessati. Questi includono:
- Fabbricazione
- Ispezione
- Futuri designer nel dipartimento di design che prenderanno il lavoro se il team di design iniziale non è disponibile
Le definizioni, il vocabolario e le regole sono semplici e universalmente comprensibili. Questo rende i simboli facili da tradurre per ogni ingegnere e un ottimo modo di trasmettere l’intenzione del progettista.
Risparmia tempo e denaro
Questo è il vantaggio più importante dell’uso di GD&T. L’uso di questo sistema riduce gli sprechi perché riduce il numero di cicli di progettazione-fabbricazione-collaudo.
Questo perché i pezzi prodotti si adattano bene al primo tentativo e, di conseguenza, il numero di scarti sarà basso. L’uso di un linguaggio comune riduce anche lo sforzo necessario per l’ispezione.
Ottieni il tuo preventivo di produzione in pochi secondi
-
Preventivo in pochi secondi
-
Tempi brevi
-
Consegna da Fractory
Ottieni preventivo
Cosa considerare?
La quotatura e tolleranza geometrica è un sistema più potente rispetto alle tolleranze tradizionali. Ma funziona solo se tutti i dipartimenti (progettazione, ingegneria, produzione) sono ben preparati a leggere e interpretare le informazioni.
Pertanto, mentre si creano i disegni di ingegneria e si tollerano varie caratteristiche dei pezzi, è importante seguire le linee guida/convenzioni raccomandate a beneficio di tutti coloro che interagiranno con il disegno in qualsiasi fase dello sviluppo del prodotto.
Osservarle assicura che il disegno sia standardizzato e che tutti siano sulla stessa pagina quando si tratta delle specifiche del disegno. Alcune di queste buone pratiche sono le seguenti.
Intelligibilità del disegno
Questa è probabilmente la qualità più importante di un disegno. L’intelligibilità si riferisce alla chiarezza con cui le caratteristiche del pezzo sono disegnate e le tolleranze sono mostrate nel disegno. Alcuni modi per migliorare l’intelligibilità di un disegno sono:
- Segnare profili reali per tutte le caratteristiche del pezzo.
- Etichettare le dimensioni e le tolleranze fuori dal disegno (non in alto). Usare efficacemente gli spazi bianchi.
- La direzione di lettura deve essere costante. Un lettore dovrebbe essere in grado di leggere tutte le dimensioni tenendo il disegno in posizione verticale.
- Spaziate le dimensioni delle caratteristiche di parti parallele.
- Spiegate brevemente la parte e la sua funzione.
- Specificare gli angoli solo quando non sono angoli retti (90°).
Tolleranze strette solo quando necessario
A meno che l’adattamento/la funzione del pezzo non lo richieda, le tolleranze devono essere tenute il più possibile libere. Questo riduce il costo di fabbricazione e il tempo di consegna. Si raccomanda di lasciare la scelta del metodo di fabbricazione ai macchinisti.
Il progettista deve anche menzionare la tolleranza generale per un disegno. Questa agisce come tolleranza standard per tutte le caratteristiche della parte. Per le caratteristiche del pezzo con un limite di tolleranza diverso, il progettista deve menzionarle nelle posizioni appropriate.
Questi limiti di tolleranza specifici prevarranno sulle tolleranze generali. Quando si specificano i limiti di tolleranza speciali, preferire le caratteristiche funzionali ad altre caratteristiche.
Caratteristiche GD&T &Simboli
Il linguaggio GD&T è in grado di definire praticamente tutte le qualità che sono necessarie per assicurare un assemblaggio perfetto.
Il sistema utilizza una serie di simboli per questo scopo. Per usare correttamente questi simboli ingegneristici sui disegni, dobbiamo prima conoscere alcuni elementi di base di questo sistema.
Possiamo iniziare con le varie definizioni, terminologie e regole prima di arrivare ai simboli GD&T.
Dimensioni nominali
Una dimensione nominale è la dimensione caratteristica del vero profilo. È la dimensione esatta che vorremmo ottenere idealmente. Le specificità della caratteristica come la dimensione, l’orientamento, la posizione da un punto di riferimento hanno una dimensione nominale che i macchinisti mirano a raggiungere.
Su un disegno, sono mostrate all’interno di una scatola. Può essere mostrato come un numero o da uno standard popolare come ASME.
Feature control frame
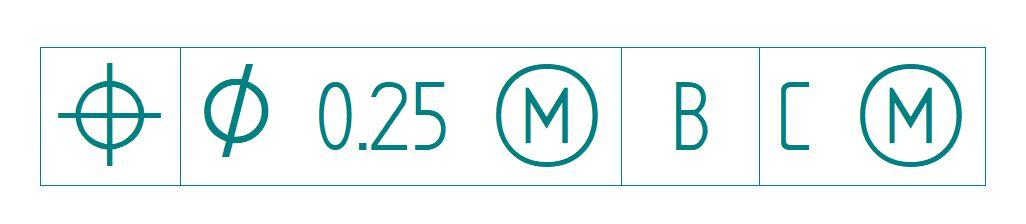
Questo frame contiene informazioni sulle specifiche del pezzo. Contiene vari compartimenti dove ogni compartimento definisce un attributo specifico della caratteristica del pezzo. In uno sguardo, il quadro di controllo della caratteristica trasmette le informazioni necessarie per la lavorazione e l’ispezione.
Il quadro di controllo della caratteristica può essere diviso in 4 parti principali come segue.
Freccia leader
Questa freccia segna la caratteristica del pezzo sotto controllo. Se conduce a una superficie, la superficie è sotto controllo geometrico. Se segna una quota diametrale, allora GD&T controlla l’asse. Questa freccia può non essere presente in alcuni casi.
Simbolo della caratteristica geometrica
Il primo scomparto (partendo da sinistra) contiene il simbolo della caratteristica geometrica. È qui che si specifica la caratteristica geometrica. In totale, ci sono 14 tipi di tolleranze geometriche in base al numero di simboli, e 15 se classificate.
I diversi tipi di caratteristiche geometriche sono il controllo di forma, il controllo di profilo, il controllo di posizione, il controllo di orientamento, ecc. Ci immergeremo più a fondo in ogni categoria più avanti.
Comparto di tolleranza delle caratteristiche
Il 2° blocco contiene un massimo di 3 (a volte 2 o 1) simboli diversi.
Il primo simbolo mostra il tipo di zona di tolleranza. Un simbolo di diametro (⌀) indica una zona diametrale (zona di tolleranza cilindrica). Per specificare una zona sferica, il simbolo è la lettera ‘S’ seguita dal simbolo del diametro (⌀). In assenza di un simbolo, si assume una zona larga totale.
Il secondo simbolo del 2° blocco dà il valore della zona di tolleranza in mm. Questo valore deve essere sempre presente nel 2° blocco.
Il terzo simbolo in questo blocco è il modificatore di tolleranza. Questo modificatore di materiale è presente solo quando la caratteristica ha una dimensione, per esempio un foro. Esempi di modificatori di materiale sono MMC (Maximum material condition) e LMC (Least material condition). Maggiori informazioni sui vari modificatori disponibili saranno discusse più avanti nell’articolo.
