Engineer は CAD ソフトウェアを使ってプロジェクトに必要なすべての部品やコンポーネントを設計しています。 デジタルの世界では、完璧を期すのは簡単です。
時には、基本寸法から数ミリのずれがあっても、まったく問題ないこともあります。 同時に、2つの嵌合部品が極めて高い精度を必要とすることもあります。
予想される偏差をあらかじめ定義された範囲に保つために、工学公差を使用することが可能です。 寸法公差は非常に一般的ですが、製造の非常に重要な側面を伝える方法が欠けています。 そこで GD&T (幾何学的寸法公差) が登場します。
これはまったく新しい方法で寸法と公差を記述する形式です。 エンジニアリング シンボルの共通言語を使用することで、すべての必要な情報を簡単に特定できます。
- GD&T とは何ですか。
- Why Implement GD&T?
- 完璧なアセンブリ
- 設計意図を説明するための共通システム
- Saves time and money
- What to Consideration ?
- Intelligibility of the drawing
- Tight tolerances only when necessary
- GD&T Features & Symbols
- フィーチャーコントロールフレーム
- Leader arrow
- Geometric characteristic symbol
- Feature tolerance compartment
- Datums
- Material Condition Modifiers
- Maximum material condition modifier
- Least material condition modifier
- Regardless of Feature Size (RFS)
- データムとフィーチャー コールアウト
- GD&T Symbols
- 形状制御
- 真直度
- Flatness
- 円形度
- Cylindricity
- プロファイル制御
- Line Profile
- Surface Profile
- 方向制御
- Angularity
- Parallelism
- Perpendicularity
- 位置制御
- Concentricity
- Symmetry
- True position
- How to Apply GD&T Position Tolerance to a Hole
- Runout controls
- 円形振れ
- 総振れ
- 検査
GD&T とは何ですか。
Geometric Dimensioning and Tolerancing (GD&T) を使用する理由としては、以下のようなものがあります。
- 嵌合する部品がうまく合うようにする
- 世界共通言語は、誰と作業していても機能する
- 公差は、最悪の場合の条件に限界を与える
- 生産および検査プロセスを定義する
Stanley Parkerは、1938年のGD&Tシステム開発の技術者として認められている。
それ以前は、すべてのフィーチャーがX-Y軸だけを使って、たとえば穴の位置を決定していた。 そのスケールで位置公差を与えるということは、円形の穴の位置が意図した場所から長方形にずれる可能性があるということです。
しかし、長方形は角に向かって長く、辺に向かって短くなりますが、これはすべての角度で均一な測定を可能にするので、実際には公差ゾーンは円であってほしいのです。
Parker はこのことに気づき、50 年代に軍のエンジニアリング標準として採用された新しい概念に取り組み始めました。
今日、GD&T はエンジニアリング、特に CNC 機械加工サービスを必要とする部品を作成する際に重要な役割を担っています。 その特徴を記述したアメリカの規格はASME Y14.5-2018であり、ヨーロッパの同等規格はISO 1101-2017です。
GD&T は製品の幾何学的形状のみに焦点を当てます。
Why Implement GD&T?
私たちには、寸法と公差を示す従来の方法があります。
Geometric dimensioning and tolerancing (GD&T) は、通常の方法と比較して、いくつかのユニークな利点を提供します。 これらが何であるか見てみましょう。
完璧なアセンブリ
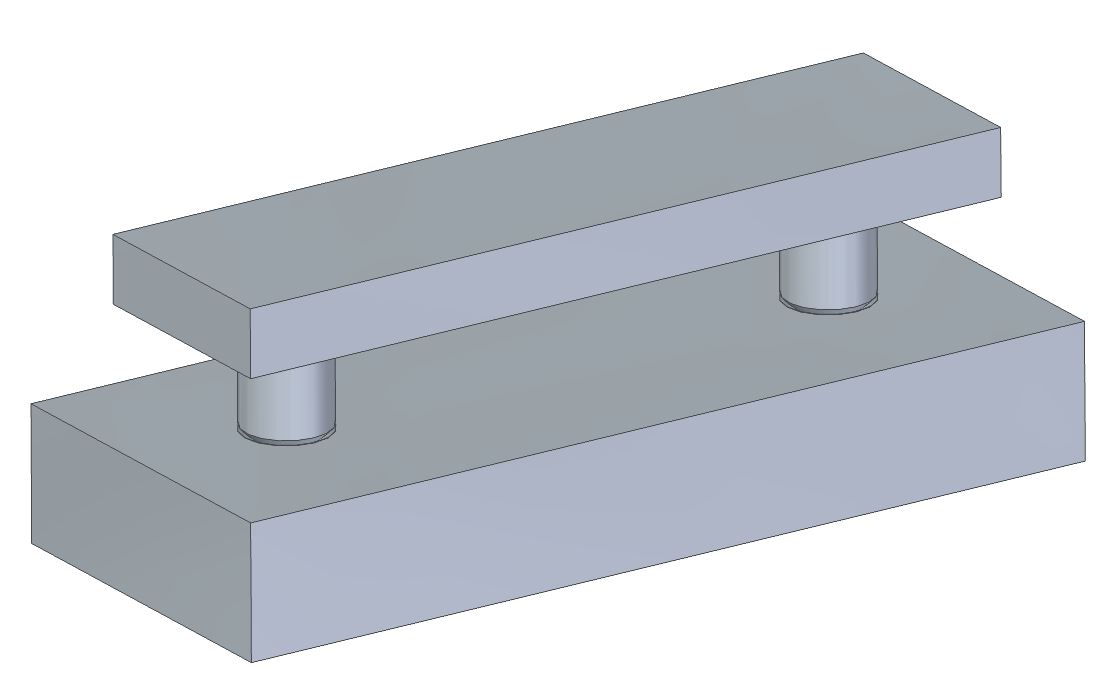
従来の寸法およびトレランスを使う場合の最も大きな欠点は、個々の部品や部品の特徴情報を示していることでした。 これは、当社のパーツがアセンブリ レベルでどれだけうまく適合し機能するかを保証するものではありません。
ほとんどのパーツはそれ自体では役に立たないので、これは重要なことです。 コネクティング ロッドの例で考えてみましょう。 それ自体は何の利益ももたらさない。 しかし、クランクシャフトとピストンに接続すると、ピストンの直線運動をクランクシャフトの回転運動に変換するため、少し便利になります。
このアセンブリがディーゼルエンジンなどの大きなアセンブリの一部になった場合、多くの用途を提供する発電機の部品として完成させることができます。 だから、GD&Tが必要なのです。
設計意図を説明するための共通システム
GD&T は、設計者が設計意図をすべての関連部門に伝えるためのプラットフォームも提供します。 これには、
- 製造
- 検査
- 最初の設計チームが使えない場合に仕事を拾う設計部門の将来の設計者
定義、語彙、ルールは、わかりやすくて世界的に理解しやすいものです。
Saves time and money
GD&T を使用する最も重要な利点は、この点です。 このシステムを使用すると、設計-製造-テスト フィットのサイクル数を削減できるため、無駄が少なくなります。
これは、製造した部品が最初の試みでうまく適合し、その結果、不合格品の数が少なくなるためです。 また、共通言語を使用することで、検査に必要な労力も軽減される。
Get your manufacturing quote in seconds
-
Quote in seconds
-
短いリードタイム
-
Fractoryによる配送
Get quote
What to Consideration ?