Datums
Il terzo blocco fornisce informazioni sui dati con un minimo di 1 e un massimo di 3 dati. Nel caso di 3 datum, si parla di datum primari, secondari e terziari, ognuno dei quali viene mostrato racchiuso in una casella diversa (l’immagine sopra ne ha 2, per esempio). Questo blocco può anche contenere un modificatore di materiale.
Tutte le informazioni di cui sopra ci aiutano a capire come leggere un quadro di controllo delle feature. Per capire meglio come la tolleranza può essere regolata usando i modificatori di condizione del materiale, dobbiamo avere familiarità con le diverse opzioni.
Modificatori di condizione del materiale
I modificatori di condizione del materiale trasmettono l’intento quando la tolleranza si applica ad una caratteristica ad una specifica dimensione della caratteristica. Ogni volta che diamo delle tolleranze a qualsiasi caratteristica, si stabiliscono due condizioni materiali
- Condizione materiale massima
- Condizione materiale minima
Consideriamo un albero di diametro 100 mm. Durante la fabbricazione, se gli diamo una tolleranza di ±0,2 mm, allora a 100,2 mm, l’albero conterrà la massima quantità di materiale. Questo è ciò che intendiamo per condizione materiale massima.
D’altra parte, lo stesso albero, quando è fabbricato con un diametro di 99,8 mm, conterrà la quantità minima di materiale. Questi limiti sono chiamati condizioni di materiale.
Le tolleranze geometriche possono essere applicate ad una caratteristica in 3 modi diversi. Questi sono i seguenti:
- Condizione massima di materiale
- Condizione minima di materiale
- Indifferentemente dalla dimensione della feature
Modificatore condizione massima di materiale
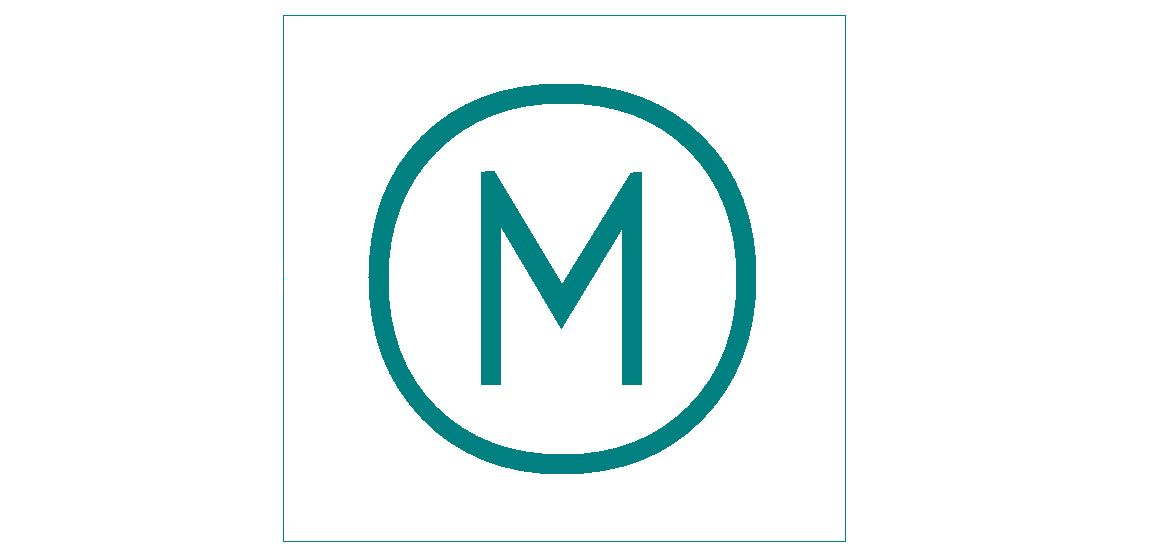
Presentiamo questa condizione con una “M” cerchiata dopo il valore della tolleranza nel vano di controllo della feature. La caratteristica contiene il materiale massimo a questa dimensione della caratteristica.
Per i FOS esterni (Feature Of Size), come il diametro di un albero, MMC rappresenta la dimensione massima. Per FOS interni, come il diametro di un foro, MMC rappresenta la dimensione più piccola possibile entro i limiti di tolleranza indicati, perché un foro più piccolo significa che rimarrà più materiale.
Quando abbiamo bisogno di applicare la tolleranza geometrica alla condizione di massimo materiale, menzioniamo questa condizione nel frame di controllo della feature.
Modificatore della condizione di minimo materiale
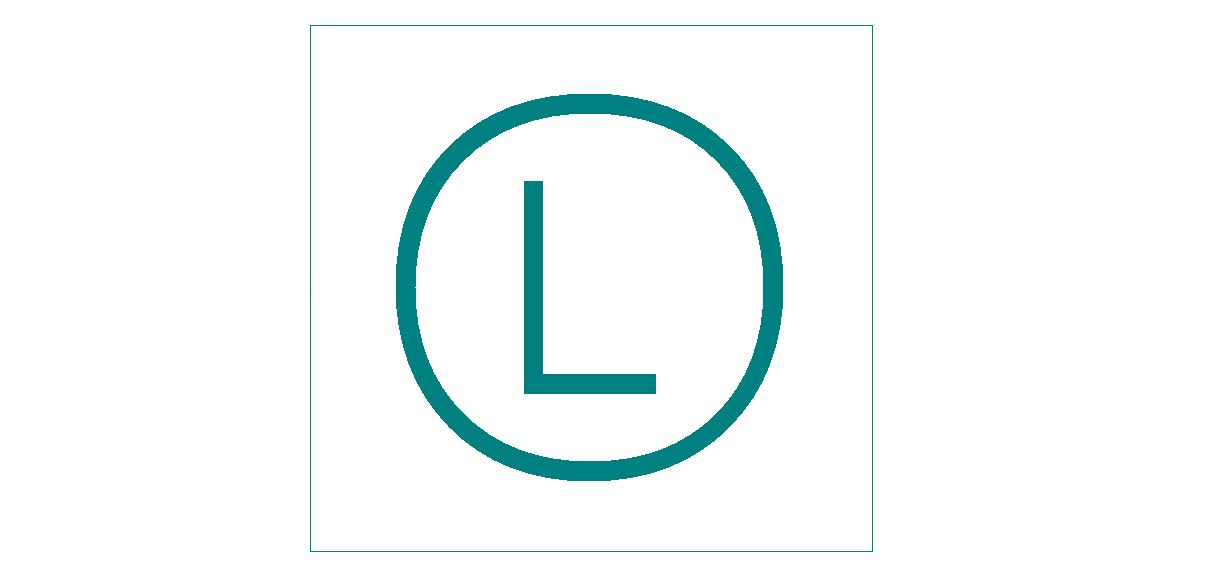
LMC è la condizione dove il materiale contiene la minor quantità di materiale.
Per i FOS esterni, sarà la dimensione più piccola possibile entro i limiti indicati. E per i FOS interni, sarà la dimensione più grande possibile.
Presentiamo questo modificatore con la lettera “L” in un cerchio. Questa caratteristica rimuove il materiale in eccesso e quindi il peso. Per applicare le tolleranze geometriche a questa condizione, usiamo il suo simbolo nel quadro di controllo della caratteristica.
A prescindere dalla dimensione della caratteristica (RFS)
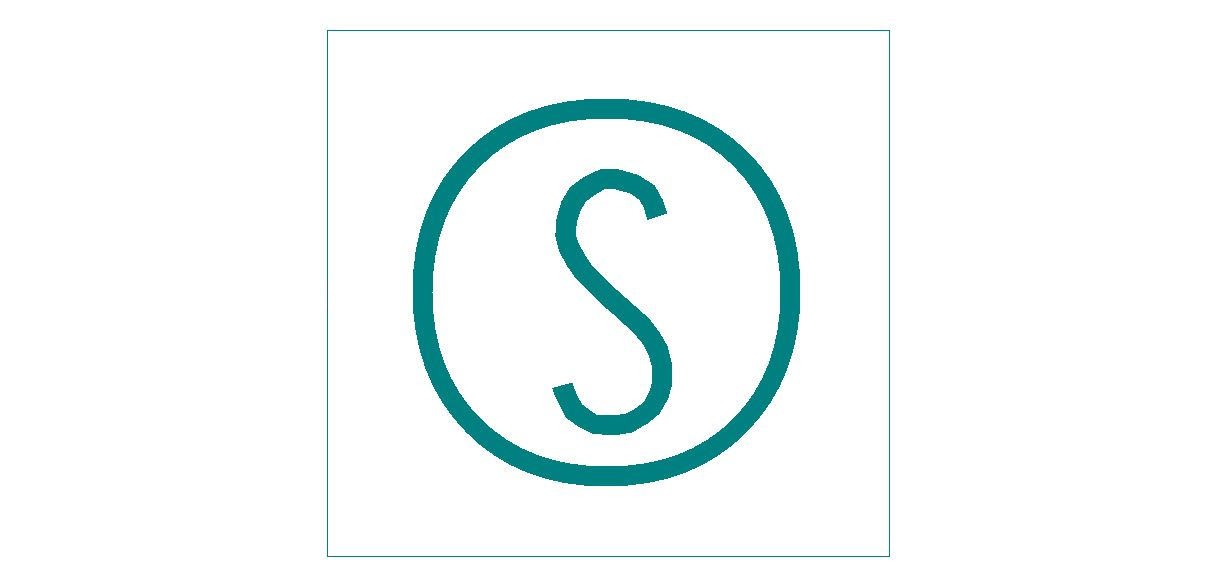
Quando le tolleranze geometriche date sono applicate a qualsiasi incremento di dimensione di FOS, lo indichiamo con RFS. Il simbolo per RFS era la lettera “S” racchiusa in un cerchio, ma non è più necessario perché RFS è considerata la condizione predefinita ora, e non ha bisogno di un simbolo.
Datum e Feature Callout
I datum sono punti di riferimento per misurare le tolleranze dimensionali. Può essere un punto, una linea o un piano. Con l’aiuto di un datum, stabiliamo dei Datum Reference Frames (DRF). Il DRF è fondamentalmente un sistema di coordinate 3D che ci aiuta a definire le posizioni di tutte le altre caratteristiche rispetto al DRF.
Ci sono 6 gradi di libertà (3 traslazionali e 3 rotazionali) che dobbiamo controllare per fabbricare e controllare efficacemente i pezzi. Usiamo il DRF per stabilire questi gradi di libertà.
Le caratteristiche del datum sono le caratteristiche effettive della parte come i fori e le scanalature. Possono mostrare variazioni dalle posizioni desiderate.
Tra tutte le caratteristiche di origine, diamo la massima preferenza a quelle che si accoppiano con altre parti nell’assemblaggio. Possiamo menzionare più di un dato nel nostro quadro di controllo delle caratteristiche. Secondo la sequenza dei DRF nel quadro di controllo della caratteristica, le parti sono accoppiate ai DRF in ordine decrescente di importanza.
Simboli GD&T
Sono disponibili fino a 14 simboli GD e T per rappresentare diverse caratteristiche geometriche delle caratteristiche. Questi simboli ci aiutano a specificare queste caratteristiche come requisiti per il prodotto finale.
Mettiamo questi simboli nel primo scomparto del quadro di controllo della caratteristica. Esamineremo questi tipi di controllo di tolleranza.
Controllo di forma
Come suggerisce il nome, il controllo di forma si riferisce alla forma finale della caratteristica. Definiamo i controlli di forma per limitare la deviazione della tolleranza geometrica dalla sua forma ideale. Alcune caratteristiche di controllo di forma popolari sono le seguenti.
Straightness
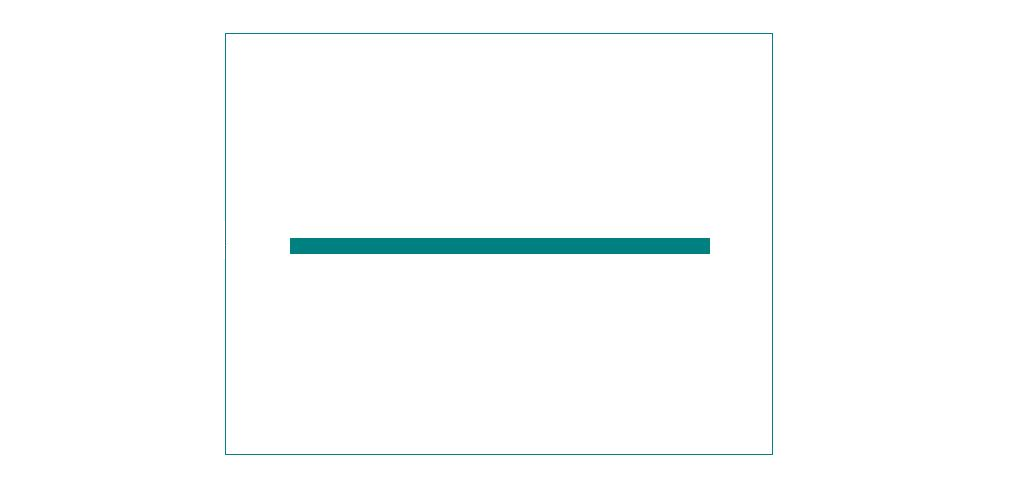
Per indicare la caratteristica di rettilineità di una caratteristica (come un asse o una superficie), usiamo il suo simbolo (una linea orizzontale dritta) nel primo scomparto.
Surface straightness può essere applicata a superfici piane come un lato di un blocco o superfici curve come un lato di un cilindro lungo la direzione dell’asse. Definisce la variazione ammissibile di una linea (2 dimensioni) sulla superficie entro una tolleranza specificata.