Geometric dimensioning and tolerancing は、従来の公差と比較して、より強力なシステムです。 しかし、すべての部門 (設計、エンジニアリング、製造) が情報の読み取りと解釈に精通している場合にのみ機能します。
したがって、エンジニアリング図面を作成し、さまざまな部品の特徴を許容する一方で、製品開発のどの段階においても、図面を扱うすべての人の利益のために、推奨ガイドライン/規約を守ることが重要です。 5583>
Intelligibility of the drawing
これは間違いなく図面の最も重要な品質です。 分かりやすさとは、部品の特徴が描かれ、公差が図面に示されていることの明瞭さのことである。
- すべての部品の特徴に真のプロファイルを描く。
- 寸法と公差を図面の外側(上部ではなく)に表示する。
- 読書方向は一定でなければならない。
- 部品とその機能を簡単に説明する。
- 直角(90°)でないときだけ角度を指定する。
Tight tolerances only when necessary
部品の適合性や機能が必要としない限り、公差はできるだけ緩く保つ必要があります。 これは製造コストとターンアラウンドタイムを削減します。 製造方法の選択は機械工に任せることを推奨します。
設計者は図面の一般的な公差についても言及する必要があります。 これは、すべての部品フィーチャーの標準的な公差として機能します。 異なる公差制限を持つパートフィーチャーについては、設計者は適切な位置でそれらを言及しなければならない。
これらの特定の公差制限は、一般公差をオーバーライドする。
GD&T Features & Symbols
GD&T言語は、完璧なアセンブリを保証するために必要な、ほとんどすべての品質を定義することができます。 図面上でこれらのエンジニアリング シンボルを正しく使用するには、まずこのシステムのいくつかの基本的な構成要素に精通している必要があります。
GD&Tシンボルに入る前に、さまざまな定義、用語、およびルールから始めることができます。 理想的に実現したい正確な寸法である。 サイズ、方向、基準点からの位置などのフィーチャーの仕様は、機械工が目標とする公称寸法を持つ。 これは、番号として、またはASMEのような一般的な規格から示されることがあります。
フィーチャーコントロールフレーム
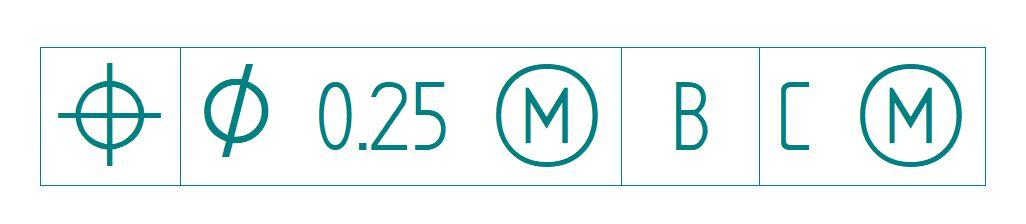
このフレームには部品の仕様についての情報が含まれています。 様々な区画があり、各区画はパーツフィーチャーの特定の属性を定義する。