La rettilineità assiale si applica solitamente all’asse di un albero o di un foro, per esempio. Go/no go gauge è lo strumento d’ispezione usato nel processo per assicurarsi che il pezzo sia conforme alle richieste.
Piattezza
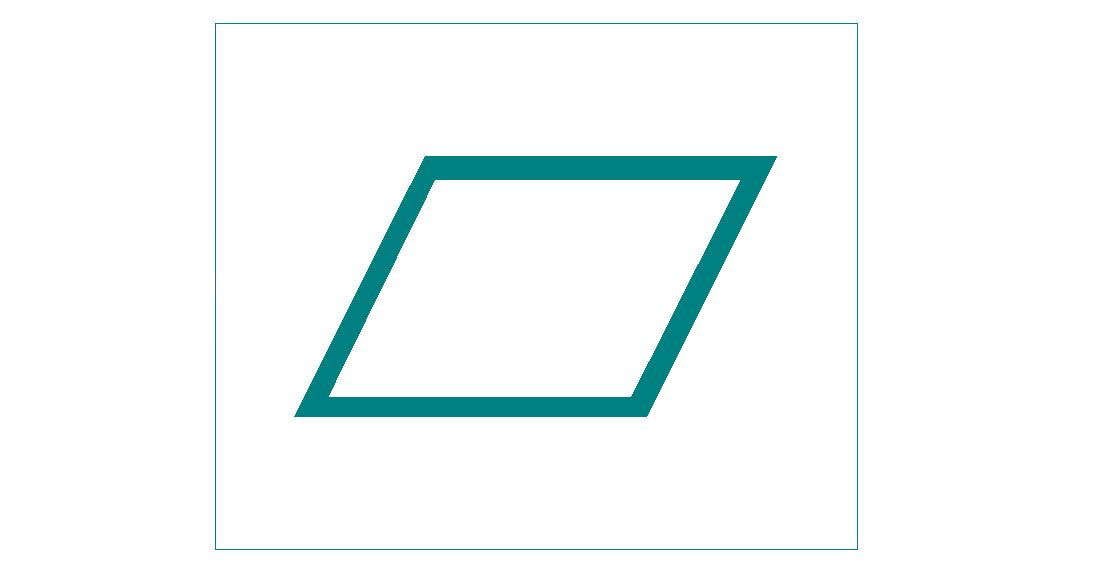
Usiamo questa caratteristica per caratteristiche come la faccia di un pezzo. Il simbolo della planarità è un parallelogramma inclinato a destra. La differenza tra il punto più alto e quello più basso di una superficie piana è la sua planarità.
Il simbolo della planarità non richiede alcun dato, poiché mostra solo un intervallo di tolleranza entro il quale l’intera superficie di un pezzo deve essere conforme in 3 dimensioni.
Un misuratore di altezza è usato per controllare i risultati. Tocca diverse aree della superficie per determinare che tutti i punti sono all’interno della zona di tolleranza.
Circolarità
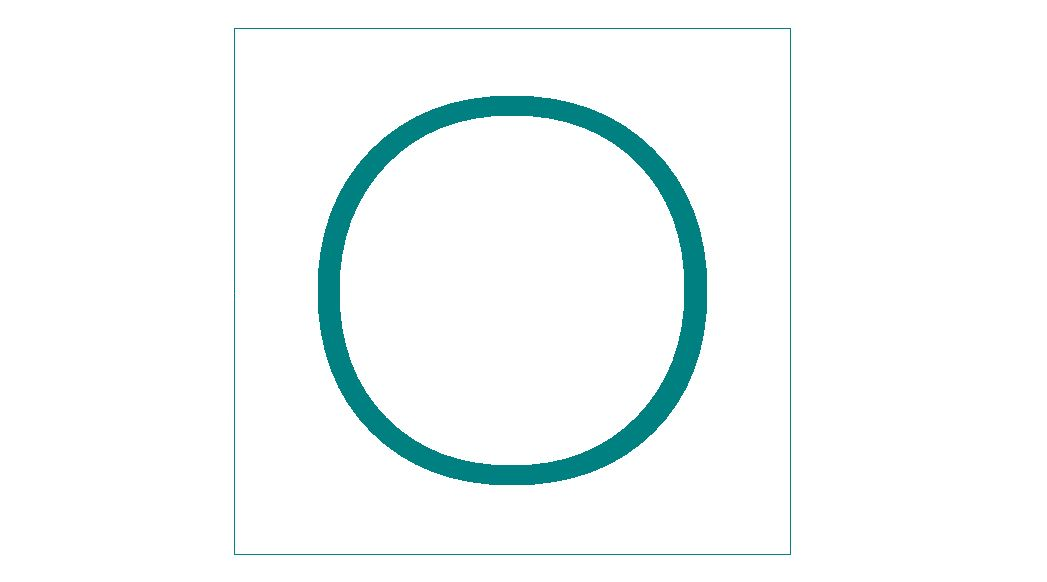
La circolarità di una caratteristica mostra quanto la circonferenza del pezzo deve essere vicina ad un cerchio perfetto. Utilizza 2 cerchi concentrici su un piano perpendicolare all’asse del pezzo per definire l’intervallo di tolleranza adatto in 2D. Ogni punto delle misure finali deve cadere tra i cerchi.
Questa caratteristica è mostrata come un cerchio nel primo scomparto del quadro di controllo della caratteristica.
Cilindricità
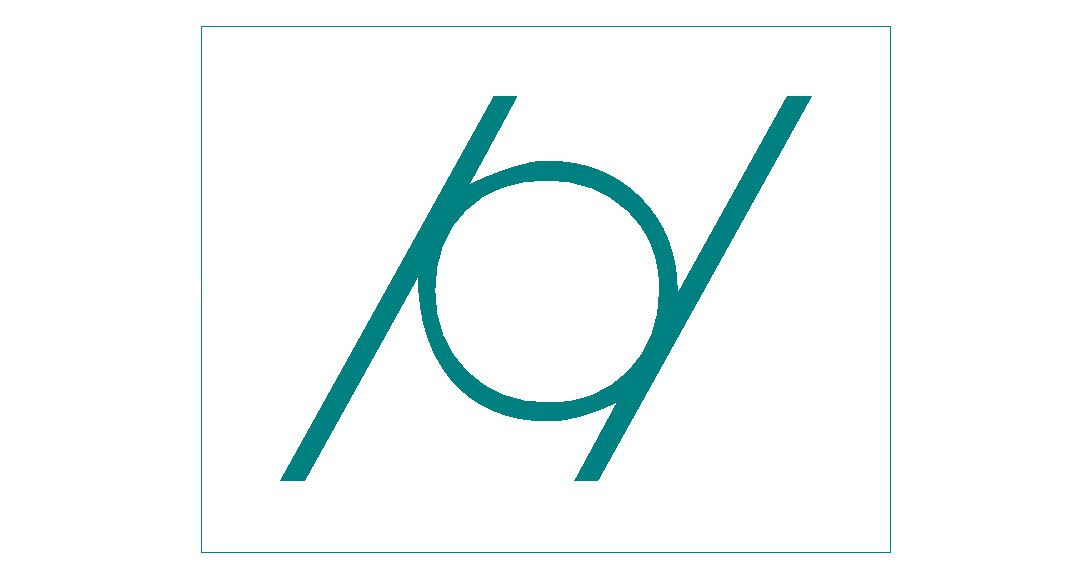
La cilindricità è fondamentalmente la circolarità in 3D, che significa che corre lungo tutta la lunghezza del pezzo.