特徴制御フレームは、次のように4つの主要部分に分けられる。
Leader arrow
この矢印は、制御対象の部品特徴を示す。 サーフェスにつながっている場合、そのサーフェスは幾何学的な制御下にある。 直径寸法をマークしている場合、GD&Tは軸を制御します。
Geometric characteristic symbol
最初の区画(左から)には、幾何学的特性記号が含まれる。 ここで幾何学的特性を指定します。 幾何公差は記号の数から全部で14種類、分類すると15種類あります。
幾何特性の種類は、形状制御、プロファイル制御、位置制御、方向制御などです。
Feature tolerance compartment
2nd blockには最大3つ(2つまたは1つの場合もある)の異なるシンボルが含まれています。
最初のシンボルは、トレランス区画の種類を示す。 直径記号(⌀)は、直径ゾーン(円筒形トレランスゾーン)を意味します。 球形ゾーンを指定するには、記号は文字’S’の後に直径記号(⌀)を付けます。 記号がない場合は、全幅のゾーンとします。
2番目のブロックの2番目の記号は、公差ゾーンの値をmm単位で与えます。 この値は常に第2ブロックに存在しなければならない。
このブロックの第3記号は公差の修飾語である。 この材料修飾子は、そのフィーチャーがサイズ、例えば穴を持つ場合にのみ存在します。 材料修飾子の例としては、MMC(最大材料条件)、LMC(最小材料条件)などがあります。
Datums
3番目のブロックは、最小で1つ、最大で3つのデータムについての情報を提供します。 3つのデータムの場合、それらは一次、二次、三次データムと呼ばれ、それぞれ別のボックスで囲まれて表示される(上の画像は2つである)。 このブロックには、材料修飾子も含まれることがあります。
以上の情報はすべて、フィーチャ コントロール フレームの読み方を理解するのに役立ちます。
Material Condition Modifiers
Material Condition Modifiers は、特定のフィーチャー サイズでフィーチャーに許容差を適用する場合の意図を伝えるものです。 任意のフィーチャーに公差を与える場合、必ず2つの材料条件
- Maximum material condition
- Least material condition
例えば、直径100mmのシャフトを考えてみましょう。 製造時に公差を±0.2mmとすると、100.2mmのところで、シャフトには最大の材料が含まれることになります。
一方、同じシャフトを直径99.8mmで製造すると、材料は最も少なくなります。
幾何公差は、3つの異なる方法でフィーチャーに適用することができます。
- Maximum material condition
- Least material condition
- Request of feature size
Maximum material condition modifier
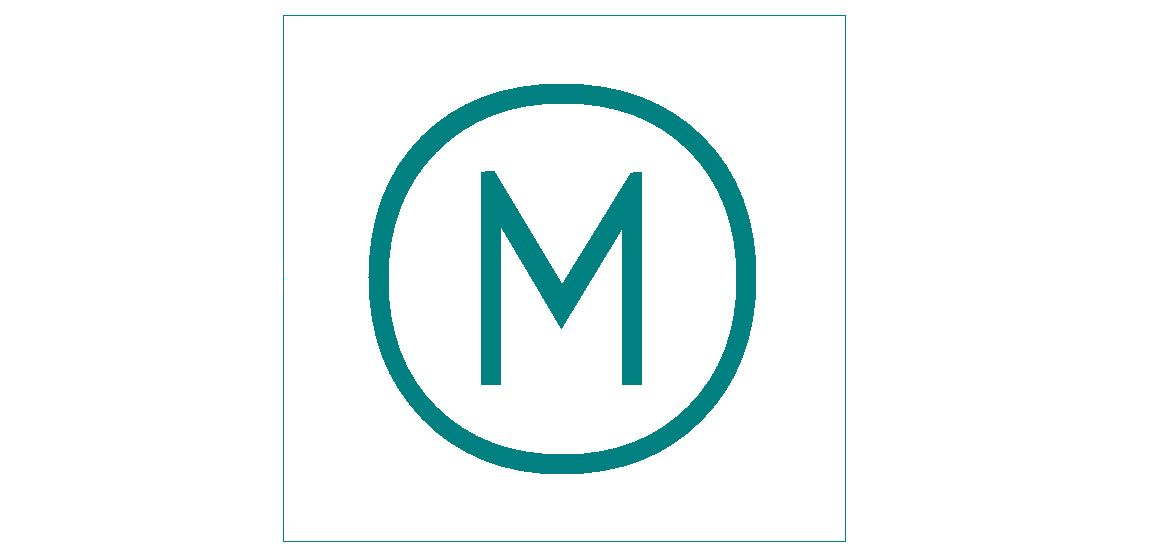
この条件は、特徴コントロール区画の許容値の後に丸で囲った「M」で表わします。 5583>
シャフトの直径のような外部 FOS (Feature Of Size) では、MMC は最大のサイズを表します。 穴の直径のような内部FOSの場合、穴が小さいとより多くの材料を残すことになるので、MMCは規定の許容範囲内で可能な最小のサイズを表します。
最大材料条件で幾何公差を適用する必要がある場合、フィーチャー コントロール フレームでこの条件に言及します。
Least material condition modifier
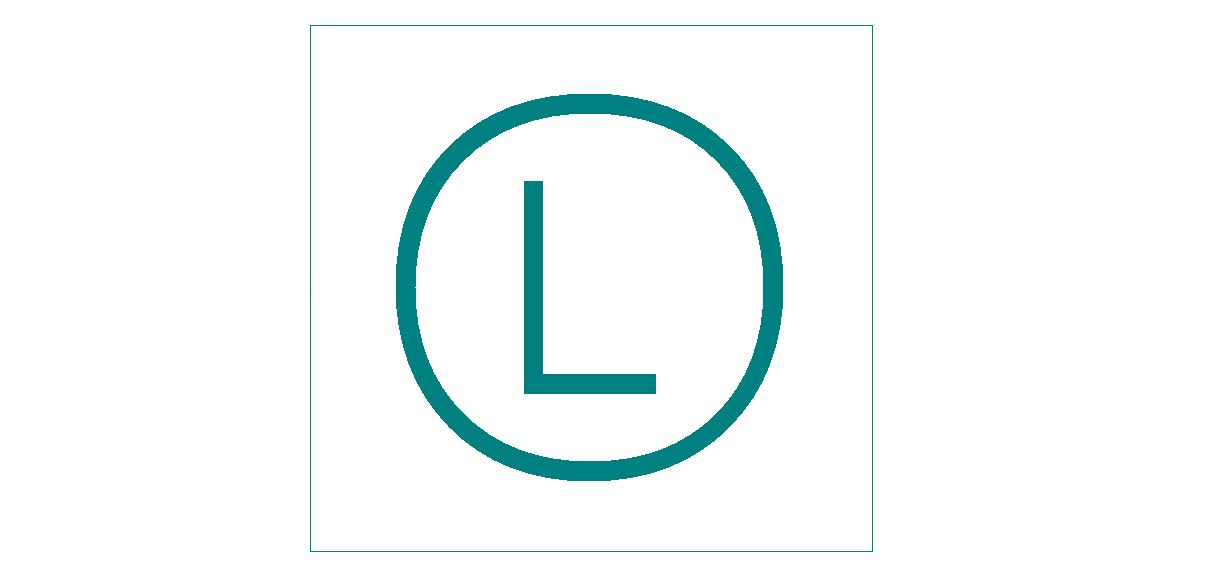
LMCは、材料に最も少ない材料が含まれる状態です。
外部FOSの場合、規定された範囲内で可能な限り小さいサイズとなります。 また、内部FOSでは、可能な限り大きなサイズになります。
この修飾語を丸に「L」の文字で表します。 この機能により、過剰な材料が取り除かれ、その結果重量が増加します。 この条件で幾何公差を適用するには、フィーチャーコントロールフレームでそのシンボルを使用する。
Regardless of Feature Size (RFS)
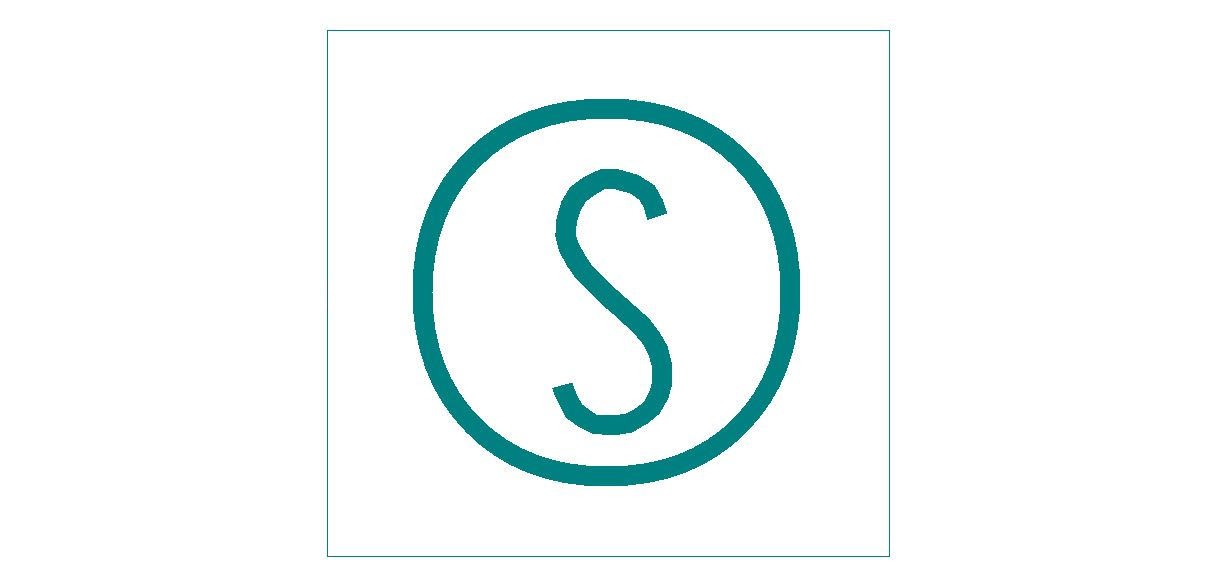
与えられた幾何公差がFOSのサイズの任意の増分で適用する場合、RFSでこれを示す。 RFS の記号は円で囲まれた文字 “S” でしたが、現在では RFS がデフォルト条件と見なされ、記号を必要としないため不要になりました。
データムとフィーチャー コールアウト
データムとは寸法公差を測定するための基準点です。 それは点であったり、線であったり、面であったりする。 データムの助けを借りて、Datum Reference Frames (DRF)を確立します。 DRF は基本的に 3D 座標系で、DRF を基準として他のすべてのフィーチャーの位置を定義するのに役立ちます。
部品を効果的に製造および検査するために制御する必要がある自由度は 6 つ(並進と回転の 3 つ)です。