Questa caratteristica descrive anche altre caratteristiche cilindriche come la sua conicità, rettilineità e rotondità. Ecco perché questa caratteristica è anche costosa da ispezionare.
Controlli di profilo
Utilizziamo i controlli di profilo per controllare la zona di tolleranza 3D intorno alla caratteristica. Questa caratteristica ci aiuta a dare limiti di tolleranza a curve e forme avanzate.
Una caratteristica che va bene per curve avanzate deve naturalmente funzionare bene anche con curve più semplici. Questo rende i controlli di profilo estremamente versatili. Questo è il motivo per cui alcuni designer raccomandano di abbandonare tutti gli altri controlli e di lavorare solo con i controlli di profilo.
Questi controlli formano un limite di tolleranza intorno alla curva avanzata imitandola su entrambi i lati. Impediscono quindi a qualsiasi punto della curva caratteristica di andare al di fuori del limite di tolleranza. I controlli di profilo sono di due tipi.
Profilo di linea
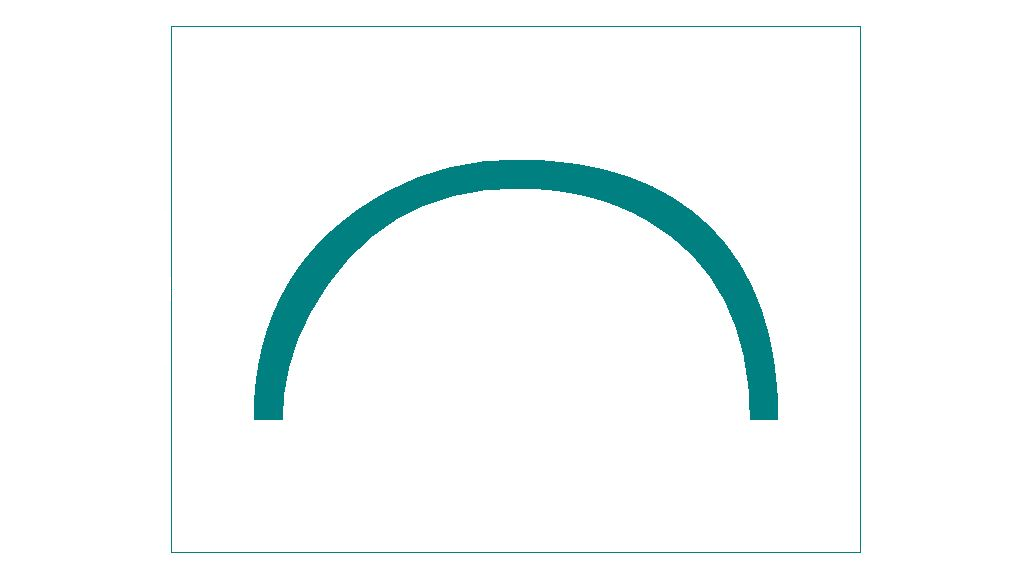
Il profilo di linea stabilisce una zona di tolleranza intorno a varie sezioni trasversali 2D della parte. Controlla i singoli elementi di linea di una caratteristica del pezzo.
Il controllo del profilo di linea traccia la curva ideale ai limiti di tolleranza su entrambi i lati. Tutti i punti sulla curva della parte devono trovarsi entro questi limiti.
Profilo della superficie
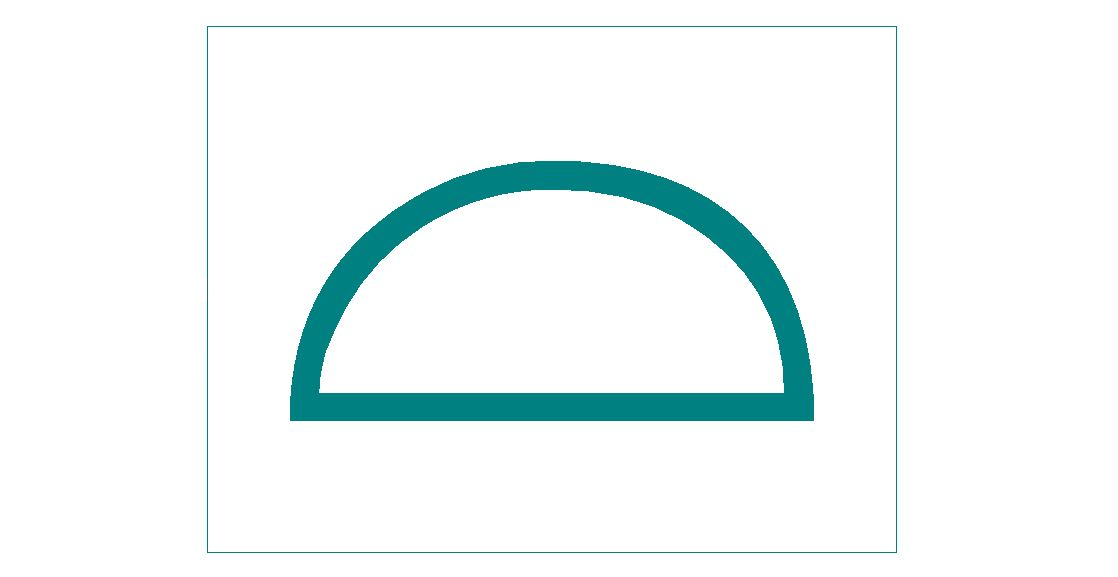
Il controllo del profilo della superficie è più popolare rispetto al controllo della linea. Invece di una zona di tolleranza bidimensionale, il controllo del profilo di superficie crea una zona 3D intorno ad una superficie.
Tutti i punti sulla superficie della tavola devono stare all’interno dei due piani virtuali.
Controlli di orientamento
La tolleranza di orientamento controlla l’orientamento di una caratteristica rispetto ad un dato definito. Ci sono tre tipi di controlli di orientamento in GD&T.