データムフィーチャーは、穴やスロットなどの実際の部品の特徴である。
データムフィーチャの中でも、アセンブリ内の他の部品と嵌合するものを最も優先的に使用する。 フィーチャーコントロールフレームには、複数のデータムを記述することができます。
GD&T Symbols
フィーチャの異なる幾何学的特性を表すために、最大 14 の GD および T 記号が利用可能です。 これらのシンボルは、これらの特性を最終製品の要件として指定するのに役立つ。
これらの記号は、フィーチャーコントロールフレームの最初の区画に配置される。
形状制御
その名が示すように、形状制御はフィーチャーの最終的な形状に関連する。 我々は、幾何公差の理想的な形からの偏差を制限するために形状制御を定義する。
真直度
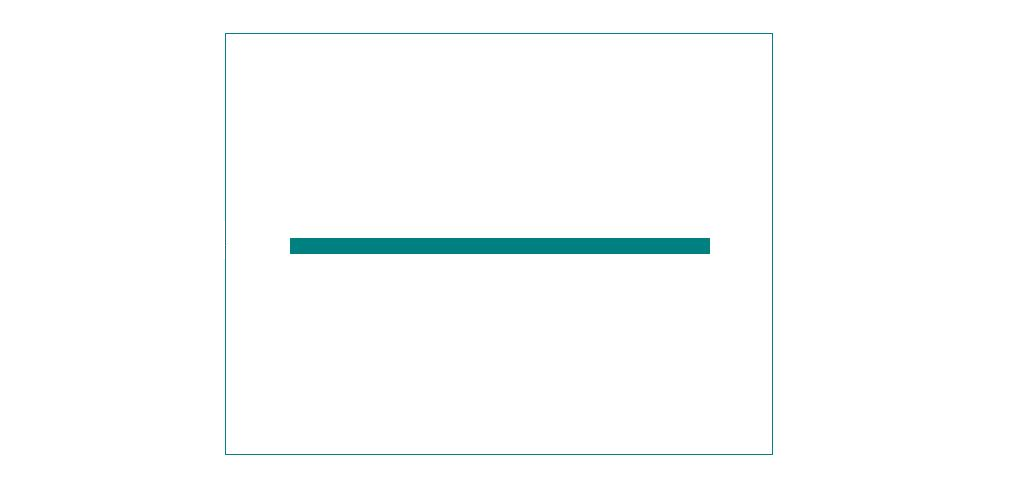
特徴(軸や表面など)の真直度特性を示すために、最初の区画でその記号(まっすぐな水平線)を使用します。
軸方向真直度は、通常、軸や穴などの軸に適用されるもので、表面上の線(2次元)の許容変動幅を規定する。
Flatness
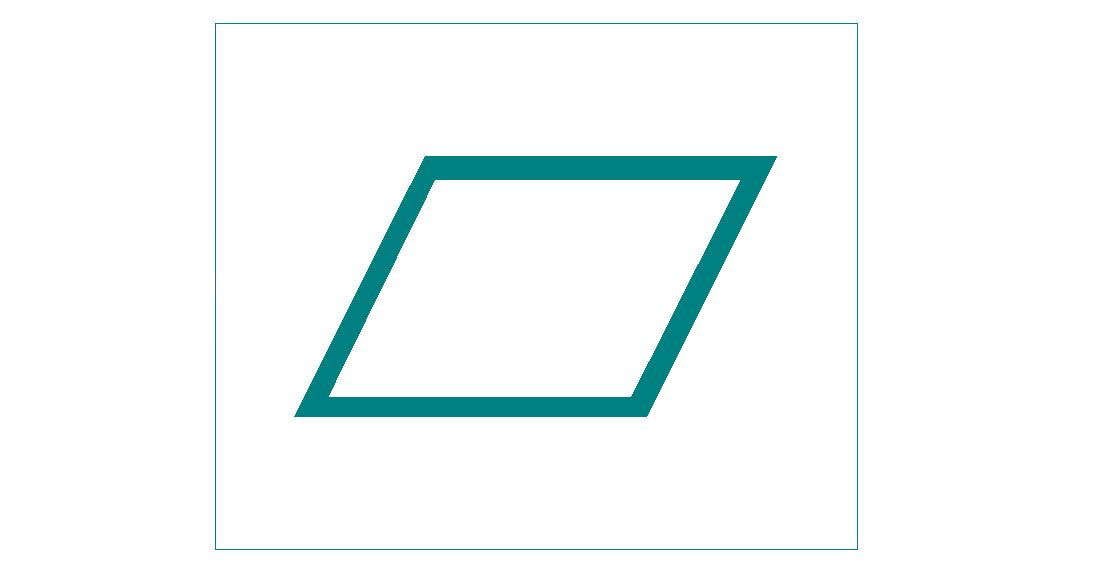
我々はこの特性を部品の表面などの特徴に使用する。 平坦さを表す記号は、右に傾いた平行四辺形である。
平坦度の記号は、部品の表面全体が3次元的に適合しなければならない許容範囲を示すだけなので、いかなるデータムも必要としない。
結果の確認にはハイトゲージが用いられる。
結果の確認にはハイトゲージが使用され、表面のさまざまな領域に触れて、すべての点が許容範囲内にあるかどうかを判断します。
円形度
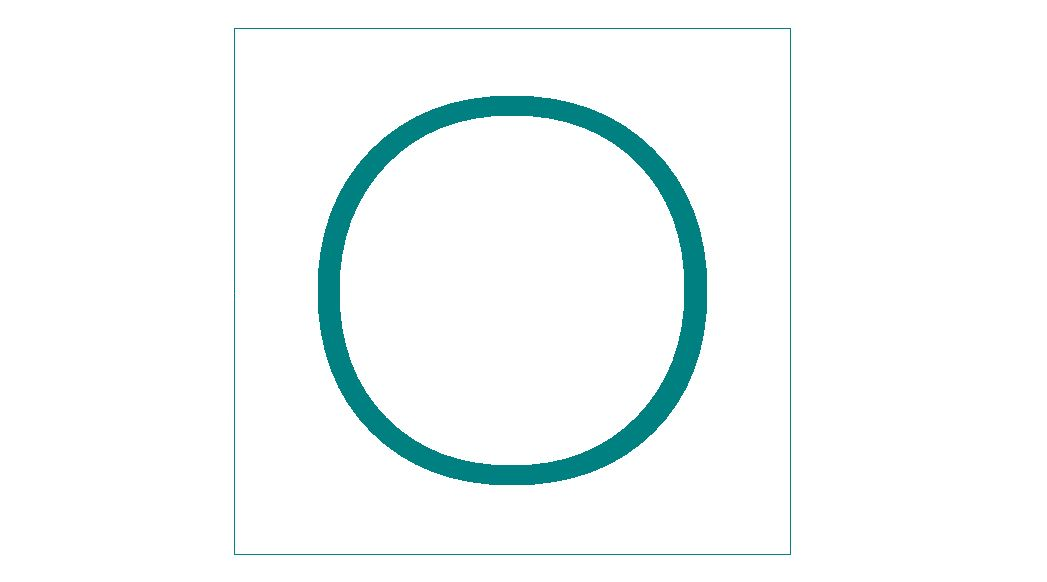
特徴の円形度は、部品の周がどれほど真円に近いべきかを示します。 部品の軸に垂直な平面上にある2つの同心円を使用して、2Dで適切な許容範囲を定義します。 最終的な測定の各ポイントは円の間に入らなければなりません。
この特性は、フィーチャーコントロールフレームの最初の区画に円として表示されます。
Cylindricity
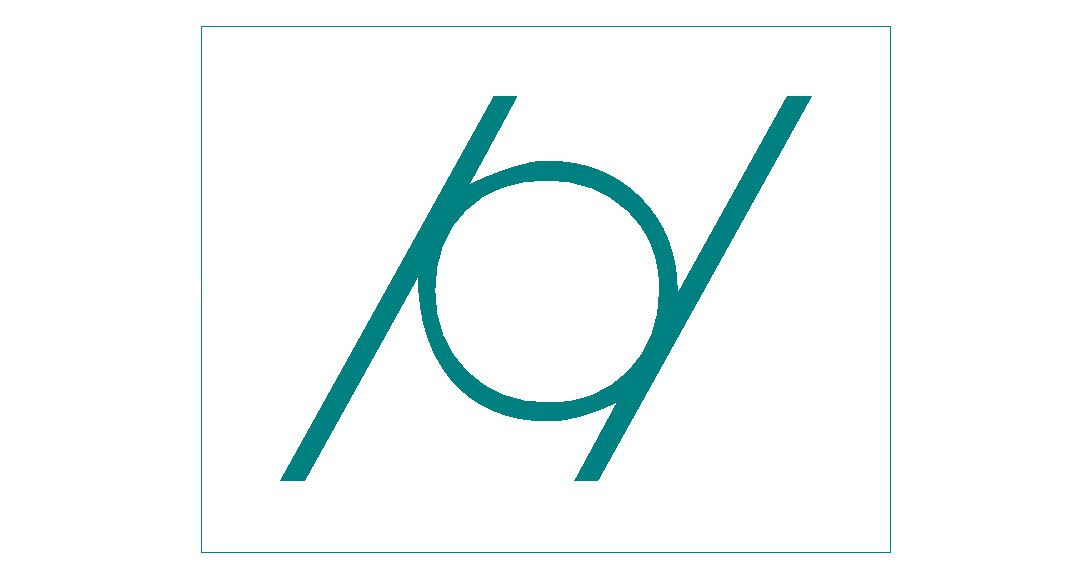
Cylindricity は基本的に3Dの真円度、つまり部品の全長に沿っていること。
この機能は、テーパー、直線度、丸さなど他の円柱特性についても記述することができます。
プロファイル制御
フィーチャー周辺の3D許容範囲を制御するために、プロファイル制御を使用します。 この機能は、高度なカーブやシェイプに許容範囲を与えるのに役立ちます。
高度なカーブに適した機能は、当然、単純なカーブでもうまく機能するはずです。 このため、プロファイル制御は非常に汎用性が高いのです。 このため、他のすべてのコントロールを放棄し、プロファイル コントロールのみで作業することを推奨するデザイナーもいます。
これらのコントロールは、両側の高度な曲線を模倣することにより、高度な曲線の周りに許容制限を形成します。 そして、フィーチャ カーブ上のどのポイントも許容限界の外に出るのを防ぎます。
Line Profile
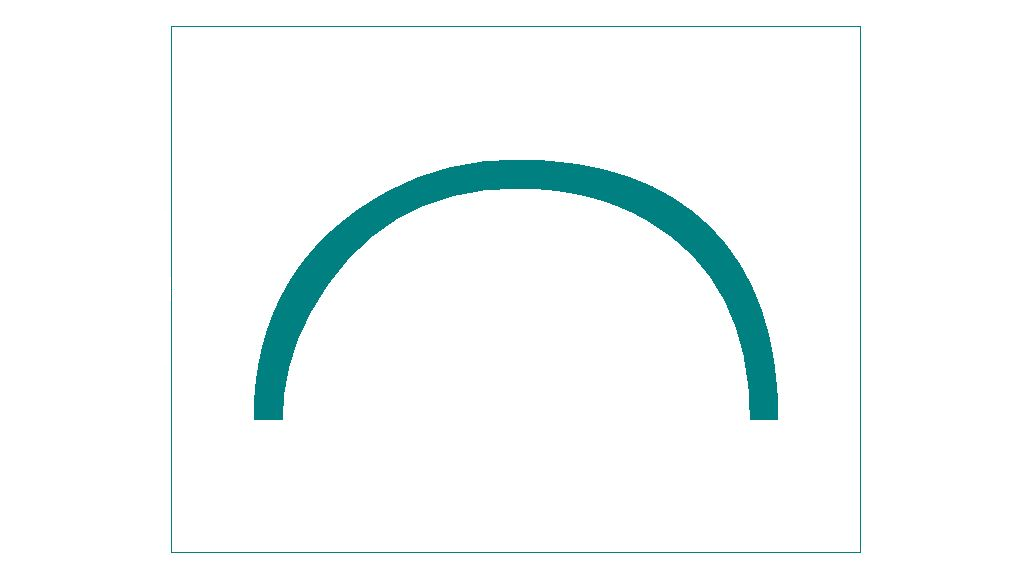
Line Profile は、パーツのさまざまな 2D 断面に対してトレランス ゾーンを設定します。 5583>
ライン プロファイル コントロールは、両側の許容限界で理想的な曲線をトレースします。
Surface Profile
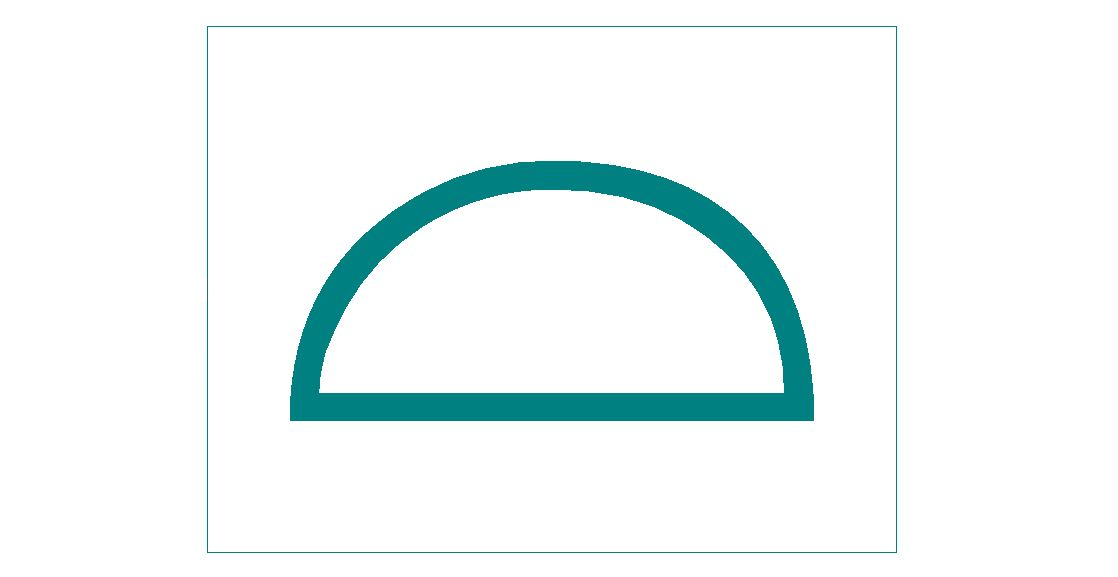
Surface Profileコントロールはラインコントロールと比較してより一般的なものです。 5583>
テーブルのサーフェス上のすべての点は、2 つの仮想平面内になければなりません。
方向制御
方向公差は、定義された基準に対するフィーチャーの方向を制御するものです。 GD&T には 3 種類の方向制御があります。
Angularity
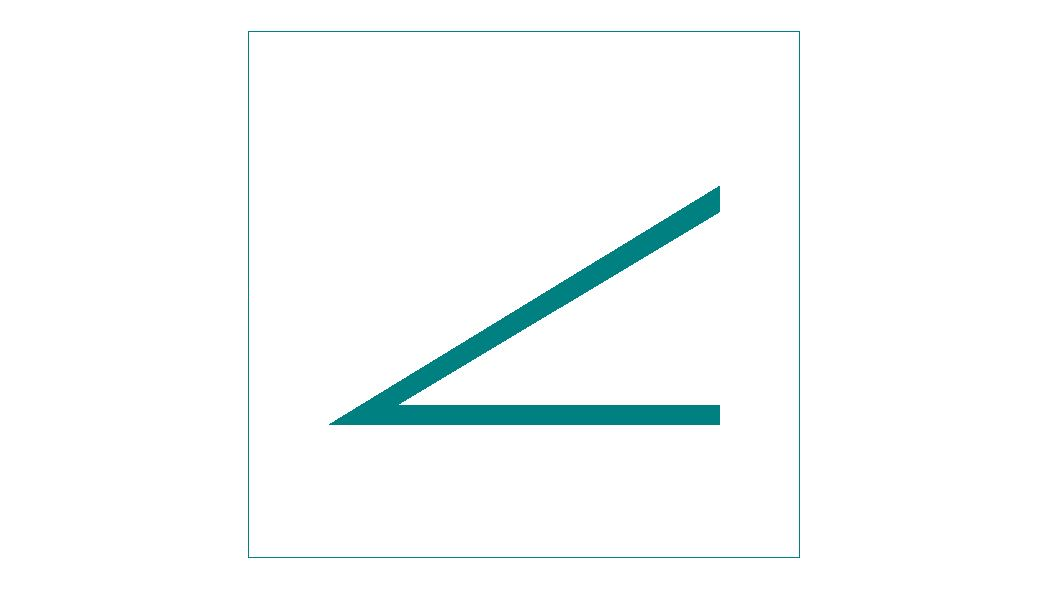
angleity 制御は、データムに対するフィーチャーの角度を抑制するものです。 2Dラインの制御にも使えますが、サーフェス(3D)の制御を維持する方がポピュラーです。
このような厳しいコントロールは、角度とサーフェスの平坦さを維持し、角度のあるサーフェスを通して他のパーツと嵌合するパーツ フィーチャーに推奨されます。
Parallelism
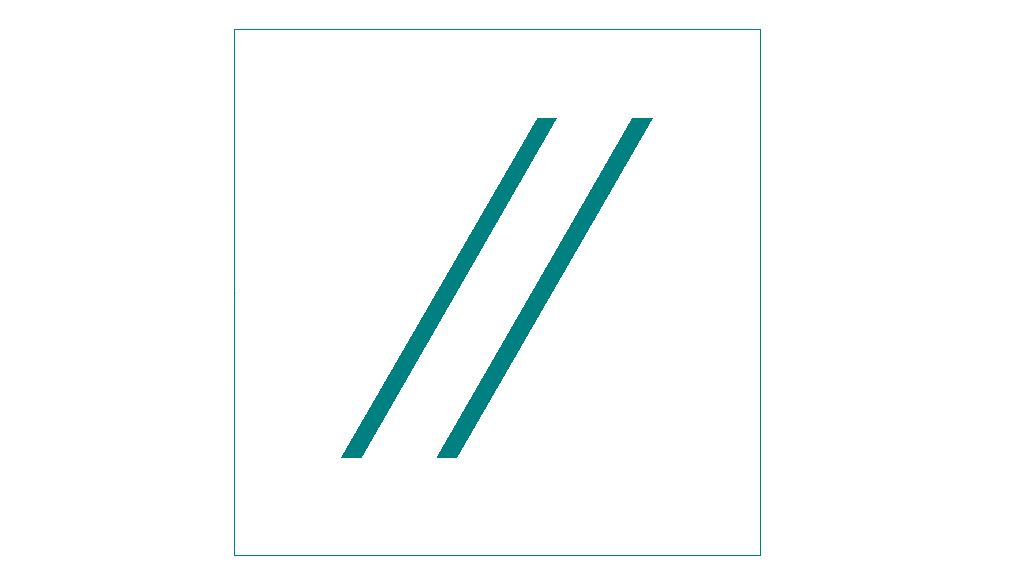
Parallelism は角度を洗練した形です。 ここで、データムは模倣する必要のある表面で、角度は0°に設定される。 平行移動には、表面平行移動と軸平行移動の2種類がある。
基準として軸または面を選択することができます。 これがデータとなり、フィーチャーコントロールフレームの3番目のブロックでフィーチャーのデータムとして参照します。
角度と同様に、実際の角度を制御するのではなく、許容範囲という形で要件を並べることによって確保するものです。
Perpendicularity