Angolarità
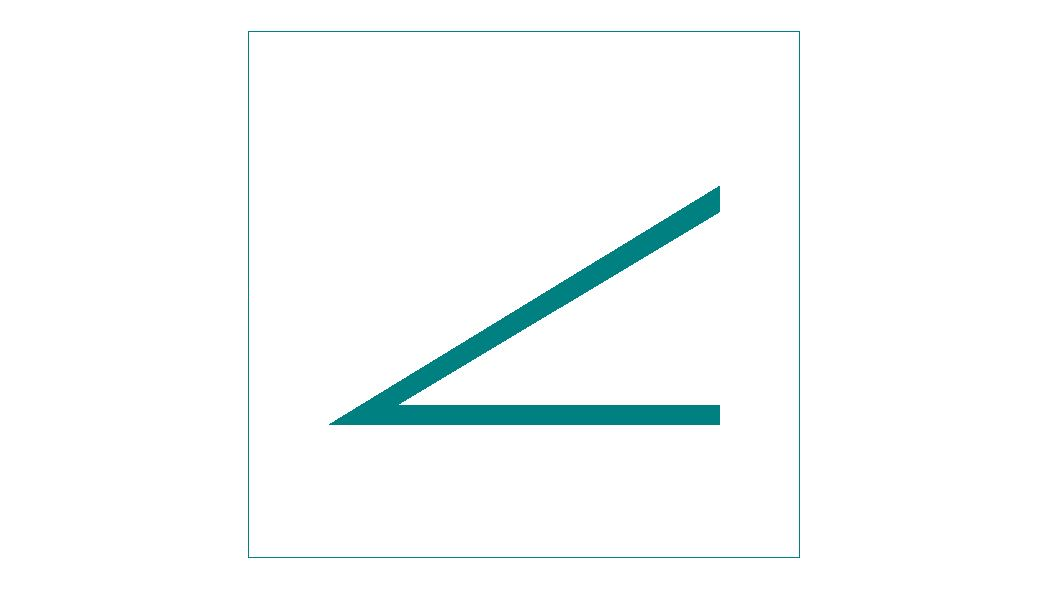
Il controllo di angolarità tiene sotto controllo l’angolo di una caratteristica rispetto al dato. Possiamo usarlo per controllare una linea 2D, ma è più popolare per tenere sotto controllo le superfici (3D).
Questo tipo di controllo stretto mantiene l’angolo e la planarità della superficie sotto controllo ed è raccomandato per le caratteristiche della parte che si accoppiano con altre parti attraverso la superficie angolata.
È importante notare che la caratteristica di angolarità controlla l’angolo indirettamente, non essendo essenzialmente la stessa di una tolleranza angolare (ad esempio +/- 2°). Piuttosto, l’angolo necessario è il risultato del rispetto dei requisiti dimensionali stabiliti da questo controllo.
Parallelismo
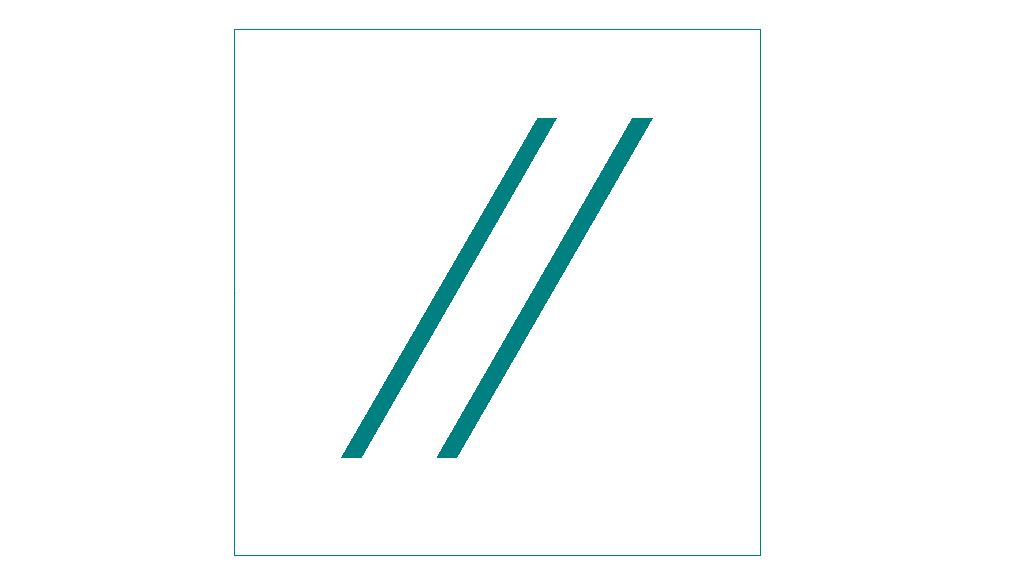
Il parallelismo è una forma raffinata di angolarità. Qui, il dato è la superficie che dobbiamo imitare e l’angolo è fissato a 0°. Ci sono 2 tipi di parallelismo: il parallelismo di superficie e il parallelismo di asse.
Possiamo scegliere un asse o una superficie come riferimento. Questo diventa il nostro dato e lo referenziamo nel 3° blocco del quadro di controllo della caratteristica come dato per la caratteristica.
Similmente all’angolarità, non controlla l’angolo reale, ma lo assicura fissando i requisiti sotto forma di una zona di tolleranza.
Perpendicolarità
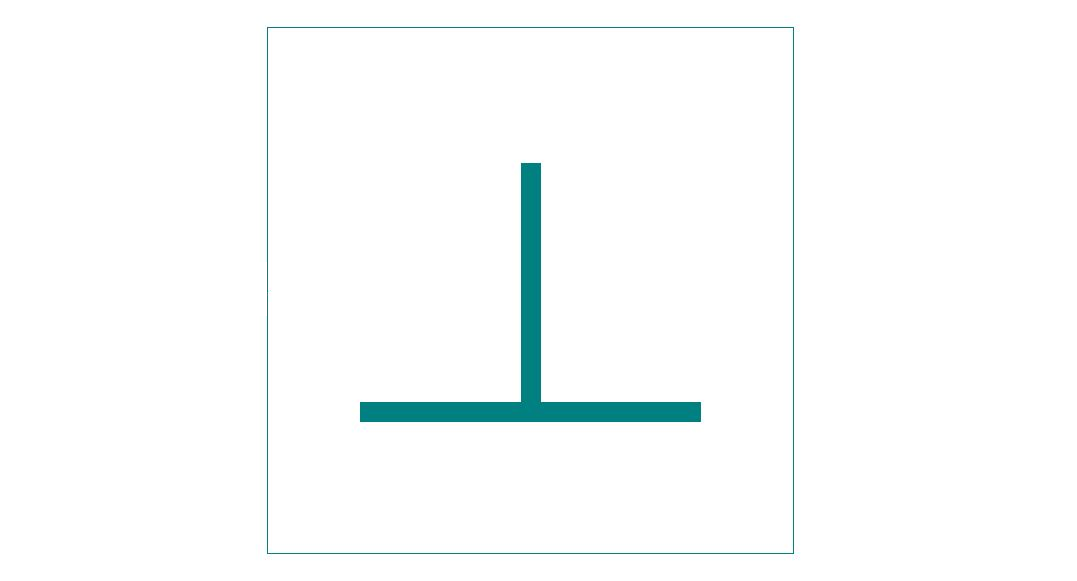
La perpendicolarità è anche una forma specifica di angolarità dove l’angolo è fissato a 90°. È un controllo difficile perché può significare due tipi di requisiti molto diversi.