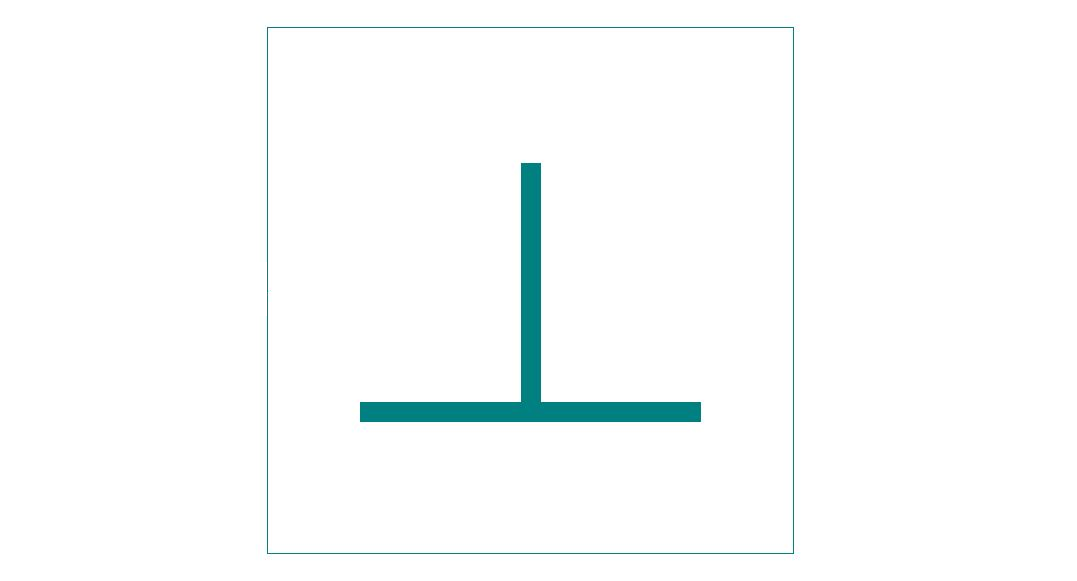
Perpendicularity も角度の特定の形で、角度を90°に設定するものである。 これは2つの全く異なるタイプの要件を意味するので、厄介なコントロールです。
表面垂直( Symbol:⟂)があり、さらに軸垂直( Symbol: ⟂+⌀)があります。
Surface perpendicularity は、角度性と同様に、サーフェスまたはラインがデータムサーフェスまたはラインに対して垂直である必要があることを指定します。 5583>
Axis perpendicularityは、軸が言及されたデータムに対してどれだけ垂直である必要があるかを指定するもので、制御のためにターゲットサーフェスの周りに2つの仮想平面/線が想定されています。
位置制御
位置公差制御は、データムに対するフィーチャーの位置を厳密に制御するために使用される。
Concentricity
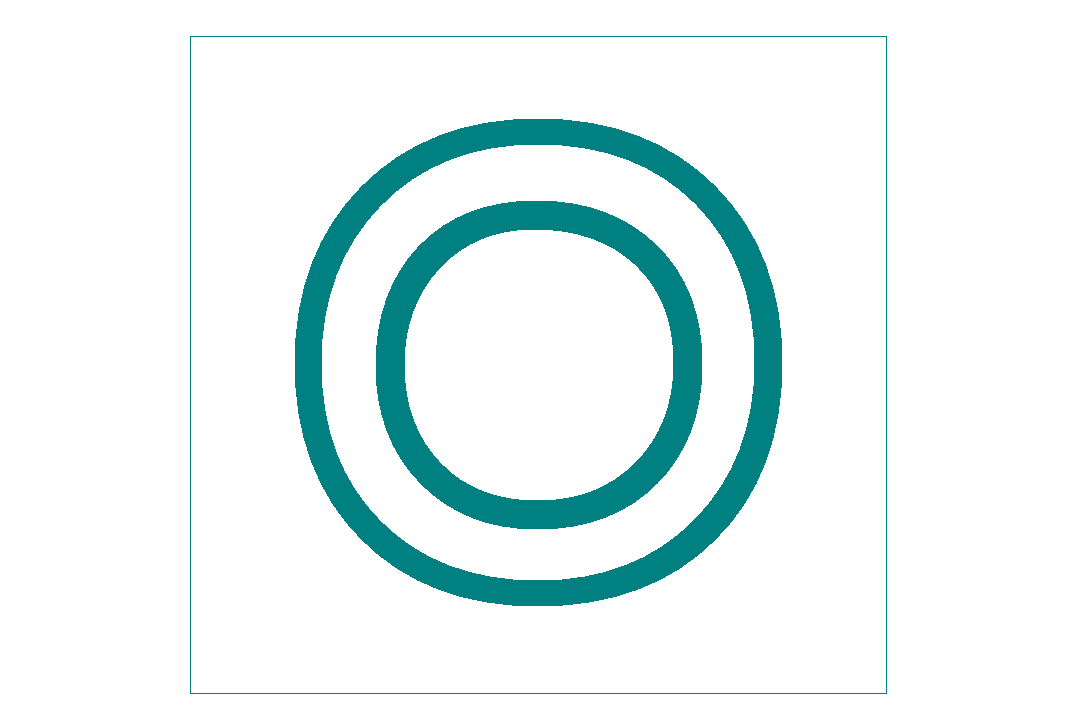
同心度、または同軸度としても知られており(まったく同じ意味ではないが)、円筒形だけでなく、円形の特徴の同心度を維持する制御です。
このコントロールは、軸が実際の配置ではなく、外部の測定値から得られるため、いくつかの混乱を引き起こす可能性があります。
Coaxiality は、サーフェス測定に基づいて、パーツが位置しなければならない 3D トレランス ゾーンを作成します。
Symmetry
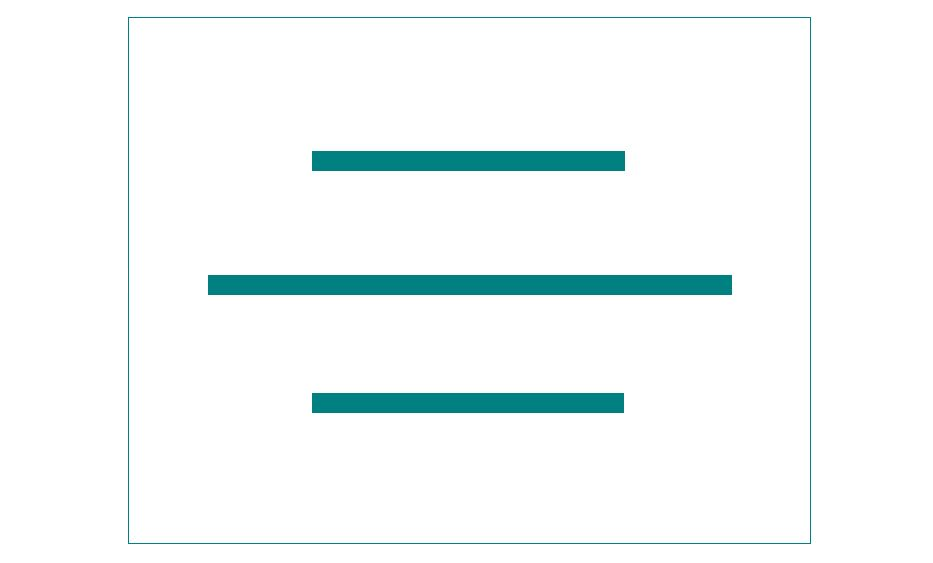
対称呼び出しによって、機能の 2 つのパーツが等間隔で置かれる中心平面を確立します。 左右の 2 点の中点は、中心平面の周囲に設定された許容範囲内になければなりません。
Symmetry callout はあまり一般的ではありません。 用途が非常に限られており、また検査も困難です。
True position
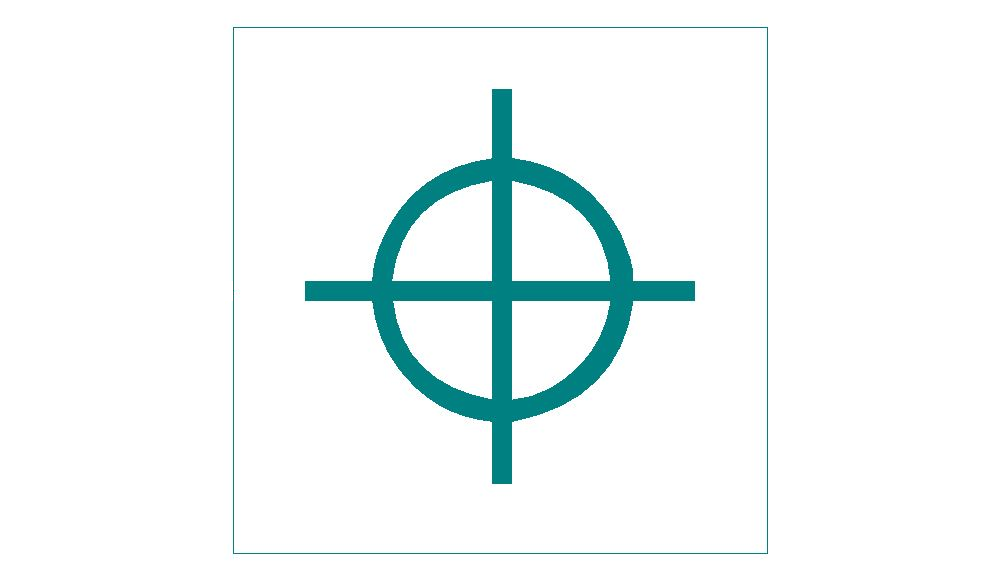
True position(一般に位置と呼ばれる)は非常に便利なコールアウトで、GD&T で広く使用されています。 この定義には、測定値が関連する基準平面が含まれます。
許容範囲が X 軸と Y 軸だけでなく円であることを強調するために、直径の記号 (⌀) を含むことがあります (GD&T を最初に作成した理由としてこの記事の冒頭でお話しました)。
True Position を使用して、図面上で公差を使用する方法を紹介する素晴らしいビデオがあります。