C’è la perpendicolarità di superficie (Simbolo:⟂), e poi c’è la perpendicolarità dell’asse (Simboli: ⟂+⌀).
La perpendicolarità della superficie specifica che una superficie o linea deve essere perpendicolare a una superficie o linea di riferimento, proprio come l’angolarità. Due piani/linee virtuali sono assunti intorno alla superficie di destinazione per il controllo.
La perpendicolarità dell’asse specifica quanto un asse deve essere perpendicolare al dato menzionato. Questo è fatto erigendo un cilindro virtuale intorno all’asse di destinazione su una superficie esattamente parallela alla superficie di riferimento.
Controlli di posizione
Il controllo di tolleranza di posizione è usato per un controllo stretto sulla posizione di una caratteristica rispetto a un dato. Ci sono quattro tipi principali di controlli di posizione.
Concentricità
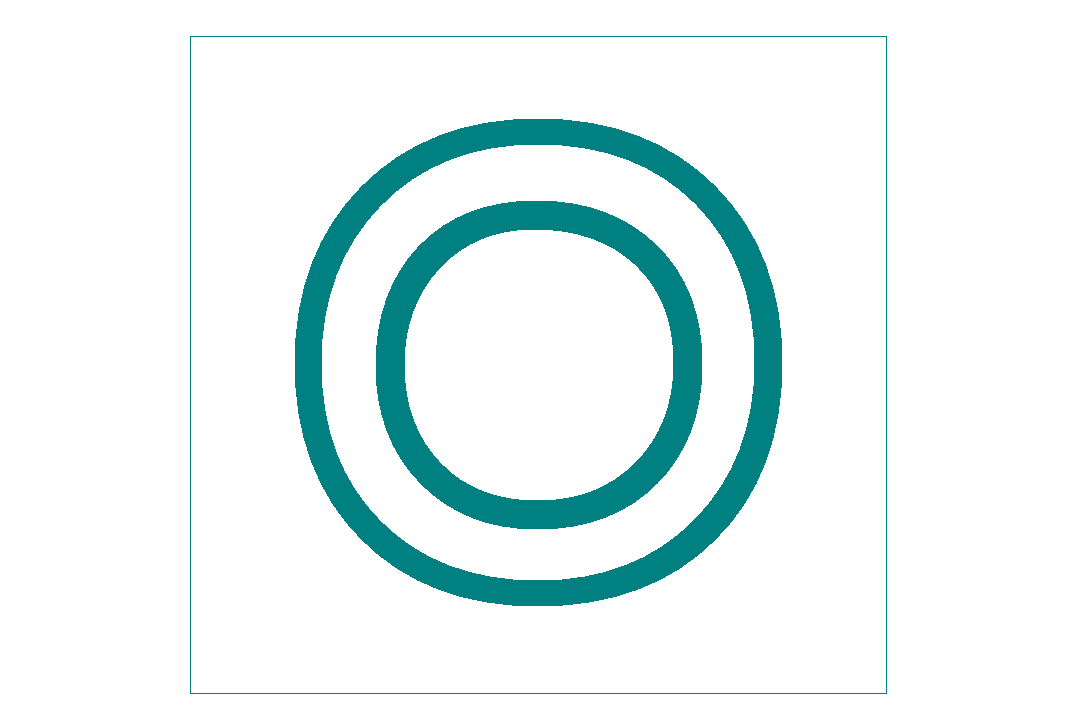
Concentricità, conosciuta anche come coassialità (anche se non è esattamente la stessa cosa), il controllo mantiene la concentricità di elementi circolari e cilindrici.
Fissa l’asse di una parte all’asse di un elemento di riferimento (asse di origine). Gli assi di entrambe le parti sono determinati per essere nei punti mediani delle parti.
Questo controllo può portare ad una certa confusione perché gli assi derivano da misure esterne, piuttosto che dal loro reale posizionamento.
La coassialità crea una zona di tolleranza 3D basata su misure di superficie in cui la parte deve trovarsi.
Simmetria
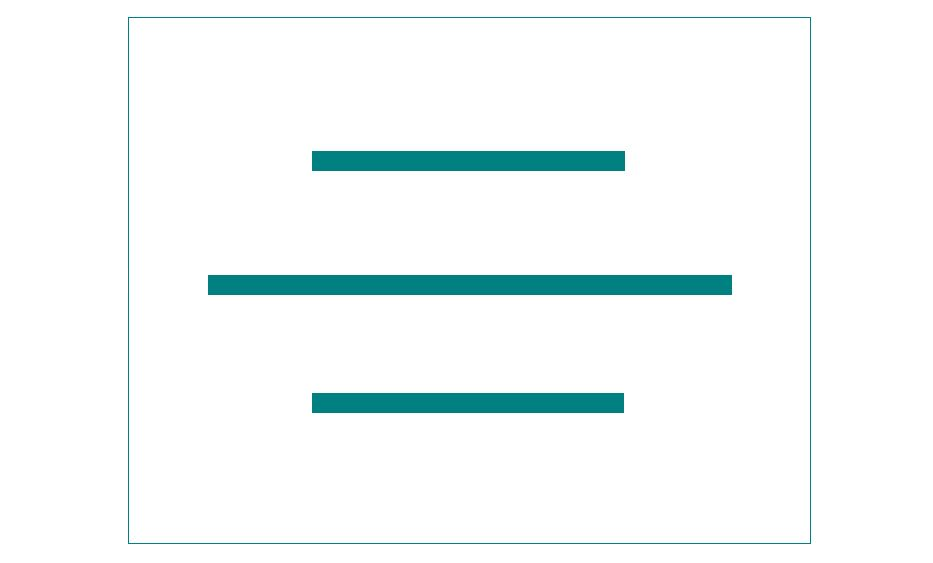
Il callout di simmetria stabilisce un piano centrale attorno al quale le due parti della feature sono poste ad uguale distanza. Il punto medio dei due punti su entrambi i lati deve trovarsi all’interno della zona di tolleranza impostata intorno al piano centrale.
Il callout di simmetria non è molto comune. Ha usi molto limitati ed è anche difficile da ispezionare. Abbiamo bisogno di una CMM per ispezionare la simmetria finale.
Posizione reale
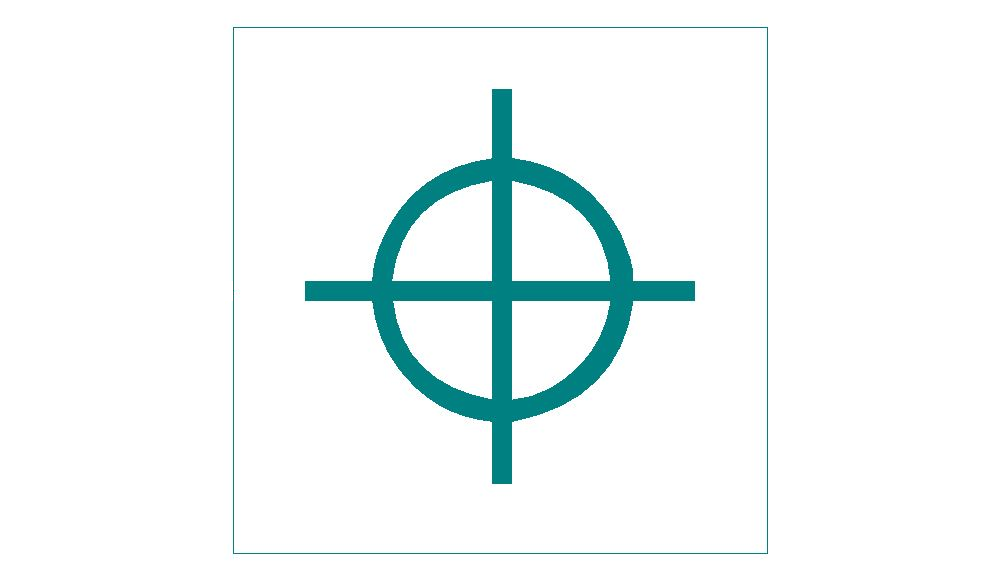
La posizione reale (popolarmente conosciuta come posizione) è un callout molto utile e trova ampio uso in GD&T.
La posizione definisce quanto la posizione reale di una caratteristica può variare dalla sua posizione prevista. La definizione include il piano di riferimento a cui la misura si riferisce.
Spesso include un segno diametrale (⌀) per evidenziare che la zona di tolleranza è un cerchio, piuttosto che solo gli assi X e Y (di cui abbiamo parlato all’inizio dell’articolo come la ragione per creare GD&T in primo luogo).
Qui c’è un bel video che mostra come usare le tolleranze su un disegno, usando la posizione reale:
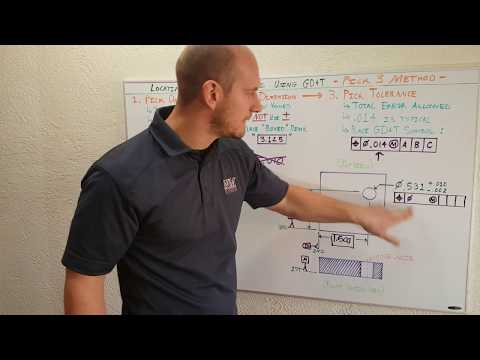
Come applicare la tolleranza di posizione GD&T a un foro
Controlli di runout
Utilizziamo i controlli di runout per misurare la deviazione di una caratteristica della parte dalla sua posizione assegnata rispetto a un dato stabilito. Questo controllo è usato per elementi circolari. Misura essenzialmente la sua oscillazione ruotando l’elemento intorno all’origine fissa.
Ci sono due tipi di controllo di runout.
Routing circolare

Il runout circolare lavora in due dimensioni per controllare la forma, la posizione e l’orientamento di vari elementi. Questo callout 2D ha bisogno che gli assegniamo un asse di riferimento per controllare queste caratteristiche.
In gergo GD&T, il runout circolare è comunemente conosciuto come runout. Il runout misura la deviazione negli elementi di superficie per rotazione.
Si intende che l’albero, per esempio, viene ruotato dal suo asse di riferimento e l’elemento caratterizzato viene misurato per la tolleranza. In sostanza, limita la vibrazione di un albero di lavoro per assicurare una vita più lunga alle parti collegate come i cuscinetti.
Routing totale
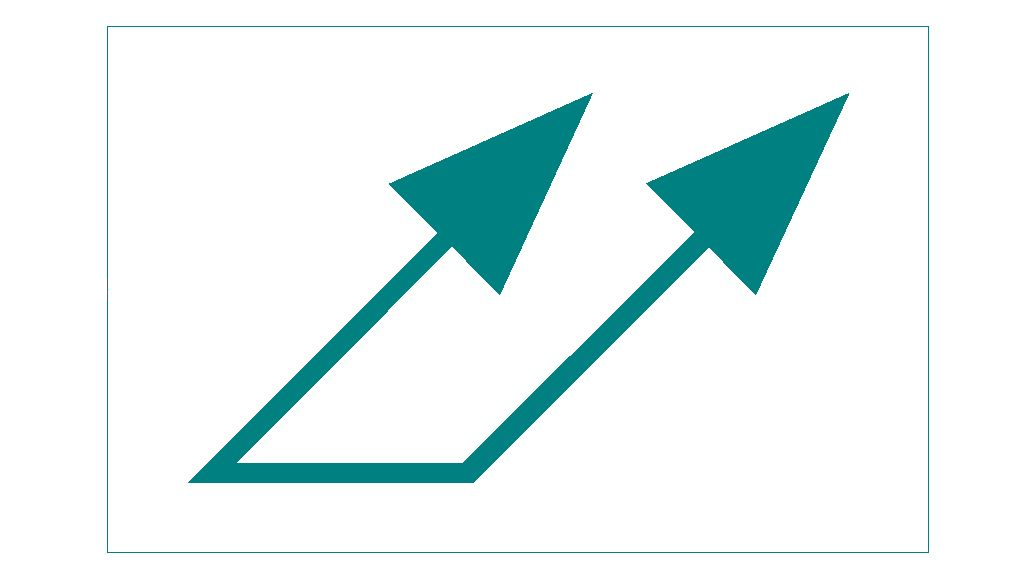
Il runout totale è la controparte 3D del runout circolare. Controlla anche la forma, la posizione e l’orientamento. Ma invece di controllare le singole sezioni trasversali (come nel runout circolare), controlla l’intera superficie. Quindi, l’uso del runout totale ci dà un controllo più severo sulle caratteristiche dell’elemento.
Ispezione
In tutte le industrie, il fallimento del processo di produzione per soddisfare le specifiche di progettazione può essere problematico. Mentre in alcuni casi, la vita dei clienti può essere a rischio, in altri casi, un richiamo del prodotto potrebbe portare a enormi perdite monetarie.
Anche se i risultati non sono così negativi, la reputazione di un’azienda si basa molto sulla qualità dei suoi prodotti e servizi.
GD&T standardizza il processo di ispezione portando gli ispettori sulla stessa piattaforma del designer. Questo elimina molti ostacoli. Ma GD&T è un argomento vasto.
Come abbiamo visto, ci sono diverse caratteristiche geometriche, ognuna molto diversa dall’altra, che possono essere controllate con GD&T. A causa di questa disparità, il controllo di ogni caratteristica richiede un metodo, uno strumento e un’abilità specifici.
Alcune di queste caratteristiche possono essere misurate con il più semplice degli strumenti mentre altre sono impossibili da misurare senza attrezzature avanzate come una macchina di misura a coordinate (CMM).
Gli ispettori dovranno avere la conoscenza e l’abilità di usare vari strumenti di misurazione come comparatori, micrometri, calibri di verniero, piastre di superficie e macchine di misura a coordinate per controllare la precisione dei pezzi in modo soddisfacente.
.