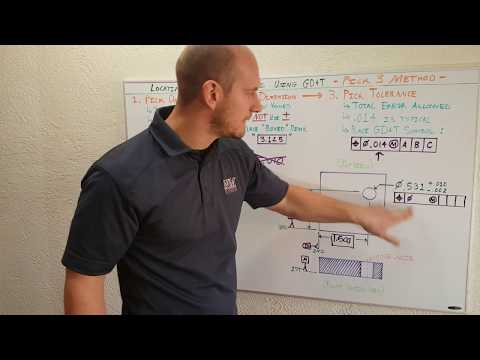
How to Apply GD&T Position Tolerance to a Hole
Runout controls
部品形状が確立したデータムを基準に割り付けられた位置からの偏差を測定するには、ランアウト コントロールを使用します。 このコントロールは円形フィーチャーに使用されます。
振れ制御には2つのタイプがあります。
円形振れ

円形振れは2次元で動作し、さまざまなパーツ形状の形状、位置、方向を制御します。 この 2D コールアウトは、これらのフィーチャをチェックするためにデータム軸を割り当てる必要があります。
GD&T の専門用語では、円形振れは一般に振れとして知られています。 振れは、回転による表面要素の偏差を測定します。
意味は、たとえばシャフトをそのデータム軸で回転させ、特徴的な要素を公差測定することです。 要するに、ベアリングのような接続部品の長寿命を確保するために、作業シャフトの振動を制限します。
総振れ
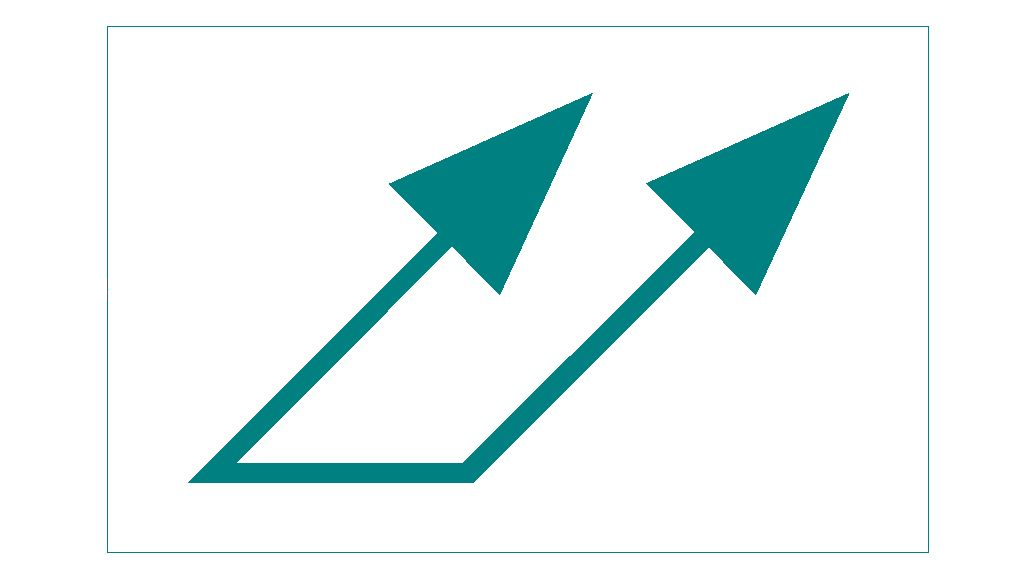
総振れは、円振れの3D対応部分です。 同様に形状、位置、向きを制御します。 しかし、(円形振れのように)個々の断面をチェックするのではなく、表面全体をチェックする。 このように、全振りを利用することで、フィーチャーの特性をより厳密に制御することができる。
検査
あらゆる産業において、製造工程が設計仕様を満たさないことが問題になることがあります。 顧客の命が危険にさらされるケースもあれば、製品回収により莫大な金銭的損失を被るケースもある。
結果がそれほど悪くなくても、企業の評判はその製品やサービスの品質に大きく依存しています。
GD&T は、検査員を設計者と同じプラットフォームに参加させることにより、検査プロセスを標準化しています。 これによって、多くの障害が取り除かれるのです。 しかし、GD&Tは広大なテーマです。
これまで見てきたように、GD&Tで制御できる幾何学的特性はいくつもあり、それぞれ非常に異なっています。 この相違のため、各特性の検査には特定の方法、ツール、およびスキルが必要です。
これらの特性の中には、最も簡単なツールで測定できるものもあれば、座標測定機 (CMM) などの高度な装置なしでは測定不可能なものもあります。
検査員は、部品の精度を満足に検査するために、ダイヤルゲージ、マイクロメータ、ノギス、定盤、座標測定機などのさまざまな測定ツールを使用する知識と技術を必要とします。